Are you looking to master the art of MIG welding? Well, one of the essential factors to consider is understanding how to calculate wire feed speed. This crucial component plays a significant role in achieving quality welds and ensuring the proper deposition of filler metal. By establishing the correct wire feed speed, you can control the heat input, the weld pool size, and the penetration depth, resulting in impeccable welds every time.
In this article, we will guide you through the process of calculating wire feed speed in MIG welding. We will break down the formula, explain the variables involved, and provide practical tips to help you achieve accurate calculations. Whether you are a beginner or an experienced welder looking to deepen your knowledge, this article will equip you with the necessary skills to optimize your MIG welding technique.
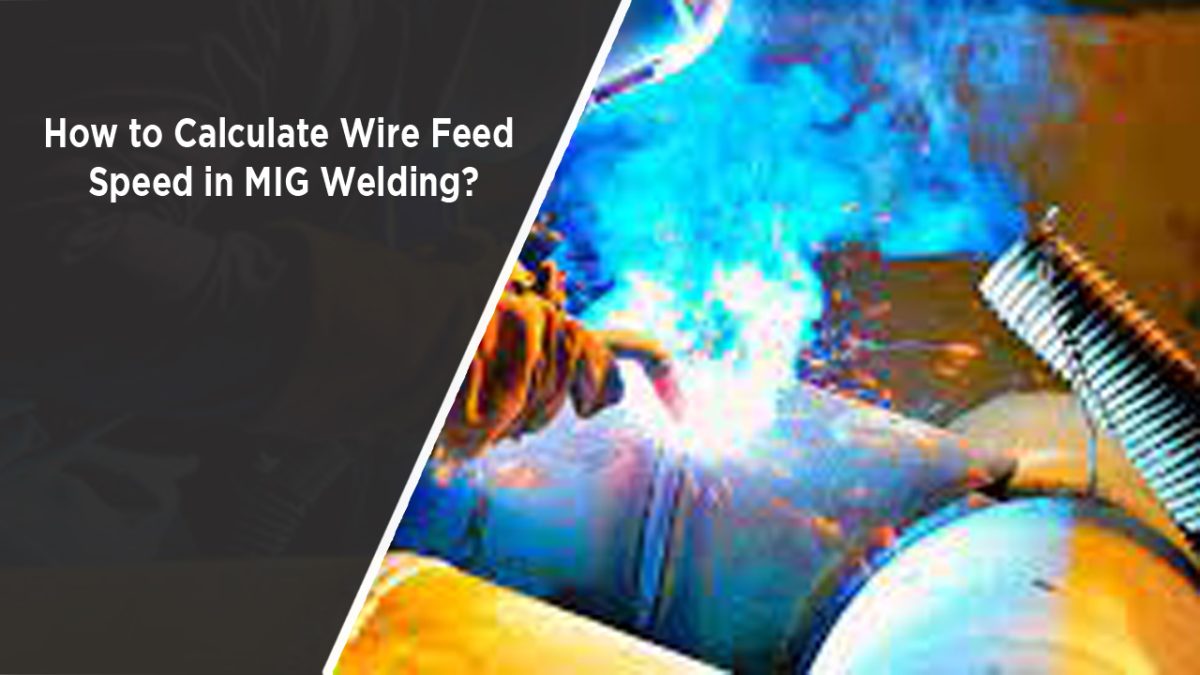
Importance of Wire Feed Speed
Wire feed speed is a critical parameter in MIG welding that determines the rate at which the electrode wire is fed into the weld pool. It directly affects the deposition rate and the quality of the weld. Welders must have a thorough understanding of wire feed speed to achieve optimal results.
The wire feed speed plays a crucial role in controlling the heat input during welding. If the wire feed speed is too slow, excessive heat input can lead to burn-through and distortion. On the other hand, if the wire feed speed is too high, the weld pool may not receive enough heat, resulting in poor fusion and weak welds. Therefore, finding the right balance is essential.
Another important aspect of wire feed speed is controlling the weld pool size. By adjusting the wire feed speed, you can increase or decrease the size of the weld pool, allowing for better control over the weld bead shape and penetration depth. This control is particularly important when welding different joint configurations and thicknesses.
Factors Affecting Wire Feed Speed
Several factors influence the wire feed speed in MIG welding. Understanding these factors will help you make accurate calculations and achieve the desired welding results. Here are some key factors to consider:
Welding current
The welding current directly affects the wire feed speed. Higher currents require faster wire feed speeds to maintain the proper deposition rate.
Welding voltage
The welding voltage also impacts the wire feed speed. Higher voltages usually require higher wire feed speeds to achieve the desired weld quality.
Electrode diameter
The diameter of the electrode wire affects the wire feed speed. Thicker wires generally require higher feed speeds, while thinner wires require slower feed speeds.
Base metal thickness
The thickness of the base metal influences the wire feed speed. Thicker materials require higher feed speeds to ensure proper fusion and penetration.
Joint configuration
Different joint configurations may require adjustments to the wire feed speed. For example, a fillet weld may require a slower feed speed than a butt joint.
By considering these factors and making appropriate adjustments, you can ensure accurate wire feed speed calculations and achieve high-quality welds.
Calculating Wire Feed Speed: The Formula and Units of Measurement
To calculate the wire feed speed in MIG welding, you need to use a simple formula that takes into account the welding current, electrode diameter, and the deposition rate. The formula is as follows:
Wire Feed Speed (in inches per minute) = (Welding Current × Deposition Rate) / (Cross-sectional Area of the Electrode)
The units of measurement for wire feed speed are typically inches per minute (IPM) in the United States and millimeters per minute (mm/min) in other countries.
Now, let’s break down the formula and understand each component in detail.
Welding Current
The welding current refers to the amount of electrical current flowing through the welding circuit. It is measured in amperes (A). The welding current directly affects the heat input and deposition rate.
Deposition Rate
The deposition rate is the amount of filler metal deposited per unit of time. It is usually expressed in pounds per hour (lb/hr) or kilograms per hour (kg/hr). The deposition rate depends on factors such as electrode diameter and welding parameters.
Cross-sectional Area of the Electrode
The cross-sectional area of the electrode is calculated using the formula: π × (Electrode Diameter / 2)². The electrode diameter is measured in inches or millimeters.
By plugging in the appropriate values for welding current, deposition rate, and electrode diameter, you can calculate the wire feed speed using the formula mentioned above.
Step-by-Step Guide to Calculating Wire Feed Speed
Now that we understand the formula and its components, let’s walk through the step-by-step process of calculating wire feed speed in MIG welding:
Determine the welding current
Consult the welding procedure specification (WPS) or the welding machine’s manual to find the recommended welding current for your specific weld.
Calculate the deposition rate
The deposition rate varies depending on factors such as electrode diameter, welding position, and joint configuration. Refer to welding reference books, online resources, or consult experienced welders to estimate the deposition rate.
Measure the electrode diameter
Use a caliper or a micrometer to measure the diameter of the electrode wire. Ensure accurate measurements for precise calculations.
Calculate the cross-sectional area of the electrode
Apply the formula mentioned earlier (π × (Electrode Diameter / 2)²) to determine the cross-sectional area of the electrode.
Plug in the values and calculate
Substitute the values of welding current, deposition rate, and electrode diameter into the wire feed speed formula and perform the calculation to obtain the wire feed speed in inches per minute or millimeters per minute.
Verify and adjust if necessary
Once you have obtained the wire feed speed, double-check your calculations and make any necessary adjustments based on practical considerations, welding position, or specific welding requirements.
By following these steps, you can accurately calculate the wire feed speed and ensure precise control over your MIG welding process.
Common Mistakes to Avoid When Calculating Wire Feed Speed
While calculating wire feed speed, it’s important to be aware of common mistakes that can lead to inaccurate calculations. Here are some mistakes to avoid:
Incorrect deposition rate estimation
Inaccurate estimation of the deposition rate can significantly affect the wire feed speed calculation. Take the time to research and gather accurate information on deposition rates for different electrode diameters and welding parameters.
Neglecting joint configuration and base metal thickness
Failure to consider the joint configuration and base metal thickness can lead to improper wire feed speed calculations. Always account for these factors to determine the correct wire feed speed.
Using incorrect units of measurement
Ensure consistency in the units of measurement throughout the calculation process. Mixing up inches with millimeters or using pounds instead of kilograms can result in incorrect wire feed speed values.
Neglecting adjustments for different welding positions
Different welding positions may require adjustments to the wire feed speed. For example, vertical-up welding may require a slower feed speed compared to flat or horizontal welding.
By avoiding these common mistakes, you can enhance the accuracy of your wire feed speed calculations and achieve better welding results.
Tips for Adjusting Wire Feed Speed for Different Welding Scenarios
While the calculated wire feed speed provides a baseline, it may need adjustments based on specific welding scenarios. Here are some tips to help you fine-tune the wire feed speed:
Practice and experimentation
As with any welding parameter, practice and experimentation are key to finding the optimal wire feed speed for different materials and joint configurations. Take the time to run test welds and evaluate the results to make informed adjustments.
Consider the welding position
Welding positions such as flat, horizontal, vertical, and overhead may require varying wire feed speeds to ensure proper fusion and penetration. Adjust the wire feed speed accordingly for each position.
Adapting for different materials
Different materials have varying thermal conductivity and melting points. Adjust the wire feed speed to suit the specific material being welded. For example, aluminum welding generally requires higher wire feed speeds than steel welding.
Account for joint configuration and base metal thickness
Welding joints with different configurations and varying base metal thicknesses may require adjustments to the wire feed speed. Thicker materials may necessitate higher feed speeds, while thinner materials may require slower speeds.
Monitor and adjust in real-time
While welding, monitor the bead appearance, penetration depth, and overall weld quality. If necessary, make real-time adjustments to the wire feed speed to achieve the desired results.
By considering these tips and adapting the wire feed speed to specific welding scenarios, you can optimize your MIG welding technique and achieve superior welds.
Tools and Equipment for Accurate Wire Feed Speed Calculations
To ensure accurate wire feed speed calculations, it’s essential to have the right tools and equipment. Here are some tools that can aid in the process:
Digital Welding Machine
Use a digital welding machine that provides precise control over welding parameters, including wire feed speed. Digital machines often have built-in calculators for quick and accurate calculations.
Caliper or Micrometer
Use a caliper or micrometer to measure the diameter of the electrode wire accurately. Accurate measurements are crucial for precise wire feed speed calculations.
Welding Reference Books
Invest in reputable welding reference books that provide comprehensive information on wire feed speed calculations, deposition rates, and other welding parameters. These resources can serve as valuable references for accurate calculations.
Welding Procedure Specification (WPS)
The WPS provides specific guidelines for welding procedures, including recommended wire feed speeds for different welding scenarios. Consult the WPS to ensure compliance and accurate calculations.
Having these tools and resources at your disposal will enable you to calculate wire feed speed with precision and achieve optimal welding results.
Troubleshooting Wire Feed Speed Issues in MIG Welding
Sometimes, despite accurate calculations, issues with wire feed speed may arise during MIG welding. Here are some troubleshooting tips to help you address common wire feed speed problems:
Erratic wire feed
If the wire feed is inconsistent or erratic, check for obstructions or kinks in the wire feed system. Clean or replace any clogged or damaged components to ensure smooth and consistent wire feed.
Wire burnback and sticking
If the wire tends to stick to the contact tip or experiences frequent burnback, it may indicate an issue with the wire feed speed. Verify that the wire feed speed is appropriate for the welding parameters and adjust if necessary.
Excessive spatter
Excessive spatter can be a sign of incorrect wire feed speed. Spatter occurs when the wire feed speed is too high, causing excessive molten metal to transfer to the workpiece. Adjust the wire feed speed to minimize spatter.
Inadequate fusion
If the welds exhibit inadequate fusion or lack of penetration, it may indicate a low wire feed speed. Increase the wire feed speed to ensure proper fusion and penetration.
Porosity in welds
Porosity, or the presence of gas pockets in the weld, can be caused by improper wire feed speed. Excessive wire feed speed can result in inadequate shielding gas coverage, leading to porosity. Adjust the wire feed speed to minimize porosity.
By troubleshooting wire feed speed issues promptly, you can ensure consistent and high-quality welds.
Conclusion and Final Thoughts
Calculating the wire feed speed is a fundamental aspect of MIG welding that directly impacts the quality and integrity of welds. By understanding the formula, variables, and factors involved, you can accurately determine the wire feed speed and achieve optimal welding results.
Remember to consider factors such as welding current, electrode diameter, base metal thickness, and joint configuration when calculating the wire feed speed. Avoid common mistakes, adjust for different welding scenarios, and troubleshoot any issues that may arise.
With practice and experience, you will develop a keen sense for finding the ideal wire feed speed for each welding project. So, use this knowledge to elevate your MIG welding technique and create flawless welds that stand the test of time.