Stepping into the world of welding galvanized steel? Understanding the correct procedure is the key to a strong and durable outcome. From the protective coating to the heat-affected zone, each step demands precision. Join us as we delve into the nuances of welding galvanized steel, uncovering the dos and don’ts to achieve impeccable results.
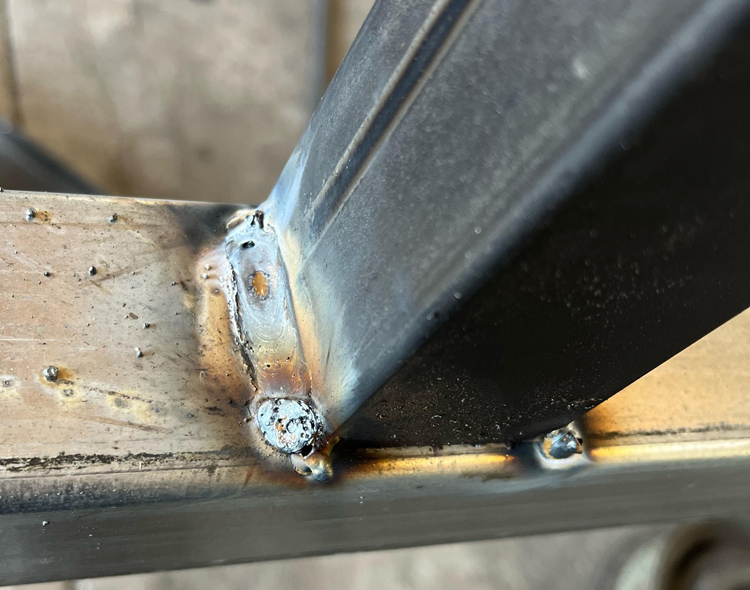
Galvanized Steel and Its Properties
Galvanized steel is steel that has been coated with a layer of zinc to protect it from corrosion. This protective coating significantly extends the lifespan of the steel, making it a popular choice for various applications. The galvanization process involves immersing the steel in a bath of molten zinc, which forms a metallurgical bond with the steel. This results in a durable, rust-resistant finish that is ideal for outdoor and industrial environments. When it comes to welding, the presence of zinc introduces complexities that require careful consideration.
The zinc coating on galvanized steel serves as a sacrificial anode, meaning it corrodes before the underlying steel does. This is an essential feature for protecting the steel, but it also presents challenges when welding. The heat generated during the welding process vaporizes the zinc coating, releasing fumes that can be hazardous to the welder and compromise the integrity of the weld. Additionally, the presence of zinc in the weld zone can affect the mechanical properties of the joint, making it crucial to follow specific procedures to ensure a successful outcome.
Understanding the properties of galvanized steel is essential for executing a successful welding procedure. The unique characteristics of this material require specialized techniques and precautions to achieve strong, durable welds without compromising the integrity of the zinc coating.
Hazards Associated and Risks of Welding Galvanized Steel
Welding galvanized steel poses significant risks and hazards that must be carefully managed to ensure the safety of the welder and the quality of the weld. One of the primary risks associated with welding galvanized steel is the release of zinc fumes during the welding process. When the zinc coating is heated to the point of vaporization, it releases zinc oxide fumes, which can cause symptoms known as metal fume fever or “zinc shakes” when inhaled. These symptoms include fever, chills, muscle aches, nausea, and fatigue, and can be particularly severe in some cases.
In addition to the health risks posed by zinc fumes, welding galvanized steel also presents challenges in terms of weld quality and integrity. The presence of zinc in the weld zone can lead to issues such as weld spattering, porosity, and reduced mechanical properties. These issues can compromise the strength and durability of the weld, making it essential to implement specific techniques and precautions to mitigate these risks.
The heat-affected zone (HAZ) in galvanized steel differs from that of uncoated steel, requiring careful attention to welding parameters and post-weld treatments to ensure the integrity of the protective coating. By understanding and addressing these risks and hazards, welders can execute a safe and effective procedure for welding galvanized steel.
Welding Preparations for Galvanized Steel
Before initiating the welding process for galvanized steel, several essential preparations must be made to ensure a successful outcome. The first step is to assess the condition of the galvanized steel, including the thickness and condition of the zinc coating. Any areas of damage or excessive corrosion on the zinc coating should be addressed before welding to prevent the introduction of contaminants into the weld zone.
Next, thorough cleaning of the galvanized surface is crucial to remove any dirt, grease, or other contaminants that could compromise the quality of the weld. This can be achieved through mechanical methods such as wire brushing or grinding, followed by solvent cleaning or alkaline degreasing to ensure a clean, oxide-free surface for welding.
After cleaning, it is essential to assess the welding environment and ensure adequate ventilation to prevent the accumulation of zinc fumes. Proper personal protective equipment (PPE), including a respirator with appropriate filters, gloves, and eye protection, should be worn to protect against inhalation of zinc fumes and contact with molten zinc during welding.
By meticulously preparing the galvanized steel and the welding environment, welders can lay the foundation for a successful welding procedure that prioritizes safety and quality.
Welding Methods and Techniques for Galvanized Steel
When it comes to welding galvanized steel, selecting the appropriate welding method and technique is crucial for achieving strong, durable welds while minimizing the risk of zinc-related issues. The most common welding methods used for galvanized steel include shielded metal arc welding (SMAW), gas metal arc welding (GMAW), and flux-cored arc welding (FCAW). Each method has its advantages and considerations when used with galvanized steel, and selecting the most suitable method depends on factors such as material thickness, joint configuration, and welding position.
In addition to choosing the right welding method, specific techniques can be employed to minimize the impact of the zinc coating on the weld. For instance, welding parameters such as voltage, amperage, and travel speed should be carefully adjusted to prevent excessive heat input, which can lead to increased vaporization of the zinc coating. Techniques such as backstepping, intermittent welding, and proper electrode manipulation can help control heat input and reduce the risk of zinc-related issues such as spattering and porosity.
The use of welding consumables specifically designed for galvanized steel, such as specialized flux-cored wires or solid wires with appropriate shielding gas, can contribute to improved weld quality and reduced zinc-related concerns. By combining the right welding method with tailored techniques and consumables, welders can achieve high-quality welds on galvanized steel while managing the challenges associated with the zinc coating.
Safety Precautions During Welding Galvanized Steel
Executing a welding procedure for galvanized steel requires strict adherence to safety precautions to protect the welder from the hazards associated with zinc fumes and molten zinc. Ventilation is critical to minimize the concentration of zinc fumes in the welding environment. Whenever possible, welding should be conducted in well-ventilated areas with the assistance of local exhaust ventilation systems to capture and remove fumes at the source.
In instances where adequate ventilation cannot be achieved, the use of respiratory protection becomes essential. Welders should wear a respirator with filters specifically designed to capture metal fumes, such as a high-efficiency particulate air (HEPA) filter or a powered air-purifying respirator (PAPR). This protective equipment helps prevent inhalation of zinc fumes, safeguarding the welder’s respiratory health during the welding process.
Proper personal protective equipment (PPE) should be worn to minimize exposure to molten zinc and other hazards. This includes flame-resistant clothing, gloves, and eye protection to shield against sparks and radiant energy. By prioritizing safety precautions and PPE, welders can mitigate the risks associated with welding galvanized steel and ensure a safe working environment.
Welding Care and Treatment for Galvanized Steel
After completing the welding procedure for galvanized steel, it is crucial to implement post-welding care and treatment to preserve the integrity of the zinc coating and the quality of the weld. One of the most critical steps is to remove any spatter or weld defects that may have occurred during the welding process. This can be achieved through mechanical methods such as chipping or grinding, taking care to avoid damage to the surrounding zinc coating.
Following the removal of spatter and defects, the welded area should be cleaned to eliminate any residual contaminants that could compromise the protective properties of the zinc coating. Solvent cleaning or alkaline degreasing can be used to ensure a clean surface free of oxides, oils, or other residues that could hinder the performance of the coating.
Once the welded area is clean, it is essential to apply a zinc-rich paint or coating to the weld and the surrounding heat-affected zone (HAZ). This helps restore the protective properties of the zinc coating in the vicinity of the weld, mitigating the risk of accelerated corrosion at the weld joint. By diligently performing post-welding care and treatment, welders can ensure the long-term durability and corrosion resistance of the galvanized steel.
Common Mistakes to Avoid When Welding Galvanized Steel
Welding galvanized steel requires precision and attention to detail to avoid common mistakes that can compromise the quality of the weld and the integrity of the zinc coating. One of the most critical mistakes to avoid is welding directly on the galvanized surface without proper cleaning and preparation. This can lead to the entrapment of contaminants in the weld, resulting in poor fusion, porosity, or other defects.
Another common mistake is using excessive heat input during welding, which can accelerate the vaporization of the zinc coating and lead to issues such as spattering and weld porosity. Proper adjustment of welding parameters and techniques is essential to control heat input and minimize the impact on the zinc coating.
Neglecting post-welding care and treatment can result in accelerated corrosion at the weld joint, compromising the long-term performance of the galvanized steel. By avoiding these common mistakes and following best practices for welding galvanized steel, welders can achieve high-quality welds that maintain the protective properties of the zinc coating.
Best Practices for Welding Galvanized Steel
Achieving exceptional results when welding galvanized steel requires adherence to best practices that prioritize safety, quality, and long-term performance. One of the fundamental best practices is to conduct a thorough assessment of the galvanized steel before welding, addressing any areas of damage or excessive corrosion to ensure a clean, sound surface for welding.
Selecting the appropriate welding method and technique based on the specific requirements of the application is another key best practice. By tailoring the welding approach to the material thickness, joint configuration, and environmental conditions, welders can optimize the quality and integrity of the weld while managing the challenges associated with the zinc coating.
Implementing robust safety precautions, including ventilation, respiratory protection, and personal protective equipment, is essential to safeguard the welder’s health and well-being during the welding process. By prioritizing safety, welders can create a secure working environment that minimizes the risks associated with welding galvanized steel.
Diligent post-welding care and treatment, including the removal of spatter, thorough cleaning, and application of a zinc-rich coating, is crucial to preserving the protective properties of the zinc coating and ensuring the long-term corrosion resistance of the weld.
Welding Equipment and Materials for Galvanized Steel
Executing a successful welding procedure for galvanized steel requires the use of specialized equipment and materials tailored to the unique characteristics of this material. When selecting welding equipment, it is essential to choose tools and accessories that are compatible with the welding method and technique being employed. This includes welding machines, electrodes, shielding gas, and other consumables that are specifically designed for use with galvanized steel.
In addition to welding equipment, the selection of materials such as flux-cored wires or solid wires with appropriate shielding gas can significantly influence the quality and performance of the weld on galvanized steel. These consumables are formulated to mitigate the challenges associated with the zinc coating, providing improved weldability and reduced risk of zinc-related issues such as spattering and porosity.
The use of personal protective equipment (PPE) such as respirators, gloves, and eye protection is essential to safeguard the welder from the hazards associated with welding galvanized steel. By equipping welders with the appropriate tools, consumables, and PPE, organizations can ensure the safety and success of welding procedures for galvanized steel.
Conclusion
Welding galvanized steel demands meticulous attention to detail, specialized techniques, and robust safety precautions to achieve exceptional results. By understanding the properties of galvanized steel, managing risks and hazards, conducting thorough pre-welding preparations, selecting appropriate welding methods and techniques, prioritizing safety, implementing post-welding care and treatment, and adhering to best practices, welders can navigate the complexities of welding galvanized steel with confidence and expertise. With the right equipment, materials, and knowledge, welders can produce strong, durable welds on galvanized steel that uphold the protective properties of the zinc coating and deliver long-term performance in a variety of applications.
I hope this article meets your expectations and provides valuable insights into the welding procedure for galvanized steel. If there are any additional details or specific areas you would like to be included, please feel free to let me know.