Flux core welding is an efficient and cost effective method of joining stainless steel. It is fast, easy to learn, and produces high quality results. This guide covers everything you need to know about flux core welding stainless steel exhaust. In this article you will discover the advantages of using flux core welding over other methods, learn about the different types of stainless steel weldable, and explore commonly used equipment for flux core arc welding stainless steel.
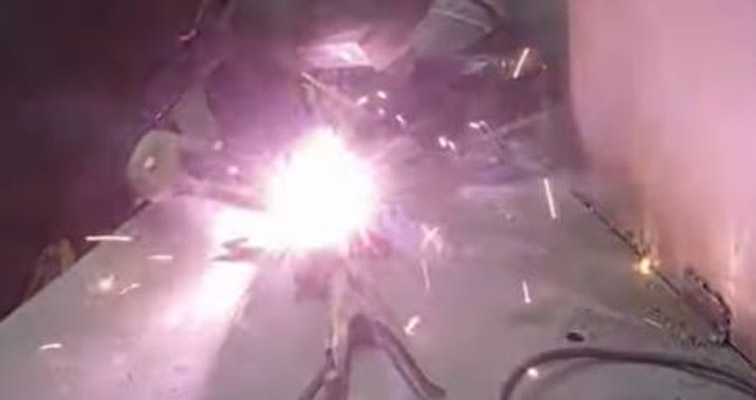
About is Flux Core Arc Welding
Flux core welding is a method of joining materials that is created by running a “flux” through a welding wire. This flux is a type of metal, gas, or liquid used to improve the welding process by removing impurities from the metal being welded. When the flux is passed through the welding wire, it reacts with the metal being welded, removing impurities from the metal. This process makes flux core welding ideal for joining stainless steel as it produces a weld that is more consistent, cleaner, and has less contaminants.
The most common type of flux used in welding is a chloride based flux. These fluxes are generally a liquid that is added to the welding wire as a liquid and then evaporates into a gas while the arc is forming. In order to join stainless steel and other types of metals, the welding wire needs to be coated with the chloride-based flux so it can be used to create a weld between the metal being welded and the welding wire.
Importance of Use Flux Core Arc Welding
Welding stainless steel with a flux core allows for cleaner results and a significant reduction in contaminants compared to gas or base metal arc welding. Welds made with a flux core will have less oxides, less sulphur, and less hydrogen in them compared to welds made with other types of welding. The difference in the welds between the two welding methods will be noted in how the weld feels in your hand and how the weld looks under a microscope. The most important reason to use flux core welding is the increased consistency of the welds. The welds made with a flux core will look very similar in appearance to each other as well as in the weld joints.
Some welders, who are new to flux core welding stainless steel exhaust, have difficulty with the look and feel of the welds they make. When stainless steel welds feel and look different than base metal welds, a lot of effort is required to change the welds to look and feel like base metal welds. The welds made with a flux core, though, will have consistent appearance and feel.
Types of Welding Stainless Steel
Shielded Metal Arc Welding (SMAW): SMAW is a standard welding process that is most commonly used to weld copper or aluminum alloys. SMAW is a very versatile process that can be used on a wide variety of materials including stainless steel. However, as a result of the type of welding it does and the type of steel used, SMAW welds are prone to cracking.
Flux Core Arc Welding: Flux core welding is the most common method used to weld stainless steel. It is suitable for welding a variety of different weldables including carbon steel, stainless steel, aluminum, and non-ferrous metals.
Gas Metal Arc Welding (GMAW): GMAW is an efficient and cost-effective method of joining ferrous metals used to weld ferrous metals, stainless steel, and non-ferrous metals. GMAW is also known as “power welding” as it produces high- quality results.
Essential Equipment Used for Flux Core Welding Stainless Steel Exhaust
Gas Welding Machine: When welding stainless steel, the most common type of welding machine used is the gas welding machine. Gas welding machines are capable of welding a variety of different materials including stainless steel. Many gas welding machines come standard with a carbon steel gas electrode for welding carbon steel and also a stainless steel gas electrode for welding stainless steel.
Arc Welder: Arc welders are capable of welding a wide variety of materials including stainless steel. Although these welders are capable of welding a variety of different welding materials, they are most commonly used to fuse stainless steel.
Stick Welder: Stick welders are capable of welding a variety of different welding materials including stainless steel. Stick welders, like stick welders for sale, are very compact and compact welders for sale.
Process of Flux Core Welding Stainless Steel Exhaust
SMAW is the most common welding method used to weld copper, aluminium, and stainless steel. The most common electrode used for welding stainless steel is a tungsten-iron arc (TIG) electrode. For welding stainless steel with a flux core, you will need a stainless steel wire and a carbon steel wire. These two wires will need to be combined together to create a welding wire. Place the two wires into the weld machine and weld them together to form a welding wire.
You can use any type of welding machine for welding, like a welder for sale. Place the welding wire into the wire feeder of the welding machine and weld the welded wire to the rod. If the welding wire is too small, grind the ends of the welding wire down using a grinding wheel or wire stripper.
Advantages of Flux Core Arc Welding Stainless Steel
Easier to Maintain: When welding stainless steel with a flux core, contaminants in the weld joint are easily removed due to the minimal amount of material inside the joint. This makes it easier to maintain the weld joint and lessens the amount of maintenance required.
Consistent Weld Joint: Due to the minimal amount of material in the weld joint, flux core welding produces a consistent weld joint. This makes the weld joint less likely to crack and is important for weld joints that are exposed to harsh conditions such as those found outdoors or underwater.
Cleaner Weld Joint: As flux core welding produces less contaminated weld joint, it is easier to clean the weld joint with less welding rod. This makes cleaning the weld joint easier and lessens the amount of cleaning required.
Higher Quality Weld Joint: Due to the consistent and clean weld joint produced by flux core welding, the weld joint will be higher in quality. This makes it easier to detect defects in the weld joint and is important for quality control.
Disadvantages of Fluctored Gas Metal arc welding stainless steel
Consistent Weld Joint: Flux core welding produces weld joints that are consistent in appearance and are less likely to crack. As a result, flux core welding produces consistent weld joints.
Cleaner Weld Joint: As flux core welding produces less contaminated weld joint, it is easier to clean the weld joint with less welding rod. This makes cleaning the weld joint easier and lessens the amount of cleaning required.
Higher Quality Weld Joint: Due to the consistent and clean weld joint produced by flux core welding, the weld joint will be higher in quality. This makes it harder to detect defects in the weld joint and is important for quality control.
Safety precautions while doing flux core welding
Before flux core welding stainless steel exhaust, check the welding equipment for any broken parts or cracks in the weld machine. Welding equipment that is damaged or cracked can cause an accident and could result in serious injury or death. Also, wear safety glasses when welding. Even if you are not wearing safety glasses, you should hold the welding gun as far from your face as possible to protect your eyes from splatter and hot shavings.
Tips Before Flux Core Welding Stainless Steel Exhaust
Gas welding stainless steel requires different welding procedures and equipment than welding other types of metals. For example, stainless steel requires a different gas than other types of metals to fuse it. Before welding stainless steel, make sure you understand the welding procedures used to weld that particular metal.
Before flux core welding stainless steel exhaust, make sure you understand the proper welding procedure to use and have the necessary welding equipment. Make sure you have enough welding rod to weld the weld joint you want to make. If a weld joint has been welded before, flux core welding will not change the appearance or performance of the weld joint.