Are you looking for ways to reduce shielding gas costs without compromising the quality of your welds? Well, you’re in luck! In this article, we will explore some effective strategies to help you achieve just that. Shielding gas plays a crucial role in the welding process, protecting the weld pool from atmospheric contamination, ensuring clean and strong welds. However, it can also be a significant expense, especially for businesses that rely heavily on welding.
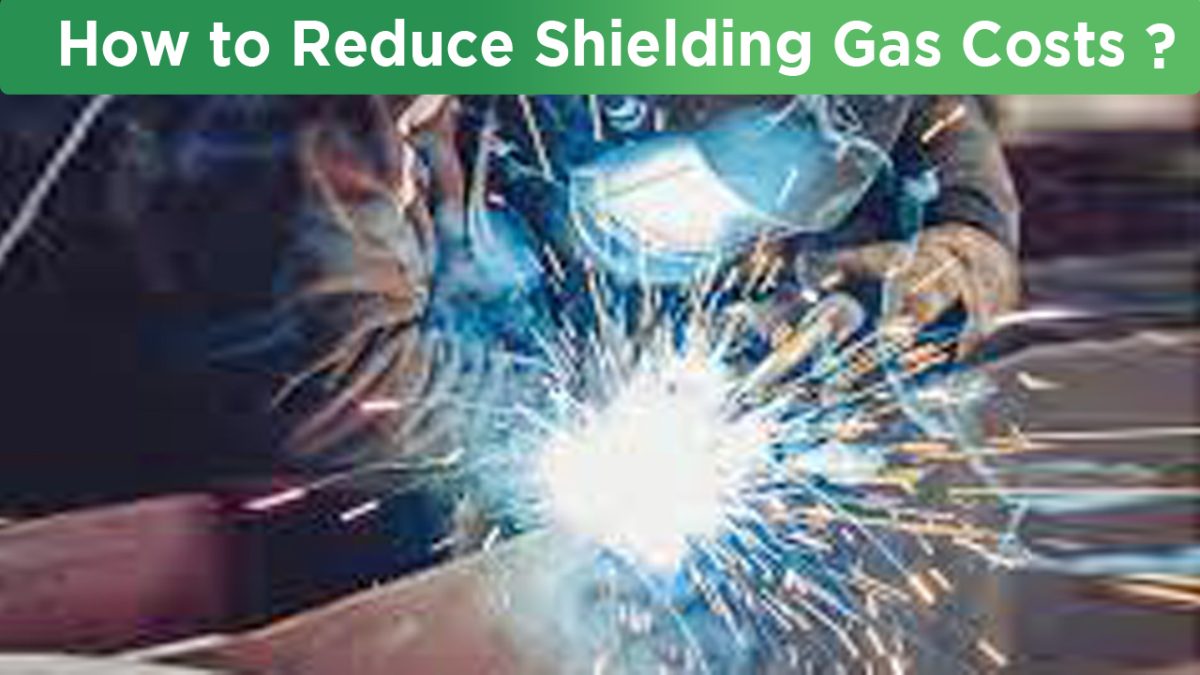
Luckily, there are several ways to optimize your shielding gas usage and save money without sacrificing weld quality. From selecting the right gas mixtures to adjusting flow rates and choosing efficient equipment, we will dive into practical tips and techniques that can help you achieve cost savings.
Importance of Shielding Gas in Weld Quality
Shielding gas is an essential component in the welding process, as it acts as a protective barrier around the weld pool, preventing it from coming into contact with the surrounding air. This is crucial because exposure to oxygen and other atmospheric gases can lead to defects in the weld, such as porosity, incomplete fusion, and excessive spatter.
The type of shielding gas used depends on the welding process and the materials being welded. Common shielding gases include argon, helium, carbon dioxide, and mixtures of these gases. Each gas has its own unique properties and is suitable for specific applications.
Factors Affecting Shielding Gas Costs
Several factors contribute to the overall cost of shielding gas, and understanding these factors can help you identify areas where cost savings can be achieved. Here are some key factors to consider:
Gas Mixtures: The composition of the shielding gas mixture can significantly impact its cost. Some gas mixtures, such as those containing helium, tend to be more expensive than others. It’s important to choose the right gas mixture that meets the requirements of your welding process while also considering the cost implications.
Gas Consumption: The amount of shielding gas consumed during the welding process directly affects the cost. Factors like weld size, welding technique, and joint design can influence gas consumption. By optimizing these factors, you can reduce gas usage and subsequently lower costs.
Gas Leakage and Waste: Gas leakage and waste can contribute to unnecessary costs. Poorly maintained equipment, worn-out hoses, and improper storage can lead to gas leaks and wastage. Regular inspection and maintenance of your gas equipment are crucial to minimize gas loss and save money.
Tips for Reducing Shielding Gas Costs
Now that we understand the importance of shielding gas and the factors that affect its cost, let’s explore some practical tips for reducing shielding gas costs without compromising weld quality.
Choosing the Right Shielding Gas for Your Welding Process
Selecting the appropriate shielding gas for your welding process is essential for achieving cost savings. Consider the material being welded, the welding technique, and the desired weld quality. Consult with welding experts or gas suppliers to determine the most suitable gas mixture that meets your requirements while also being cost-effective.
Proper Gas Flow Rate and Settings for Cost-Saving
Optimizing the gas flow rate and settings can significantly impact gas consumption and cost. Higher flow rates than necessary can lead to excessive gas usage, while lower flow rates may compromise weld quality. Consult the welding specifications and guidelines provided by the manufacturer to determine the recommended flow rates and settings for your specific welding application.
Regular Maintenance and Inspection of Gas Equipment
Regular maintenance and inspection of your gas equipment are crucial to minimize gas leakage and waste. Ensure that all connections are secure, hoses are in good condition, and regulators are functioning properly. Implement a preventive maintenance schedule to identify and address any issues before they escalate and result in unnecessary gas loss.
Utilizing Shielding Gas Alternatives
In some welding applications, it may be possible to substitute or partially replace shielding gas with alternatives that are more cost-effective. For example, in certain processes, flux-cored arc welding (FCAW) can be used instead of gas metal arc welding (GMAW) to eliminate the need for shielding gas altogether. Consider exploring such alternatives to achieve cost savings.
Monitoring Gas Usage and Waste Reduction Techniques
Implementing a system to monitor gas usage can provide valuable insights into consumption patterns and identify areas for improvement. By tracking gas usage per weld, per project, or per time period, you can identify potential waste and take corrective measures. Additionally, implementing waste reduction techniques, such as using gas flow control devices and reducing idle time, can further optimize gas usage and save costs.
Balancing Cost Savings and Weld Quality
Reducing shielding gas costs without compromising weld quality is a goal that many welders and businesses strive to achieve. By implementing the strategies discussed in this article, such as choosing the right gas mixtures, optimizing flow rates, conducting regular equipment maintenance, exploring gas alternatives, and monitoring gas usage, you can achieve significant cost savings while maintaining the integrity of your welds.
Remember, it’s essential to strike a balance between cost savings and weld quality. Cutting corners or compromising on the quality of your welds can have long-term consequences that outweigh any short-term cost savings. Therefore, always prioritize weld quality and consult with welding experts or gas suppliers for guidance specific to your welding applications.
Reducing shielding gas costs is not a one-size-fits-all approach, and it may require some trial and error to find the most effective strategies for your specific welding processes. However, with careful consideration, proper planning, and continuous improvement, you can achieve cost savings without compromising weld quality, ultimately benefiting your business’s bottom line.