Aluminum welding can be challenging, but it can also be a rewarding experience. With the right tools, techniques, and knowledge, you can tackle your next aluminum welding project with confidence. In this ultimate guide, we will explore the world of welding aluminum with flux core. We will cover everything from the basics of aluminum welding to advanced techniques, including tips and tricks for success.
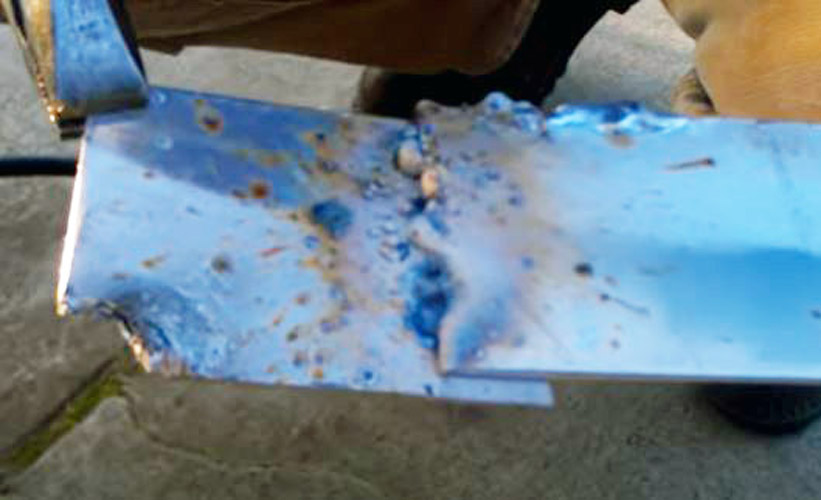
Photo by lpoiy
Understanding the metal properties
Before starting your welding, it’s essential to understand its unique properties. Aluminum has a high thermal conductivity, which means it will dissipate heat quickly. As a result, aluminum requires more heat input to melt and weld than other metals. Its low melting point also makes it prone to warping and distortion during the welding process. Aluminum has a thin oxide layer on its surface, which can make it difficult to weld. This oxide layer melts at a higher temperature than aluminum, which can create a barrier between the aluminum and the welding wire.
Benefits and limitations of flux core welding for aluminum
Flux core welding is a popular welding technique that uses a flux-filled wire to shield the weld from the surrounding air. Compared to other welding techniques, flux core welding offers several benefits for aluminum welding. For example, it allows for deeper penetration of the weld, which can create a stronger bond between the metals.
However, flux core welding also has its limitations. For instance, it produces more spatter than other techniques, which can make cleaning up the weld more challenging. Flux core welding requires more heat input than other techniques, which can increase the risk of warping and distortion.
Preparing for aluminum welding with flux core
Before you start welding aluminum with flux core, you need to prepare your workspace and materials. Start by cleaning the aluminum thoroughly to remove any kind of dirt, grease, or other contaminants. Use a stainless-steel brush to remove the oxide layer from the surface of the aluminum. This will help the welding wire to make contact with the aluminum and create a stronger bond.
Next, make sure you have plenty of ventilation in your workspace. Flux core welding produces a lot of smoke and fumes, which can be harmful if inhaled. Wear a respirator to protect yourself from the fumes.
Choosing the right equipment for aluminum welding with flux core
Welding aluminum with flux core as a beginners, you need to choose the right equipment. Start by selecting a flux core wire that is specifically designed for aluminum welding. These wires have a special flux core that helps to break through the aluminum oxide layer and create a strong bond between the metals. You will also need a welding machine that is capable of producing enough heat to melt the aluminum. Look for a machine with a high amperage output and a duty cycle that can handle the demands of aluminum welding.
Setting up your welding machine for aluminum welding with flux core
Once you have your equipment, it’s time to set up your welding machine for aluminum welding with flux core. Start by selecting the appropriate wire speed and voltage settings for your machine. These settings will vary depending on the thickness of the aluminum you’re welding and the diameter of the wire you are using. Adjust the amperage and arc length to achieve the proper penetration and heat input. It’s important to balance the heat input with the travel speed to avoid overheating the aluminum and causing warping or distortion.
How to weld aluminum with flux core wire
To weld aluminum with flux core wire, start by positioning the metal to be welded. Hold the welding gun at a slight angle to the workpiece, and start the arc by pulling the trigger. Move the welding gun in a circular motion to create a pool of molten metal. As you weld, make sure to maintain a consistent travel speed and maintain the proper distance between the welding gun and the workpiece. Use a weaving motion to create a wide bead that covers the joint thoroughly.
Techniques for welding aluminum with flux core
To achieve a successful weld, there are several techniques you can use when welding aluminum with flux core. One technique is to use a push-pull method, where you push the welding gun forward while pulling it back slightly. This helps to maintain a consistent distance between the welding gun and the workpiece.
Another technique is to use a backhand method, where you pull the welding gun towards you while maintaining a slight angle. This technique can help to reduce the amount of spatter produced during the welding process.
Common mistakes to avoid when welding aluminum with flux core
When welding aluminum with flux core, there are several common mistakes to avoid. One mistake is to use too much heat, which can cause warping and distortion of the metal. Another mistake is to weld too quickly, which can result in a weak or incomplete weld. It’s essential to avoid contaminating the aluminum with grease, oil, or other contaminants. These can create a barrier between the welding wire and the aluminum, making it difficult to create a strong bond.
Tips for achieving a successful weld
To achieve a successful weld when welding aluminum with flux core, there are several tips you can follow. First, make sure to clean the aluminum thoroughly before welding to remove any contaminants. Use the right equipment and settings to achieve the proper heat input and penetration.
Additionally, use a weaving motion when welding to create a wide bead that covers the joint thoroughly. Finally, take your time and be patient when welding aluminum with flux core. It can be a challenging process, but with practice and persistence, you can achieve great results.
Final steps for mastering aluminum welding with flux core
Welding aluminum with flux core can be challenging, but with the right tools, techniques, and knowledge, it can also be a rewarding experience. By understanding the properties of aluminum, preparing your workspace and materials, and using the right equipment and settings, you can achieve a successful weld.
Remember to avoid common mistakes, use proper techniques, and follow the tips for success. With practice and persistence, you can master the art of welding aluminum with flux core and tackle any aluminum welding project with confidence.