Dual shield welding is a welding technique that uses a flux-cored electrode for shielding and a shielding gas to protect the weld. It is a popular method, especially in industrial and heavy-duty applications, due to its ability to create strong, high-quality welds with minimal spatter and excellent penetration.
The process involves feeding a continuous electrode through a welding gun and into the weld joint while the shielding gas is fed through the gun to protect the weld from atmospheric contamination. The flux in the electrode melts and solidifies to create a slag that covers the weld and protects it from contamination.
One of the unique aspects of dual shield welding is that it can be used with a variety of metals, including carbon steel, stainless steel, and low-alloy steel. It is also suitable for welding thicker materials, making it a popular choice in the construction and fabrication industries.
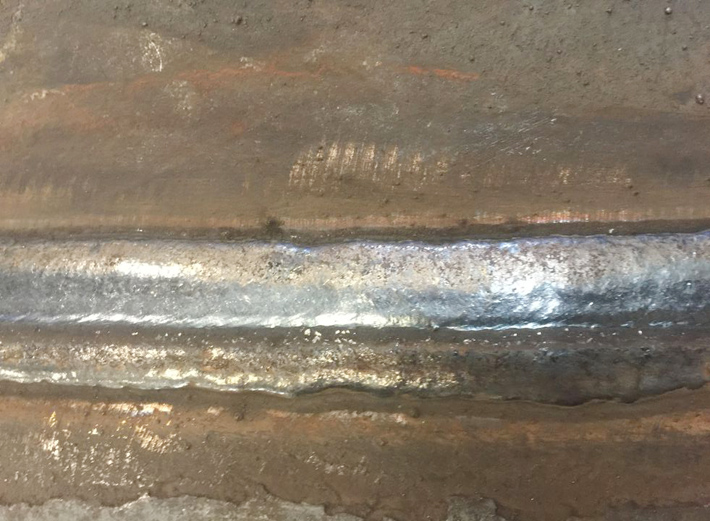
Photos by mail-13.top
Basics of Dual Shield Welding
Dual shield welding is a popular welding method that offers various benefits over other techniques. Let’s explore some of the advantages of this welding method:
- Higher deposition rates: Dual shield welding allows for faster welding speeds due to its higher deposition rates. This results in increased productivity and reduced labor costs.
- Better penetration: The use of flux in welding provides better penetration compared to other welding techniques. This leads to stronger and more robust welds.
- Works well with thick materials: Dual shield welding is particularly effective when working with thicker materials where other techniques may struggle.
- Less dependent on operator skill: Dual shield welding is relatively easy to learn and is less dependent on the operator’s skill level than other welding techniques.
Overall, dual shield welding is a versatile and efficient welding method that is commonly used across various industries.
Understanding the Process of Dual Shield Welding
Dual shield welding is a popular welding technique used to create high-quality welds with excellent mechanical properties. The process involves the use of a continuously fed wire electrode, which is shielded by a fluxing agent that protects the weld pool from atmospheric contamination.
To achieve optimal results in dual shield welding, it is essential to understand the various techniques used and the equipment required for the process. Below, we will delve into the step-by-step process of dual shield welding and explore the techniques and equipment involved.
The dual shield welding process involves the following steps:
- Material preparation: Selecting the proper material and preparing the joint to be welded is a critical step in the dual shield welding process. The joint must be clean and free from any contaminants to ensure successful welding.
- Wire electrode selection: Dual shield welding requires the use of a continuously fed wire electrode. Careful consideration must be taken when selecting the appropriate wire for the application.
- Flux selection: Flux plays a vital role in dual shield welding by shielding the weld pool from atmospheric contamination. The type of flux selected is dependent on the welding application and material being welded.
- Equipment setup: The proper equipment setup is crucial for successful dual shield welding. This includes selecting the correct welding machine, setting the appropriate voltage and amperage, and ensuring the welding gun and wire feeder are in good working order.
- Welding technique: Dual shield welding involves several techniques, including travel speed, weaving, and gun angle. The proper technique is dependent on the application and can impact the overall quality of the weld.
- Quality control: Quality control is crucial in all welding applications, and dual shield welding is no exception. Proper quality control measures should be taken to ensure the weld meets the desired specifications and standards.
Dual Shield Welding Techniques
Dual shield welding techniques vary depending on the application and material being welded. Here are a few commonly used techniques:
- Weaving: The weaving technique involves moving the welding gun in a back-and-forth motion while depositing the molten metal. This technique is useful for creating wider and stronger welds.
- Circumferential welding: Circumferential welding is commonly used in pipe welding applications and involves moving the welding gun in a circular motion around the pipe.
- Stringer beads: Stringer beads involve running a straight bead of weld metal along the joint, producing a narrow, precise weld.
Dual Shield Welding Equipment
Dual shield welding requires specific equipment to achieve optimal results. The equipment required for dual shield welding includes:
Equipment | Purpose |
---|---|
Welding machine | Provides the necessary power to weld the material |
Wire feeder | Feeds the wire electrode into the welding gun |
Welding gun | Deposits the filler material onto the joint being welded |
Flux hopper | Holds and dispenses the fluxing agent onto the weld pool |
Gas flow meter | Regulates the flow of shielding gas used in the welding process |
Understanding the dual shield welding process and the techniques and equipment involved is crucial for achieving optimal welding results. Proper preparation, equipment setup, and technique selection are essential for successful dual shield welding.
The Role of Flux in Dual Shield Welding
Flux is a critical component of the dual shield welding process. It serves multiple purposes, including stabilizing the electric arc, protecting the weld pool from atmospheric contamination, and enhancing the mechanical properties of the finished weld.
Dual shield welding flux is a granular material that is poured into the welding wire before the welding process. The wire electrode is then coated with the flux, which melts and creates a protective gas shield around the weld as it is deposited.
The flux used in dual shield welding is typically made up of a variety of materials, including metal powders, minerals, and chemical compounds. These materials are carefully selected to provide the necessary chemical reactions during the welding process, such as producing shielding gases and refining the weld metal.
Benefits of Flux in Dual Shield Welding | How Flux Works in Dual Shield Welding |
---|---|
Protects the weld from atmospheric contamination Reduces porosity in the weld Enhances the mechanical properties of the finished weld | Produces a protective gas shield around the weld Creates a slag layer that protects the weld pool from contamination Reacts with impurities in the weld to improve its quality |
“The use of flux in dual shield welding is essential for achieving high-quality and durable welds. It not only prevents atmospheric contamination but also improves the weld metal’s mechanical properties, making it ideal for critical applications.”
In addition to its protective properties, the type of flux used in dual shield welding can also influence the welding process’s overall speed and efficiency. For example, some types of flux can be designed to reduce spatter and increase weld deposition rates, leading to faster and more cost-effective welding operations.
Overall, the use of flux in dual shield welding is a crucial step for achieving optimal results. Proper selection and application of flux can lead to high-quality, durable welds that meet the most demanding industry standards.
Dual Shield Welding vs MIG vs TIG Welding – A Comparative Analysis
Dual shield welding is a popular welding technique that offers many benefits over other commonly used welding methods. Let’s take a closer look at how dual shield welding compares to other techniques:
Welding Technique | Advantages | Disadvantages |
---|---|---|
Dual Shield Welding | Provides high deposition rates. Works well with thick materials. Produces less spatter and fumes. Good for outdoor welding. Creates strong, durable welds | Requires a higher initial investment in equipment. Not ideal for thin materials. Requires a high level of skill. May require preheating in certain applications. |
MIG Welding | Fast welding speed. Easy to learn and use. Good for thin materials. | Produces more spatter and fumes. Not ideal for outdoor welding. Weaker welds compared to other methods |
TIG Welding | Produces high-quality, precise welds. Works well with a variety of materials. Good for small, intricate welds. | Requires a high level of skill Slower welding speed compared to other methods. Not ideal for thick materials. |
As shown in the table, dual shield welding offers some significant advantages over other welding techniques. However, it may not be suitable for every application. Welders must consider the thickness of the materials they are working with, the required welding speed, and the desired quality of the weld before choosing a welding method.
“While dual shield welding requires a higher initial investment and a higher skill level compared to other welding methods, it produces strong, durable welds with minimal spatter and fumes.”
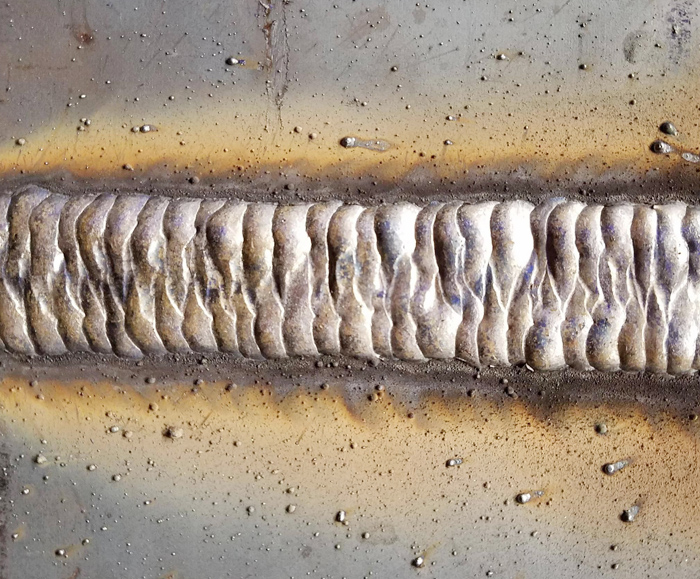
Photos by stilolinea.it
Applications of Dual Shield Welding
Dual shield welding is an effective technique that delivers high-quality results. It is widely used across various industries to join metals with superior strength, durability, and corrosion resistance. Here are some common applications of dual shield welding:
Industry | Applications |
---|---|
Construction | Joining structural steel, welding steel pipes, metal fabrication |
Shipbuilding | Welding marine vessels, joining steel plates and frames |
Aerospace | Welding aircraft parts, joining aluminum and titanium alloys |
Automotive | Welding car frames, joining exhaust systems, repairing automobile parts |
Manufacturing | Welding heavy machinery, joining pressure vessels, welding boilers |
As you can see, dual shield welding is a versatile and robust method that finds applications in many different areas. Its ability to withstand extreme temperatures, pressures, and environmental conditions makes it an ideal choice for welding in demanding industries.
Additionally, dual shield welding enables welders to work with a wide variety of metals, including steels, cast irons, aluminum, copper, and nickel alloys. Its versatility and adaptability make it a valuable asset in any welding project.
Overall, dual shield welding is a popular and reliable method for joining metals and delivering high-quality results. Its widespread usage in diverse fields demonstrates its effectiveness and usefulness for various welding applications.
Advancements in Dual Shield Welding Technology
Over the years, there have been significant advancements in dual shield welding technology, resulting in improved welding efficiency and quality. In this section, we will explore some of the latest developments in dual shield welding technology.
Automated Dual Shield Welding
One of the most significant advancements in dual shield welding is the use of automated welding systems. These systems use robots or computer-controlled equipment to perform welding tasks, improving speed, accuracy, and safety. Automated welding can also reduce labor costs and increase productivity.
Improved Dual Shield Welding Wires
Recent advancements in welding wire technology have resulted in improved performance and efficiency in dual shield welding. Manufacturers have developed wires with better flux coverage, higher deposition rates, and reduced spatter, resulting in higher quality welds.
Advanced Welding Power Sources
Newer welding power sources have been specifically designed to support dual shield welding. These power sources offer greater control over the welding process and produce consistently high-quality welds. They also provide a greater range of welding parameters, making it easier to fine-tune the process for specific applications.
Real-Time Monitoring and Control
Modern welding equipment is equipped with sensors that can monitor the welding process in real-time. This information can be used to adjust the welding parameters, ensuring optimal weld quality. Real-time monitoring and control also allow for the early detection of defects and can prevent the occurrence of welding defects.
Augmented Reality Welding
Another exciting development in dual shield welding technology is the use of augmented reality. Welders can wear AR headsets that provide visual overlays of the welding process, highlighting areas that require attention and displaying real-time welding parameters. This technology enhances welder training, improves accuracy, and reduces the time required for weld inspection.
The advancements in dual shield welding technology have significantly improved the welding process, making it faster, safer, and more efficient. Welders can now achieve high-quality welds with greater ease and accuracy. As technology continues to evolve, we can expect even more exciting developments in dual shield welding.
Preparing for Dual Shield Welding
Before engaging in dual shield welding, there are several essential steps that welders must follow to ensure a successful and safe welding process. These steps include:
- Material Selection: The type and thickness of the materials being welded will determine the welding parameters and equipment needed for the job. It’s essential to choose the appropriate filler metal and shielding gas to achieve optimal results.
- Joint Preparation: Proper joint preparation is crucial to ensure proper fusion and penetration during welding. Joint preparation can include cleaning the joint, aligning the pieces, and beveling the edges to create a V-groove, U-groove, or J-groove.
- Equipment Inspection: Prior to starting the welding process, welders must inspect the equipment to ensure it’s in good working condition. This includes checking the welding machine, wire feeder, torch, and gas regulator.
- Safety Precautions: Safety should always be a top priority when engaging in welding. Welders should wear appropriate personal protective equipment, including gloves, safety glasses, and welding helmets. Adequate ventilation and fire prevention measures should also be in place.
Dual shield welding requires thorough preparation and attention to detail to achieve optimal results. Following these steps will help ensure a successful welding process and maintain a safe working environment.
Dual Shield Welding Tips for Successful Welding
Dual shield welding is a highly effective welding technique that delivers high-quality results. However, achieving successful dual shield welding requires adherence to best practices and careful attention to detail. Here are some tips for successful dual shield welding:
- Select the Right Materials: Use high-quality materials with excellent weldability to ensure a successful welding outcome. Select materials that are compatible with the welding process and have the necessary mechanical properties.
- Prepare the Joint Properly: Proper joint preparation is critical in dual shield welding. Remove any dirt, oil, rust, or other contaminants that could affect the weld quality. Ensure proper fit-up and alignment to promote uniformity.
- Follow the Correct Welding Techniques: Adhere to the correct welding techniques, such as choosing the right current and voltage, welding speed, and travel angle. Follow the recommended procedures for setting up and running the welding equipment.
- Monitor the Welding Environment: Keep the welding environment clean and dry. Monitor the temperature, humidity, and other environmental conditions that could affect the welding process.
- Perform Quality Control: Regularly inspect the welds for quality and accuracy. Use non-destructive inspection methods and destructive testing to ensure that the welds meet the specified requirements.
- Practice Safety Precautions: Always wear the appropriate personal protective equipment (PPE) when welding. Follow safety procedures to minimize the risk of accidents and injuries. Ensure proper ventilation and control of harmful welding fumes.
By following these best practices, you can achieve successful dual shield welding and produce high-quality welds. Always consult the welding procedure specification (WPS) and other relevant welding standards when performing dual shield welding.
Common Challenges in Dual Shield Welding
Like any other welding technique, dual shield welding presents its own set of challenges. Some of the common issues that welders may encounter during the process include:
- Poor fusion between the base metal and the filler material
- Porosity in the weld
- Incomplete penetration
- Excessive spatter
- Cracking
Fortunately, most of these challenges can be addressed through proper troubleshooting techniques. Here are some tips to help welders overcome common challenges in dual shield welding:
- Poor fusion: This issue can be caused by a cold base metal, insufficient heat, or incorrect welding technique. To address this issue, ensure that the base metal is clean, preheated to the proper temperature, and that the welding technique used is appropriate for the material being welded.
- Porosity: Porosity can be caused by a contaminated welding environment, improper shielding gas, or incorrect welding technique. To overcome this challenge, ensure that the welding area is clean and free of contaminants, use the correct shielding gas, and adjust the welding parameters to the appropriate settings.
- Incomplete penetration: Incomplete penetration can be caused by insufficient heat or an incorrect welding technique. To address this issue, ensure that the base metal is properly preheated and the welding technique used is appropriate for the material being welded.
- Excessive spatter: Excessive spatter can be caused by an incorrect welding technique or the use of a contaminated filler material. To overcome this challenge, ensure that the welding technique used is appropriate for the material being welded and that the filler material used is clean and free of contaminants.
- Cracking: Cracking can occur due to a variety of reasons, including improper welding preparation, high levels of residual stress, or a lack of ductility in the welding material. To address this issue, ensure that the joint is properly prepared, use appropriate welding techniques to minimize residual stress, and select materials with appropriate levels of ductility.
By following these troubleshooting tips and techniques, welders can overcome common challenges in dual shield welding and ensure high-quality, consistent results.
Dual Shield Welding Safety Precautions
Safety is paramount when it comes to dual shield welding. The process involves high temperatures and intense light, which means that welders must take necessary safety precautions to avoid accidents or injuries. Here are some essential safety measures that welders must observe when engaging in dual shield welding:
- Welders must wear appropriate PPE, including welding helmets, gloves, and flame-resistant clothing.
- Ensure proper ventilation in the welding area to avoid inhaling toxic gases and fumes generated by the welding process.
- Welders must inspect welding equipment and cables before starting the welding to ensure that they are in good condition and free from damage or defects.
- Welders must use welding screens to protect nearby personnel from the intensely bright light emitted during welding.
- Materials used in dual shield welding may be hot and dangerous to touch. Welders should avoid touching materials with ungloved hands.
- Welders must ensure that the work area is free from flammable materials, as sparks generated during the welding process can ignite these materials.
- Welders should conduct regular safety training and education to enhance their knowledge and skills in dual shield welding safety.
By following these safety precautions, welders can minimize the risks associated with dual shield welding and ensure a safe working environment for themselves and others.
Final Thoughts
As we conclude our discussion on dual shield welding, it is evident that this welding technique offers numerous benefits and advantages over other methods. Dual shield welding provides high-quality and efficient welds, making it a popular choice in various industries and applications. Understanding the dual shield welding process is critical to achieving optimal results. It involves selecting the right equipment, preparing the materials correctly, and taking the necessary safety precautions before commencing the welding process.
Flux plays a crucial role in dual shield welding, facilitating the process by protecting the weld puddle and preventing oxidation. Additionally, advancements in technology have led to significant improvements in the quality and efficiency of the dual shield welding process. As with any welding technique, dual shield welding comes with its set of challenges. However, by adhering to best practices, taking appropriate safety measures, and troubleshooting potential issues, welders can overcome these challenges and achieve excellent welding results.
In conclusion, dual shield welding is a highly effective and versatile welding technique with numerous advantages. With proper preparation, equipment selection, and adherence to safety protocols, welders can achieve optimal results and produce high-quality welds.
FAQ
What is dual shield welding?
Dual shield welding is a welding technique that involves the use of a flux-cored electrode and a shielding gas. The flux-cored electrode contains a flux compound that provides additional protection to the weld, resulting in a stronger and more robust weld joint.
How does dual shield welding work?
In dual shield welding, the flux-cored electrode is continuously fed into the weld joint while a shielding gas is simultaneously supplied to protect the molten weld puddle from atmospheric contamination. The combination of the flux and shielding gas creates a highly efficient and controlled welding process.
What are the benefits of dual shield welding?
Dual shield welding offers several benefits, including increased productivity, improved weld quality, and greater weld penetration. It also provides excellent arc stability and reduced spatter, making it a preferred choice for many welding applications. Additionally, dual shield welding is versatile and can be used for both indoor and outdoor welding projects.
What equipment is required for dual shield welding?
The equipment required for dual shield welding includes a welding machine capable of handling flux-cored welding, a wire feeder, a suitable power source, a welding gun, and a gas cylinder for the shielding gas. It is important to have the appropriate safety gear, such as welding gloves, helmet, and protective clothing, to ensure a safe working environment.
What is the role of flux in dual shield welding?
Flux plays a crucial role in dual shield welding. It acts as a chemical cleaner, removing impurities from the weld joint and protecting the molten weld puddle from atmospheric contamination. The flux also helps in controlling the weld pool shape, improving the weld quality, and facilitating the release of gases during the welding process.
How does dual shield welding compare to other welding techniques?
Dual shield welding offers several advantages over other welding techniques. It provides better penetration and higher deposition rates compared to shielded metal arc welding (SMAW) and gas metal arc welding (GMAW). Dual shield welding also allows for welding in challenging environments and can be used with a wide range of materials, making it a versatile choice for many applications.
What are the common applications of dual shield welding?
Dual shield welding is commonly used in industries such as construction, shipbuilding, heavy equipment manufacturing, and pipeline welding. It is suitable for welding thick materials, structural steel, and pressure vessels. Dual shield welding is also used for repairs and maintenance in various sectors, including automotive, aerospace, and oil and gas.
What advancements have been made in dual shield welding technology?
Dual shield welding technology has advanced significantly in recent years. There have been improvements in wire formulations, allowing for better control of weld quality and reduced spatter. Additionally, advancements in welding machines and equipment have increased efficiency and ease of use, enhancing the overall welding process.
How should one prepare for dual shield welding?
Preparation for dual shield welding involves selecting the appropriate materials, ensuring proper welding preparation, and adhering to safety precautions. It is important to clean and remove any contaminants from the weld joint before welding. Additionally, proper storage and handling of the flux-cored electrode and shielding gas are essential for optimal welding results.
What are some best practices for dual shield welding?
To achieve optimal results in dual shield welding, it is important to maintain a stable arc length, control the travel speed, and ensure the correct wire feed rate. Adequate preheating and interpass temperature control are also crucial. Regular inspection and quality control of the weld joint, as well as proper troubleshooting techniques, can help mitigate potential issues.
What are some common challenges in dual shield welding?
Common challenges in dual shield welding include excessive spatter, improper shielding gas flow, lack of fusion, and inadequate penetration. It is important to troubleshoot these issues by adjusting welding parameters, optimizing the welding technique, and ensuring proper joint preparation. Regular training and experience can help welders overcome these challenges.
What safety considerations should be taken into account in dual shield welding?
Safety is of utmost importance in dual shield welding. It is essential to wear appropriate protective gear, such as welding gloves, helmet, and clothing, to protect against arc radiation, sparks, and heat. Adequate ventilation and proper handling of the welding equipment and materials are also crucial. Following safety guidelines and receiving proper training are essential for a safe working environment.