If you’ve ever wondered about the feasibility of joining stainless steel and mild steel using this welding method, you’ve come to the right place. In this article, we will explore the possibilities and best practices for achieving a successful fusion between these two metals. Welding stainless steel to mild steel can be a challenging task, but with the proper welding techniques and precautions, it is definitely achievable. By understanding the composition and properties of these metals and utilizing the appropriate welding parameters, you can create a strong and reliable bond.
Flux core wire plays a crucial role in this process. Its versatility and ease of use make it a popular choice for welding stainless steel and mild steel. We will delve into the characteristics of flux core wire and its compatibility with these metals, providing you with valuable insights for your welding projects. Throughout this article, we will discuss the step-by-step process of preparing the materials, selecting the right welding parameters, and ensuring proper joint integrity. We will also address common challenges and provide troubleshooting tips to help you overcome any obstacles.
It’s important to be aware of the considerations and limitations when welding stainless steel to mild steel. Joint design, compatibility issues, and potential pitfalls should be taken into account to ensure successful outcomes for your welding endeavors.
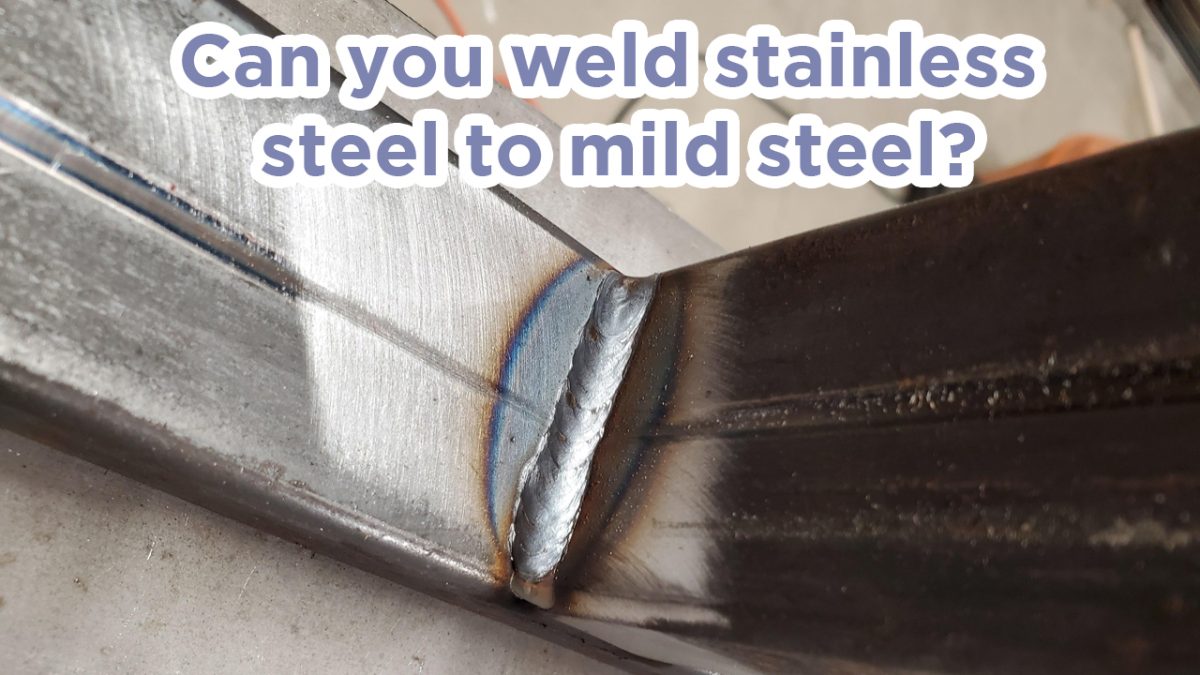
Photo by adalbon
Stainless steel and mild steel welding
Before attempting to weld stainless steel to mild steel, it is important to understand the fundamental differences between these two metals. The composition and properties of stainless steel and mild steel play a crucial role in determining the welding techniques and challenges involved in joining them together.
Composition and properties of stainless steel
Stainless steel is an alloy that contains iron, carbon, and a minimum of 10.5% chromium. This high chromium content provides stainless steel with its unique corrosion-resistant properties, making it suitable for various applications in industries such as construction, automotive, and aerospace. Stainless steel also offers excellent strength and heat resistance, making it a popular choice for welding projects.
Composition and properties of mild steel
Mild steel, on the other hand, is a low-carbon steel variant that lacks the chromium content found in stainless steel. It is known for its affordability, versatility, and ease of weldability. Mild steel is commonly used in structural applications, automotive components, and general fabrication.
Challenges in welding stainless steel and mild steel
Welding stainless steel to mild steel presents a unique set of challenges due to the differences in their composition and properties. The main challenge arises from the potential for carbon migration from the mild steel to the stainless steel during the welding process. This can result in a zone of reduced corrosion resistance known as “sensitization.” The weld joint may also experience differences in thermal expansion and contraction, which can lead to cracking or distortion.
Additionally, stainless steel and mild steel have different melting points and thermal conductivities, requiring careful consideration of welding parameters such as heat input, voltage, and wire feed speed.
By understanding these challenges and taking appropriate precautions, it is possible to achieve successful welds between stainless steel and mild steel. In the following sections, we will discuss the use of flux core wire, best practices, and considerations when welding these two metals together.
Flux core wire for stainless steel and mild steel welding
When it comes to welding stainless steel to mild steel, flux core wire is an excellent choice that offers versatility and ease of use. Flux core wire contains a flux compound that shields the weld pool from oxygen, preventing oxidation and ensuring a strong and clean weld.
What makes flux core wire particularly suitable for stainless steel and mild steel welding is its ability to provide effective shielding without the need for an external shielding gas. This makes it more convenient and cost-effective compared to other welding methods.
Flux core wire for stainless steel and mild steel welding is available in different types and sizes, ensuring compatibility with various applications and thicknesses of metal. It is essential to select the appropriate wire diameter and composition based on the specific welding project to achieve optimal results.
The table below provides a comparison of commonly used flux core wires for welding stainless steel and mild steel:
Flux Core Wire Type | Composition | Wire Diameter | Recommended Applications |
---|---|---|---|
ER308L | Stainless Steel | 0.030″, 0.035″ | Joining stainless steel to stainless steel or mild steel |
ER309L | Stainless Steel | 0.030″, 0.035″ | Joining stainless steel to stainless steel or mild steel with higher carbon content |
E71T-11 | Mild Steel | 0.030″, 0.035″ | Joining mild steel to mild steel |
It is crucial to follow the manufacturer’s recommendations regarding the welding parameters, such as wire feed speed and voltage, for the specific flux core wire being used. Properly adjusting these parameters ensures optimal performance and minimizes the risk of defects.
In the next section, we will discuss the best practices for welding stainless steel to mild steel with flux core wire, including preparation techniques and troubleshooting tips to overcome challenges that may arise during the welding process.
Best practices for welding stainless steel to mild steel with flux core wire
Welding stainless steel to mild steel requires careful planning and execution to ensure a strong and reliable fusion. By following the best practices listed below, you can achieve successful welds between these two metals using flux core wire.
Step-by-Step Process:
- Preparation of Materials:
- Choosing the Right Flux Core Wire:
- Setting the Welding Parameters:
- Ensuring Joint Integrity:
Common Challenges and Tips for Troubleshooting:
Even with careful planning, welding stainless steel to mild steel can present challenges. Here are some common issues and tips for troubleshooting:
Cracking
Welding stainless steel to mild steel can result in cracking due to the differences in thermal expansion and contraction rates. To minimize cracking, preheat the materials and utilize a low-hydrogen welding technique. Additionally, consider employing buttering techniques or using intermediate filler materials.
Porosity
Porosity, or the presence of gas pockets within the weld, can weaken the joint. To reduce porosity, ensure a clean welding environment and avoid excessive moisture. Utilizing the correct shielding gas, such as a high-purity argon-based mixture, can also help minimize porosity.
Burn-through
When welding stainless steel to mild steel, avoiding burn-through is crucial to maintaining the integrity of the joint. To prevent burn-through, adjust the welding parameters to achieve proper heat control. Employing a backstepping technique and using proper weld sequence can also help control heat buildup.
By adhering to these best practices and troubleshooting tips, you can successfully weld stainless steel to mild steel using flux core wire. Remember to always prioritize safety and consult welding professionals or experts if needed.
Considerations and limitations
When it comes to welding stainless steel to mild steel using flux core wire, there are important considerations and limitations to be aware of. Understanding these factors will help you make informed decisions and ensure successful welds.
Joint Design
Proper joint design plays a crucial role in welding stainless steel to mild steel with flux core wire. It is important to ensure a strong and secure joint that can withstand the demands placed on it. Consider factors such as the type of joint (lap joint, butt joint, T-joint), joint preparation (cleaning, beveling, and chamfering), and fit-up (gap and alignment).
Compatibility Issues
While flux core wire offers versatility, it is essential to consider the compatibility between the stainless steel and mild steel. The dissimilar nature of these two metals can lead to challenges such as differences in melting points, thermal expansion rates, and potential formation of brittle intermetallic compounds. Proper selection of flux core wire and welding parameters can help mitigate compatibility issues.
Potential Pitfalls
Flux core welding stainless steel to mild steel can pose certain pitfalls that need to be addressed. Some common issues include excessive spatter, incomplete fusion or penetration, and porosity in the weld. By understanding these potential pitfalls and implementing appropriate techniques, such as adjusting the wire feed speed, voltage, and travel speed, you can achieve high-quality welds.
Considerations | Actions |
---|---|
Joint Design | Properly prepare and fit-up the joint to ensure a strong and secure connection. |
Compatibility Issues | Select flux core wire and adjust welding parameters to mitigate compatibility challenges. |
Potential Pitfalls | Implement appropriate techniques and adjustments to overcome common welding issues. |
Conclusion
Welding stainless steel to mild steel with flux core wire is a viable option for achieving a strong and reliable fusion. By understanding the characteristics of these metals and adopting best welding practices, you can successfully join stainless steel and mild steel together.
Throughout this article, we have discussed the importance of comprehending the differences between stainless steel and mild steel before attempting to weld them. Proper joint preparation, including cleaning and removing any surface contaminants, is crucial for ensuring a successful weld.
Selecting the appropriate flux core wire is essential for achieving optimal results. Flux core wire offers versatility and ease of use, making it an ideal choice for welding stainless steel to mild steel. By following the recommended welding parameters and techniques, you can overcome compatibility issues and create durable welds.
Welding stainless steel to mild steel with flux core wire requires careful planning and attention to detail. From joint design to troubleshooting, having a thorough understanding of the process will lead to successful welds that meet your requirements. With practice and the implementation of best practices, you can confidently tackle the task of welding stainless steel to mild steel with flux core wire.