Welding aluminum boats can be a challenge because the material is so soft. But you don’t need to be intimidated by the challenge, with the right information and techniques, it can be quite simple. In this article, we will discuss why you should consider welding your boats, as well as some of the challenges that are likely to come up. Keep reading for everything you need to know about welding aluminum boats.
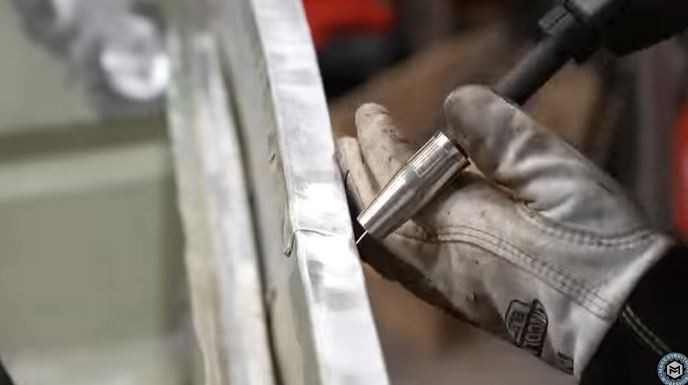
Photo by MakeEverything on YT
What is Welding Aluminum?
Aluminum is not a metal that naturally occurs in the earth’s crust. Instead, it is a very silvery white metal that has a very low melting point of 660°C. Aluminum can be formed into various alloys, which are combinations of a metal with another material to alter its properties. Welding aluminum is a process that involves melting the aluminum, pouring the metal into a pipe, then causing it to fuse by applying an electrical current. Once the metal has fused, it is cut out. Aluminum welding is not done with oxyacetylene or MIG welding torches. Welding aluminum uses an arc welding machine that creates a very short arc between two electrodes. This process is what makes aluminum welding possible.
Things to Consider Before Welding Aluminum Boats
Why would you want to weld an aluminum boat? There are a few good reasons. First of All, welding aluminum Is not risky welding aluminum is not a dangerous process. A lot of people are afraid to weld aluminum boats because they assume that it will be very dangerous. But this is not necessarily the case. Welding aluminum is not any more dangerous than welding steel, copper, or aluminum. If you are not familiar with the process, it may be more dangerous, but once you learn the right welding techniques, it is not. But you must also have the right welding equipment.
Welding aluminum requires a specific aluminum welder and an electrode that can work with the aluminum. You also need to know the right shielding and grounding techniques so you don’t cause a dangerous buildup of static electricity. Welding aluminum is a great option if your boat is made of aluminum, but not steel or copper.
Check for Durability Before You Begin
You will want to make sure your aluminum boat is up for the welding work. You will need to check the thickness of the aluminum and look for any major dents or other damage. You will also want to check that the areas of the boat that might get welded, like the ribs and seams, are in good condition. Are the seams in good condition? Are the ribs strong and not cracked or otherwise damaged?
If there are any problems with the boat or areas where welding might affect the integrity of the boat, you will want to fix them before welding so as to minimize the risk of damage. Once you have made sure your boat is in good shape, you hall want to make sure it’s not on a seismic zone.
Which Welder Should You Use for Welding Aluminum Boats
This is a question that you should consider before you begin welding aluminum boats. Welding aluminum requires a special aluminum welder. You can use a standard gas or acetylene welder for steel, copper, and non-aluminum materials, but it will damage the aluminum and cannot be used on aluminum. To weld aluminum, you will need a Millermatic or a Millermatic Plus aluminum welder.
The Millermatic Plus is a dual voltage welder that can weld either a 220V or 110V circuit. It is specifically designed to work with aluminum, offering a more precise weld with less heat than a standard welder.
It also has a built-in ground-fault circuit interrupter (GFCI) that protects you from dangerous electric shock that can be caused by welding on 110V circuits.
How to Weld Aluminum Boats?
Aluminum welding is a specialized process, and it is not for everybody. Welding aluminum boats requires a lot of practice and knowledge about the process. If you are interested in welding aluminum boats, you will have to practice welding on aluminum scraps until you get the technique down. There are a few things you will want to keep in mind when welding aluminum boats. These include ramping the voltage, keeping the aluminum cool, and shielding the aluminum from the weld spot to prevent damage.
First of all, you will want to make sure that you do not weld on an aluminum boat that has been submerged in water. The aluminum will be extremely fatigued and damaged by the welding process. When welding aluminum, you will want to ramp up the voltage slowly. A lower voltage will result in a weaker weld and is not recommended.
So, you will want to start off with a higher voltage, and then as you weld, you will want to gradually lower the voltage to minimize the amount of damage to the aluminum.
Comparison of Welding Methods
Here are some of the characteristics of each welding method:-
Welding Aluminum – This is a process that uses an arc welding machine to create a very short arc between two electrodes. The aluminum is then melted and pushed through the machine to form a welded joint. Aluminum welding is not done with oxyacetylene or MIG welding torches. It is only done with an arc welding machine.
Oxyacetylene Welding – This welding method used a torch with an oxygen cylinder to melt the metal. The oxygen in the torch increased the heat of the welding, producing a strong weld that was also highly corrosive. Oxyacetylene welding is not used for aluminum welding.
MIG Welding – This is a process similar to oxyacetylene welding. A MIG welding torch has a sparkles arc, which produces a weld that is not highly corrosive. MIG welding is not used for aluminum welding.
Tips for Successful Welding
Here are some tips for successful welding: –
- Make sure that the work area is clean and free of any sparks. Make sure that the ground is clean and dry and the shielding is tight.
- Make sure that the work area is clean and free of any sparks. Make sure that the ground is clean and dry and the shielding is tight.
- Wear welding gloves. There are many types of welding gloves that help to protect your hands from the heat and sparks of the welding process.
- Wear welding gloves. There are many types of welding gloves that help to protect your hands from the heat and sparks of the welding process.
- Keep the work area clean from sparks. Aluminum will begin to oxidize as soon as it comes in contact with oxygen, and it is very difficult to remove the oxidation once it has formed.
- Keep the work area clean from sparks. Aluminum will begin to oxidize as soon as it comes in contact with oxygen, and it is very difficult to remove the oxidation once it has formed.
- Watch the arc. The arc in the welding machine should be at about the middle of the electrode. If it goes too low or too high, then the weld will be weak and the weld spot will be damaged.
- Watch the arc. The arc in the welding machine should be at about the middle of the electrode. If it goes too low or too high, then the weld will be weak.
Why Welding Aluminum Is a Good Idea
Aluminum is a very strong metal that is lightweight and very flexible. But aluminum is also very soft. Welding aluminum is a great way to strengthen a weak spot in the boat while increasing its flexibility. Welding aluminum is another great way to create a more durable boat. It can be done quickly, easily, and relatively inexpensively. It is also a great way to make your boat more resistant to wear and tear.
Welded aluminum is much harder than an aluminum boat that is not welded. You will not have to worry about your boat getting dented or cracked as easily. Welded aluminum is also more resistant to corrosion, which means it will last longer than an aluminum boat that is not welded.