As a professional welder, the allure of mastering the art of underwater welding can be both exciting and challenging. The unique environment of underwater welding presents a set of difficulties that require specialized techniques, equipment, and safety measures. In this comprehensive guide, we will delve into the world of underwater welding, exploring the various techniques, challenges, safety measures, and advancements in technology. Whether you are an experienced welder or someone interested in pursuing a career in underwater welding, this article will provide valuable insights into this fascinating field.
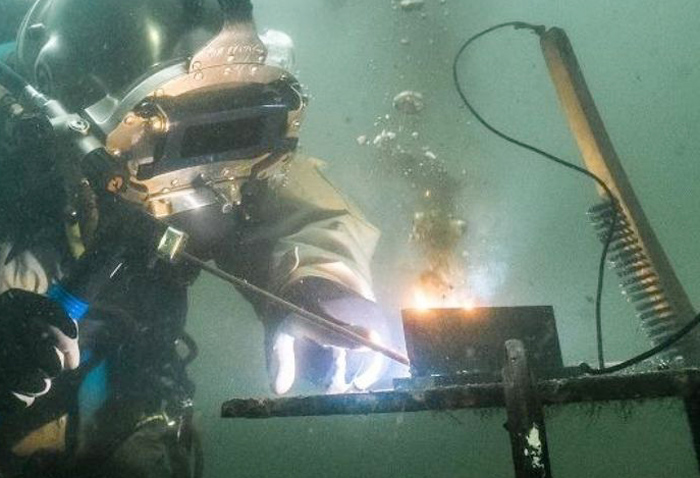
Photos: facts.net
Underwater Welding Process
Underwater welding, also known as hyperbaric welding, is a specialized welding process that takes place underwater. It is commonly used in marine construction, offshore drilling, and repair of underwater structures such as pipelines, ships, and oil platforms. There are two primary methods of underwater welding: dry welding and wet welding. Dry welding involves welding in a dry chamber that is sealed and pressurized, allowing welders to work in a dry environment underwater. Wet welding, on the other hand, is performed directly in the water, using specialized equipment and techniques to ensure the integrity of the welds.
Underwater welding presents unique challenges due to the underwater environment, including water pressure, visibility, and the presence of marine life. The welding process must also account for the corrosive nature of water and the need for structural integrity in underwater applications. Understanding the fundamentals of underwater welding is essential for welders looking to master this specialized skill and ensure the safety and quality of their work.
The Challenges of Underwater Welding
One of the primary challenges of underwater welding is working in an environment with high water pressure. As a welder descends into the depths, the pressure increases, requiring careful planning and equipment to ensure the safety of the welder and the integrity of the welds. Additionally, underwater welding often takes place in low-visibility conditions, making it essential for welders to rely on specialized lighting and visual aids to carry out their work effectively.
Another challenge is the presence of marine life, which can pose a hazard to welders and interfere with the welding process. Welders must be mindful of their surroundings and take precautions to minimize the impact of marine life on their work. The corrosive nature of water can affect the quality of welds, requiring specialized techniques and materials to mitigate the effects of corrosion and ensure the longevity of the welds in underwater applications.
Safety Measures for Underwater Welding
Safety is paramount in underwater welding, given the unique challenges and potential hazards associated with working in an underwater environment. Prior to any underwater welding operation, a thorough risk assessment must be conducted to identify potential hazards and implement appropriate safety measures. This includes ensuring that all equipment is in optimal working condition, that the welder is properly trained and certified, and that emergency procedures are in place.
Welders must also be equipped with the necessary personal protective equipment (PPE) designed specifically for underwater welding, including diving suits, helmets, and communication devices. These specialized PPE items are essential for protecting welders from the effects of water pressure, maintaining clear communication, and providing a barrier against potential hazards in the underwater environment. Adherence to established safety protocols and continuous monitoring of environmental conditions are critical to ensuring the safety of underwater welding operations.
Underwater Welder Requirements
Becoming an underwater welder requires a unique set of skills, qualifications, and certifications. In addition to being a certified welder, individuals pursuing a career in underwater welding must undergo specialized training to familiarize themselves with the challenges and techniques specific to underwater environments. This typically involves completing a commercial diving program that includes coursework in diving physics, physiology, and underwater welding procedures.
Obtaining certification from reputable organizations such as the American Welding Society (AWS) or the Association of Diving Contractors International (ADCI) is essential for demonstrating the proficiency and competence required for underwater welding. These certifications validate the welder’s ability to perform underwater welding safely and effectively, providing assurance to employers and clients that the welder meets industry standards and best practices.
Essential Equipment for Underwater Welding
Underwater welding requires specialized equipment to ensure the safety and effectiveness of the welding process. This includes diving gear such as drysuits, helmets, and breathing apparatus, as well as welding equipment adapted for use in underwater environments. The welding equipment used for underwater welding must be designed to withstand the pressures and conditions encountered underwater, and it often includes specialized welding electrodes, power sources, and shielding gases.
In addition to welding equipment, underwater welders rely on a range of tools and accessories to facilitate the welding process, including cutting devices, cleaning tools, and lighting systems to enhance visibility in low-light conditions. The proper selection and maintenance of underwater welding equipment are crucial for achieving high-quality welds and ensuring the safety of welders operating in challenging underwater environments.
Underwater Welding Techniques
Mastering the techniques for successful underwater welding is essential for achieving strong, durable welds in underwater applications. Wet welding, in particular, requires specialized techniques to account for the presence of water and the challenges of working in a submerged environment. The use of proper welding techniques, such as shielded metal arc welding (SMAW) and gas tungsten arc welding (GTAW), is crucial for ensuring the integrity and quality of underwater welds.
Welders must be proficient in the use of underwater cutting and cleaning tools to prepare the welding area and ensure the proper alignment of the materials being joined. The ability to effectively navigate underwater conditions, maintain control of the welding process, and adapt to the challenges of the underwater environment is fundamental to achieving successful welds in underwater welding operations.
Common Types of Underwater Welding
Within the realm of underwater welding, there are several common types of underwater welding processes that are utilized based on the specific requirements of the project. These include wet welding, dry welding, and hyperbaric welding, each with its own distinct advantages and applications.
- Wet welding: Wet welding, as the most common method, involves performing welding directly in the water, utilizing specialized equipment and techniques to ensure the quality and integrity of the welds.
- Dry welding: Dry welding, on the other hand, takes place in a sealed and pressurized chamber, allowing welders to work in a dry environment underwater. This method is often preferred for projects requiring a higher level of control and precision.
- Hyperbaric welding: Hyperbaric welding, which encompasses both wet and dry welding techniques, involves welding in a chamber that is pressurized to match the surrounding water pressure, providing a controlled environment for the welding process. Understanding the nuances of each type of underwater welding is essential for selecting the most suitable method for a given project.
Underwater Welding Certification and Training
The specialized nature of underwater welding necessitates comprehensive training and certification to ensure the proficiency and safety of welders operating in underwater environments. Training programs for underwater welding encompass a range of topics, including diving techniques, welding procedures, safety protocols, and emergency response procedures. These programs are designed to equip welders with the knowledge and skills necessary to perform underwater welding operations effectively and safely.
Furthermore, obtaining certification from recognized organizations is essential for demonstrating the competence and adherence to industry standards required for underwater welding. Certification programs typically involve practical assessments, written examinations, and adherence to established guidelines and best practices. By completing rigorous training and certification processes, underwater welders can establish themselves as qualified professionals capable of meeting the demands of underwater welding projects.
Advancements in Underwater Welding Technology
The field of underwater welding continues to evolve with advancements in technology, equipment, and techniques aimed at enhancing the safety, efficiency, and quality of underwater welding operations. Innovations in welding equipment, such as the development of specialized welding electrodes and power sources designed for underwater use, have contributed to improved weld quality and productivity in underwater applications.
Advancements in diving technology, including the use of remotely operated vehicles (ROVs) and underwater welding robots, have expanded the capabilities of underwater welding, allowing for greater precision and access to challenging underwater environments. These technological advancements have not only improved the efficiency of underwater welding but have also contributed to the safety of welders by reducing the need for direct human intervention in certain underwater welding operations.
Conclusion
Mastering the art of underwater welding requires a combination of specialized skills, training, equipment, and adherence to stringent safety measures. As advancements in technology continue to shape the field of underwater welding, welders must stay abreast of the latest developments and best practices to ensure the success of underwater welding projects. By understanding the challenges, techniques, and safety measures associated with underwater welding, welders can embark on a rewarding journey into the fascinating world of underwater welding, contributing to vital marine construction and repair efforts while upholding the highest standards of quality and safety.