In the realm of plastic fabrication, it is a vital process used to join thermoplastics together. Extrusion welding involves heating and melting the plastic, then fusing it together using high pressure, allowing for a strong and durable bond between the components. This technique is widely used in industries such as construction, automotive, and healthcare, to name a few.
In this article, we will explore the fundamentals of extrusion welding. We will discuss the equipment used, the process, and its various applications. Additionally, we will delve into temperature control during extrusion welding and why it is essential to maintain the right temperature range. Lastly, we will examine the benefits and advancements of extrusion welding, which make it a preferred choice in plastic fabrication.
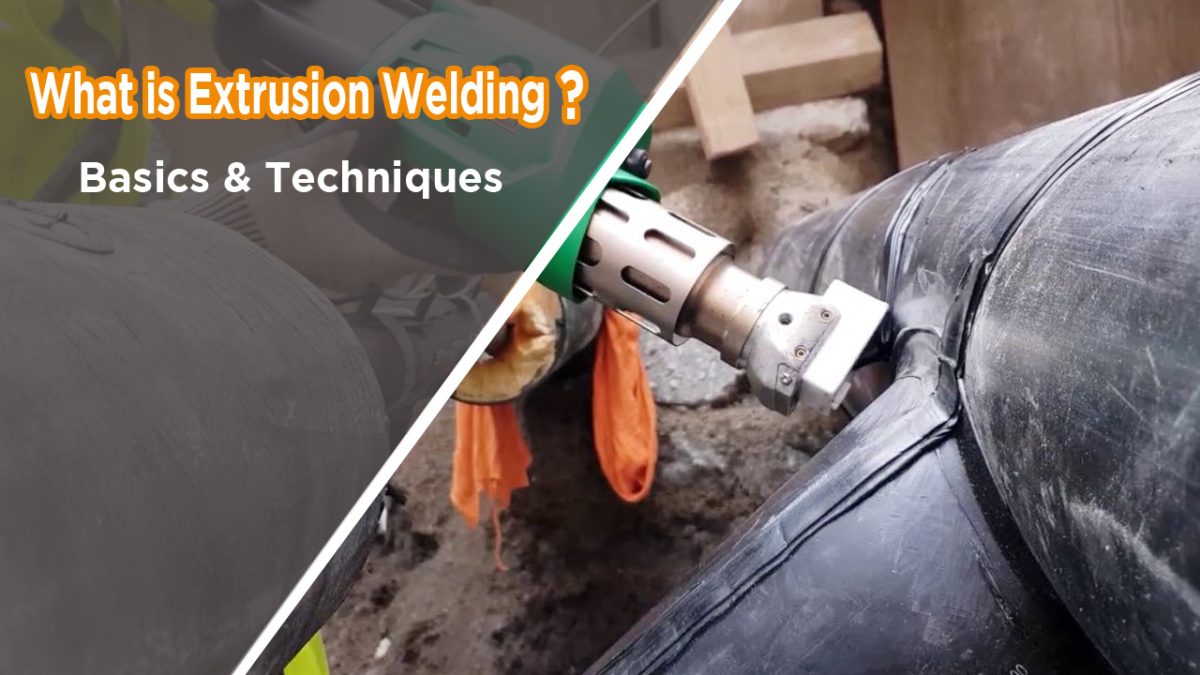
Understanding the Extrusion Welding Process
Extrusion welding is a plastic welding process that involves melting and joining two plastic components. It is widely used in various plastic fabrication applications and offers several advantages over other welding techniques.
Principles Behind Plastic Welding
Plastic welding involves using heat to melt and join thermoplastics. Extrusion welding, in particular, utilizes a plastic welding gun to heat and melt the plastic at the joint. Once the plastic reaches the proper temperature, it is extruded from the welding gun and applied to the joint.
Specific Techniques Employed in Extrusion Welding
During extrusion welding, there are several techniques used to ensure a strong, durable weld. One technique is to preheat the plastic components to the appropriate temperature before welding. This ensures that the components soften evenly and create a strong weld. Other techniques include selecting the correct welding tip and adjusting the extrusion rate to fit the application.
Factors That Impact the Quality of the Weld
There are several factors that can affect the quality of the weld, including the temperature of the plastic, the welding speed, and the pressure applied to the joint. It is essential to maintain a consistent temperature, speed, and pressure during the welding process to produce a strong, long-lasting weld.
Overall, extrusion welding is a reliable and efficient method for joining plastic components. By understanding the principles behind plastic welding, as well as the specific techniques and factors that impact the quality of the weld, professionals can harness this process to create durable and high-quality plastic structures.
Essential Equipment for Extrusion Welding
To achieve successful extrusion welding, specific equipment is essential. You need the right extrusion welding machines and components that cater to your application requirements. The equipment usually includes:
- Extrusion welding machine
- Welding rod feeder
- Heating element
- Welding gun
Extrusion welding machines come in various types, namely:
Type | Description |
---|---|
Manual extrusion welding machine | Perfect for small or simple jobs. |
Semi-automatic extrusion welding machine | Efficient for a broad range of jobs. |
Fully automatic extrusion welding machine | Ideal for larger and more complex jobs. |
When purchasing extrusion welding equipment, take into account the specifics of your application. Some factors to consider include:
- Type of plastic
- Thickness of plastic
- Width of the welding joint
- Speed and rate of production
Temperature Considerations in Extrusion Welding
Temperature control is an integral aspect that ensures the successful completion of extrusion welding. Extrusion welding temperature can have a significant impact on the quality of the resulting weld. Hence it’s crucial to maintain appropriate temperature ranges during the welding process, depending on the plastic material.
Several factors can influence the temperature control mechanism, such as the welding speed, material thickness, and environmental conditions. Among these, welding speed plays a significant role in the temperature of extrudate. High welding speeds can lead to excessively high extrusion temperatures, resulting in material degradation and a weaker weld.
The recommended extrusion welding temperature varies for different types of plastic. For instance, the temperature range is from 200°C to 240°C for polyethylene (PE) and from 240°C to 300°C for Polypropylene (PP). The recommended temperatures for welding thermoplastics should be followed closely, as recommended by plastic manufacturers’ guidelines.
It’s important to monitor the temperature throughout the welding process and make the necessary adjustments. Regular temperature checks can help detect possible defects and prevent massive losses.
Applications and Benefits of Extrusion Welding
Extrusion welding has ample applications in different industries, primarily for joining thermoplastics with consistent quality and strength. By melting and fusing the plastic together, extrusion welding creates a waterproof, airtight, and chemical-resistant joint. Here we present some of the best applications for extrusion welding, along with its benefits.
Tanks
Extrusion welding is ideal for creating tanks, especially for storing liquids. The welded joints are durable and leak-proof, ensuring the integrity of the tank. Tanks made with extrusion welding can be found in the chemical, agricultural, and food processing industries.
Pipes
Extrusion welding of pipes allows for installation efficiency, reducing the number of joints for a more continuous flow along the pipeline. Proper extrusion welding guarantees that the joints are smooth and controlled and increases the pipeline’s durability, even for high-stress environments or buried pipes.
Geomembranes
Geomembranes comprise synthetic liners that protect the environment from various hazards, such as seepage from landfills, impoundment basins, and waste storage ponds. Extrusion welding allows for the fast and easy installation of these materials, which require reliable sealing to prevent contamination and pollution.
Benefits of Extrusion Welding
Extrusion welding boasts numerous benefits, such as:
- Strong joints: Extrusion welding produces sturdy and robust connections.
- Controlled process: Extrusion welding provides regulated temperature to create consistent welding quality.
- Economical: Extrusion welding is an affordable method for joining plastics.
- Waterproof: Extrusion welding creates joints that are water-resistant, making it perfect for use in any waterproofing application.
- Chemical resistance: Extrusion welding joints can withstand harsh chemicals, acids, and other hazardous materials, crucial for chemical containment.
Advancements and Innovations in Extrusion Welding
Extrusion welding has come a long way since its inception. The technology has evolved in leaps and bounds, resulting in numerous advancements and innovations that are enhancing the precision, efficiency, and quality of extrusion welding. Let’s take a closer look at some of the latest developments in this field.
New Welding Techniques
One of the most exciting advancements in extrusion welding is the development of new welding techniques. For instance, robots are now being used to perform automated extrusion welding, reducing the need for human intervention and increasing accuracy. Moreover, laser extrusion welding – which uses laser heat sources in place of hot air – is becoming increasingly popular, especially in high-precision applications.
Improved Equipment
The quality of extrusion welding equipment has also improved significantly in recent years. For example, manufacturers are now producing machines with better temperature controls, allowing for more precise temperature regulation during welding. Additionally, new extruders are being designed with improved mechanical features, such as adjustable heads, specialized nozzles, and automatic cleaning systems.
Emerging Trends
There are several emerging trends in extrusion welding that are worth noting. For instance, there is a growing interest in using extrusion welding for large-scale projects, such as bridge building and automotive manufacturing. To accommodate these applications, companies are developing new extruders with larger capacities and more advanced controls. Additionally, sustainability is becoming an increasingly important factor in extrusion welding, with manufacturers seeking out eco-friendly materials and sustainable production processes.
Advancements in Extrusion Welding | Innovations in Extrusion Welding |
---|---|
New welding techniques | Automated extrusion welding |
Improved equipment | Extruders with better temperature controls and mechanical features |
Emerging trends | Larger-scale projects and sustainability |
These advancements and innovations in extrusion welding are transforming the field and opening up new possibilities for plastic fabrication across a range of industries. By staying up-to-date with the latest developments, professionals can take advantage of these advances to create even more impressive and durable plastic structures for their clients.
Final Thoughts
Undoubtedly, extrusion welding is a crucial process for plastic fabrication, and its significance cannot be overstated. With the help of this technique, professionals can create durable and high-quality plastic structures to meet various industry requirements. As discussed, extrusion welding involves combining plastic materials through the application of heat and pressure, and it has numerous applications, including tanks, pipes, geomembranes, and more.
Whether you are a novice or seasoned professional, it is essential to understand the basics and techniques of extrusion welding to use it effectively in plastic fabrication. It requires the right equipment, temperature control, and expertise to achieve optimal results.
The advancements and innovations in extrusion welding technology have made the process more efficient and precise, leading to better-quality plastic structures. With the emergence of new welding techniques and equipment, the future of extrusion welding looks promising.
In conclusion, extrusion welding is an effective and reliable method for creating strong and durable plastic structures. For plastic fabrication needs, this technique remains a top choice for professionals who desire high-quality results.
FAQs
What is extrusion welding?
Extrusion welding is a plastic welding technique used to join thermoplastics together. It involves the use of an extrusion welding machine to melt and fuse the plastics, creating a strong and durable bond.
How does the extrusion welding process work?
The extrusion welding process begins with the preparation of the workpieces, ensuring they are clean and properly aligned. The welding machine’s nozzle is then placed between the workpieces, and a plastic welding rod is fed into the machine. The machine heats the rod and the adjacent plastic surfaces, melting them. The molten plastic is then pressed together, creating a homogenous weld.
What are the advantages of extrusion welding?
Extrusion welding offers several advantages, including the ability to join large and complex plastic structures, high weld strength, and excellent structural integrity. It is also a versatile process that can be used with various thermoplastics, making it suitable for a wide range of applications.
What types of plastics can be extrusion welded?
Extrusion welding is compatible with numerous thermoplastics, including polyethylene, polypropylene, PVC, ABS, and HDPE. However, it is essential to consider the specific properties of the plastic being welded to ensure suitable welding conditions and a successful bond.
What is the recommended extrusion welding temperature?
The recommended extrusion welding temperature varies depending on the type of plastic being welded. Generally, temperatures range from 200°C to 300°C (392°F to 572°F). It is crucial to follow the manufacturer’s guidelines and perform temperature tests to achieve optimal welding results.
What are some common applications of extrusion welding?
Extrusion welding has various applications across industries, including the fabrication of plastic tanks, pipes, geomembranes, and lining systems. It is also used in the construction of chemical storage facilities, landfill sites, and water treatment plants.
Is extrusion welding a suitable method for repairing plastic components?
Yes, extrusion welding can be utilized for repairing damaged plastic components. By melting and fusing the damaged area with a compatible welding rod, extrusion welding restores the structural integrity of the component.
What safety precautions should be followed during extrusion welding?
When performing extrusion welding, it is essential to wear appropriate personal protective equipment (PPE), such as safety glasses, gloves, and protective clothing. Adequate ventilation is necessary to prevent exposure to fumes. Additionally, operators should be trained in the safe operation of the equipment and follow proper machine maintenance procedures.
Can extrusion welding be automated?
Yes, extrusion welding can be automated by integrating extrusion welding machines into production lines. This automation enhances efficiency and productivity, particularly in high-volume manufacturing settings.
How can I choose the right extrusion welding equipment?
When selecting extrusion welding equipment, consider factors such as the type of plastic being welded, the required welding speed, and the specific application. It is essential to choose a reliable machine from trusted manufacturers and ensure it meets the necessary quality and safety standards.