When it comes to welding, there are various techniques available. Two of the most commonly used methods are gas welding and arc welding. While they may seem similar, they differ in several ways. This article will explore the key differences between gas welding vs arc welding, including their processes, advantages, and applications. By the end of this article, you will have a better understanding of which welding technique is best suited for your needs.
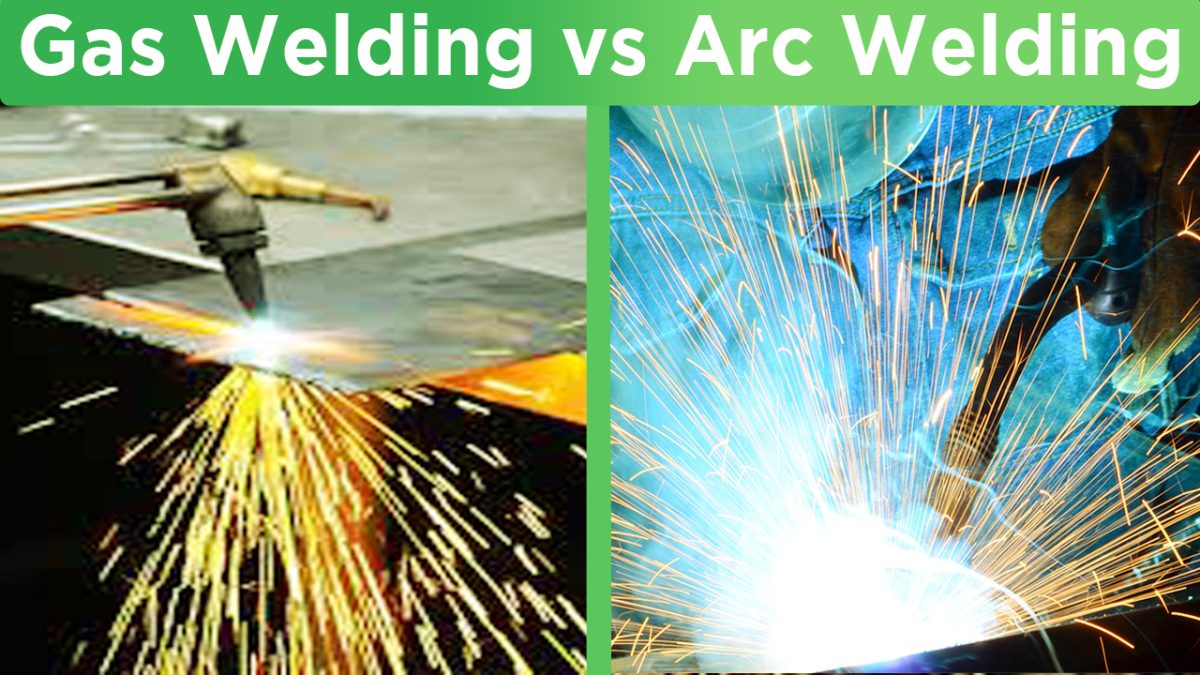
Gas Welding Process and Advantages
Gas welding is a welding process that uses a torch to heat a metal surface until it melts and forms a bond with another metal. The process is highly versatile and can be used to weld a wide range of thin and thick metals, such as aluminum, stainless steel, and mild steel. Gas welding is particularly useful for repairing parts, as it can create a strong and durable bond.
The gas welding process typically involves the use of an oxy-fuel torch, which is a tool that mixes two gases, oxygen and acetylene, to create a hot flame. The torch is typically equipped with a set of regulators, which control the flow and pressure of the gases. The equipment required for gas welding is relatively inexpensive, making it a popular choice for beginners and hobbyists.
One of the main advantages of gas welding is its versatility. The process can be used in a wide range of applications, including automotive repair, construction, and metal fabrication. Gas welding is also a relatively clean process, producing minimal smoke or fumes. This makes it ideal for use in enclosed or indoor spaces. Additionally, because the heat is adjustable, gas welding can be used to weld metals of varying thicknesses.
Advantages of Gas Welding |
---|
Can be used to weld a wide range of metals |
Equipment is relatively inexpensive |
Produces minimal smoke or fumes |
Heat is adjustable |
Gas welding is a versatile and effective welding process that can be used to create strong bonds between metals. Whether you are a beginner or an experienced welder, gas welding is a skill that can be learned and mastered with time and practice.
Arc Welding Techniques and Materials
Arc welding is a widely used welding technique that requires a power source to create an electric arc between an electrode and the material being welded. Different arc welding techniques can be used based on the type of material and the welding process required.
Stick Welding
Also known as Shielded Metal Arc Welding (SMAW), Stick Welding is a popular arc welding technique that relies on a consumable electrode coated in flux to weld the material. Stick welding can be used with various materials such as steel, cast iron, and nickel alloys.
Metal Inert Gas (MIG) Welding
MIG welding utilizes a wire electrode that is fed through a spool at a constant rate and a shielding gas to protect the weld from oxidation. This technique is ideal for welding thin materials and can be used on steel, aluminum, and stainless steel.
Tungsten Inert Gas (TIG) Welding
TIG welding uses a tungsten electrode that does not melt during welding. This technique also uses a shielding gas to protect the weld pool. TIG welding produces a precise and clean weld and is ideal for welding thin materials such as aluminum, magnesium, and stainless steel.
Material | Arc Welding Techniques |
---|---|
Steel | Stick, MIG, TIG |
Aluminum | MIG, TIG |
Cast Iron | Stick |
Nickel Alloys | Stick |
Understanding the different arc welding techniques and materials is essential in choosing the right welding method for your project. Whether you are making repairs or fabricating new parts, each technique has its strengths and can be valuable assets in various welding scenarios.
Gas Welding Applications and Safety Precautions
Gas welding is a popular welding technique that is used in several industries. It is particularly useful for welding non-ferrous metals like aluminum, copper, and brass. Gas welding is also commonly used in plumbing, automotive repairs, and metal sculpture.
Although gas welding is a relatively safe process, it is still important to follow certain safety precautions to avoid accidents or injuries. The most crucial safety measure is to work in a well-ventilated area to prevent inhaling toxic gases. It is also essential to wear protective gear like welding helmets, gloves, and jackets to shield yourself from heat, sparks, and radiation.
Gas Welding Safety Precautions |
---|
Work in a well-ventilated area |
Wear protective gear like welding helmets, gloves, and jackets |
Avoid welding near flammable materials or gases |
Use a fire extinguisher or water hose nearby |
By following these safety measures, you can minimize the risk of accidents and ensure a safe working environment. When performing gas welding, it is also essential to inspect your equipment regularly to ensure it is in good working condition.
Overall, gas welding is a versatile and valuable welding technique for many applications. With proper safety measures in place, you can harness the benefits of gas welding while protecting yourself and others from harm.
Conclusion
After exploring the key differences between gas welding vs arc welding, it is clear that each technique has its unique advantages and applications. Gas welding is commonly used for welding thin sections of steel and non-ferrous metals, while arc welding is ideal for welding thicker materials and working in outdoor conditions.
When choosing between gas welding vs arc welding, consider the type of material you will be welding, the project requirements, and your personal skill level. It is important to follow safety precautions for both welding techniques, as they can pose potential hazards if proper measures are not taken.
In conclusion, both gas welding vs arc welding are valuable techniques that can be utilized for a range of welding projects. By understanding their differences and applications, you can choose the best welding method for your needs and achieve high-quality results. So, get your gear together and start welding with confidence!
FAQs
What is the difference between gas welding vs arc welding?
Gas welding involves using a flame produced by a mixture of fuel gas and oxygen to heat and melt the metals being joined. Arc welding, on the other hand, uses an electric arc between an electrode and the workpiece to create a weld. The main difference lies in the heat source and the welding process.
What are the advantages of gas welding?
Gas welding offers several advantages, including versatility, portability, and the ability to work with different types of metals. It is also suitable for both thick and thin materials, making it ideal for various applications.
How does the gas welding process work?
The gas welding process involves the use of a torch that combines a fuel gas, such as acetylene, with oxygen to create a flame. This flame is then directed at the workpiece to generate enough heat for the metals to melt and fuse together.
What are some arc welding techniques and materials?
Arc welding encompasses various techniques, including stick welding (SMAW), MIG welding (GMAW), and TIG welding (GTAW). The choice of materials used in arc welding depends on the specific technique and desired application, ranging from mild steel to more exotic alloys like aluminum and stainless steel.
What are some common applications of gas welding?
Gas welding finds application in several industries, including automotive, construction, and plumbing. It is commonly used for repairs, fabrications, and joining materials such as steel, copper, and brass.
What safety precautions should I follow while gas welding?
When performing gas welding, it is important to wear appropriate protective gear, including safety glasses, gloves, and flame-resistant clothing. Adequate ventilation is necessary to prevent the accumulation of hazardous gases. Additionally, ensuring proper equipment maintenance and adhering to proper handling and storage procedures for fuel gas and oxygen are crucial for safety.