Gas Metal Arc Welding, commonly known as GMAW, is one of the most popular welding techniques used in various industries. GMAW is a welding process that uses a continuously fed metal electrode and a shielding gas to join two metal parts. But how does gas metal arc welding work? Let’s explore the fundamentals of this welding process and gain a deeper understanding.
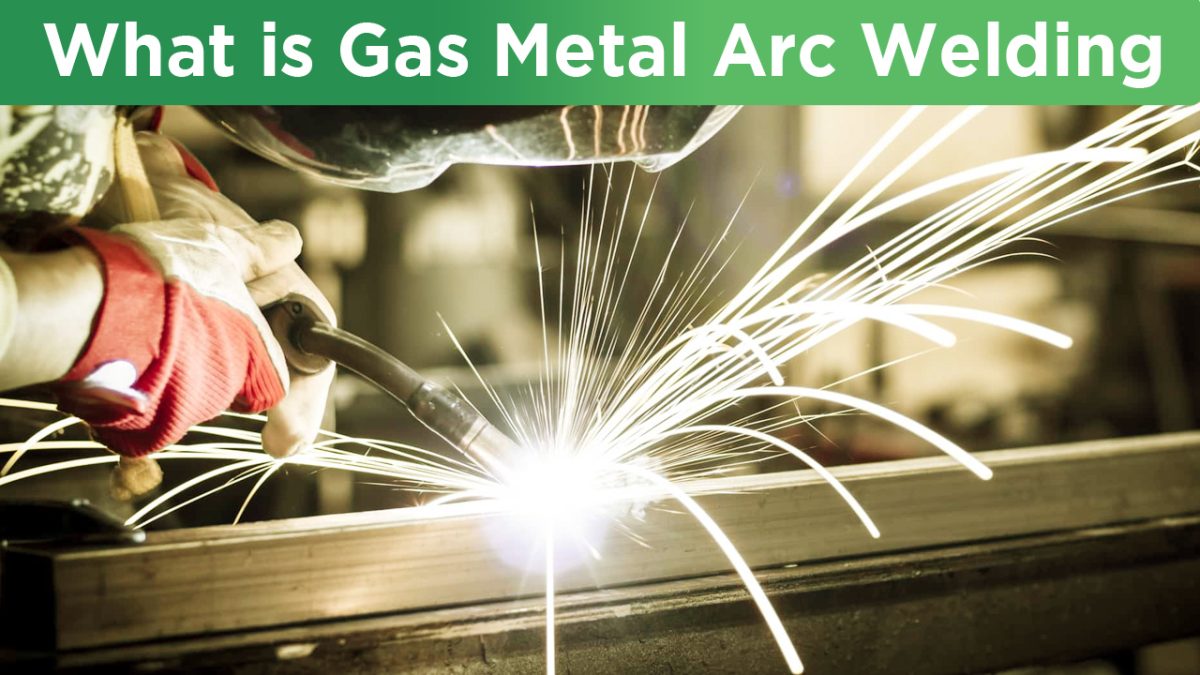
Gas Metal Arc Welding Process
Gas Metal Arc Welding, also known as Metal Inert Gas (MIG) welding, is a popular welding technique used in various industries to join metal parts together. The process involves the use of a continuous wire electrode, which is fed through a welding gun and melted by an electric arc, producing the heat required to join the metal parts.
The Gas Metal Arc Welding Process in Detail
The Gas Metal Arc Welding process can be broken down into several steps:
- Preparation: The metal surfaces that are to be joined are cleaned and prepared to ensure they are free from any contaminants.
- Power Supply: A power source is used to generate an electric arc that melts the wire electrode and the metal parts to be joined.
- Wire Feeder: The wire electrode is automatically fed through a wire feeder and into the welding gun.
- Shielding Gas: A shielding gas, usually comprised of a mixture of argon and carbon dioxide, is used to protect the molten metal from atmospheric contamination.
- Welding Gun: The welding gun, or torch, is used to control the wire feed speed and the amount of shielding gas flowing to the weld area.
- Welding: The electric arc melts the wire electrode and the metal parts, fusing them together to form a strong weld.
Gas Metal Arc Welding Equipment
The Gas Metal Arc Welding process requires several pieces of equipment, including:
Equipment | Function |
---|---|
Power Supply | Generates an electric arc for welding |
Wire Feeder | Automatically feeds the electrode wire into the welding gun |
Welding Gun | Controls wire feed speed and shielding gas flow |
Shielding Gas | Protects molten metal from atmospheric contamination |
Other equipment may include a wire spool holder, a regulator to control gas flow, and a ground clamp to attach to the metal workpiece.
Overall, the Gas Metal Arc Welding process is a reliable and efficient welding technique that produces high-quality welds. Whether you’re welding thin sheets or thick plates of metal, Gas Metal Arc Welding is an excellent choice for fusing metal parts together.
Gas Metal Arc Welding Equipment
Gas Metal Arc Welding (GMAW) requires several essential pieces of equipment. Let’s take a closer look at each one.
Welder
The welder is the primary piece of equipment required for GMAW. The welder provides the power to generate the welding arc and control the welding process parameters.
Wire Feeder
The wire feeder is responsible for feeding the wire electrode through the welding gun at a precise and constant speed. This component is essential for ensuring a consistent weld bead.
Welding Gun
The welding gun is the part of the equipment that holds the wire electrode and provides the shielding gas that protects the weld pool. The welding gun also controls the wire feed speed and the amperage of the welding arc.
Power Source
The power source is what provides the electricity needed to create the welding arc and heat the wire electrode. The power source can either be a constant voltage or a constant current power supply.
Shielding Gas
The shielding gas is used to protect the weld pool from contamination and oxidation during the welding process. A mixture of argon and carbon dioxide is the most commonly used shielding gas for GMAW.
Wire Electrode
The wire electrode is the material that is melted to form the weld pool. GMAW typically uses a solid wire electrode made of mild steel or stainless steel. However, there are also flux cored wire electrodes that can be used for welding thicker materials.
Equipment | Function |
---|---|
Welder | Generates the welding arc and controls welding process parameters |
Wire Feeder | Feeds wire electrode through welding gun at a precise and constant speed |
Welding Gun | Holds wire electrode and provides shielding gas, controls wire feed speed and amperage |
Power Source | Provides electricity to create welding arc and heat wire electrode |
Shielding Gas | Protects weld pool from contamination and oxidation during welding process |
Wire Electrode | Melted to form weld pool; typically made of mild or stainless steel, with flux-cored options for thicker materials |
Having the right equipment is crucial for achieving high-quality, consistent welds with GMAW. Each component must work together seamlessly to produce the desired results.
Advantages of Gas Metal Arc Welding
Gas Metal Arc Welding (GMAW) offers numerous advantages over other welding techniques. These advantages include:
- Speed: GMAW is a fast welding process, allowing for high productivity and efficient use of time.
- Versatility: GMAW can be used to weld a wide range of metals, including aluminum, stainless steel, and mild steel.
- Quality: GMAW produces high-quality welds with smooth, clean finishes. It also causes minimal distortion, resulting in less rework and fewer defects.
- Automation: GMAW can be easily automated, reducing the need for manual labor and increasing efficiency.
- Accessibility: GMAW equipment is widely available and easy to use, making it accessible to both professionals and hobbyists.
Overall, Gas Metal Arc Welding is a reliable and versatile welding technique that offers numerous advantages over other welding processes.
Disadvantages of Gas Metal Arc Welding
While Gas Metal Arc Welding (GMAW) offers many advantages, there are also some notable disadvantages to consider when choosing a welding technique. We will explore these drawbacks in detail below:
Equipment Complexity
The equipment required for Gas Metal Arc Welding can be more complex and expensive compared to other welding processes. The need for a constant voltage power supply, wire feeder, and shielding gas supply can add to the overall cost of the welding setup.
Accessibility
Not all locations or environments are suitable for Gas Metal Arc Welding. It requires a clean and dry area, and the presence of shielding gas can be impractical in outdoor or windy environments. The need for electricity also limits its use in remote locations.
Weld Quality
While Gas Metal Arc Welding can produce high-quality welds, it is not suitable for all materials. It may result in porosity if used on materials that are susceptible to oxidation, such as aluminum, and may also produce weld spatter.
Cost
The cost of the equipment and consumables for Gas Metal Arc Welding can be higher compared to other welding processes. The need for shielding gas and the continuous feeding of the welding wire can add to the overall cost.
Skills Required
Gas Metal Arc Welding requires a high level of skill and experience to achieve consistent and quality welds. The welder needs to have a good understanding of the welding parameters and techniques to produce welds that meet the required standards.
While Gas Metal Arc Welding has its limitations and drawbacks, it is still a highly versatile and widely used welding technique in various industries. Proper training, equipment maintenance, and selection of appropriate welding parameters can help minimize the disadvantages and ensure successful welds.
Gas Metal Arc Welding Parameters
Gas Metal Arc Welding (GMAW) requires precise control of various parameters to achieve optimal results. The following are the crucial parameters:
Parameter | Description |
---|---|
Voltage | The electrical potential difference between the welding torch and the workpiece, affecting the heat input into the weld. |
Current | The flow of electrical current through the torch and the wire, affecting the depth of penetration and the size of the weld puddle. |
Wire Feed Speed | The rate of wire feed, affecting the weld deposition rate, the shape and size of the weld bead, and the penetration depth. |
Shielding Gas Selection | The gas used to shield the weld from the atmosphere, affecting the weld quality, appearance, and spatter level. |
Proper selection and adjustment of these parameters are crucial for achieving consistent, high-quality welds. Deviations from the optimal values can result in issues such as poor penetration, porosity, or cracking.
- Too high voltage can lead to excessive heat input and distortion, while too low voltage can result in incomplete fusion and lack of penetration.
- Too high current can cause excessive spatter and burn-through, while too low current can lead to poor fusion and lack of penetration.
- Too high wire feed speed can create an irregular weld bead and poor fusion, while too low wire feed speed can result in inadequate weld deposition and poor penetration.
- Improper shielding gas selection can cause defects such as porosity, contamination, or undercutting.
Hence, welders must carefully adjust the parameters based on the type and thickness of the base metal, the desired weld size and shape, and the welding position and technique. Experience and skill are key factors in achieving optimal GMAW performance and avoiding defects.
Conclusion
Gas Metal Arc Welding (GMAW) is a popular and versatile welding technique used in various industries. This process involves the use of a consumable wire electrode and a shielding gas to produce high-quality welds that are both strong and durable.
One of the key advantages of GMAW is its speed – this welding technique allows for high welding speeds, making it an efficient and cost-effective option for many applications. Additionally, GMAW is highly versatile and can be used on a wide range of materials, including aluminum, stainless steel, and carbon steel.
However, like any welding process, GMAW has its limitations and potential drawbacks. One of the main disadvantages of GMAW is the cost and complexity of the equipment required, as well as the need for a constant supply of shielding gas.
When using GMAW, it is important to consider various parameters, including voltage, current, wire feed speed, and shielding gas selection. By carefully selecting and adjusting these parameters, you can achieve optimal results and produce high-quality welds that meet your specific needs and requirements.
In conclusion, if you are looking for a versatile and efficient welding technique that can be used on a wide range of materials, Gas Metal Arc Welding may be the right choice for your project. With the right equipment, parameters, and techniques, you can achieve outstanding results and produce welds that are strong, durable, and precise.
FAQ
What is Gas Metal Arc Welding? How Does It Work?
Gas Metal Arc Welding (GMAW) is a welding process that uses a continuous and consumable wire electrode, along with a shielding gas, to create a weld. The wire electrode is fed through a welding gun, while the shielding gas protects the weld from contamination. The electrical current is passed through the wire and creates an arc between the electrode and the base material, melting them and forming a weld.
What is the Gas Metal Arc Welding Process?
The Gas Metal Arc Welding process involves several steps. First, the welding machine is set up with the appropriate voltage and wire feed speed. The workpiece and the welding gun are properly positioned. Then, an electrical current is passed through the wire electrode, creating an arc with the base material. The wire is continuously fed into the weld pool, and the shielding gas protects the weld from atmospheric contamination. The welding gun is moved along the joint, creating a continuous and consistent weld.
What Equipment is Used in Gas Metal Arc Welding?
Gas Metal Arc Welding requires several pieces of equipment, including a power source, a wire feeder, a welding gun, and a shielding gas supply. The power source provides the electrical energy for the welding process. The wire feeder delivers the consumable wire electrode to the welding gun. The welding gun holds the wire electrode and directs the shielding gas to the weld area. The shielding gas supply provides the necessary protection for the weld.
What are the Advantages of Gas Metal Arc Welding?
Gas Metal Arc Welding offers numerous advantages. It is a versatile welding process that can be used on a variety of materials and thicknesses. GMAW is known for its high welding speed, making it an efficient choice for many applications. Additionally, Gas Metal Arc Welding produces high-quality welds with good fusion and minimal spatter.
What are the Disadvantages of Gas Metal Arc Welding?
Although Gas Metal Arc Welding has many advantages, there are some potential drawbacks. The equipment required for GMAW can be complex and expensive, making it less accessible for some welders. Additionally, Gas Metal Arc Welding may not be suitable for certain applications, such as welding in windy or outdoor environments. Lastly, the use of shielding gas adds an additional cost and requires careful selection and management.
What Parameters are Important in Gas Metal Arc Welding?
Several parameters need to be considered in Gas Metal Arc Welding. The voltage and current settings impact the heat input and penetration of the weld. The wire feed speed determines the amount of filler metal being added to the weld pool. The type and composition of the shielding gas affect the weld quality and protection level. Proper selection and control of these parameters are crucial for achieving the desired weld characteristics.