Have you ever wondered how automated welding systems achieve excellent seam quality and precision? The answer lies in welding seam tracking technology. What is welding seam tracking and how does it work? This technology enables real-time tracking of seams during the welding process, enhancing efficiency and productivity in automated welding systems.
In this article, we will explore the function and process of welding seam tracking. We will explain how this technology works and its significance in the welding process, particularly in automated welding. Keep reading to find out more about this game-changing technology and how it can benefit your welding operations.
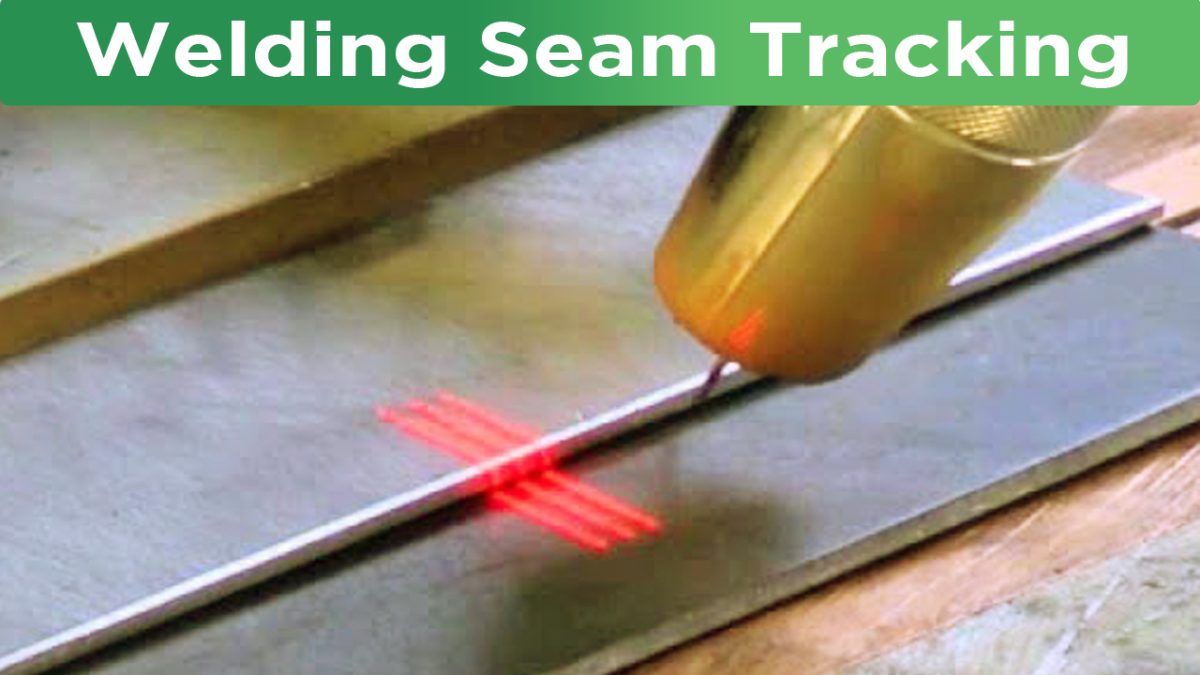
Image by toyotamaterialhandlingindia
What is Welding Seam Tracking?
Welding seam tracking is the process of using sensors to monitor and analyze the position and movement of the welding seam during the welding process. Real-time tracking enables the system to precisely follow seam positions, ensuring the welding torch remains at the correct angle and distance from the seam. This technology is widely used in welding technology, particularly in automated welding machines and robotic welding systems.
Robotic welding machines have become increasingly popular in manufacturing industries due to their speed, accuracy, and consistency. Welding seam tracking technology enhances these benefits by ensuring that the welding torch follows the seam perfectly, producing consistent quality welds without any errors. This level of accuracy and precision is vital in automated welding operations as it reduces scrap, improves productivity, and reduces defects.
How Does Welding Seam Tracking Work?
Welding seam tracking utilizes advanced technologies such as laser tracking and arc welding to track and locate seams during the welding process. This technology enables real-time tracking, providing accuracy and precision in ensuring optimal seam quality.
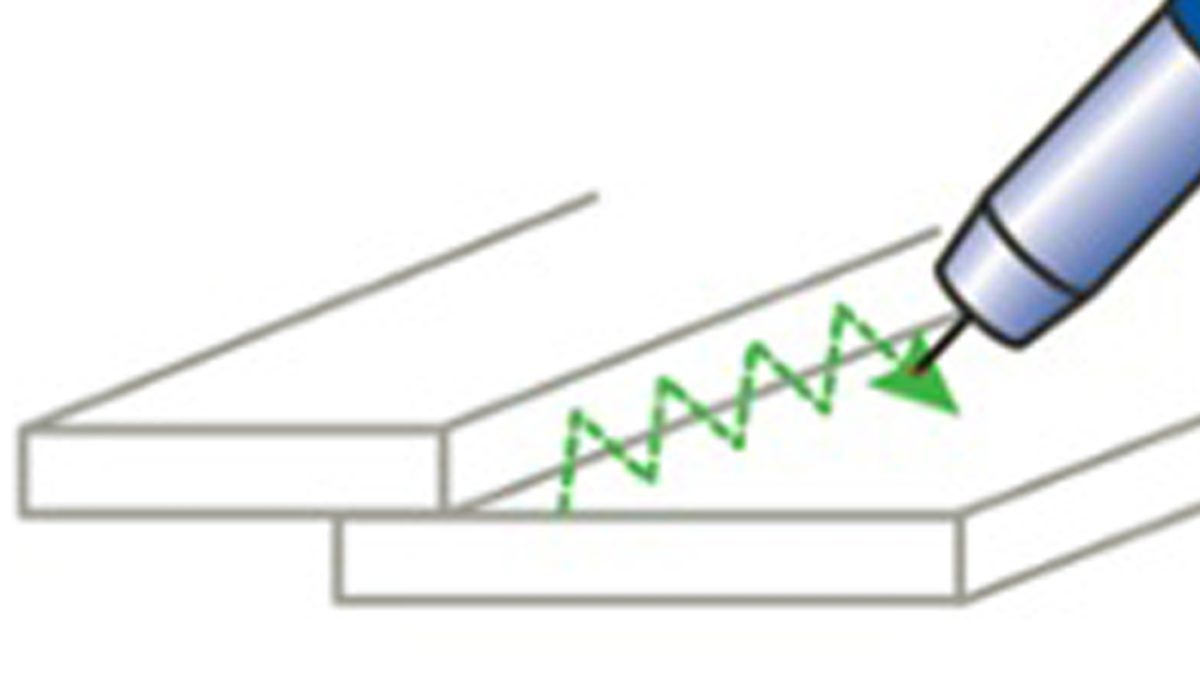
Image by motoman
Laser Tracking
Laser tracking involves the use of laser sensors to track the seam’s location during the welding process. The sensors detect discrepancies in the seam’s position, then adjust the welding parameters accordingly to ensure optimal welding quality. With the ability to operate in real-time, laser tracking provides accurate feedback on seam position and enables automated correction of the welding process, enhancing seam quality and minimizing errors.
Arc Welding
Arc welding utilizes an electric arc to generate heat, causing the metals to melt and fuse together. The process involves a robot that moves along the seam while an advanced computer system tracks the seam’s position. The system detects any deviations and adjusts the welding parameters accordingly, ensuring optimal seam quality. With the ability to track seams in real-time, arc welding ensures precision and accuracy in the welding process, minimizing errors and enhancing productivity.
Welding seam tracking technology is revolutionizing the welding process, enabling real-time tracking and providing the accuracy and precision required for optimal seam quality. Utilizing advanced technologies such as laser tracking and arc welding, it ensures efficiency and improves overall welding performance, particularly in the realm of automated welding operations.
Enhancing Welding Process Efficiency with Seam Tracking
Welding seam tracking is a crucial technology that enhances the efficiency of the welding process, particularly in automated welding operations. By utilizing real-time tracking, it enables precise and accurate tracking of seams, resulting in improved seam quality and overall productivity.
Automated welding systems with integrated seam tracking technology can significantly increase efficiency and reduce production costs by minimizing the time required for manual inspection and correction of errors. Additionally, the use of welding seam tracking ensures that the welding process is consistent, with a higher degree of accuracy and precision, resulting in better seam quality and ultimately, a higher-quality end product.
Seam tracking technology also helps improve safety conditions in welding applications as it helps reduce errors and enhance the accuracy of the welding process. Overall, the benefits of welding seam tracking make it an indispensable tool in modern-day welding operations.
Ensuring Superior Seam Quality with Welding Seam Tracking
Welding seam tracking plays a critical role in enhancing the overall quality of welding seams, particularly in robotic welding applications. This technology ensures high accuracy and precision, resulting in superior seam quality. Through real-time tracking, welding seam tracking allows for precise adjustment of the welding process, ensuring consistent and optimal seam quality. It eliminates the possibility of human error, resulting in better control of the welding process and higher quality outputs.
Welding seam tracking also significantly reduces the risk of incorrect positioning or misalignment during the welding process, which can lead to defects in the final product. By ensuring precise placement of welds, it significantly improves the strength and durability of the final product. Furthermore, welding seam tracking helps detect defects and inconsistencies in the welding process, enabling immediate action to correct the issue and prevent further defects. Hence, if superior seam quality is the priority, utilizing welding seam tracking technology in the welding process is a must.
Conclusion
Welding seam tracking technology offers several advantages for the welding process. It enables real-time tracking of seams and enhances the efficiency of the process, particularly in automated welding operations. The accuracy and precision provided by this technology ensure superior seam quality, which is of utmost importance in welding applications. Welding seam tracking also positively impacts overall productivity and performance.
The use of advanced tracking methods such as laser tracking and arc welding further adds to its significance in the welding industry. As such, welding seam tracking is an essential tool for improving welding operations and achieving optimal results.
FAQs
What is welding seam tracking?
Welding seam tracking is a technology used in the welding process to track and follow the seam in real-time. It ensures that the welding torch or electrode stays aligned with the seam, resulting in accurate and precise welds. This technology is particularly important in automated welding systems.
How does welding seam tracking work?
Welding seam tracking works by using sensors, cameras, or lasers to detect the position of the seam during the welding process. The system continuously collects data and adjusts the position of the welding torch or electrode, ensuring that it remains on track. This real-time tracking eliminates the need for manual adjustments and ensures consistent weld quality.
How does seam tracking improve the welding process?
Seam tracking improves the welding process by enhancing efficiency and productivity. It eliminates the need for manual adjustments, saving time and reducing errors. Additionally, by keeping the welding torch or electrode aligned with the seam, it improves the quality of the welds and reduces the chances of defects or inconsistencies.
How does welding seam tracking contribute to seam quality?
Welding seam tracking contributes to superior seam quality by ensuring accurate and precise welds. It eliminates the risk of misalignment or deviations from the intended path, resulting in uniform welds with minimal defects. This technology is particularly beneficial in robotic welding applications, where consistent seam quality is essential.
What are the benefits of using welding seam tracking in automated welding?
Using welding seam tracking in automated welding offers numerous benefits. It improves productivity by eliminating the need for manual adjustments and reducing downtime. It also enhances the quality of welds by maintaining precise alignment with the seam. Overall, it increases the efficiency of the welding process and allows for greater output in automated welding operations.