Welding is an essential process in many industries, and the cost of welding can add up quickly. Whether you’re managing a small business or a large enterprise, reducing welding costs is always a top priority. Luckily, there are many practical tips and techniques you can implement to optimize your welding process and save money.
In this section, we will share cost-saving tips and welding cost reduction techniques that can help you reduce expenses without compromising quality. By following these strategies, you can streamline your welding operations for cost efficiency, maximize welding productivity and efficiency, and implement preventive maintenance practices to optimize welding costs. We’ll explore the importance of selecting the right materials and welding techniques and the role of automation and technology solutions in reducing welding costs.
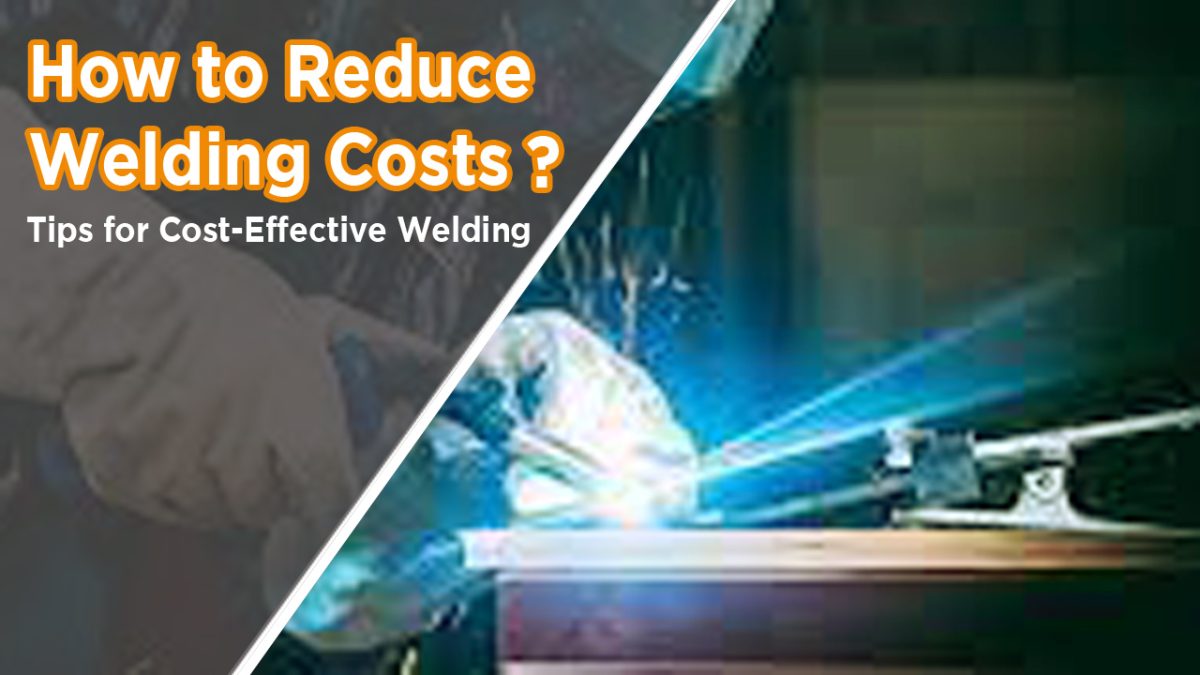
Streamlining Welding Operations for Cost Efficiency
Welding operations can be costly, especially when there’s a lot of waste and inefficiency. However, there are strategies you can use to streamline your welding operations and minimize expenses. By doing so, you can save money and increase profitability without sacrificing quality.
Implement Efficient Workflows
One way to reduce welding costs is to implement efficient workflows. This involves analyzing your current processes and identifying areas where you can improve efficiency. For example, you can rearrange workstations to minimize the distance between workstations, eliminate unnecessary movement, and reduce time spent setting up equipment. By streamlining workflows, you can save time and reduce labor costs.
Reduce Waste
Reducing waste is another effective way to minimize welding expenses. By being more mindful of the materials you use and the way you use them, you can eliminate waste that would otherwise end up in landfills. You can also reduce the amount of time spent cleaning up waste, which can save labor costs.
Invest in Equipment Maintenance
Maintaining welding equipment is essential for preventing costly repairs in the future. By regularly maintaining your equipment and fixing minor issues as they arise, you can avoid the need for more expensive repairs down the road. This helps to keep your welding expenses in check and ensures that your equipment continues to operate efficiently.
Train Your Welders
Well-trained welders are more efficient and produce higher-quality results. By investing in advanced training for your welders, you can boost productivity and reduce labor costs. Training can include everything from basic welding techniques to more advanced methods that help to optimize welding processes. It may even be worth investing in certification programs that will increase your welders’ qualifications.
By implementing these strategies and making a conscious effort to optimize your welding operations, you can effectively minimize expenses and increase profitability. Streamlining workflows, reducing waste, maintaining equipment, and investing in training are just a few ways to improve efficiency and save on welding costs.
Maximizing Welding Productivity and Efficiency
Maximizing welding productivity and efficiency can lead to significant cost savings in welding operations. The following techniques can help lower welding expenditures and decrease welding expenses:
Optimize Equipment Usage
Make the most of your welding equipment by utilizing it to its fullest capacity. Use automatic or robotic welding equipment where possible to reduce labor costs and improve efficiency. Ensure that the equipment is well-maintained and calibrated to avoid wasting time and energy on unnecessary welds or rework.
Improve Welder Training
Properly trained welders can increase productivity and reduce welding errors, ultimately lowering costs. Invest in welder training programs to ensure that your welders have the necessary skills and knowledge to complete the job efficiently and effectively.
Implement Time-Saving Measures
Time is money, so finding ways to save time in the welding process can lead to significant cost savings. Consider using welding positioners or fixtures to hold the workpiece in place and reduce the time spent repositioning it. Preparing the workpiece before welding, such as cutting, grinding, and beveling, can also save time in the welding process and reduce the risk of errors.
Selecting the Right Materials and Welding Techniques
One of the most important factors in achieving cost-effective welding is selecting the right materials and welding techniques for the job. By choosing the right materials, you can cut down on costs without sacrificing quality. Similarly, utilizing the most efficient welding techniques can help you save money on labor and time.
Tips for Cost-Effective Welding
- Consider using lower-cost materials that still meet the quality requirements of the project. For example, utilizing a lower grade of steel or aluminum can significantly reduce costs.
- Look for discount options when purchasing materials in bulk or sourcing them from different suppliers. You might even consider purchasing second-hand materials that are still in good condition.
- Choose welding techniques that don’t require too much preparation or finishing work. For instance, using submerged arc welding can reduce the need for pre-cleaning and post-finishing.
- Invest in materials that are easier to weld and require less time for welding. This can help to reduce labor and equipment costs.
How to Save Money on Welding?
Aside from selecting the right materials, there are also several techniques you can utilize to minimize welding costs. Some of these include:
- Maximizing machine uptime through preventive maintenance. By regularly servicing and maintaining your welding equipment, you can avoid unplanned downtime that can cut into productivity and increase costs.
- Implementing automation or semi-automation where possible. By utilizing robots or other machinery, you can reduce the need for manual labor and save money on wages and time.
- Continuously evaluating and optimizing your welding processes to identify areas where you can cut costs. For example, you might discover that you’re using too much shielding gas or that certain welding positions require more equipment and time.
- Providing training and resources for your welders to ensure that they are using the most efficient and cost-effective techniques.
Overall, selecting the right materials and welding techniques and utilizing these cost-saving methods can help you achieve significant savings in your welding operations.
Implementing Preventive Maintenance Practices
Regular maintenance and inspection of welding equipment can significantly reduce costs related to repairs and downtime, providing long-term cost savings. Preventive maintenance practices encompass a variety of activities aimed at extending equipment life, avoiding unexpected failures and minimizing repair costs. A variety of techniques are available to optimize welding equipment lifespan and minimize expenses:
- Keeping welding equipment clean, properly lubricated, and free of moisture and dust
- Ensuring proper alignment and calibration of welding machines
- Replacing worn or damaged parts promptly, such as welding nozzles and consumables
- Conducting regular inspections of welding equipment to identify potential issues early on
- Providing regular training to welders on the proper use and care of equipment
- Using condition monitoring techniques, such as vibration analysis, to identify potential issues before they become costly problems
By implementing preventive maintenance practices, welding operations can reduce the amount of money spent on repairs, downtime, and replacement equipment. Moreover, proactive maintenance promotes a safer and more dependable working environment for welding operators, which in turn, boosts productivity and efficiency.
Exploring Automation and Technology Solutions
One of the most effective ways to reduce welding costs is by exploring automation and technology solutions. Welding automation involves using machines to carry out welding tasks, thereby reducing labor costs and increasing productivity.
Automated welding systems can perform repetitive welding tasks with a high degree of accuracy, speed, and consistency. This means that welders can focus on tasks that require specialized skills, while reducing the overall time and cost associated with welding.
The Benefits of Welding Automation
Welding automation offers several benefits that can help reduce welding costs:
- Increased efficiency and productivity
- Reduced labor costs
- Improved weld quality and consistency
- Lowered material costs and waste
- Safer working conditions for welders
Aside from welding automation, technology solutions such as virtual and augmented reality can help reduce welding costs. With virtual and augmented reality, welders can train in realistic environments without the need for physical equipment. This reduces training costs and ensures that welders are adequately trained to carry out tasks when they are hired.
Examples of Welding Automation Solutions
There are several welding automation solutions available, including:
Product | Description |
---|---|
Welding Robots | Robotic systems that can carry out welding tasks with a high degree of precision and speed. They can perform tasks that are repetitive, dangerous, or require a high level of skill. |
Automated Welding Cells | Cell-based systems that can perform multiple welding tasks in succession for a particular project. They can also be customized for specific applications and product lines. |
Welding Positioners | Rotating units that can adjust the workpiece to the most convenient angle and orientation for welding. They reduce the time and effort needed to reposition the workpiece and improve the quality and consistency of welds. |
By implementing welding automation and technology solutions, you can achieve significant cost savings in your welding operations, reduce labor and material costs, and improve productivity and efficiency. However, it is essential to choose the right solutions that fit your welding needs and ensure that they are properly maintained and optimized to achieve optimal results.
Final Thoughts
We hope these practical tips and techniques have provided you with valuable insights into reducing welding costs. Remember, cost savings should never come at the expense of quality or safety. By implementing the right strategies, you can optimize your welding operations for both efficiency and cost-effectiveness.
Going forward, it’s crucial to continuously evaluate your processes and look for areas of improvement. By incorporating preventive maintenance practices, utilizing advanced welding technology and automation, and optimizing equipment usage and welder training, you can achieve significant cost savings without compromising on quality.
Remember, welding cost reduction is an ongoing process, and you must continuously strive for improvement to stay ahead of the competition. Implement these cost-saving measures today, and start realizing the benefits of optimized and efficient welding operations.
FAQ
What are some practical tips for reducing welding costs?
There are several effective techniques for reducing welding costs. Some of these include optimizing welding parameters, minimizing material waste, and implementing lean manufacturing principles. By focusing on efficiency and waste reduction, you can save money on welding operations.
How can I minimize welding expenses?
To minimize welding expenses, you can consider using pre-cut and pre-formed materials, which reduce the need for material preparation. Additionally, investing in efficient welding equipment and training your operators to use it effectively can help optimize productivity and minimize costs.
What strategies can I use to lower welding expenditures?
There are several effective strategies for lowering welding expenditures. These include streamlining workflow processes, utilizing automated welding systems, and implementing effective material sourcing strategies. By optimizing your operations and making smart choices, you can reduce welding expenses.
How can I decrease welding expenses while maximizing productivity?
To decrease welding expenses while maximizing productivity, you can focus on improving welder training and optimizing equipment usage. By ensuring your welders have the necessary skills and knowledge, and by properly maintaining and utilizing your equipment, you can achieve higher productivity and lower expenses.
What are some tips for cost-effective welding?
To achieve cost-effective welding, it is important to carefully select the right materials and welding techniques for your specific project. Additionally, optimizing welding parameters, such as arc length and travel speed, can help minimize costs while maintaining quality.
How can implementing preventive maintenance practices help optimize welding costs?
Implementing preventive maintenance practices, such as regular equipment inspections and timely repairs, can help avoid costly breakdowns and downtime. By ensuring your welding equipment is properly maintained, you can reduce repair expenses and maximize productivity.
What are the benefits of exploring automation and technology solutions for reducing welding costs?
Automation and technology solutions, such as robotic welding systems and advanced welding machines, can significantly reduce labor costs and improve productivity. These solutions offer precise control and repeatability, resulting in higher quality welds and reduced material waste.