When it comes to joining aluminium, welding has long been considered the go-to method. Welding can be complex and time-consuming, requiring specialized equipment and skilled operators. Fortunately, there are alternative methods available that allow you to join aluminium without the need for welding. In this article, we will explore some of these innovative techniques, offering durable results with ease.
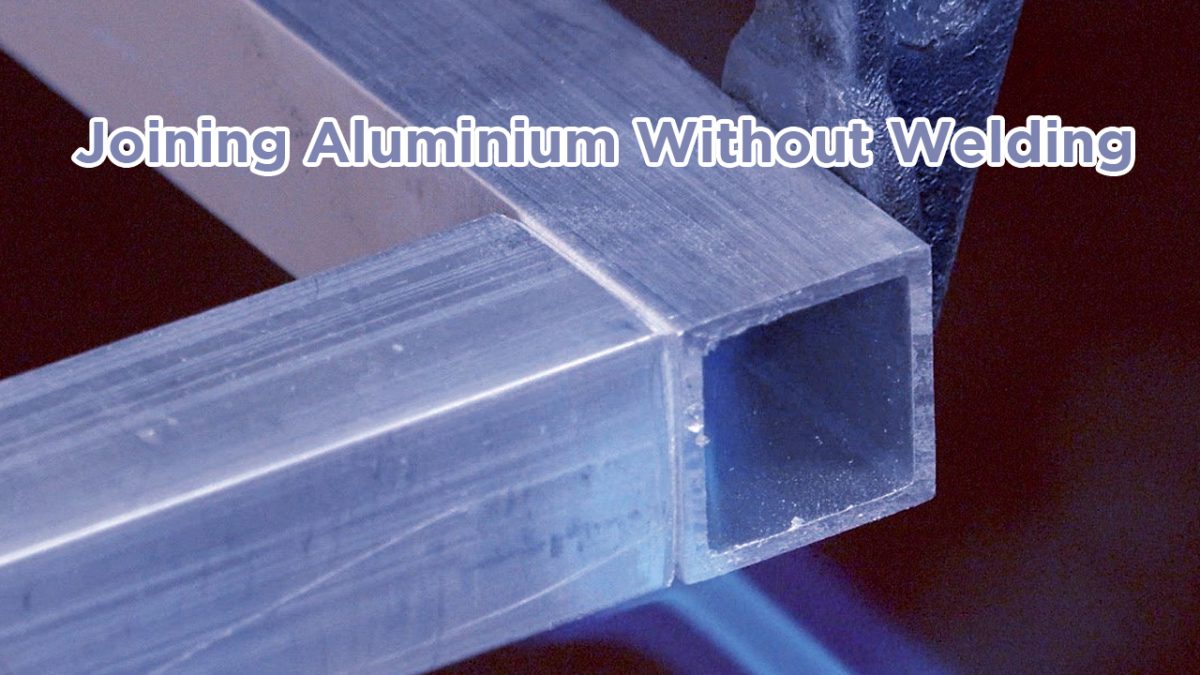
Photo by makesomething
Adhesive Bonding Aluminium
When it comes to joining aluminium, adhesive bonding offers a reliable and effective solution. With the right adhesive, such as epoxy-based adhesives specifically designed for aluminium bonding, strong and durable bonds can be achieved.
Adhesive bonding aluminium comes with several advantages. Firstly, it eliminates the need for welding, avoiding the potential for distortion or damage to the material. This makes it an ideal choice for joining lightweight aluminium structures that require precision and integrity.
Adhesive bonding provides a seamless and aesthetically pleasing appearance, as there are no visible welds or fasteners. This makes it particularly suitable for applications where the aesthetics play a critical role, such as architectural designs or consumer electronics.
When bonding aluminium with epoxy, it is important to consider a few key factors. Proper surface preparation is crucial to ensure the adhesive effectively bonds with the substrate. Cleaning the aluminium surface and applying a primer or pretreatment can enhance the bond strength.
Adhesive bonding is highly versatile, allowing for bonding of dissimilar materials, such as aluminium to plastics or composites. This opens up new possibilities for lightweight and multi-material designs.
Advantages of Adhesive Bonding Aluminium | Considerations for Adhesive Bonding Aluminium |
---|---|
– Eliminates the need for welding – Provides a seamless appearance – Enables bonding of dissimilar materials | – Proper surface preparation is crucial – Requires appropriate adhesive selection – Long curing times may be required for optimal bond strength |
Adhesive bonding offers a reliable and efficient method for joining aluminium. With the right adhesive selection and proper surface preparation, strong bonds can be achieved, providing structural integrity and a visually appealing finish. Consider adhesive bonding for your next aluminium assembly project.
Mechanical Fastening Aluminium
When it comes to joining aluminium structures, mechanical fastening methods offer a reliable and efficient solution. These techniques utilize mechanical components to create secure joints without the need for welding. In this section, we will explore two popular mechanical fastening methods for aluminium: riveting and clinching.
Riveting Aluminium
Riveting is a traditional method of mechanical fastening that has stood the test of time. It involves using solid cylindrical fasteners, called rivets, to hold together two or more aluminium pieces. The rivet is inserted into pre-drilled holes in the metal and deformed at the other end to form a mechanical lock, creating a tight bond between the components. Riveting is known for its strength and durability, making it suitable for applications that require a high load-bearing capacity.
One of the advantages of riveting aluminium is its versatility. It can be used in various industries, including aerospace, automotive, and construction, to join different aluminium alloys and thicknesses. Riveted joints offer excellent vibration resistance, ensuring the stability and longevity of the assembled structures.
Clinching Aluminium
Clinching is a modern method of mechanical fastening that offers several advantages over traditional riveting. It involves joining aluminium components using a combination of force and cold forming. Clinching uses a punch and a die to deform the metals, creating a mechanical interlock that holds the pieces together.
One of the main advantages of clinching is that it does not require any additional fasteners. This eliminates the need for rivets or other joining elements, reducing material and labor costs. Clinching also creates a flush joint, making it aesthetically pleasing and suitable for visible applications. Clinched joints provide excellent resistance to corrosion and fatigue.
Overall, mechanical fastening methods like riveting and clinching provide reliable and efficient solutions for joining aluminium without welding. Depending on your specific application requirements, you can choose between traditional riveting or modern clinching techniques to create strong and secure connections.
Mechanical Fastening Method | Advantages | Applications |
---|---|---|
Riveting | High strength and durability, versatility | Aerospace, automotive, construction |
Clinching | No additional fasteners required, flush joint, corrosion resistance | Various industries, visible applications |
Alternative Joining Techniques
When it comes to joining aluminium, traditional welding methods are not the only option. Alternative joining techniques such as friction stir welding aluminium, laser welding aluminium, and brazing aluminium offer unique advantages that are worth exploring. Let’s take a closer look at these innovative methods and their applications in the aluminium assembly process.
Friction Stir Welding Aluminium
Friction stir welding (FSW) is a solid-state joining technique that utilizes friction between a rotating tool and the workpiece to generate heat and plasticize the material. This method is especially suitable for joining aluminium, as it produces strong, defect-free welds with excellent mechanical properties. FSW is commonly used in industries such as automotive, aerospace, and shipbuilding, where high-quality joints are critical. Its advantages include minimal distortion, no filler materials required, and the ability to weld dissimilar aluminium alloys. However, FSW does have its limitations, such as limited joint thickness and the requirement for specialized equipment.
Laser Welding Aluminium
Laser welding is a precise and efficient joining technique that utilizes a high-energy laser beam to melt and join the aluminium pieces. It offers several benefits, including high welding speeds, narrow heat-affected zones, and minimal distortion. Laser welding is commonly used in industries that require precise control over weld dimensions and high-quality joints. However, the process can be sensitive to variations in material thickness and joint fit-up. Laser welding aluminium requires careful consideration of process parameters to ensure optimal results.
Brazing Aluminium
Brazing is a joining method that utilizes a filler material, typically in the form of a brazing alloy, to join aluminium pieces. The filler material is heated above its melting point but below the melting point of the base material, allowing it to flow and create a strong bond. Brazing offers several advantages, including good joint strength, lower heat input compared to welding, and the ability to join dissimilar metals. It is commonly used in the production of heat exchangers, automotive components, and electrical systems. However, brazed joints may have slightly lower mechanical properties compared to welded joints.
Comparison of Alternative Joining Techniques
Joining Technique | Advantages | Considerations |
---|---|---|
Friction Stir Welding Aluminium | Strong, defect-free welds No filler materials Ability to weld dissimilar alloys | Limited joint thickness Specialized equipment required |
Laser Welding Aluminium | High welding speeds Narrow heat-affected zones Minimal distortion | Sensitivity to material thickness and joint fit-up Process parameter optimization |
Brazing Aluminium | Good joint strength Lower heat input Ability to join dissimilar metals | Slightly lower mechanical properties compared to welding |
By exploring alternative joining techniques such as friction stir welding aluminium, laser welding aluminium, and brazing aluminium, manufacturers and engineers can expand their options for creating strong and reliable aluminium joints. These methods offer unique advantages and considerations that should be taken into account when selecting the most suitable technique for a specific application.
Conclusion
When it comes to joining aluminium without welding, there are several effective methods to choose from. Adhesive bonding offers a reliable and versatile solution, allowing for strong and durable bonds in aluminium structures. By using epoxy-based adhesives specifically designed for aluminium, you can ensure optimal adhesion and long-lasting results.
Mechanical fastening techniques such as riveting and clinching provide secure joints in aluminium assemblies. These methods offer simplicity and ease of installation, making them suitable for a wide range of applications. With proper selection and installation of mechanical fasteners, you can achieve robust connections in your aluminium projects.
For those looking for alternative joining techniques, friction stir welding, laser welding, and brazing provide unique advantages. Friction stir welding offers high strength and excellent weld quality, while laser welding provides precise and efficient joins. Brazing, on the other hand, allows for joining aluminium to other metals, expanding the range of possibilities for your assemblies.
The choice of joining method will depend on the specific requirements of your project. Consider factors such as load-bearing capacity, aesthetic appearance, and production efficiency. By understanding the benefits and limitations of each technique, you can make an informed decision and achieve successful results when joining aluminium without welding.
FAQ’s
How does adhesive bonding work for joining aluminium?
Adhesive bonding is a process in which an adhesive material is used to join two or more aluminium parts together. The adhesive creates a strong bond between the surfaces, eliminating the need for welding. Epoxy-based adhesives are commonly used for aluminium bonding due to their excellent bonding properties and durability.
What are the advantages of adhesive bonding aluminium?
Adhesive bonding offers several advantages for joining aluminium. It provides a uniform distribution of stress over the joint area, resulting in improved overall strength. Adhesive bonding also avoids the distortion and residual stress associated with welding. It allows for the joining of dissimilar materials and reduces the risk of corrosion caused by welding heat.
Can aluminium be joined using mechanical fastening techniques?
Yes, aluminium can be joined using various mechanical fastening techniques, such as riveting and clinching. Riveting involves the insertion of a rivet through pre-drilled holes in the aluminium parts, securing them together. Clinching, on the other hand, involves the use of a special tool to deform the metal in a way that interlocks the joint and creates a secure bond.
What are the benefits of using mechanical fasteners to join aluminium?
Mechanical fastening techniques offer several benefits for joining aluminium. They provide high strength and can withstand shear and tensile forces. These methods also allow for easy disassembly and reassembly, making them suitable for applications that require frequent maintenance or repairs. Mechanical fasteners do not require any heat input, reducing the risk of distortion or material damage.
What are some alternative techniques for joining aluminium without welding?
Alternative techniques for joining aluminium without welding include friction stir welding, laser welding, and brazing. Friction stir welding uses a rotating tool to create friction and heat, resulting in a forged joint between the aluminium parts. Laser welding utilizes a high-energy laser beam to melt and fuse the adjoining surfaces. Brazing involves using a filler metal to bond the aluminium parts under elevated temperatures.
How do I choose the most suitable method for joining aluminium without welding?
When selecting a method for joining aluminium without welding, consider the specific requirements of your project, including joint strength, durability, assembly complexity, and maintenance needs. Adhesive bonding provides flexibility and corrosion resistance. Mechanical fastening techniques offer high strength and easy disassembly. Alternative techniques like friction stir welding, laser welding, and brazing provide unique advantages depending on the application. Assess your priorities and consult with experts to determine the best method for your specific project.