Have you ever wondered how two pieces of metal are joined together? The answer lies in the fascinating world of fusion welding. But, what is fusion welding, and how does it work?
Fusion welding is a process that joins two metals by applying heat until they melt and fuse together. In simple terms, it’s like using a glue gun, but with metal. The process allows for a strong and seamless joint that can withstand high stress and wear. But, how does fusion welding work?
The process typically involves heating the metals to their melting point, applying sufficient pressure to join them together, and allowing them to cool and solidify. The heat is generated using a variety of sources, including electric arcs, gas flames, or lasers. Different types of fusion welding techniques exist, each with their unique advantages and applications. Fusion welding is widely used across many industries, from construction and automotive to aerospace and manufacturing.
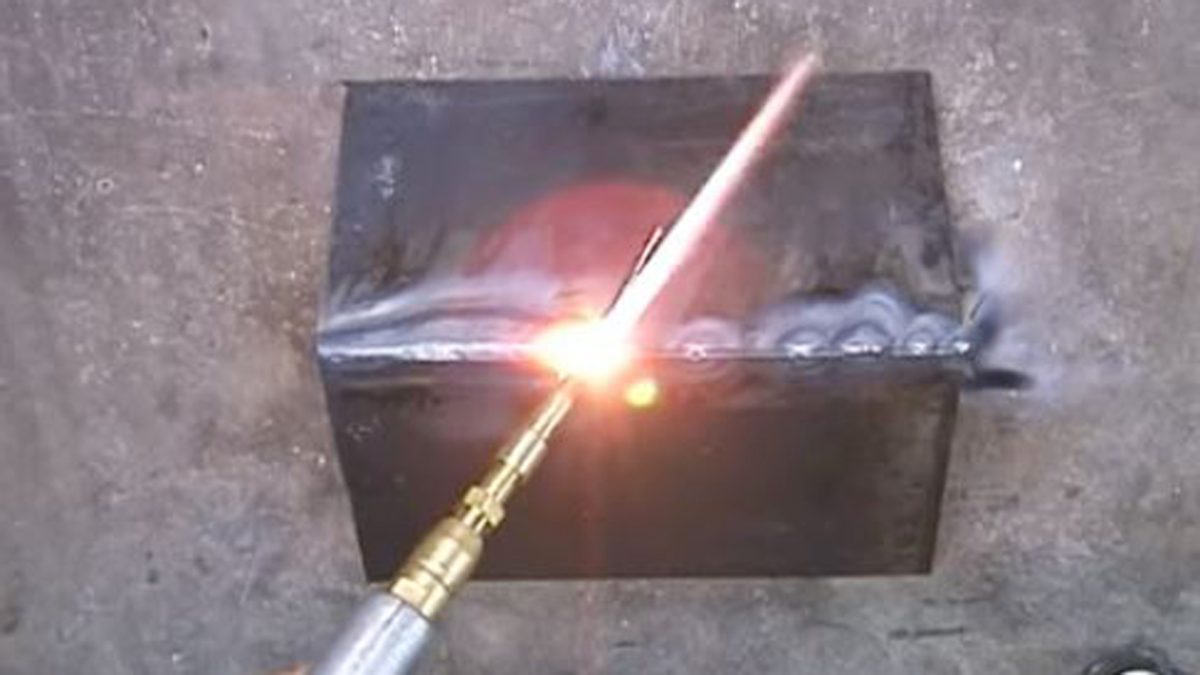
Image by 897473 on YT
Understanding Fusion Welding – A Brief Overview
When it comes to welding, fusion welding is one of the most widely used techniques. It involves melting the edges of two pieces of metal until they fuse together to form a strong bond.
Types of Fusion Welding
There are several different types of fusion welding techniques, including:
- Gas Tungsten Arc Welding (GTAW): Also known as Tungsten Inert Gas (TIG) welding, this technique uses a non-consumable tungsten electrode to produce the weld.
- Gas Metal Arc Welding (GMAW): This is also known as Metal Inert Gas (MIG) welding. It uses a consumable wire electrode to create the weld.
- Flux-cored Arc Welding (FCAW): This Flux-cored Arc Welding technique uses a wire that is filled with flux to produce the weld.
- Submerged Arc Welding (SAW): This technique involves feeding a consumable wire electrode into a pool of molten flux to create the weld.
Each of these techniques has its own advantages and disadvantages, and the choice of technique will depend on the specific application.
Fusion Welding Techniques
There are several techniques that are used in fusion welding, including:
- Butt welding: Butt welding involves two plates together along their edges. It is commonly used in the construction of ships and bridges.
- Lap welding: This involves welding two plates together where they overlap. It is commonly used in the construction of automobiles and aircraft.
- Fillet welding: This involves welding two plates together where they meet at a right angle. It is commonly used in the construction of buildings and other structures.
Fusion Welding Importance
Fusion welding is an incredibly important process that is used across a wide range of industries. It is used to manufacture everything from cars and airplanes to bridges and buildings. Without fusion welding, many of the products and structures that we rely on every day would not exist.
The Science Behind Fusion Welding
Fusion welding involves melting the edges of two materials and fusing them together to create a single, solid piece. The process requires a heat source to raise the temperature of the materials to the point where they become molten. Once the materials are in a liquid state, they’re joined together in a process called coalescence.
There are several types of fusion welding techniques, including:
- Gas Tungsten Arc Welding (GTAW) – uses a non-consumable tungsten electrode and an inert gas to create the weld.
- Gas Metal Arc Welding (GMAW) – uses a consumable wire electrode and an inert gas to create the weld.
- Plasma Arc Welding (PAW) – Plasma Arc are uses a constricted arc between a non-consumable tungsten electrode and the workpiece.
- Submerged Arc Welding (SAW) – uses a granular flux to shield the weld and create a deep penetration weld.
The choice of fusion welding technique depends on the specific application and the materials being joined. Each technique has its advantages and disadvantages, and selecting the appropriate one requires careful consideration.
Types of Fusion Welding | Advantages | Disadvantages |
---|---|---|
Gas Tungsten Arc Welding (GTAW) | Produces high-quality welds, is easy to control, and results in minimal distortion. | Slow process, requires a high level of skill, and is not suitable for all materials. |
Gas Metal Arc Welding (GMAW) | Produces high-quality welds quickly and is suitable for a wide range of materials. | Not suitable for outdoor use, requires a shielding gas, and produces more fumes than other techniques. |
Plasma Arc Welding (PAW) | Produces a highly concentrated and stable arc, resulting in a precise and clean weld. | Requires extensive knowledge and skill, expensive equipment, and is not suitable for all materials. |
Submerged Arc Welding (SAW) | Produces high-quality welds quickly, and is suitable for thick materials and long welds. | Requires a lot of equipment and is not suitable for small or intricate welds. |
Overall, the fusion welding process requires a high level of skill and precision. The equipment used must be properly maintained and calibrated to ensure the best results. By selecting the appropriate technique and understanding the science behind it, fusion welding can produce strong and reliable welds for a wide range of applications.
Advantages of Fusion Welding
Fusion welding offers many advantages over other welding techniques. Here are some of the most significant benefits:
Advantages | Description |
---|---|
Strength | Fusion welding creates a high-strength bond between materials. This bond is often stronger than the materials themselves, providing added durability and resilience. |
Precision | Fusion welding allows for highly precise and controlled welds, ensuring accuracy and consistency throughout the process. |
Joining Different Materials | Fusion welding can join different types of materials, such as plastics and metals, with relative ease. This versatility makes it a valuable option in many industries. |
Reduced Distortion | Fusion welding creates a narrow heat-affected zone, which reduces the risk of distortion or warping when welding thin or delicate materials. |
Efficiency | Fusion welding is an efficient process that requires less prep time and material than other welding methods. This can result in significant cost savings over time. |
Why is Fusion Welding Important?
Fusion welding plays a crucial role in many industries, including construction, automotive, aerospace, and manufacturing. Its ability to join different types of materials and create strong, precise bonds makes it a valuable option for creating everything from buildings to machinery.
Additionally, the efficiency and cost-effectiveness of fusion welding make it an attractive option for businesses looking to streamline their production processes and save money. By using fusion welding techniques, companies can increase their output while reducing waste and rework.
Overall, fusion welding is an essential process that helps create the products and structures we rely on every day. Its importance cannot be overstated, and its benefits will continue to be felt in industries around the world for years to come.
Step-by-Step Guide to Fusion Welding
Fusion welding is a complex process that involves the fusion of two materials through the application of heat. To help you understand how fusion welding works, we’ve created a step-by-step guide below.
Step 1: Prepping the Materials
The first step in fusion welding is to properly prepare the materials that need to be welded. This involves cleaning and beveling the edges to ensure they are free from any debris or contaminants that could affect the strength of the weld.
Step 2: Positioning the Materials
Once the materials have been prepped, the next step is to position them in the correct orientation for welding. This involves aligning the materials and holding them in place to prevent any movement during the welding process.
Step 3: Applying Heat
With the materials in position, the next step is to apply heat. This is typically done using a torch or other heat source, which is brought close to the materials to melt them and create a molten pool.
Step 4: Adding Filler Material
Once the materials have been melted, the next step is to add filler material. This is typically a metal that is compatible with the materials being welded and is added to the molten pool to help strengthen the weld.
Step 5: Cooling and Solidifying
After the filler material has been added, the weld is allowed to cool and solidify. During this process, the materials are fused together to create a strong bond that can withstand a significant amount of stress and pressure.
And there you have it – a quick overview of the steps involved in the fusion welding process. Whether you are a professional welder or just getting started, understanding the science and techniques behind fusion welding is essential. By following the step-by-step guide above, you can begin to master the art of fusion welding and create strong, reliable connections between materials.
Applications and Industries that Utilize Fusion Welding
Fusion welding plays an essential role in various sectors, making it an indispensable process in many industries. Here are some examples of applications that rely on fusion welding:
Industry | Application |
---|---|
Construction | Welding steel beams to create structural support for buildings, bridges, and roads |
Aerospace | Welding sections of an airplane fuselage or spacecraft frame |
Automotive | Welding components to form the car’s body, frame, and exhaust system |
Manufacturing | Welding parts to create machinery, equipment, and tools |
These are just a few examples of how fusion welding is utilized in various applications. Its importance cannot be overstated, as it allows for the creation of strong and durable connections between materials.
Moreover, with advancements in fusion welding technology, new applications are emerging all the time. For example, in the medical industry, fusion welding is used to create medical devices, implants, and prosthetics. In the energy sector, fusion welding is utilized in the construction and maintenance of oil rigs, pipelines, and refineries.
It is clear that fusion welding plays a crucial role in many industries, enabling them to achieve greater efficiency, reliability, and safety in their operations. As such, it will continue to be an essential process for years to come.
Appreciating the Importance of Fusion Welding
Understanding the basics of fusion welding and its applications can leave us amazed by the intricacies of this technique that involves the joining of materials at a molecular level. The advantages of fusion welding over other welding methods are clear, making it a preferred choice for many industries.
The Science Behind Fusion Welding Simplified
The science behind fusion welding can appear complex at first glance. However, by breaking down the process and techniques involved, we can gain a basic understanding of the science behind fusion welding. This practical approach is useful for appreciating the importance of fusion welding and why it holds such a significant place across various industries.
By following a step-by-step guide, we can achieve successful fusion welding results that provide strong and reliable connections. When applied correctly, fusion welding can deliver outstanding and long-lasting results for many applications.
Overall, the significance of fusion welding in contemporary technology and infrastructure is underlined by its advantages, ranging from accuracy and strength to durability and flexibility. We hope this article has helped you gain a better understanding of fusion welding and its importance in diverse fields.
Final Thoughts
Fusion welding is a critical process used to join materials together through the application of heat. We hope that this article has provided you with a comprehensive understanding of fusion welding, from its explanation to the science behind the process and the advantages it offers. Through studying the step-by-step guide and highlighting the different applications and industries that utilize fusion welding, we can appreciate its significance. Fusion welding is an innovative and effective technique that plays a crucial role in various sectors.
FAQ
What is fusion welding?
Fusion welding is a process that joins materials together by melting and fusing them. It involves the application of heat to create a molten pool, which cools and solidifies to form a strong bond between the materials.
How does fusion welding work?
Fusion welding works by heating the materials to their melting point, allowing them to become molten. The molten pool is then manipulated to join the materials together, and as it cools and solidifies, a strong bond is formed.
What are the types of fusion welding techniques?
There are several types of fusion welding techniques, including arc welding, laser welding, electron beam welding, and gas welding. Each technique utilizes different heat sources and methods, but the underlying principle of melting and fusing materials remains the same.
Why is fusion welding important?
Fusion welding is important because it allows for the creation of strong and durable connections between materials. It is widely used in various industries, including construction, automotive, aerospace, and manufacturing, to join different components and structures together.
What is the process of fusion welding?
The process of fusion welding involves several steps. First, the materials to be joined are prepared by cleaning and aligning them. Then, heat is applied to melt the materials, creating a molten pool. The molten pool is manipulated to join the materials together, and as it cools and solidifies, a strong bond is formed.
What are the advantages of fusion welding?
Fusion welding offers several advantages over other welding methods. It provides high strength and integrity to the welded joints, ensuring durability. It also allows for precise control over the welding process, resulting in accurate and reliable connections. Additionally, fusion welding can join different materials, making it versatile in various applications.
Which industries utilize fusion welding?
Fusion welding is widely used in various industries, including construction, automotive, aerospace, manufacturing, and many more. It is essential in creating strong and reliable connections for structures, components, and products in these sectors.