Diving into the depths of underwater welding unveils a fascinating world where technology meets the ocean’s uncharted territories. From hyperbaric welding to dry and wet underwater welding, the types of techniques available offer a spectrum of challenges and opportunities. For those with a passion for welding and a sense of adventure, exploring the methods and intricacies of underwater welding can be both exhilarating and rewarding.
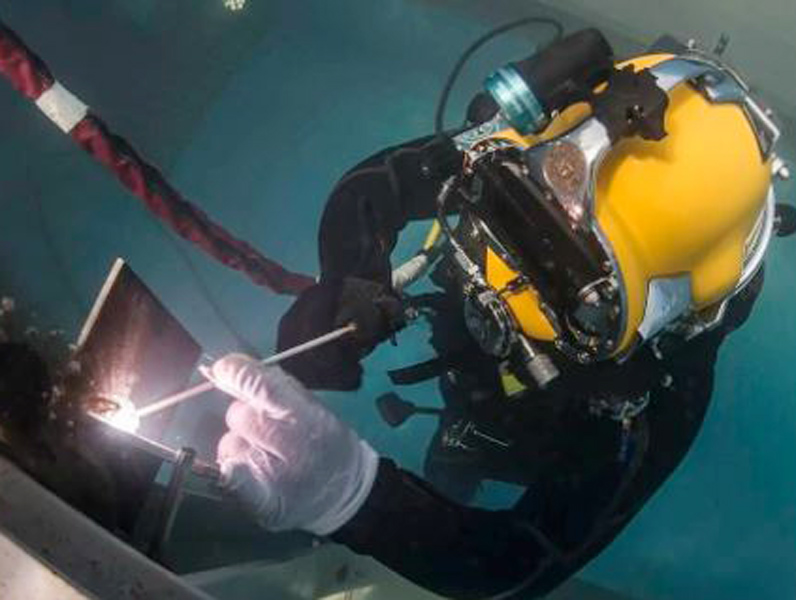
Photos by waylanderwelding.com
Wet Welding Techniques and Equipment
Wet welding, also known as underwater wet welding, is a technique that involves welding in the direct presence of water. It requires specialized equipment designed to work effectively in wet conditions, including waterproof electrodes and insulated welding machines. The process demands a high level of skill and precision due to the dynamic nature of the underwater environment.
Welders must contend with factors such as water currents, visibility challenges, and the need for constant monitoring of the welding arc’s stability. Despite these complexities, wet welding is a widely used method for repairing marine structures, pipelines, and offshore platforms.
Wet welding presents unique considerations, including the management of hydrogen embrittlement and the use of specialized welding rods to mitigate the effects of water on the welding process. The safety of the underwater welder is of paramount importance, with stringent protocols in place to ensure the protection of both the welder and the surrounding environment. As technology continues to advance, innovations in wet welding equipment and techniques are continually improving the efficiency and safety of underwater welding operations.
Dry Welding Techniques and Equipment
In contrast to wet welding, dry welding takes place in enclosed environments that are isolated from the surrounding water. This method often involves the use of cofferdams, hyperbaric chambers, or other structures that create a dry space for welding activities. Dry welding offers distinct advantages in terms of improved visibility, control over environmental variables, and reduced exposure to the inherent risks of working directly in water. As a result, it is commonly employed for more intricate and critical welding tasks, such as the repair of nuclear power plant components and the construction of underwater tunnels.
The specialized equipment utilized in dry welding includes hyperbaric welding systems, welding habitats, and advanced gas management solutions to maintain the appropriate atmospheric conditions within the welding environment. Welders trained in dry welding techniques must possess a comprehensive understanding of the unique challenges posed by confined spaces and the complexities of working in pressurized conditions. As with wet welding, safety protocols are rigorously enforced to ensure the well-being of the welder and the integrity of the welding operation.
Hyperbaric Welding and Its Applications
Hyperbaric welding, also referred to as “dry hyperbaric welding,” is a specialized form of dry welding that takes place in a hyperbaric chamber. This method allows for welding at significant depths and under higher pressures, enabling the repair and construction of critical infrastructure in extreme underwater environments. Hyperbaric welding is particularly suited for projects that require precise control over environmental factors, such as the maintenance of oil and gas pipelines, the installation of offshore wind turbines, and the construction of subsea infrastructure.
The application of hyperbaric welding extends beyond traditional construction and repair tasks, encompassing cutting-edge projects in the fields of scientific research and exploration. Submersibles, deep-sea habitats, and underwater observatories benefit from the precise welding capabilities offered by hyperbaric welding techniques. As technology continues to advance, the potential for hyperbaric welding to support innovative initiatives in ocean exploration and sustainable resource development becomes increasingly apparent.
Challenges and Risks of Underwater Welding
Underwater welding presents a myriad of challenges and risks that demand a high degree of technical expertise and safety consciousness. Factors such as limited visibility, fluctuating water currents, and the potential for rapid changes in environmental conditions necessitate meticulous planning and execution. Welders must also contend with the physical demands of working in water, including the need to maintain buoyancy and stability while performing intricate welding tasks.
One of the primary risks of underwater welding is the potential for electric shock, as the presence of water creates an environment conducive to electrical conductivity. To mitigate this risk, specialized welding equipment and thorough safety protocols are employed to safeguard the welder and prevent potential hazards.
Additionally, the management of gas pockets and the prevention of hydrogen embrittlement are critical considerations that require careful attention throughout the welding process.
Training and Certification for Underwater Welders
Given the specialized nature of underwater welding, comprehensive training and certification programs are essential for welders seeking to embark on underwater welding careers. These programs encompass theoretical knowledge, practical skills development, and rigorous assessment of competency to ensure that welders are equipped to handle the unique challenges of underwater welding.
Training often includes instruction on diving techniques, welding procedures, equipment maintenance, and emergency preparedness to instill a thorough understanding of the complexities involved in underwater welding operations.
Certification for underwater welders typically involves meeting stringent industry standards and demonstrating proficiency in both diving and welding competencies. Regulatory bodies and industry organizations play a crucial role in establishing and upholding certification requirements, ensuring that underwater welders adhere to the highest levels of safety and proficiency. Continuous professional development and adherence to evolving industry standards are fundamental aspects of maintaining certification as an underwater welder.
Notable Projects and Applications of Underwater Welding
The applications of underwater welding span a diverse range of industries and projects, reflecting the vital role it plays in maintaining and expanding critical infrastructure around the world. Notable projects include the repair and maintenance of offshore oil and gas platforms, the construction and installation of undersea telecommunications cables, and the restoration of historic shipwrecks and marine monuments. The versatility of underwater welding extends to supporting scientific research initiatives, such as the assembly of deep-sea research facilities and the repair of underwater observatories.
Innovative applications of underwater welding also encompass the development of renewable energy infrastructure, including the installation and maintenance of offshore wind farms and tidal energy systems. These projects require the precision and reliability of underwater welding techniques to ensure the durability and integrity of subsea structures in challenging marine environments.
As technological advancements continue to drive the expansion of marine-based industries, the demand for skilled underwater welders capable of meeting diverse project requirements remains consistently high.
Environmental Impact and Regulations
The environmental impact of underwater welding is a significant consideration that necessitates adherence to stringent regulations and best practices. Efforts to minimize the ecological footprint of underwater welding operations include the implementation of measures to prevent the release of contaminants into marine ecosystems and the responsible disposal of waste materials. Additionally, environmental assessments and monitoring play a crucial role in ensuring that underwater welding activities are conducted in a manner that safeguards the health of aquatic environments and marine life.
Regulatory frameworks governing underwater welding operations are established to uphold environmental standards and mitigate potential risks to marine ecosystems. Compliance with these regulations requires a proactive approach to environmental management, encompassing the implementation of pollution prevention measures, the utilization of environmentally friendly welding materials, and the adoption of sustainable practices throughout the lifecycle of underwater welding projects. By prioritizing environmental stewardship, underwater welders and industry stakeholders contribute to the preservation of marine environments for future generations.
Advancements and Future Trends in Underwater Welding
The evolution of underwater welding continues to be shaped by advancements in technology, materials, and industry practices, paving the way for innovative solutions and enhanced capabilities. As the demand for underwater welding services grows across diverse sectors, research and development efforts focus on improving the efficiency, safety, and environmental sustainability of underwater welding operations. Advancements in welding equipment, such as the development of robotic underwater welding systems and advanced remote monitoring technologies, contribute to the automation and precision of welding tasks in challenging underwater environments.
Future trends in underwater welding also encompass the integration of digital technologies, such as augmented reality (AR) and virtual reality (VR) systems, to enhance welder training and facilitate real-time collaboration in underwater welding projects. The use of advanced materials and coatings designed to withstand corrosive marine conditions further enhances the longevity and performance of underwater welds, contributing to the resilience of marine infrastructure.
As the boundaries of underwater welding continue to be pushed by technological innovation, the outlook for the industry points toward increased efficiency, safety, and sustainability in meeting the evolving needs of marine-based projects.
Final Thoughts
The diverse types of underwater welding techniques and their applications reflect the dynamic intersection of technology and the marine environment. From the intricate challenges of wet and dry welding to the precision of hyperbaric welding, each method contributes to the maintenance, construction, and exploration of critical infrastructure beneath the waves.
As the industry continues to evolve, the demand for skilled underwater welders equipped with the expertise to navigate the complexities of underwater welding operations remains essential. By embracing innovation, upholding safety standards, and prioritizing environmental stewardship, the future of underwater welding holds promise for sustainable advancements in marine engineering and exploration.