Curious about the sparks flying in the world of metal fabrication? Let’s delve into the realm of resistance welding. This ingenious process joins metal components using heat generated by electrical resistance. From automotive to aerospace industries, resistance welding is the unsung hero behind robust and efficient metal assemblies.
Whether you are a seasoned welder or just embarking on your fabrication journey, understanding the nuances of resistance welding is pivotal. This article aims to demystify the intricacies, applications, and advancements in resistance welding, empowering you to make informed decisions in your metalworking endeavors.
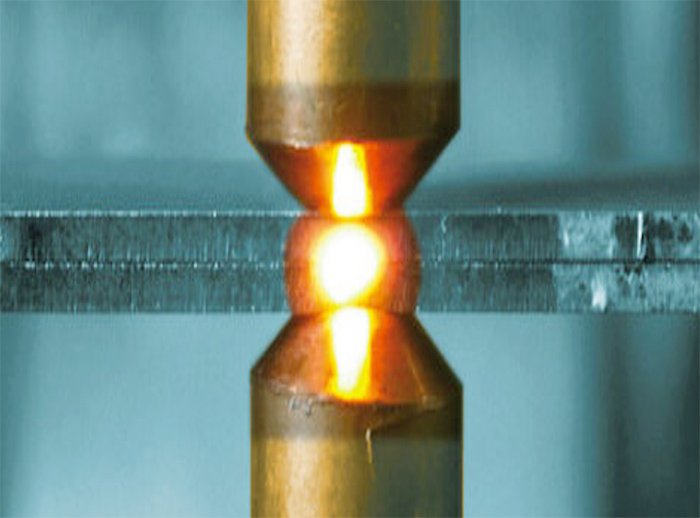
Image: electricaldesks
So, buckle up as we embark on a journey through the sizzling world of resistance welding, exploring its diverse techniques, benefits, and the pivotal role it plays in shaping the modern industrial landscape. Join us as we unravel the sparks, science, and success stories woven within the realm of resistance welding. Ready to spark your curiosity? Let’s ignite the flame of knowledge!
Types of Resistance Welding Techniques
Resistance welding encompasses various techniques, each tailored to specific applications and materials. The most common methods include spot welding, seam welding, projection welding, and flash welding.
Spot Welding: This technique is widely used to join overlapping metal sheets by applying pressure and passing a high electrical current through the metal. It’s popular in automotive and aerospace industries for its speed and efficiency in creating strong, durable welds.
Seam Welding: Seam welding involves continuously welding the length of overlapping metal sheets, producing a leak-tight and uniform joint. This technique is ideal for manufacturing fuel tanks, pipes, and other cylindrical components.
Projection Welding: In projection welding, localized heat is generated at predetermined spots on the metal components, creating strong welds at specific points. It’s commonly used in the production of wire mesh, fasteners, and electrical components.
Flash Welding: Flash welding utilizes the heat generated by electrical resistance to join large, complex metal components. The process involves creating an arc between the workpieces, resulting in a high-strength bond. It’s often employed in the fabrication of railway tracks, pipes, and heavy machinery components.
Advantages of Resistance Welding
Resistance welding offers a myriad of benefits that make it a preferred choice in various industries. One of its primary advantages is the ability to create strong, reliable welds without the need for additional materials such as filler metals or flux.
Furthermore, resistance welding is highly efficient, with rapid cycle times and minimal heat-affected zones, ensuring the structural integrity of the welded components. Its suitability for automation and integration into production lines makes it a cost-effective solution for mass production.
The process also boasts environmental advantages, as it produces minimal fumes, gases, and waste materials compared to traditional welding methods. This aligns with the growing emphasis on sustainable manufacturing practices across industries.
Applications of Resistance Welding in Different Industries
Resistance welding finds extensive use across a spectrum of industries, ranging from automotive and aerospace to electronics and construction. In the automotive sector, it’s pivotal in the assembly of car bodies, exhaust systems, and battery packs, contributing to the structural integrity and longevity of vehicles.
In the aerospace industry, resistance welding plays a crucial role in fabricating aircraft components, fuel tanks, and hydraulic systems, meeting the stringent quality and safety standards required for aerospace applications.
The electronics industry benefits from resistance welding in the production of circuit boards, wire harnesses, and semiconductor packaging, ensuring precise and reliable connections essential for electronic devices’ functionality.
Additionally, the construction sector leverages resistance welding for manufacturing pipelines, structural components, and reinforcing mesh, delivering robust and durable structures for various infrastructure projects.
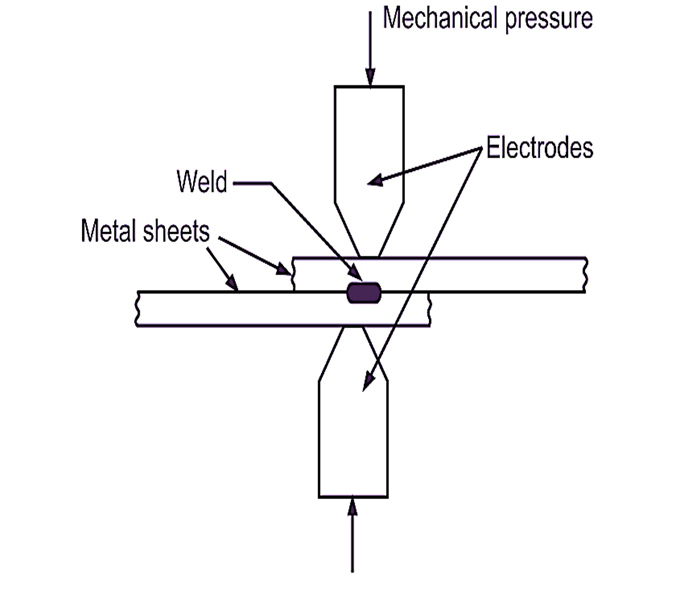
Image: electricaldesks
Factors to Consider for Successful Resistance Welding
Achieving optimal results in resistance welding requires careful consideration of several factors. The selection of appropriate welding parameters, including current, time, and pressure, is critical to ensure consistent and robust welds. Material properties such as conductivity, thickness, and surface condition significantly influence the welding process.
Understanding the behavior of different metals under electrical resistance is essential for achieving high-quality welds. The design of the welding electrodes and fixtures, as well as the maintenance of the welding equipment, also play a vital role in ensuring the repeatability and accuracy of the welding process.
Common Challenges in Resistance Welding and How to Overcome Them
Despite its numerous advantages, resistance welding presents certain challenges, including electrode wear, material inconsistency, and heat dissipation. Addressing these challenges requires a combination of advanced equipment, precise process control, and thorough material testing.
Implementing preventive maintenance programs for the welding equipment, optimizing electrode designs, and employing advanced monitoring and control systems can mitigate the impact of these challenges, ensuring consistent and high-quality welds.
Safety Measures in Resistance Welding
Ensuring the safety of personnel involved in resistance welding operations is paramount. Adequate training, personal protective equipment, and adherence to established safety protocols are essential to prevent electrical hazards, heat-related injuries, and exposure to fumes and radiation.
Employing safety interlocks, ventilation systems, and periodic safety audits further enhance the overall safety of resistance welding operations, creating a secure working environment for welding professionals.
Future Developments in Resistance Welding Technology
As industries continue to evolve, so does resistance welding technology. The integration of advanced automation, robotics, and data analytics is poised to revolutionize the efficiency and precision of resistance welding processes, catering to the increasing demand for high-volume, customized production.
Moreover, ongoing research and development efforts focus on enhancing the compatibility of resistance welding with new materials, such as composites and lightweight alloys, expanding its applicability in emerging industries and next-generation manufacturing technologies.
Training and Certification in Resistance Welding
Proficiency in resistance welding techniques and processes is best attained through comprehensive training and certification programs. These programs equip welders and industry professionals with the knowledge and skills necessary to perform resistance welding operations effectively and safely.
Certification in resistance welding not only validates an individual’s expertise but also ensures compliance with industry standards and regulations, reinforcing the commitment to quality and excellence in metal fabrication.
Conclusion
Resistance welding stands as a cornerstone in the realm of metal fabrication, offering a versatile, efficient, and reliable means of joining metal components across diverse industries. Its continued evolution, coupled with advancements in technology and materials, underscores its enduring relevance in the modern industrial landscape. As we have journeyed through the diverse techniques, advantages, applications, and future prospects of resistance welding, we have gained a deeper appreciation for its pivotal role in shaping the world of manufacturing and engineering.
Armed with this knowledge, both seasoned professionals and aspiring welders are empowered to harness the potential of resistance welding, driving innovation, and excellence in metalworking endeavors. So, the next time you witness the sparks of resistance welding, remember the intricate science and engineering prowess behind this remarkable process. It’s not just about sparks; it’s about igniting the future of metal fabrication.