When it comes to the field of welding, safety should always be the top priority. Welding involves working with high temperatures, sparks, and hazardous materials, making it crucial for welders to take the necessary precautions to protect themselves and others around them. In this blog post, we will discuss 10 welding safety rules that every welder must absolutely follow to ensure a safe and secure work environment. By adhering to these rules, welders can minimize the risk of accidents, injuries, and property damage, ultimately promoting a culture of safety first in the welding industry.
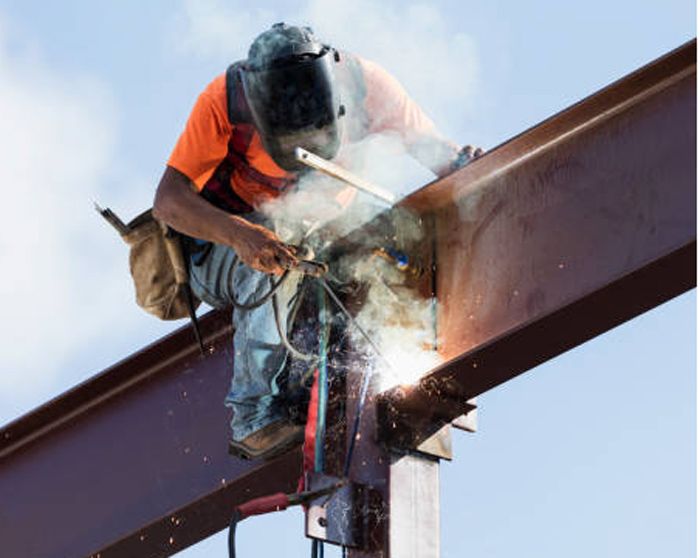
Photos by eticampus.edu
Importance of welding safety
Ensuring safety in the welding industry is of utmost importance. Welding poses numerous hazards that can lead to accidents, injuries, and even fatalities if proper safety precautions are not followed. By understanding and implementing the essential 10 welding safety rules, welders can significantly reduce the risk of accidents and protect themselves and others around them.
Firstly, welding involves working with high temperatures, which can produce intense heat and sparks that can easily cause fires or burn injuries. By following safety rules such as wearing appropriate protective clothing, using fire-resistant barriers, and keeping a fire extinguisher nearby, welders can prevent and quickly respond to fire-related incidents.
Secondly, welding requires the use of hazardous materials such as gases, fumes, and chemicals. Inhaling these substances can lead to serious respiratory issues and other health problems. It is vital for welders to ensure proper ventilation, wear respiratory protection, and use effective fume extraction systems to minimize the exposure to these harmful substances.
Proper training and education are crucial for welders to understand the potential dangers and learn safe welding practices. Regular maintenance and inspection of welding equipment, as well as the proper storage and handling of welding materials, are also essential to prevent equipment failures and accidents.
The importance of welding safety cannot be overstated. Following the 10 welding safety rules not only protects the welder from harm but also contributes to a culture of safety and promotes a secure work environment in the welding industry. So, let us prioritize safety first and ensure that every welder is equipped with the knowledge and tools to weld safely.
Rule #1: Know and understand the potential hazards
To ensure welding safety, it is imperative for welders to have a thorough understanding of the potential hazards associated with the work. This knowledge enables them to identify and mitigate risks effectively. One of the primary hazards in welding is the exposure to intense heat and sparks, which can lead to fires and burn injuries. Welders need to be aware of the proper use of fire-resistant barriers, protective clothing, and the availability and operation of fire extinguishers.
Another crucial hazard is the inhalation of hazardous substances such as gases, fumes, and chemicals. Welders must be well-educated on the proper ventilation techniques and the use of respiratory protection to minimize the risk of respiratory issues and other health problems.
Additionally, welders need to be acquainted with equipment-related hazards. Regular equipment maintenance and inspection, proper storage and handling of welding materials, and adherence to safe working practices are necessary to prevent accidents caused by equipment failures.
By knowing and understanding the potential hazards, welders can take proactive measures to protect themselves and others. This knowledge empowers them to create a safe and secure work environment, aligning with the overarching aim of prioritizing safety in the welding industry.
Rule #2: Wear appropriate personal protective equipment (PPE)
Wearing the appropriate personal protective equipment (PPE) is crucial for welders to ensure their safety while on the job. PPE includes items such as safety glasses, welding helmets, gloves, and protective clothing, all of which are designed to shield the welder from potential hazards.
Safety glasses or goggles with side shields should always be worn to protect the eyes from flying sparks, debris, and harmful radiation. Welding helmets with the appropriate shade level should be used to shield the face and eyes from the intense light, heat, and sparks produced during welding.
Gloves made of flame-resistant materials provide protection against burns, cuts, and abrasions. It is important to choose gloves that are appropriate for the type of welding being performed. Welders should also wear durable clothing made of non-flammable materials to protect their skin from sparks and heat.
In addition to wearing the correct PPE, it is crucial to regularly inspect and maintain the equipment. Any damaged or worn-out PPE should be replaced immediately to ensure its effectiveness.
By following Rule no. 2 and wearing the appropriate PPE, welders can greatly reduce the risk of injury and create a safe working environment.
Rule #3: Ensure proper ventilation in the workspace
Proper handling and storage of welding materials is imperative for maintaining a safe working environment. By following Rule no. 3, welders can prevent accidents and reduce the risk of injuries. One crucial aspect of Rule no. 3 is ensuring proper ventilation in the workspace. Welding produces hazardous fumes and gases that can be harmful if inhaled. These fumes contain toxic substances such as lead, zinc, and cadmium, which can lead to respiratory issues or long-term health problems.
To maintain adequate ventilation, it is recommended to work in an open and well-ventilated area. If working indoors, make sure to install exhaust systems or use local exhaust ventilation to capture and remove fumes and gases from the welding area. It is also important to regularly clean and check the ventilation systems to ensure their efficiency.
Rule #4: Maintain a clean and organized work area
Maintaining a clean and organized work area is essential for ensuring safety during welding operations. Rule no. 4 focuses on fire prevention measures, and a clutter-free workspace plays a crucial role in preventing accidents and minimizing the risk of fires.
By keeping the work area clean, welders can reduce the chances of flammable materials coming into contact with sparks or hot metal. It is important to remove any combustible materials, such as wood, plastic, or paper, from the vicinity of the welding area. Additionally, all flammable liquids should be stored in designated containers away from the welding zone.
Regularly inspecting the work area for any potential fire hazards, such as oil spills or loose wires, is also vital. Implementing proper housekeeping practices, such as sweeping up metal shavings or debris, can significantly contribute to fire prevention.
By following this rule and maintaining a clean and organized work area, welders can create a safer environment that minimizes the risk of fires and ensures their own well-being.
Rule #5: Use the right tools and equipment for the job
Rule no. 5 emphasizes the importance of using the right tools and equipment for welding tasks. Welders must ensure that they have the appropriate tools and protective equipment to carry out their work safely and effectively. Using the wrong tools or equipment can not only lead to subpar results but also pose significant safety risks. It is crucial to familiarize oneself with the specific tools and equipment required for each welding project. This includes wearing the correct gloves, goggles, helmets, and clothing that provide adequate protection against sparks, intense heat, and harmful fumes.
Investing in high-quality tools and regularly maintaining them is essential to ensure their proper functioning and longevity. Neglecting to do so can result in equipment malfunctions, which can be dangerous for both the welder and those nearby. Remember, using the right tools and equipment is not just about achieving quality welds; it’s about prioritizing safety and reducing the risk of accidents. Stay tuned for the next section, where we will discuss Proper ventilation and respiratory protection.
Rule #6: Follow proper welding techniques and procedures
Following proper welding techniques and procedures is crucial for ensuring safety in the welding process. Rule no. 6 emphasizes the importance of using the correct welding techniques and procedures to minimize the risk of accidents and produce high-quality welds.
Welders must be trained and experienced in the specific techniques of welding, such as arc welding, MIG welding, or TIG welding. They should understand how to properly set up the welding equipment, prepare the workspace, and handle the materials being welded.
Adhering to proper welding procedures, such as maintaining the correct voltage and current settings, using the appropriate welding technique for the material being welded, and ensuring proper joint preparation, can significantly reduce the chances of equipment failure, weld defects, and workplace injuries.
By following rule no. 6 and using the right welding techniques and procedures, welders can create strong, durable, and safe welds while minimizing the risks associated with the welding process.
Rule #7: Never operate welding equipment without proper training and certification
When it comes to welding safety, proper training and certification are non-negotiable. Rule no. 7 emphasizes the importance of never operating welding equipment without the necessary knowledge and credentials. Welding is a skilled trade that requires expertise and proficiency. Without the proper training, welders can put themselves and others at risk of serious accidents and injuries. It is essential to receive formal training from a reputable institution or under the guidance of an experienced welder.
Certification is equally vital in the welding industry. Acquiring certification demonstrates that you have met the standards and possess the necessary skills to perform welding tasks safely and efficiently. Employers often require certified welders to ensure the highest level of quality and safety in their operations. By adhering to this rule and only operating welding equipment with proper training and certification, you can contribute to a safer work environment and achieve better welding outcomes.
Rule #8: Keep flammable materials away from the welding area
In continuation of our discussion on welding safety rules, we come to Rule no. 8, which emphasizes the importance of keeping flammable materials away from the welding area.
Welding involves the use of heat and sparks, which can easily ignite flammable substances such as oils, solvents, and gases. Having these materials in close proximity to the welding operation can lead to fires, explosions, and severe injuries.
To ensure a safe working environment, it is crucial to maintain a clear and designated welding area free from flammable materials. Store all flammable substances in appropriate containers and a safe distance away from the welding zone. Make sure that the surrounding area is free from any clutter or debris that could potentially catch fire.
Rule #9: Inspect and maintain welding equipment regularly
In continuation of our discussion on welding safety rules, we move on to Rule no. 9, a crucial guideline that focuses on inspecting and maintaining welding equipment regularly.
It is essential to regularly inspect and maintain your welding equipment to ensure its proper functioning and minimize the risk of accidents. Over time, wear and tear can occur, leading to faulty equipment that can compromise safety. By conducting regular inspections, you can identify any potential issues such as leaks, damaged cables, or faulty connections.
Regular maintenance of your welding equipment includes cleaning, lubricating, and replacing worn-out parts as necessary. It is also important to follow the manufacturer’s instructions for maintenance and calibration.
By following this rule and inspecting and maintaining your welding equipment regularly, you can ensure that it is in optimal condition, reducing the risk of equipment failure and enhancing safety in the workplace.
Rule #10: Always have a fire extinguisher nearby
In our final rule, we highlight the importance of keeping a fire extinguisher in close proximity at all times during welding operations. While proper equipment maintenance and adherence to safety protocols significantly reduce the risk of fires, accidents can still happen.
Welding involves intense heat and sparks, which can easily ignite flammable materials in the vicinity. Having a fire extinguisher readily available can help you swiftly and effectively respond to any potential fires, preventing them from spreading and causing further damage. When selecting a fire extinguisher for your welding area, opt for one specifically designed for Class D fires, which involve combustible metals commonly used in welding processes. Ensure that the extinguisher is easily accessible, regularly inspected, and properly maintained.
By following rule no. 10 and having a fire extinguisher nearby, you are prepared to handle any fire emergencies swiftly, protecting yourself, your colleagues, and your workspace.
Conclusion and Putting safety first in welding operations
Adhering to the ten welding safety rules discussed throughout this blog series is crucial for maintaining a safe work environment. Each of these rules focuses on specific aspects of welding safety, ranging from personal protective equipment to equipment maintenance and fire safety.
By following these rules diligently, welders can greatly reduce the risk of accidents, injuries, and property damage. Taking the time to evaluate and address potential hazards before starting any welding task is essential. Remember, shortcuts in safety procedures can have severe consequences.
Incorporating these safety rules into your daily welding practices is not only about compliance but also about prioritizing your well-being and the well-being of those around you. Welding can be a rewarding and fulfilling profession, but it is essential to prioritize safety to ensure a long and successful career.