In the world of welding, there are several important factors to consider, and one of them is wire feed speed. If you’re new to welding, you may be wondering what exactly wire feed speed is, and how it affects the quality of your welds. Simply put, wire feed speed refers to the rate at which the welding wire is fed into the welding arc. It plays a significant role in determining the heat input and penetration of the weld.
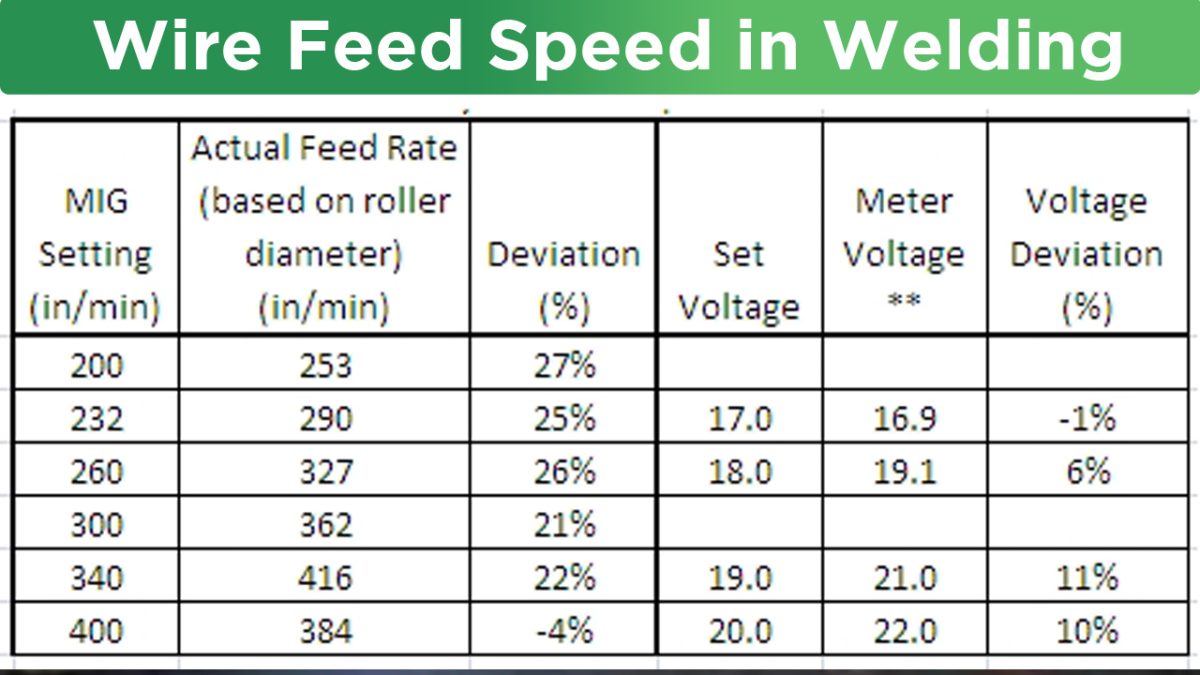
Image by everlastgenerators
Wire feed speed is a crucial parameter in the welding process, as it directly affects the quality and strength of the weld. The wire feed speed is typically measured in inches per minute (IPM) or meters per minute (MPM), and it determines how quickly the electrode wire is consumed during welding.
When the wire feed speed is too high, the welding wire can create excessive spatter, which is the small molten metal droplets that are ejected during the welding process. This can result in poor fusion and a weaker weld. On the other hand, if the wire feed speed is too low, the weld may lack penetration, leading to a weak joint.
Achieving the right wire feed speed is essential for producing quality welds. It requires finding the perfect balance between the wire feed speed, welding current, and voltage settings to ensure optimal heat input and penetration.
Importance of wire feed speed in welding
Wire feed speed plays a crucial role in the welding process, as it directly affects the quality and strength of the weld. When the wire feed speed is set correctly, it ensures proper fusion between the base metal and the welding wire, resulting in a strong bond. Additionally, the wire feed speed determines the size and shape of the weld bead, which can impact the overall appearance of the weld.
A proper wire feed speed setting also helps control the heat input, which is crucial for preventing distortion, warping, and excessive heat-affected zones. By adjusting the wire feed speed, welders can achieve the desired penetration depth and control the amount of filler material deposited.
Furthermore, wire feed speed affects the efficiency and productivity of the welding process. By finding the optimal wire feed speed, welders can minimize downtime spent on rework, reduce material waste, and increase overall productivity.
Factors that affect wire feed speed
Several factors can influence the ideal wire feed speed for a specific welding application. Understanding these factors is crucial for achieving the best results in your welding projects.
Welding process: Different welding processes, such as MIG (Metal Inert Gas) welding, TIG (Tungsten Inert Gas) welding, and Flux-Cored Arc Welding (FCAW), have different wire feed speed requirements. It’s important to consider the specific welding process being used to determine the appropriate wire feed speed.
Material type and thickness: The type and thickness of the base metal being welded also affect the wire feed speed. Thicker materials typically require a higher wire feed speed to ensure proper penetration, while thinner materials may require a slower wire feed speed to prevent burn-through.
Electrode diameter: The diameter of the welding wire electrode can impact the wire feed speed. Thicker electrodes may require a higher feed speed, while thinner electrodes may require a lower feed speed.
Welding position: The position in which the weld is being performed can also influence the wire feed speed. Welding in a vertical or overhead position may require a slower wire feed speed to prevent excessive spatter and ensure proper fusion.
Welding current and voltage: The welding current and voltage settings are closely related to the wire feed speed. Adjusting these parameters can help fine-tune the wire feed speed to achieve the desired weld quality.
By considering these factors, welders can determine the appropriate wire feed speed for their specific welding application.
Determining the appropriate wire feed speed for different welding processes
Each welding process has its own recommended wire feed speed range, which serves as a starting point for finding the optimal setting. Here are the general guidelines for determining the appropriate wire feed speed for different welding processes:
MIG welding: For MIG welding, start with a wire feed speed of around 250-300 IPM (inches per minute) and adjust as needed based on the specific welding application. Thicker materials may require a higher wire feed speed, while thinner materials may require a lower feed speed.
TIG welding: TIG welding typically requires a lower wire feed speed compared to MIG welding. Start with a wire feed speed of around 50-100 IPM and make adjustments based on the material thickness and desired weld penetration.
Flux-Cored Arc Welding (FCAW): FCAW utilizes a tubular wire filled with flux, which affects the wire feed speed requirements. Start with a wire feed speed of around 150-200 IPM and adjust accordingly based on the specific welding application.
Remember that these are general guidelines, and it’s important to consult the welding equipment manufacturer’s recommendations and conduct test welds to fine-tune the wire feed speed for optimal results.
Tips for adjusting wire feed speed
Finding the correct wire feed speed can be a trial-and-error process, but here are some tips to help you make the necessary adjustments:
Start with the manufacturer’s recommendations: Consult the welding machine’s manual or the wire manufacturer’s guidelines to determine the recommended wire feed speed range for your specific welding application.
Conduct test welds: Perform test welds on scrap materials to evaluate the weld quality and make adjustments to the wire feed speed as necessary. Pay attention to the appearance of the weld bead, penetration depth, and overall fusion.
Observe spatter: Excessive spatter is often an indicator of a wire feed speed that is too high. If you notice excessive spatter, try reducing the wire feed speed gradually until the spatter is minimized while maintaining good fusion.
Evaluate penetration: Insufficient penetration may indicate a wire feed speed that is too low. If the weld lacks penetration, increase the wire feed speed gradually until the desired penetration is achieved.
Consider travel speed: The travel speed of the welding torch can also impact the wire feed speed. A slower travel speed may require a lower wire feed speed, while a faster travel speed may require a higher wire feed speed.
By following these tips and closely monitoring the weld quality, you can make the necessary adjustments to find the optimal wire feed speed for your welding projects.
Common wire feed speed errors to avoid
While adjusting the wire feed speed, it’s important to be aware of common errors that can negatively impact the weld quality. Here are some mistakes to avoid:
Inconsistent wire feed speed: Maintaining a consistent wire feed speed throughout the welding process is crucial for achieving uniform welds. Inconsistent wire feed speed can result in an uneven weld bead and poor fusion.
Over-reliance on default settings: While manufacturers provide recommended wire feed speed ranges, it’s important to remember that these are starting points. Different welding applications may require adjustments to the default settings to achieve optimal results.
Neglecting other welding parameters: Wire feed speed is just one of the parameters that affect the quality of the weld. Neglecting other parameters, such as welding current, voltage, and shielding gas flow rate, can result in subpar welds.
Ignoring the sound of the arc: The sound of the welding arc can provide valuable feedback on the quality of the weld. A steady, crackling sound indicates good fusion and indicates that the wire feed speed is set correctly.
By avoiding these common errors, you can improve the quality and consistency of your welds.
Tools and equipment to measure wire feed speed
Accurately measuring the wire feed speed is essential for fine-tuning your welding process. Here are some tools and equipment commonly used to measure wire feed speed:
Wire feed speed meters: These devices are specifically designed to measure the wire feed speed. They can be attached to the welding torch or wire feeder to provide real-time wire feed speed readings.
Marking the welding wire: Marking the welding wire at a specific point and measuring the time it takes for the marked point to pass through the wire feeder can provide an estimation of the wire feed speed.
Counting revolutions: Counting the number of revolutions the wire feeder motor makes in a given time period can provide an approximate wire feed speed measurement.
It’s important to consult the welding equipment manufacturer’s recommendations and guidelines for accurate wire feed speed measurement.
Troubleshooting wire feed speed issues
Sometimes, welders may encounter issues with the wire feed speed that can affect the weld quality. Here are some common wire feed speed issues and possible solutions:
Excessive spatter: Excessive spatter can be caused by a wire feed speed that is too high. Try reducing the wire feed speed gradually until the spatter is minimized while maintaining good fusion.
Lack of fusion and penetration: If the weld lacks fusion and penetration, the wire feed speed may be too low. Increase the wire feed speed gradually until the desired fusion and penetration are achieved.
Inconsistent weld bead: Inconsistent wire feed speed can result in an uneven weld bead. Ensure that the wire feed speed remains consistent throughout the welding process.
Wire feed motor issues: If the wire feed motor is not functioning properly, it can affect the wire feed speed. Regular maintenance and inspection of the wire feed motor can help prevent issues.
If troubleshooting the wire feed speed issues becomes challenging, it’s recommended to consult a welding professional or seek assistance from the welding equipment manufacturer.
Conclusion: the role of wire feed speed in achieving quality welds
Wire feed speed is a critical parameter in the welding process that directly impacts the quality, strength, and appearance of the weld. Finding the right wire feed speed requires considering various factors such as welding process, material type and thickness, electrode diameter, welding position, and welding current and voltage settings.
By understanding the importance of wire feed speed and making the necessary adjustments, welders can achieve strong, consistent welds with optimal penetration and fusion. Remember to conduct test welds, observe spatter and penetration, and make gradual adjustments to find the perfect wire feed speed for your specific welding application.
Accurate measurement of wire feed speed using specialized tools and equipment, along with troubleshooting common wire feed speed issues, will further enhance the welding process and ensure quality welds.
So, whether you’re a beginner looking to learn more about welding or an experienced welder looking to fine-tune your skills, mastering wire feed speed is essential for successful welding projects.