Welding water pipe is a critical aspect of infrastructure development and maintenance. Proper welding techniques are essential to ensure the integrity and longevity of water pipe systems. Whether it’s for municipal water supply, industrial processes, or residential plumbing, the quality of welding water pipe directly impacts the safety and reliability of the entire water distribution network.
Proper welding techniques not only ensure leak-free joints but also prevent contamination of the water supply. In addition, high-quality welds contribute to the overall efficiency of the water distribution system, reducing the risk of pipe failures and minimizing maintenance costs. This article will explore various aspects of welding water pipe, including different welding processes, safety measures, required equipment, welding techniques, common challenges, best practices, and the importance of training and certification.
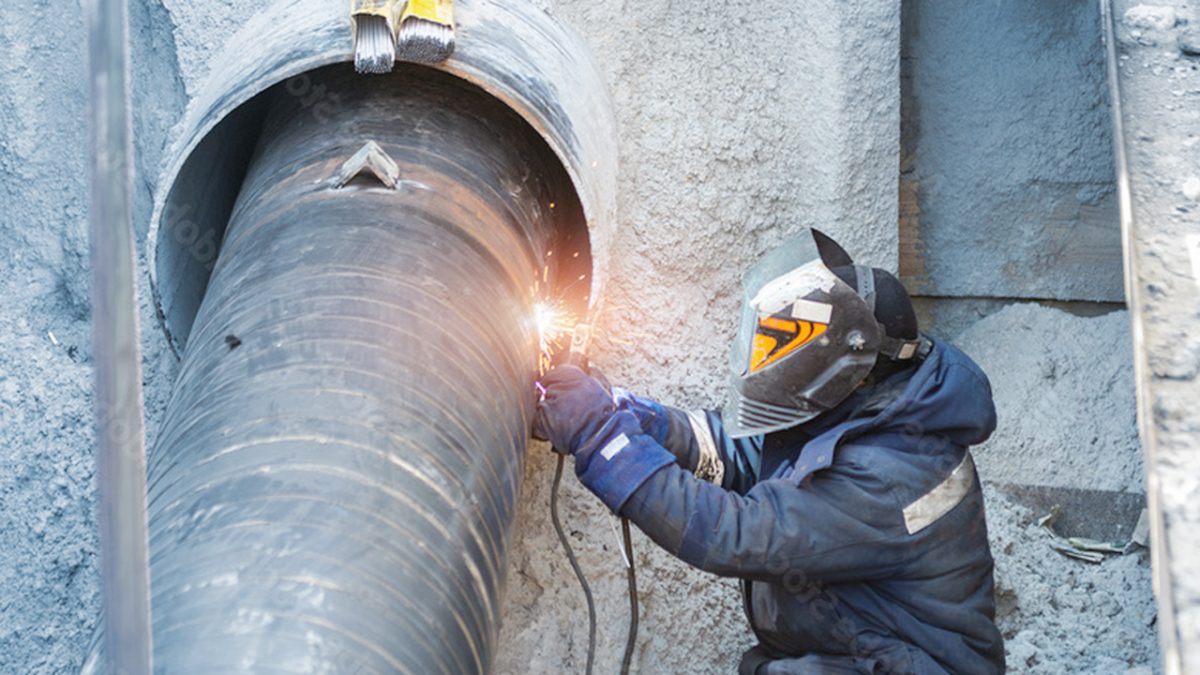
Image by kirill-gorlov on adobe
Welding water pipe plays a crucial role in maintaining public health and safety, as well as supporting industrial and residential activities. Understanding the significance of proper techniques is the first step towards ensuring the reliability and durability of water pipe systems.
Types of Water Pipe Welding Processes
Several welding processes are commonly used for joining water pipes, each with its unique advantages and applications. The two primary types of welding processes for water pipes are fusion welding and MIG welding. Fusion welding, including butt fusion and electrofusion, is widely used for joining thermoplastic pipes, such as high-density polyethylene (HDPE) and polyvinyl chloride (PVC) pipes.
On the other hand, MIG welding, also known as gas metal arc welding (GMAW), is commonly employed for joining metal pipes, including steel and stainless steel. Each welding process requires specific techniques, equipment, and safety measures to achieve durable and reliable welds. Understanding the characteristics of different welding processes is essential for selecting the most suitable method based on the type of water pipe material, project requirements, and environmental conditions.
Choosing the appropriate welding process is crucial for ensuring the structural integrity and leak-free performance of water pipe joints. By exploring the characteristics and applications of fusion welding and MIG welding, water pipe professionals can make informed decisions to achieve high-quality welds that meet industry standards and regulatory requirements.
Welding Safety Measures for Welding Water Pipe
Safety is paramount in welding water pipe, given the potential hazards associated with the process. Prioritizing safety measures not only protects the welding personnel but also ensures the overall integrity and reliability of the water pipe joints. Welding safety measures encompass various aspects, including personal protective equipment (PPE), fire prevention, ventilation, and hazard awareness.
Before initiating any welding operations, it is essential to conduct a thorough risk assessment to identify potential hazards and implement appropriate control measures. Providing comprehensive training to welding personnel on safety protocols and emergency procedures is essential for minimizing the risk of accidents and injuries. Additionally, maintaining a clean and organized work environment reduces the likelihood of tripping hazards and facilitates efficient workflow during welding water pipe.
Implementing stringent safety measures not only safeguards the well-being of welding personnel but also contributes to the overall quality and durability of water pipe joints. By prioritizing safety, water pipe professionals can create a work environment that promotes efficiency, precision, and adherence to industry standards.
Required Equipment for Welding Water Pipe
Successful water pipe welding relies on the use of specialized equipment designed to facilitate precise and reliable joint formation. The essential equipment for water pipe welding includes welding machines, cutting tools, clamping devices, and testing instruments. For fusion welding of thermoplastic pipes, dedicated butt fusion and electrofusion machines are utilized to achieve seamless and leak-free joints.
In the case of MIG welding for metal pipes, welding machines equipped with appropriate power sources and shielding gases are essential for ensuring proper fusion and metallurgical bonding. Cutting tools, such as pipe cutters and beveling machines, are indispensable for preparing pipe ends with precise angles and smooth surfaces, enabling optimal welding conditions. Additionally, clamping devices and alignment tools aid in maintaining proper joint alignment and preventing misalignment during the welding process.
Testing instruments, including pressure testing equipment and non-destructive testing tools, play a crucial role in verifying the integrity and leak-tightness of water pipe welds. By utilizing the required equipment for water pipe welding, professionals can ensure the accuracy, efficiency, and reliability of the welding process, ultimately contributing to the long-term performance of water distribution systems.
Techniques for Achieving High Quality Welding
Achieving high-quality water pipe welds demands precision, expertise, and adherence to established welding techniques. The proper execution of welding techniques is essential for ensuring the structural integrity and leak-free performance of water pipe joints. For fusion welding of thermoplastic pipes, it is imperative to follow strict procedures for heating, joining, and cooling to achieve homogeneous and robust fusion zones.
MIG welding of metal pipes requires meticulous control of welding parameters, such as voltage, current, and travel speed, to create sound and uniform weld deposits. Employing proper welding techniques, including consistent bead placement and effective heat control, is crucial for minimizing defects and ensuring the mechanical strength of water pipe welds. Furthermore, maintaining cleanliness and preventing contamination of welding surfaces is essential for achieving durable and reliable joints.
By mastering the techniques for achieving high-quality water pipe welds, welding professionals can contribute to the overall performance and longevity of water distribution systems. Adhering to best practices and meticulous attention to detail during the welding process are fundamental for producing robust and leak-resistant joints that meet industry standards and regulatory requirements.
Common Challenges in Welding Water Pipe and How to Overcome Them
Welding water pipe presents various challenges that can impact the quality and integrity of weld joints. Common challenges include inadequate surface preparation, improper fusion zone formation, joint misalignment, and insufficient control of welding parameters. Addressing these challenges requires a proactive approach, comprehensive training, and the implementation of effective corrective measures.
Inadequate surface preparation, such as insufficient cleaning and beveling of pipe ends, can result in weak and defective welds. Implementing thorough surface preparation procedures, including cleaning, beveling, and inspection, is essential for creating optimal conditions for successful welding. Improper fusion zone formation, characterized by incomplete fusion or excessive bead width, can compromise the structural integrity and leak-tightness of water pipe welds.
Addressing this challenge involves meticulous control of welding parameters, proper heating and cooling cycles, and adherence to recommended fusion techniques. Joint misalignment during the welding process can lead to uneven weld deposits and compromised mechanical strength. Utilizing clamping devices, alignment tools, and precise joint fit-up techniques is crucial for overcoming misalignment challenges and achieving uniform and robust weld joints.
Insufficient control of welding parameters, such as voltage, current, and travel speed, can result in weld defects and inadequate fusion. Through comprehensive training, continuous monitoring, and adherence to established welding procedures, water pipe professionals can overcome these challenges and ensure the reliability and durability of water pipe welds.
Best Practices for Water Pipe Welding
Adhering to best practices is essential for achieving consistent and reliable water pipe welds that meet industry standards and regulatory requirements. Best practices encompass a wide range of aspects, including surface preparation, welding techniques, equipment maintenance, and quality control. Thorough surface preparation, including cleaning, beveling, and inspection, is fundamental for creating optimal conditions for successful welding of water pipes.
Employing proper welding techniques, such as controlled heating, joint alignment, and precise bead placement, is crucial for achieving robust and leak-resistant weld joints. Regular maintenance and calibration of welding equipment, including machines, cutting tools, and testing instruments, are essential for ensuring the accuracy and reliability of the welding process. Implementing comprehensive quality control measures, such as visual inspection, non-destructive testing, and pressure testing, is vital for verifying the integrity and leak-tightness of water pipe welds.
By embracing best practices for water pipe welding, professionals can uphold the highest standards of workmanship and contribute to the long-term performance and reliability of water distribution systems. Consistent adherence to best practices fosters a culture of excellence, precision, and quality assurance in water pipe welding operations.
Training and Certification for Welding Water Pipe
Proficiency in welding water pipe is cultivated through comprehensive training programs and certification processes that validate the skills and expertise of welding professionals. Training programs cover a wide range of topics, including welding techniques, equipment operation, safety protocols, and industry regulations. Hands-on training, coupled with theoretical knowledge, equips welding personnel with the necessary competencies to perform water pipe welding with precision and proficiency.
Certification processes provide formal recognition of an individual’s competence in water pipe welding, serving as a testament to their expertise and capability. Attaining relevant certifications, such as those offered by recognized welding organizations and regulatory bodies, demonstrates a commitment to professional development and adherence to industry standards. Employers and project stakeholders often prioritize certified welding professionals for water pipe welding projects, knowing that they possess the requisite skills and knowledge to deliver high-quality and compliant weld joints.
Investing in training and certification for welding water pipe not only enhances the individual’s professional credentials but also contributes to the overall quality and reliability of water distribution systems. By supporting continuous learning and skills validation, training and certification programs elevate the standards of water pipe welding and promote the delivery of exceptional workmanship.
Ensuring Quality and Durability in welding water pipe
Water pipe welding is a critical aspect of infrastructure development and maintenance, influencing the reliability and longevity of water distribution systems. The importance of proper welding techniques, encompassing fusion welding and MIG welding processes, cannot be overstated in ensuring leak-free joints and preventing contamination of the water supply. Prioritizing welding safety measures, utilizing the required equipment, and mastering high-quality welding techniques are essential for achieving durable and reliable water pipe welds.
Addressing common challenges, embracing best practices, and investing in comprehensive training and certification programs elevate the standards of water pipe welding and support the delivery of exceptional workmanship. By adhering to industry standards and regulatory requirements, water pipe professionals contribute to the overall performance and reliability of water distribution systems, safeguarding public health and safety while supporting industrial and residential activities.
Conclusion
In conclusion, a commitment to quality and durability in welding water pipe is fundamental for upholding the integrity of water infrastructure and ensuring the continuous and safe supply of this vital resource. Through comprehensive knowledge, rigorous training, and meticulous attention to detail, water pipe welding professionals play a pivotal role in shaping resilient and dependable water distribution networks that serve communities and industries with unwavering reliability.