Gas welding is a versatile welding process widely used in various industries. One of the critical factors that determine the success of a gas welding operation is the proper understanding and selection of welding flames. In this article, we will explore the different types of gas welding flames and their uses.
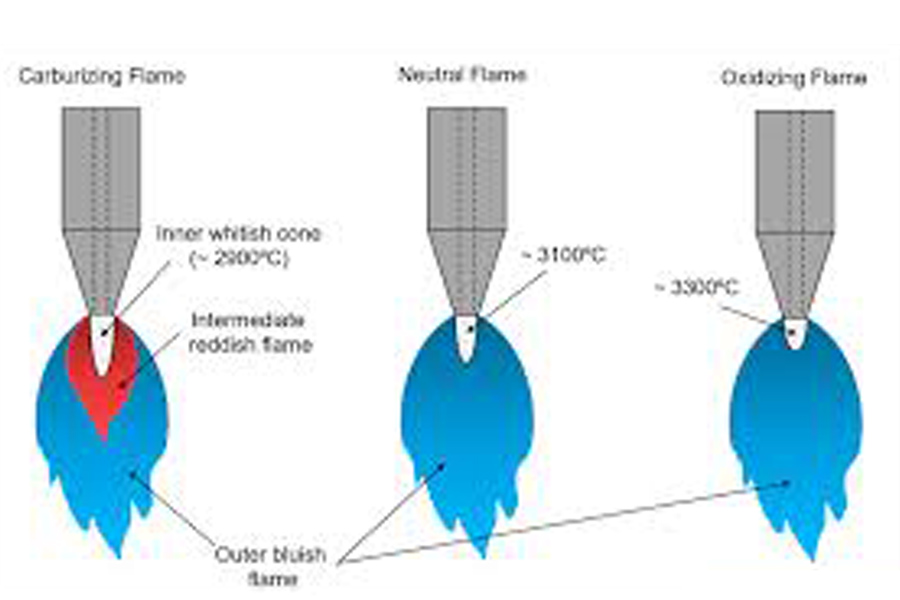
Neutral Flame: Characteristics and Uses
The neutral flame, with a well-defined blue cone and a light inner cone, maintains a balance between oxygen and acetylene. It is suitable for general welding applications involving mild and stainless steels.
The neutral flame is often considered the most versatile gas welding flame. It provides a stable and controlled heat source, making it ideal for welding tasks that require precision and control. The blue cone of the neutral flame is the hottest part, reaching temperatures of around 5,500 degrees Fahrenheit (3,000 degrees Celsius). This high temperature allows for efficient melting and fusion of metals.
One of the primary uses of the neutral flame is in the welding of mild steel and stainless steels. It produces a clean, strong weld with good penetration. The neutral flame is also used for brazing and soldering operations, as it provides sufficient heat to melt the filler material without causing excessive distortion or damage to the base metals.
In addition to its welding applications, the neutral flame is also utilized for cutting tasks. By increasing the oxygen flow, the neutral flame can be transformed into an oxy-fuel cutting flame, which is capable of severing metals with ease.
Overall, the neutral flame is a reliable and versatile option for a wide range of gas welding applications. Its ability to provide controlled heat makes it an indispensable tool for welders working with various metals and alloys.
Oxidizing Flame: Characteristics and Uses
The oxidizing flame, characterized by a short, pointed blue cone, has excess oxygen. It is used for welding metals like copper and bronze, as it helps remove impurities and create cleaner welds. The oxidizing flame is often used when working with metals that have a high affinity for oxygen, such as copper and bronze. The excess oxygen in the flame reacts with impurities in the metal, such as oxides and other contaminants, allowing them to be easily removed. This helps create cleaner welds with improved integrity.
The oxidizing flame is also beneficial when welding materials that have a tendency to absorb gases, such as aluminum and stainless steel. The excess oxygen in the flame helps prevent the absorption of atmospheric gases, reducing the risk of porosity and ensuring a sound weld.
Another application of the oxidizing flame is in the brazing and soldering of certain metals. The increased oxygen content aids in the removal of surface oxides, promoting better wetting and capillary action of the filler material.
However, it is important to note that the oxidizing flame should be used with caution, as excessive oxidation can lead to the formation of brittle welds or excessive heat-affected zones. It is crucial to maintain a proper balance and avoid prolonged exposure to the oxidizing flame to prevent these issues.
Carburizing Flame: Characteristics and Uses
The carburizing flame, distinguished by a long, luminous feather, has excess acetylene. It is used for applications where additional carbon content is desired, such as surface hardening and case hardening. The carburizing flame is primarily used in gas welding operations where carbon enrichment is required. The excess acetylene in the flame provides an additional source of carbon, which can be absorbed into the surface of the metal being welded.
One of the main applications of the carburizing flame is in surface hardening. By directing the carburizing flame onto the surface of the metal, the high carbon content of the flame can be absorbed, resulting in increased hardness and wear resistance. This process is commonly used in the heat treatment of tools and machine parts that require a hardened surface to withstand abrasion and wear.
The carburizing flame is also utilized in case hardening, where only the outer layer of the metal is hardened. This technique is often employed in the manufacturing of gears, cams, and other components that require a combination of strength and toughness.
It is important to note that the carburizing flame should be used with caution, as excessive carbon absorption can lead to brittleness and reduced ductility. Careful control of the carburizing process is essential to achieve the desired hardness without compromising the overall integrity of the metal.
Differences Between Neutral, Oxidizing, and Carburizing Flames
Each type of gas welding flame has distinct characteristics and uses. The neutral flame provides a balanced heat source, making it suitable for general welding applications involving mild and stainless steels. The oxidizing flame, with its excess oxygen, is used for welding metals like copper and bronze to remove impurities and create cleaner welds. The carburizing flame, with its excess acetylene, is employed for applications where additional carbon content is desired, such as surface hardening and case hardening.
The neutral flame is the most versatile of the three flames, offering a controlled heat source for precise welding and cutting tasks. The oxidizing flame is beneficial for metals that have a high affinity for oxygen, allowing for the removal of impurities and gas absorption prevention. The carburizing flame is used when carbon enrichment is required, providing increased hardness and wear resistance.
It is crucial to understand the differences between these flames to ensure optimal welding results. Selecting the appropriate flame for each welding task is essential for achieving strong and reliable welds.
Safety Precautions for Gas Welding Flames
When working with gas welding flames, it is important to prioritize safety to prevent accidents and injuries. Here are some essential safety precautions to follow:
- Ensure proper ventilation: Gas welding produces harmful fumes and gases, so it is crucial to work in a well-ventilated area or use exhaust fans to remove the fumes.
- Wear appropriate personal protective equipment (PPE): Always wear protective clothing, including flame-resistant gloves, a welding helmet with a suitable shade, and safety goggles to protect your eyes from sparks and debris.
- Use flashback arrestors: Flashback arrestors should be installed on both the oxygen and acetylene regulators to prevent the flame from traveling back into the gas supply hoses.
- Inspect equipment regularly: Regularly inspect the gas welding equipment, including hoses, regulators, and torches, for any signs of damage or wear. Replace any faulty or worn-out parts immediately.
- Store and handle cylinders safely: Store gas cylinders in an upright position, secured with appropriate restraints. Always handle cylinders with care, avoiding any rough handling or dropping that could cause damage.
- Keep a fire extinguisher nearby: Have a fire extinguisher readily available in case of emergencies. Ensure that you are familiar with its operation beforehand.
Following these safety precautions will help minimize the risk of accidents and create a safe working environment when using gas welding flames.
Common Mistakes to Avoid When Using Gas Welding Flames
While gas welding can be a highly effective welding process, there are some common mistakes that welders should avoid to ensure optimal results:
Incorrect flame adjustment
Improper adjustment of the flame can lead to poor weld quality and weak joints. It is essential to follow the manufacturer’s instructions and adjust the flame according to the specific welding task.
Inadequate cleaning and preparation
Failing to clean and prepare the base metals properly can result in poor fusion and weak welds. Thoroughly clean the surfaces to be welded, removing any dirt, rust, or coatings that may hinder the welding process.
Insufficient gas flow
Insufficient gas flow can lead to incomplete fusion and weak welds. Make sure that the gas flow rates are set correctly according to the welding requirements.
Lack of joint fit-up
Proper joint fit-up is crucial for achieving strong welds. Ensure that the parts being welded are properly aligned and have the correct gap or overlap.
Welding in windy conditions
Welding in windy conditions can negatively impact the stability of the flame and the quality of the weld. Whenever possible, choose a sheltered location or use windshields to protect the flame from drafts.
By avoiding these common mistakes, welders can improve the quality and integrity of their gas welding projects.
Applications of Gas Welding Flames in Different Industries
Gas welding flames find applications in various industries due to their versatility and effectiveness. Here are some industries where gas welding flames are commonly used:
Automotive industry: Gas welding is widely employed in the automotive industry for various applications, including body repair, exhaust system fabrication, and frame welding.
Construction industry: Gas welding is utilized in the construction industry for tasks such as joining structural steel components, fabricating metal frameworks, and repairing metal structures.
Manufacturing industry: Gas welding is an essential process in the manufacturing industry, used for the fabrication of machinery, tools, and equipment.
Aerospace industry: Gas welding plays a vital role in the aerospace industry, where it is used for welding aircraft components, such as fuel tanks, engine parts, and structural elements.
Artistic and decorative metalwork: Gas welding is commonly employed in artistic and decorative metalwork, allowing for the creation of intricate designs and sculptures.
These are just a few examples of the many industries that rely on gas welding flames for their welding needs. The versatility and effectiveness of gas welding make it a preferred choice in various applications.
Choosing the Right Gas Welding Flame for Your Project
Selecting the appropriate gas welding flame for a specific project is crucial for achieving optimal results. Consider the following factors when choosing the right flame:
Material type: Different metals and alloys require different gas welding flames. Consider the material you are working with and choose a flame that is suitable for that particular metal.
Welding process: Determine the specific welding process you will be using, such as fusion welding, brazing, or soldering. Each process may require a different flame type.
Welding position: Consider the position in which the welding will be performed, such as flat, vertical, horizontal, or overhead. Some flame types may be more suitable for certain positions.
Joint design and thickness: The joint design and thickness of the materials being welded can influence the choice of flame. Thicker materials may require a different flame setting to ensure proper fusion.
Welding application: Consider the specific application or purpose of the weld. Different applications may require specific flame characteristics, such as cleaner welds or increased carbon content.
By considering these factors, you can select the appropriate gas welding flame that will yield the best results for your project.
Conclusion
Understanding the different types of gas welding flames and their uses is crucial for achieving optimal welding results. The neutral flame provides a balanced heat source for general welding applications, while the oxidizing flame removes impurities and creates cleaner welds. The carburizing flame enriches the metal with additional carbon for surface hardening and case hardening. By selecting the right flame and following safety precautions, welders can achieve strong and reliable welds in various industries.