Welcome to the world of carbon arc welding, where sparks fly and metal fuses with precision. In this article, we will delve into the techniques and uses of carbon arc welding, an age-old but highly effective welding method. With a maximum of 160 words, we’ll provide you with a concise and informative introduction to this fascinating welding technique.
Carbon arc welding involves creating an electric arc between a carbon electrode and the workpiece, melting the base metal and filling in the joint with a filler metal. This versatile welding method is known for its ability to weld various types of metals, from steel to cast iron, making it a popular choice among welders worldwide.
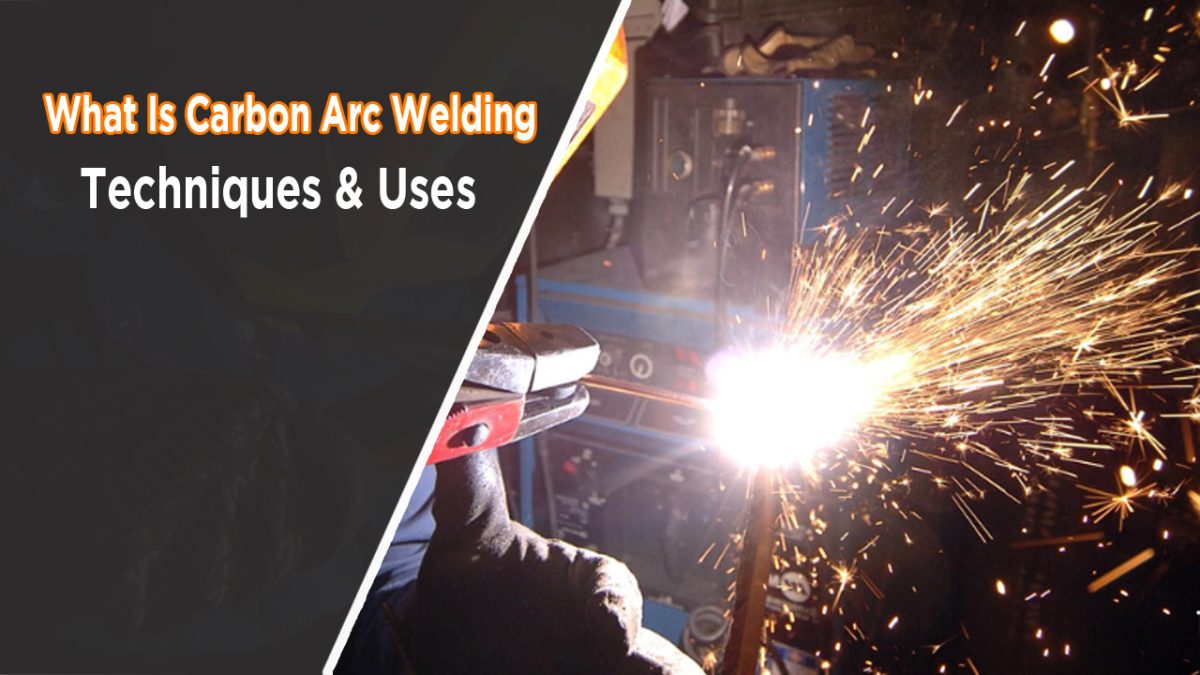
Image by weldingproperty
Whether you’re a seasoned welder looking to expand your skillset or a curious beginner exploring the world of welding, this article will equip you with the knowledge you need to understand the ins and outs of carbon arc welding. From the different techniques used to the wide range of applications, we’ll cover it all.
History of Carbon Arc Welding
Carbon arc welding has a rich history that dates back to the late 19th century. It was first developed by a Russian engineer named Nikolay Benardos in 1881, who used carbon electrodes to create an arc and weld metal. This early form of carbon arc welding was mainly used for repair work and was limited in its applications.
As the technique evolved, so did its uses. In the early 20th century, carbon arc welding became widely adopted in shipbuilding, construction, and manufacturing industries. The ability to weld various metals together made it a valuable skill for welders around the world.
Understanding the Carbon Arc Welding Equipment
To perform carbon arc welding, you’ll need a few essential pieces of equipment. The main components include a power source, carbon electrode holder, carbon electrode, workpiece, and safety gear.
The power source provides the electrical current needed to create the arc. It can be a transformer, generator, or even a battery pack, depending on the scale of the welding project. The carbon electrode holder holds the carbon electrode in place and allows for easy maneuvering during the welding process.
The carbon electrode is the heart of carbon arc welding. It is made of high-quality carbon and serves as the conductor for the electrical current. The workpiece, on the other hand, is the metal that you’ll be welding. It should be properly cleaned and prepared before starting the welding process.
Lastly, safety gear is crucial to protect yourself from the intense heat, sparks, and fumes generated during welding. This includes a welding helmet, gloves, apron, and protective clothing. Always ensure you have the right safety equipment before starting any welding project.
Types of Carbon Arc Welding Techniques
Carbon arc welding encompasses various techniques, each suited for different applications. Here are the most common techniques used in carbon arc welding:
Single Carbon Arc Welding
This technique involves using a single carbon electrode to create the arc. It is primarily used for welding thin materials or in situations where precise control is required.
Twin Carbon Arc Welding
In twin carbon arc welding, two carbon electrodes are used simultaneously. This technique allows for faster welding speeds and deeper penetration, making it suitable for thicker materials and heavy-duty applications.
Multiple Carbon Arc Welding
Multiple carbon arc welding involves using three or more carbon electrodes to create multiple arcs simultaneously. This technique is typically used in industrial settings where large-scale welding is required.
Each technique has its advantages and disadvantages, and the choice depends on the specific project requirements and the skill level of the welder. It’s essential to understand the differences between these techniques to achieve the desired welding results.
Advantages and Disadvantages of Carbon Arc Welding
Like any welding method, carbon arc welding has its pros and cons. Understanding these can help you determine whether it’s the right technique for your welding needs.
Advantages of carbon arc welding:
Versatility
Carbon arc welding can be used to weld various metals, including steel, cast iron, and non-ferrous alloys. This versatility makes it a valuable skill for welders working with different materials.
Low equipment cost
Compared to some other welding methods, carbon arc welding equipment is relatively affordable, making it accessible to a wide range of welders.
High deposition rates
Carbon arc welding allows for fast deposition rates, meaning you can complete welding projects in less time compared to other methods.
Disadvantages of carbon arc welding:
High heat input
Carbon arc welding generates a significant amount of heat, which can lead to distortion and warping of the workpiece if not properly controlled.
Limited joint access
The size and shape of the carbon electrode can limit access to tight or hard-to-reach areas, making it challenging to weld certain joints.
Requires skill and practice
Carbon arc welding requires skill and practice to achieve quality welds. It can be more challenging for beginners compared to other welding methods.
Understanding the advantages and disadvantages of carbon arc welding can help you determine its suitability for your specific welding projects.
Common Uses of Carbon Arc Welding
Carbon arc welding finds applications in various industries due to its versatility and ability to weld different types of metals. Some common uses of carbon arc welding include:
Shipbuilding and marine industry
Carbon arc welding is widely used in the shipbuilding industry to weld steel plates and other metal components. It provides strong and durable welds necessary for marine vessels.
Construction industry
Carbon arc welding is used in the construction industry to join structural steel components, such as beams and columns. It is also utilized for repairing heavy machinery and equipment.
Manufacturing industry
Carbon arc welding is employed in the manufacturing industry to fabricate metal products, such as tanks, pipes, and frames. It ensures strong and reliable welds for industrial applications.
Automotive industry
Carbon arc welding is utilized in the automotive industry for various applications, including body repairs, frame welding, and manufacturing of exhaust systems.
These are just a few examples of the many industries that rely on carbon arc welding for their welding needs. The ability to weld different metals together makes carbon arc welding a versatile and valuable technique in the welding industry.
Safety Precautions for Carbon Arc Welding
Safety should always be a top priority when engaging in carbon arc welding. Here are some essential safety precautions to follow:
Wear appropriate safety gear
Always wear a welding helmet, gloves, apron, and other protective clothing to shield yourself from sparks, heat, and UV radiation.
Ensure proper ventilation
Carbon arc welding produces fumes and gases that can be hazardous if inhaled. Work in a well-ventilated area or use local exhaust ventilation to remove the fumes.
Inspect equipment
Regularly inspect your welding equipment, including cables, electrodes, and power sources, to ensure they are in good working condition. Faulty equipment can lead to accidents and poor weld quality.
Avoid flammable materials
Keep flammable materials, such as oil, paint, or solvents, away from your welding area. Sparks and heat generated during welding can cause these materials to ignite.
Ground the workpiece
Properly ground the workpiece to avoid electrical shock and ensure a stable welding process.
By following these safety precautions, you can protect yourself and others from potential hazards associated with carbon arc welding.
Tips for Successful Carbon Arc Welding
To achieve quality welds with carbon arc welding, consider the following tips:
Clean the workpiece
Properly clean the workpiece before welding to remove any contaminants, such as rust, paint, or grease. This ensures a strong and clean weld.
Control the heat
Carbon arc welding generates intense heat. To avoid distortion and warping of the workpiece, control the heat input by adjusting the welding parameters, such as current and arc length.
Maintain electrode angle
Maintain a consistent electrode angle during welding to ensure proper penetration and fusion of the base metals.
Practice and refine your technique
Carbon arc welding requires practice and skill. Continuously refine your technique by experimenting with different welding parameters and practicing on scrap materials.
By following these tips, you can improve your carbon arc welding skills and achieve high-quality welds.
Comparison with Other Welding Methods
Carbon arc welding is just one of many welding methods available. Let’s compare it with some other commonly used welding techniques:
Shielded Metal Arc Welding (SMAW)
Unlike carbon arc welding, SMAW uses a consumable electrode coated in flux to create an arc. It is a versatile and widely used welding method but requires more frequent electrode changes compared to carbon arc welding.
Gas Metal Arc Welding (GMAW)
Also known as MIG welding, GMAW uses a continuous wire electrode and a shielding gas to protect the weld pool. It offers high productivity and is suitable for a wide range of materials.
Tungsten Inert Gas Welding (TIG)
TIG welding uses a non-consumable tungsten electrode and a shielding gas to protect the weld area. It provides precise control and produces high-quality welds but requires advanced skills.
While carbon arc welding has its unique advantages and applications, the choice of welding method depends on factors such as the type of material, project requirements, and the skill level of the welder.
Final Thoughts
Carbon arc welding is a fascinating welding method that has stood the test of time. Its ability to weld various metals and its versatility have made it a popular choice among welders across different industries. From shipbuilding to construction, carbon arc welding finds applications in a wide range of fields.
By understanding the techniques, equipment, advantages, and precautions associated with carbon arc welding, you can expand your welding skillset and explore new possibilities in the world of metal fabrication. Remember to always prioritize safety and practice to achieve quality welds.
So, don your safety gear, grab your carbon electrode, and embark on the captivating journey of carbon arc welding. Let the sparks fly and the metal fuse as you master this age-old but highly effective welding method.