Pipeline welding is a specialized field that involves joining segments of pipes to create a continuous network for transporting crucial resources such as oil, natural gas, and water. This process is essential for maintaining the infrastructure that powers the modern world. Pipeline welders play a critical role in ensuring the integrity and safety of these vital systems. From the construction of new pipelines to the maintenance and repair of existing ones, pipeline welding demands a high level of expertise, precision, and dedication.
The fusion of technical know-how, advanced welding techniques, and stringent safety protocols distinguishes pipeline welding from other forms of welding. It requires a deep understanding of various welding processes, materials, and environmental factors. Whether it’s laying miles of pipeline across rugged terrain or working on intricate connections in confined spaces, pipeline welding presents unique challenges that demand specialized skills and experience.
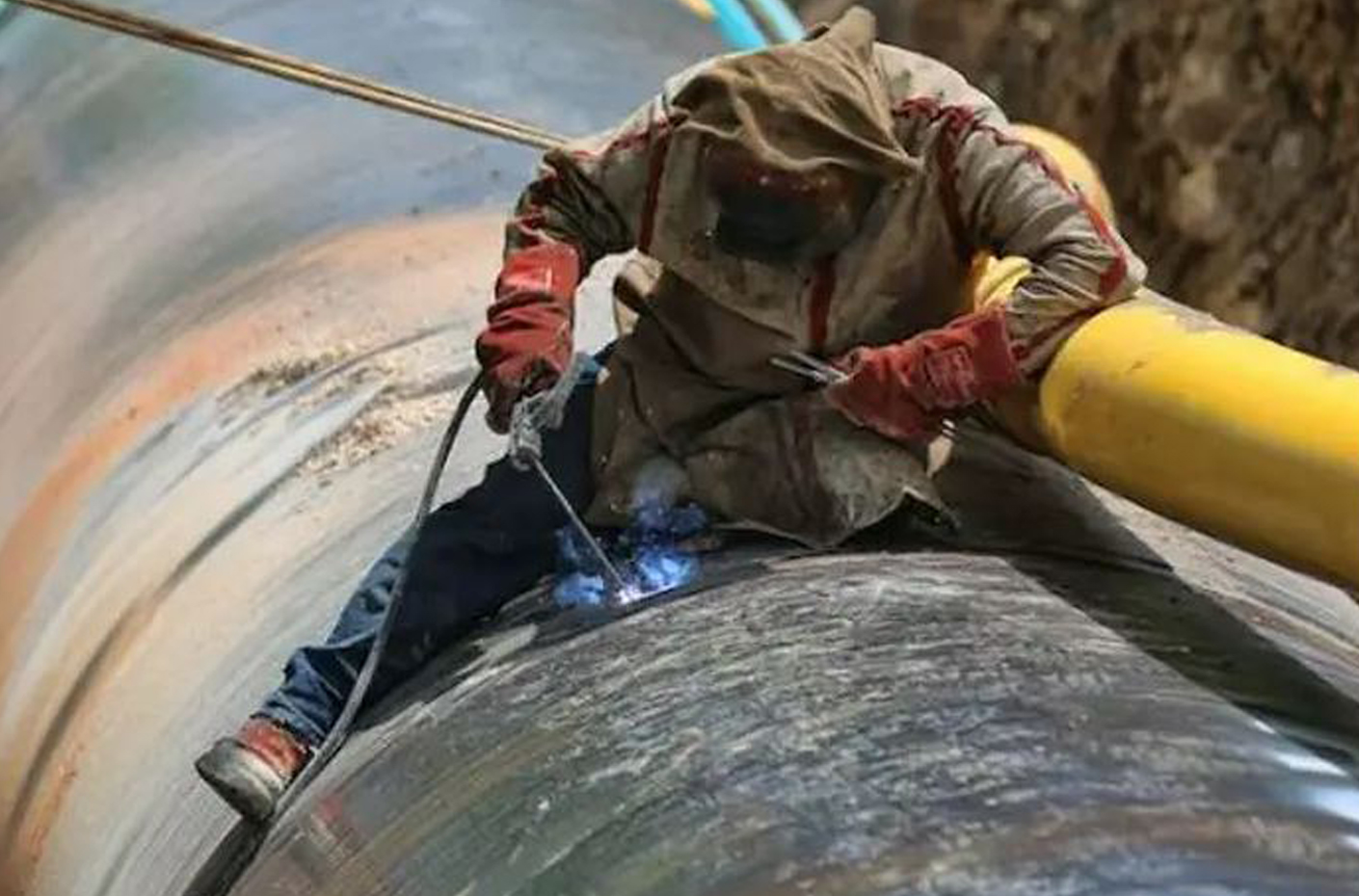
As the demand for energy and infrastructure continues to grow, the importance of proficient pipeline welders cannot be overstated. Their work forms the backbone of the energy industry, enabling the reliable and efficient transportation of vital resources across vast distances. In this article, we will explore the intricacies of pipeline welding, shedding light on the techniques, equipment, safety measures, and qualifications that define this essential trade.
Importance of Pipeline Welding
The significance of pipeline welding extends far beyond the welding process itself. It directly impacts the reliability, safety, and efficiency of the infrastructure that sustains our modern way of life. Pipelines serve as the lifelines of the energy industry, facilitating the transportation of oil, natural gas, and other essential resources from production sites to distribution centers and end-users. Without robust and well-maintained pipelines, the entire energy supply chain would be compromised.
Efficient pipeline welding ensures the structural integrity of the network, minimizing the risk of leaks, ruptures, and environmental hazards. By creating strong, durable connections between pipe segments, skilled pipeline welders contribute to the seamless flow of resources that power homes, businesses, and industries. Moreover, effective pipeline welding plays a crucial role in preventing costly downtime, operational disruptions, and environmental damage that can result from pipeline failures.
Beyond the energy sector, pipeline welding also supports the transportation of water, chemicals, and other essential fluids. The reliable infrastructure created by proficient pipeline welders is vital for various industries, including agriculture, manufacturing, and municipal utilities. As the global demand for energy and resources continues to rise, the expertise of pipeline welders becomes increasingly indispensable in ensuring the resilience and sustainability of critical infrastructure.
Types of Pipeline Welding
Several welding processes are commonly used in pipeline construction and maintenance, each offering unique advantages and applications. The choice of welding process depends on factors such as the type of materials being welded, the environmental conditions, and the specific requirements of the project. Among the primary pipeline welding processes are shielded metal arc welding (SMAW), gas metal arc welding (GMAW), flux-cored arc welding (FCAW), and gas tungsten arc welding (GTAW).
- Shielded metal arc welding: Shielded metal arc welding, also known as stick welding, is a widely used process for pipeline welding due to its portability and versatility. It involves the use of a consumable electrode coated in flux to create the weld.
- Gas metal arc welding: Gas metal arc welding, on the other hand, utilizes a continuous solid wire electrode and a shielding gas to protect the weld from atmospheric contamination, making it suitable for welding various types of steel and alloys.
- Flux-cored arc welding: Flux-cored arc welding combines elements of both stick and MIG welding, offering high deposition rates and enhanced productivity, particularly in outdoor and windy conditions.
- Gas tungsten arc welding: Gas tungsten arc welding, commonly referred to as TIG welding, is favored for its precision and ability to produce high-quality welds in thin materials. While not as commonly used for pipeline welding as other processes, GTAW finds application in specialized projects that demand exceptional weld quality and control.
Each welding process has its own set of benefits and considerations, and experienced pipeline welders are proficient in selecting and executing the most suitable process for each unique application.
Pipeline Welding Equipment and Tools
Pipeline welding demands specialized equipment and tools designed to meet the unique challenges of working in diverse environments and conditions. Essential tools for pipeline welding include welding machines, welding rigs, welding generators, welding electrodes, welding wire, and various hand tools. Welding machines, specifically designed for field welding, must be capable of providing consistent and reliable power output while being rugged enough to withstand the rigors of pipeline construction and maintenance.
Welding rigs, commonly mounted on trucks or trailers, serve as mobile workstations that house welding equipment and tools, providing a versatile and efficient setup for on-site welding operations. Welding generators are crucial for providing power to welding machines and other electrical tools in remote or off-grid locations. The selection of welding electrodes and wire is critical, as different materials and welding processes require specific consumables to achieve high-quality and durable welds.
In addition to welding-specific equipment, pipeline welders rely on a range of hand tools, such as grinders, clamps, cutting torches, and measuring instruments, to prepare and assemble the pipe sections for welding. Safety equipment, including personal protective gear, welding helmets, and ventilation systems, is also indispensable for ensuring the well-being of welders working in hazardous or confined spaces. The proper selection and maintenance of welding equipment and tools are fundamental to the success and safety of pipeline welding projects.
Safety Measures in Pipeline Welding
Safety is paramount in pipeline welding, given the demanding nature of the work and the potential hazards associated with welding operations. Pipeline welders are exposed to various risks, including electric shock, fumes and gases, fire and explosion, confined spaces, and heavy equipment. As such, stringent safety measures and protocols are essential to protect the well-being of welders and ensure the integrity of the welding process.
Before commencing any welding activities, thorough risk assessments and hazard evaluations are conducted to identify potential dangers and implement appropriate control measures. Adequate training in the safe use of welding equipment, handling of hazardous materials, and emergency procedures is essential for all personnel involved in pipeline welding projects. Personal protective equipment, such as flame-resistant clothing, gloves, safety glasses, and respiratory protection, is mandatory to mitigate the risks of exposure to heat, sparks, and welding fumes.
Proper ventilation and air monitoring are critical, particularly when welding in confined spaces or in the presence of hazardous substances. Fire prevention and suppression systems, as well as hot work permits, are implemented to minimize the risk of fire and explosion. Additionally, strict adherence to industry regulations and standards, such as those set forth by the Occupational Safety and Health Administration (OSHA) and the American Petroleum Institute (API), is integral to maintaining a safe working environment and preventing accidents and injuries.
Qualifications and Skills for Pipeline Welders
Becoming a proficient pipeline welder requires a combination of formal education, hands-on training, and practical experience. While a high school diploma or equivalent is typically the minimum educational requirement, aspiring pipeline welders often pursue vocational or trade school programs that offer specialized training in welding techniques, blueprint reading, metallurgy, and safety practices. Some may choose to enroll in apprenticeship programs, where they receive on-the-job training under the guidance of experienced welders.
In addition to technical knowledge, pipeline welders must possess strong problem-solving abilities, spatial awareness, and a keen eye for detail. Familiarity with welding codes and standards, such as those established by the American Welding Society (AWS) and the American Society of Mechanical Engineers (ASME), is essential for ensuring the quality and compliance of welded joints. Proficiency in interpreting welding symbols, understanding metallurgical properties, and performing non-destructive testing (NDT) is also valuable in the field of pipeline welding.
Furthermore, physical fitness and dexterity are crucial attributes for pipeline welders, as the work often involves lifting, bending, and working in challenging environments. Effective communication and teamwork skills are essential for collaborating with other tradespeople, supervisors, and project stakeholders.
As the demand for skilled pipeline welders continues to grow, individuals who demonstrate a strong work ethic, a commitment to safety, and a willingness to adapt to new technologies and welding processes are well-positioned for success in this dynamic and rewarding profession.
Pipeline Welding Techniques
The successful execution of pipeline welding relies on the application of various welding techniques tailored to the specific requirements of each project. Butt welding, a common technique in pipeline construction, involves joining two pipe segments end-to-end to create a continuous connection. This technique demands precise alignment and welding to ensure the strength and integrity of the joint. Welders often employ mechanized welding processes, such as automatic welding systems and orbital welding, to achieve consistent and high-quality welds in long sections of pipeline.
In addition to butt welding, branch welding and tie-in welding are employed to connect branch pipes and fittings to the main pipeline, requiring specialized skills in fitting and alignment. The use of preheat and post-weld heat treatment techniques is essential for controlling the cooling rate and preventing weld cracking in high-stress areas. Hydrostatic testing, a non-destructive method of evaluating the integrity of welded joints by pressurizing the pipeline with water, is commonly performed to ensure the reliability of the welds under operating conditions.
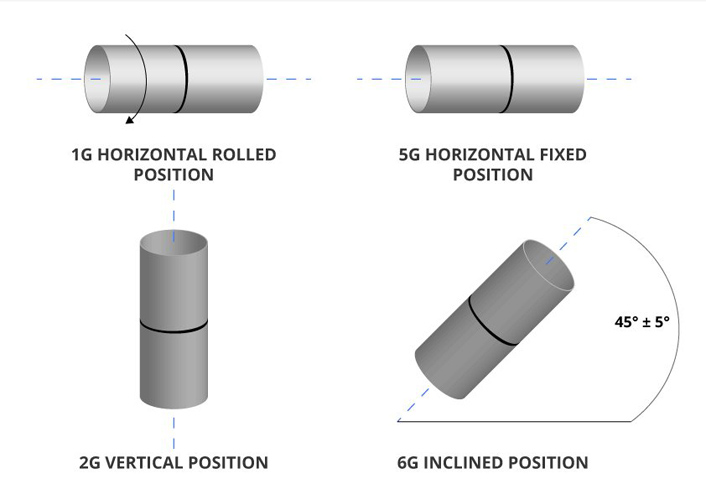
Image: twi-global
Pipeline welders are also adept at performing repair and maintenance welding, addressing issues such as corrosion, pitting, and mechanical damage in existing pipelines. They utilize techniques such as weld overlay and in-situ welding to restore the structural integrity and extend the service life of pipelines. The ability to adapt welding techniques to diverse materials, pipe diameters, and environmental factors is a hallmark of skilled pipeline welders, enabling them to meet the complex and evolving demands of the industry.
Challenges in Pipeline Welding
Pipeline welding presents a myriad of challenges that demand a high level of expertise, adaptability, and problem-solving skills from welders. Working in remote and environmentally diverse locations, pipeline welders must contend with extreme weather conditions, rugged terrain, and logistical complexities. The need to maintain precise welding parameters, such as temperature control and shielding gas coverage, becomes particularly challenging in outdoor settings and adverse weather.
Moreover, the construction and maintenance of pipelines often involve working in confined spaces, elevated locations, or underwater environments, requiring welders to navigate complex safety considerations and access challenges. Ensuring the quality and integrity of welds in such conditions demands specialized equipment, advanced welding techniques, and meticulous attention to detail. Welders must also be vigilant in detecting and addressing potential defects, such as porosity, lack of fusion, and weld discontinuities, which can compromise the performance and longevity of the pipeline.
Another prominent challenge in pipeline welding is the need to comply with stringent industry standards and regulations governing the quality, testing, and documentation of welded joints. Welders must demonstrate a comprehensive understanding of welding codes and specifications, as well as the ability to produce welds that meet the rigorous criteria for strength, durability, and integrity. Continuous training and certification in the latest welding technologies and techniques are essential for pipeline welders to stay abreast of industry best practices and advancements.
Pipeline Welding Certifications and Training
Obtaining relevant certifications and training is an integral part of a pipeline welder’s professional development. Various organizations, such as the American Welding Society (AWS), the American Petroleum Institute (API), and the Pipeline Welding Association (PWA), offer certification programs tailored to pipeline welding. These certifications validate the skills and competencies of welders in performing specific welding procedures, adhering to industry standards, and ensuring the quality of welded joints.
Certifications such as the AWS Certified Welder and the API 1104 Welding of Pipelines and Related Facilities are highly regarded in the industry, signaling a welder’s proficiency in the specialized techniques and quality requirements of pipeline welding. These certifications often involve practical welding tests, written examinations, and ongoing recertification to ensure that welders maintain the highest standards of performance and safety. Additionally, specialized training programs focusing on pipeline welding techniques, safety protocols, and industry-specific requirements are valuable for welders seeking to advance their careers in this field.
Continuous education and professional development are essential for pipeline welders to stay ahead of industry trends, technological advancements, and regulatory changes. Many employers prioritize hiring welders with relevant certifications and a commitment to ongoing training, recognizing the value of a skilled and knowledgeable workforce in maintaining the integrity and reliability of critical infrastructure.
As the demand for pipeline welders continues to grow, the pursuit of certifications and training opportunities can enhance welders’ career prospects and open doors to diverse and rewarding opportunities within the energy and construction sectors.
Conclusion
Pipeline welding stands as a cornerstone of the energy industry, uniting the intricate network of pipelines that form the lifelines of modern civilization. Skilled pipeline welders play a pivotal role in constructing, maintaining, and ensuring the integrity of these vital systems, employing specialized techniques, equipment, and safety measures to meet the complex demands of the trade. From butt welding and mechanized processes to adhering to stringent industry standards, pipeline welders exemplify the fusion of technical expertise, precision, and innovation that powers the veins of our world.
As the global demand for energy and critical resources continues to evolve, the importance of proficient pipeline welders remains unwavering. Their contributions to the construction and maintenance of pipelines extend beyond welding joints; they form the bedrock of a resilient and efficient infrastructure that sustains industries, communities, and economies.
With a commitment to continuous training, adherence to safety protocols, and a dedication to mastering the art of pipeline welding, professionals in this field stand poised to shape the future of essential infrastructure and drive the progress of the energy industry.
FAQ’s
1. Is Pipeline Welding Difficult?
Pipeline welding is often more challenging than from other types of welding and requires a higher level of skill and experience. This can be due to the working conditions as well as factors such as the travel angle of the weld, the pipe position and the diameter of the pipeline. The difficulty increases as the position changes from 1G to 6G .
2. What is 5g Pipeline Welding?
5G pipe welding relates to the position in which the pipeline is welded. In 5G welding, the pipes are placed horizontally in a fixed position and the welder moves around the pipelines, welding in a vertical direction.
3. Is Pipeline Welding Dangerous?
Pipeline welding can be dangerous if the correct precautions are not taken. Welding can expose welders to fumes, dust and other airborne particles, as well as heat and dangerous levels of light that can be harmful without the correct safety equipment. The hazards are increased due to the conditions that pipe welders may be required to operate in, making pipe welding potentially dangerous.
4. What is 6g Pipeline Welding?
6G pipe welding relates to the position in which the pipe is welded. In this position, the pipeline is placed at an angle so that it slopes at around 45° from the horizontal (X) axis or vertical (Y) axis. The pipe is fixed and the welder moves around the pipeline to perform the weld. This is the most advanced pipe welding position.
5. What is Stove Pipeline Welding?
Stove pipeline welding (sometimes called ‘stovepipe’) is a variant of the manual/shielded metal arc welding (MMA/SMAW) technique. It is one of the most commonly used methods for welding pipelines in industries transporting oil, gas and water and allows for positional welding and high production rates for steel pipeline laying.
6. What is Downhill Pipeline Welding?
Downhill pipeline welding is when the welding is carried out with a downward progression, as opposed to uphill pipe welding, where the welding is carried out with an upward progression. Although uphill welding is considered stronger and is better for thicker materials, it takes longer to perform and has a greater potential for burn through than with downhill welding. On thinner pipe walls, downhill welding lets the welder run ‘hot and fast,’ improving productivity where heat penetration is not such an issue.
7. What is a Pipeline Welder Called?
Pipe welders, as opposed to pipeline welders, are also sometimes called pipefitters, simply just ‘fitters.’ They are responsible for the assembly, maintenance, installation and repair of piping systems and fixtures.