Welding is a crucial process in various industries, but it’s not without its challenges. From faulty equipment to improper technique, welders often encounter common problems that can hamper productivity and affect the quality of their work. Fortunately, there are solutions to overcome these hurdles and ensure successful welds every time.
In this article, we will explore some of the most common welding problems and their solutions. We will delve into issues like porosity, which causes tiny holes to form in the weld, and how to address it. We’ll also discuss how to tackle inconsistencies in weld bead appearance, such as lack of fusion or undercutting. Plus, we’ll provide tips for troubleshooting electrical issues and dealing with spatter.
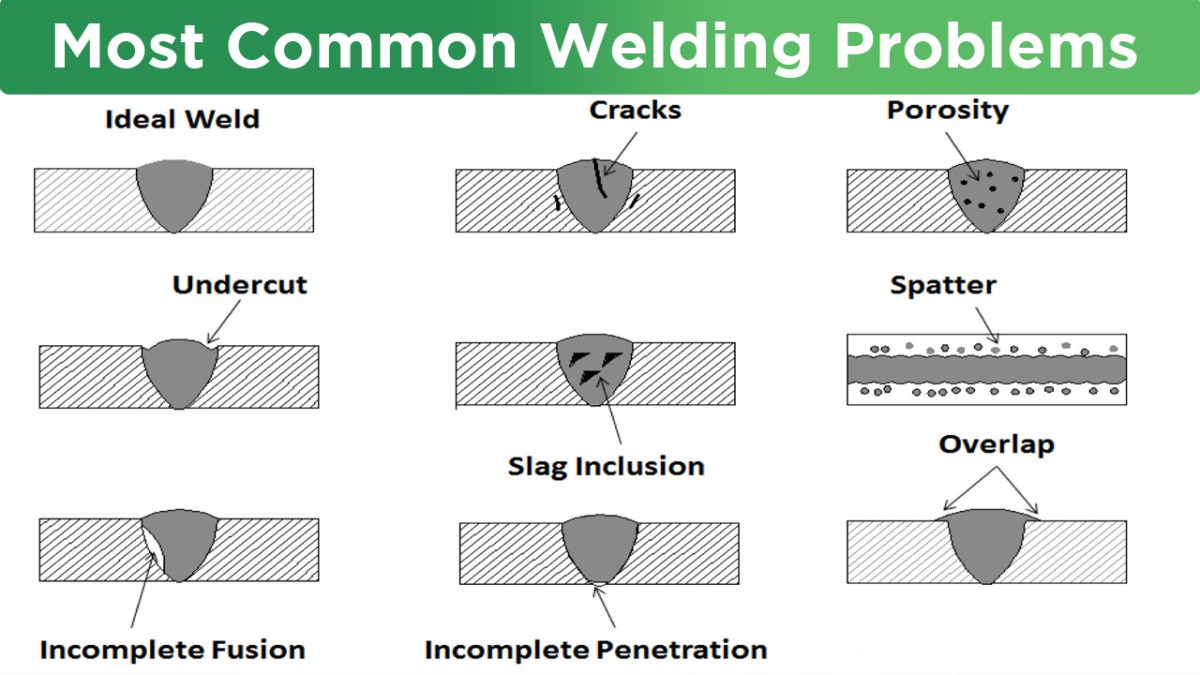
Image by thepipingmart
Whether you’re a beginner welder or a seasoned professional, having the knowledge to identify and resolve common welding problems is essential. By understanding these issues and their solutions, you can enhance your welding skills, improve the quality of your work, and increase your overall efficiency.
Common Welding Problems
Porosity
Porosity is a common welding problem that occurs when tiny holes form in the weld. These holes can weaken the weld and compromise its integrity. There are several causes of porosity, including moisture, improper shielding gas, and contaminated electrodes.
To address porosity, it’s important to ensure that the welding area is clean and free from any moisture or contaminants. Proper storage and handling of electrodes can also help prevent porosity. Additionally, using the correct shielding gas and ensuring proper gas flow can minimize the risk of porosity. Regularly checking and maintaining your welding equipment, including gas regulators and hoses, is crucial for avoiding this problem.
Lack of Fusion
Lack of fusion refers to a situation where the weld fails to bond properly with the base metal. This problem can result in weak welds that are susceptible to cracking and failure. Lack of fusion can be caused by factors such as improper welding technique, incorrect heat settings, or using the wrong welding process for the material being welded.
To overcome lack of fusion, it’s important to ensure proper heat control and weld technique. Using the correct welding process for the material being welded is also essential. Additionally, cleaning the base metal thoroughly and using the appropriate filler material can help promote better fusion. Regularly practicing and refining your welding technique through training and experience can also improve your ability to achieve proper fusion.
Cracking
Cracking is a welding problem that can occur during or after the welding process. It can be caused by factors such as excessive heat, rapid cooling, or high levels of stress in the weld. Cracks can compromise the strength and integrity of the weld, leading to potential failure.
To prevent cracking, it’s important to control the heat input during welding and ensure proper cooling after welding. Preheating the base metal can help reduce the risk of cracking, especially when dealing with materials prone to cracking, such as high carbon steels. Proper joint design and the use of appropriate welding techniques, such as backstepping, can also help minimize the risk of cracking. Additionally, stress-relieving techniques, such as post-weld heat treatment, can be employed to reduce residual stress and prevent cracking.
Undercutting
Undercutting refers to a groove or depression that forms along the edges of the weld joint. It can weaken the weld and make it more susceptible to cracking. Undercutting is often caused by factors such as improper welding technique, excessive heat input, or incorrect electrode angle.
To address undercutting, it’s important to maintain proper welding technique, including maintaining the correct electrode angle and travel speed. Avoiding excessive heat input and using the appropriate welding process for the material being welded can also help prevent undercutting. Proper joint preparation, including the removal of any contaminants or oxides, is crucial for minimizing the risk of undercutting. Regularly inspecting and correcting any issues with your welding equipment, such as worn or damaged electrodes, is also important for preventing undercutting.
Distortion
Distortion is a common problem in welding that refers to the deformation or warping of the base metal during the welding process. It can occur due to factors such as uneven heating and cooling, high levels of residual stress, or improper joint design.
To minimize distortion, it’s important to control the heat input and ensure proper cooling during and after welding. Preheating the base metal can help reduce the risk of distortion, especially when dealing with materials prone to distortion, such as aluminum. Using proper fixtures and clamps to hold the workpiece in place during welding can also help prevent distortion. Proper joint design, including the use of appropriate weld sizes and joint configurations, is crucial for minimizing distortion.
Spatter
Spatter refers to the small droplets of molten metal that are expelled during the welding process. It can cause a messy work environment, lead to poor weld appearance, and contaminate nearby surfaces. Spatter is often caused by factors such as improper shielding gas, incorrect wire feed speed, or using the wrong welding process for the material being welded.
To reduce spatter, it’s important to ensure proper shielding gas coverage and flow. Using the correct wire feed speed and adjusting the voltage settings can also help minimize spatter. Regularly cleaning the welding gun and replacing worn or damaged consumables, such as contact tips and nozzles, is crucial for preventing spatter. Proper joint preparation, including the removal of any contaminants or oxides, is also important for minimizing spatter.
Solutions to Common Welding Problems
We have explored some of the most common welding problems and provided practical solutions to overcome them. By understanding these issues and implementing the appropriate solutions, you can enhance your welding skills, improve the quality of your work, and increase your overall efficiency. Remember to always prioritize safety and follow industry best practices when performing any welding task.
Conclusion and Final Thoughts
Welding is a complex process that requires skill, knowledge, and attention to detail. While common welding problems can be frustrating, they are not insurmountable. By understanding the causes and implementing the appropriate solutions, you can overcome these challenges and become a better welder.
Remember to regularly inspect and maintain your welding equipment, practice proper welding techniques, and prioritize cleanliness in the welding area. Continuously seek opportunities to improve your skills through training, experience, and staying updated with the latest industry advancements.
By addressing common welding problems head-on, you can ensure successful welds, enhance the quality of your work, and ultimately excel in your welding career. Let’s embrace these challenges as opportunities for growth and become the best welders we can be. Together, we can overcome common welding problems and achieve outstanding results.