Welding is a crucial process in many industries, ranging from automotive and aerospace to construction and fabrication. As such, it is essential to know the different welding techniques available and which one to use for a particular project. Two popular welding techniques are laser welding and MIG welding.
Laser welding uses a high-energy beam of light to melt and fusion two materials together. MIG welding, on the other hand, uses a consumable wire electrode to join two materials together. Both techniques have their advantages and disadvantages, and understanding these differences is essential when selecting the best method for a particular application.
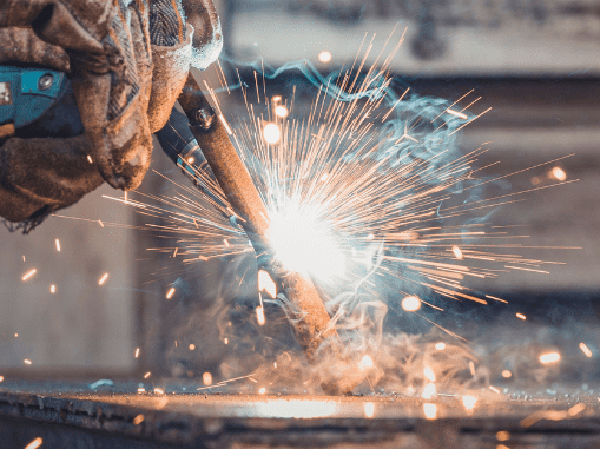
What is Laser Welding?
Laser welding is a process that uses a high-powered laser beam to melt and fuse two or more materials together. The laser beam provides a concentrated heat source that can quickly and accurately melt the materials, creating a strong bond between them.
The process of laser welding involves the use of a laser, which emits a beam of light that is highly focused and coherent. The laser can be programmed to move along a specific path, allowing it to target specific areas of the material being welded. As the laser beam melts the material, a weld pool is formed, which then solidifies to create a bond between the two pieces of material.
Laser welding offers several advantages over other welding techniques. One major advantage is its precision. The laser beam can be fine-tuned to create a very narrow weld seam, which reduces the amount of material that needs to be melted. This precision also reduces the amount of heat that is introduced to the material, which can help to minimize distortion and warping. Additionally, laser welding provides a fast and efficient welding process, making it ideal for high-volume production environments.
Other advantages of laser welding include:
- Excellent weld quality
- Ability to weld dissimilar materials
- Minimal or no post-weld cleanup required
- Low heat input, reducing the risk of thermal distortion or damage to the material
- Narrow weld seam, reducing material waste
- High welding speeds, making it ideal for high-volume production
Laser welding is a highly efficient and precise welding method that offers many benefits over traditional welding techniques.
What is MIG Welding?
Metal Inert Gas (MIG) welding is a welding process that uses a spool of wire fed through a welding gun to create a weld. A shielding gas is also used to protect the weld from contamination and oxidation.
MIG welding is a versatile process that can be used to weld a variety of metals, including steel, stainless steel, and aluminum. This process is commonly used in industries such as construction, fabrication, and automotive repair due to its cost-effectiveness and suitability for large-scale applications.
One of the key advantages of MIG welding is its ease of use. The process can be performed by relatively unskilled operators, making it a popular choice for many applications. MIG welding also allows for welding of thicker materials, making it a suitable technique for heavy-duty applications.
Advantages of MIG Welding
Advantages | Description |
---|---|
Versatility | MIG welding can be used to weld a variety of metals, making it a versatile process. |
Cost-effectiveness | MIG welding is a relatively inexpensive process, making it a popular choice for many industries. |
Suitable for large-scale applications | MIG welding allows for high productivity, making it a good choice for large-scale projects. |
Easy to use | The process can be performed by relatively unskilled operators, making it a popular choice for many applications. |
Ability to weld thicker materials | MIG welding allows for welding of thicker materials, making it a suitable technique for heavy-duty applications. |
Despite its advantages, MIG welding also has some limitations and challenges. The process can result in higher heat input, which can lead to distortion of the weld and potential for welding defects. MIG welding also requires a higher level of skill to produce high-quality welds, which can be a challenge for some operators.
Pros of Laser Welding
Laser welding offers numerous benefits that make it ideal for a variety of applications.
Benefits | Applications |
---|---|
Precision welding | Medical devices, electronics, and jewelry |
Reduced heat input | Welding of thin materials, heat-sensitive components, and dissimilar materials |
Ability to weld dissimilar materials | Automotive and aerospace industries |
High accuracy and quality | Welding of intricate shapes and patterns, and automation purposes |
Laser welding is widely used in the automotive industry, especially for the production of body and powertrain components. It is also used in aerospace, electronics, and medical industries for its precision and accuracy.
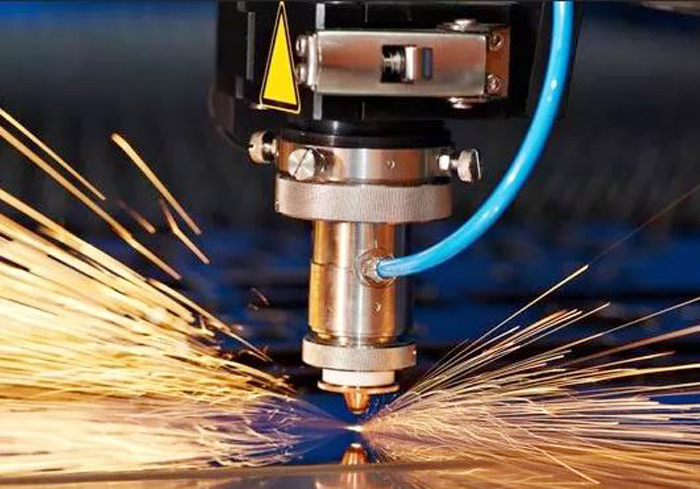
The reduced heat input of laser welding makes it ideal for welding of thin materials, heat-sensitive components, and dissimilar materials. Additionally, its ability to weld dissimilar materials is particularly useful in the automotive and aerospace industries.
The high accuracy and quality of laser welding make it an excellent choice for welding of intricate shapes and patterns. It is also an ideal process for automation purposes.
Pros of MIG Welding
MIG welding offers a variety of benefits that make it a popular choice for various applications. Here are some of its key pros:
Ability to weld thicker materials
MIG welding can weld materials ranging from thin gauge to thick plate. This makes it a suitable technique for welding materials of varying thicknesses, which is often required in the fabrication and construction industries.
Versatility in welding different types of metals
MIG welding can weld a variety of metals, including stainless steel, aluminum, nickel, and copper alloys. This versatility makes it a reliable choice for welding different types of metals in numerous applications.
Cost-effectiveness
MIG welding equipment is relatively inexpensive, and the cost of consumables such as wire and gas is also low. This makes it an affordable option for smaller businesses or those with limited budgets.
These benefits make MIG welding a popular choice for various industries. Let’s take a closer look at some of its applications:
Industry | Application |
---|---|
Construction | Fabrication of structural steel, handrails, and fences |
Fabrication | Manufacturing of metal products, machinery, and tools |
Automotive Repair | Repair of car frames, exhaust systems, and body panels |
As the above table illustrates, MIG welding is widely used in a variety of industries due to its versatility and cost-effectiveness. It is an ideal choice for welding thicker materials and different types of metals for various applications.
Cons of Laser Welding
While laser welding offers many benefits, it also has its limitations and challenges. These include:
- Higher initial investment cost: Laser welding equipment can be expensive to purchase and maintain, making it less accessible for smaller businesses or projects with lower budgets.
- Sensitivity to surface conditions: Laser welding requires precise alignment between the laser and the material being welded. Any surface imperfections or irregularities can interfere with the welding process and compromise the quality of the weld.
- Limited access: Laser welding can be difficult or impossible to perform in certain situations where access is restricted, such as in narrow or hard-to-reach areas.
Additionally, some materials are more difficult to weld with laser welding than with other techniques. For example, highly reflective materials like copper and aluminum can reflect the laser beam, leading to inconsistent welds and increased risk of damage.
Despite these limitations, laser welding continues to be a popular choice for a wide range of applications. By carefully considering the specific requirements of a project and choosing the right equipment and techniques, the challenges of laser welding can be overcome.
Cons of MIG Welding
While MIG welding is a versatile and cost-effective welding technique, it does come with some limitations and challenges that users should be aware of. These include:
Higher heat input
MIG welding can produce higher levels of heat, which may not be suitable for thin materials or materials that are sensitive to heat. This can lead to warping, distortion, and weak welds.
Potential for welding defects
When performing MIG welding, there is a higher risk of welding defects such as porosity, lack of fusion, and undercutting. Proper preparation, techniques, and quality control measures are critical to avoid these issues.
Need for skilled operators
MIG welding requires skilled operators who can adjust the welding parameters based on the material thickness, position, and joint type. Inadequate training or experience can lead to poor-quality welds and safety hazards.
In order to address these challenges, it is important to use appropriate equipment and consumables, follow proper welding procedures, and ensure proper training and certification for operators. Being aware of these limitations can help you make informed decisions when selecting a welding technique for your project.
Ideal Applications for Laser Welding vs MIG Welding
Both laser welding vs MIG welding have their respective strengths and weaknesses, which make them suitable for different applications. Here we’ve identified the ideal applications for each technique:
Applications for Laser Welding
Industry | Application |
---|---|
Automotive | Welding of body parts, suspension assemblies, and exhaust systems. |
Aerospace | Welding of engine parts, fuel systems, and landing gear components. |
Electronics | Welding of microelectronics, sensors, and medical devices. |
Laser welding is particularly useful in industries that require high-precision welding, such as electronics and medical device manufacturing. It is also beneficial in situations where the material being welded is difficult to handle, or where access is limited. Its ability to weld dissimilar materials makes it a popular choice in the automotive and aerospace industries.
Applications for MIG Welding
Industry | Application |
---|---|
Construction | Welding of structural components, pipes, and heavy machinery. |
Fabrication | Welding of metal furniture, gates, and fences. |
Automotive repair | Welding of vehicle frames, exhaust systems, and trailer hitches. |
For industries that require welding of thicker materials or large-scale projects, MIG welding is an ideal choice. It is also versatile in welding different types of metals, making it a popular choice in the construction and fabrication industries. MIG welding is also cost-effective, making it a suitable choice for smaller-scale projects.
Overall, the choice between laser welding vs MIG welding will depend on the specific requirements of the project, including the type and thickness of the material being welded, the required accuracy, the budget, and the skill level of the operator.
Choosing the Right Welding Technique for Your Project
It’s crucial to consider the specific needs of each project before deciding on a welding technique. For applications that require high accuracy and minimal distortion, laser welding may be the best option. Industries such as automotive, aerospace, and electronics benefit greatly from this process.
For applications that prioritize versatility, cost-effectiveness, and thicker material welding, MIG welding may be the better choice. It is widely used in construction, fabrication, and automotive repair industries.
Final Thoughts and Conclusions
After exploring the differences between laser welding and MIG welding, it is clear that both techniques have their own advantages and limitations. Choosing the right welding process depends on various factors, such as the project requirements, available resources, and industry-specific applications.
While laser welding is known for its precision, speed, and ability to weld dissimilar materials, it requires a significant initial investment and is sensitive to surface conditions. On the other hand, MIG welding is versatile, cost-effective, and suitable for large-scale applications, but it produces a higher heat input and requires skilled operators.
Understanding the differences between laser welding vs MIG welding and their respective strengths and limitations is critical to selecting the best welding technique for each project. By considering the specific requirements of each application, project managers and engineers can make informed decisions that lead to successful outcomes.
FAQ’s
What is laser welding?
Laser welding is a process that uses a high-energy laser beam to join or fuse materials together. The laser beam melts the materials at the joint, creating a strong, precise weld.
What is MIG welding?
MIG welding, short for Metal Inert Gas welding, is a process that uses an electric arc and a consumable wire electrode to join materials together. The electrode melts and fuses the materials, creating a weld.
What are the advantages of laser welding?
Laser welding offers several advantages, including high precision, fast welding speed, and minimal distortion. It is also capable of welding dissimilar materials and is widely used in industries such as automotive, aerospace, and electronics.
What are the advantages of MIG welding?
MIG welding is known for its versatility, cost-effectiveness, and suitability for large-scale applications. It can weld thicker materials, handle different types of metals, and is commonly used in industries such as construction, fabrication, and automotive repair.
What are the limitations of laser welding?
Laser welding has some limitations, including the initial investment cost for equipment, sensitivity to surface conditions, and limited access in certain applications. It requires skilled operators and may not be suitable for all welding projects.
What are the limitations of MIG welding?
MIG welding has limitations such as higher heat input, potential for welding defects, and the need for skilled operators. It may not be as precise as laser welding and is not ideal for all types of materials or projects.
When should I choose laser welding or MIG welding?
The choice between laser welding vs MIG welding depends on the specific requirements of your project. Laser welding is well-suited for applications that demand high precision and weld quality, especially in industries like automotive and electronics. MIG welding, on the other hand, is more versatile and cost-effective, making it a popular choice for construction, fabrication, and repair projects involving thicker materials. Consider your project’s needs, materials, and available resources to determine the most suitable welding technique.