Cast iron and steel are two materials that are naturally incompatible. While this is true for any join between cast iron and other types of steel, the challenge rises exponentially when it comes to welding these two together. In addition to being two entirely different engineering materials, they also have very different physical properties. As a result of this incompatibility, welding cast iron to steel presents a number of unique challenges and very few successful solutions which can make it seem like a fool’s errand at times.
There are ways to overcome these difficulties and weld cast iron to steel effectively without suffering too many consequences in the process. With that in mind, let’s explore why this type of joint poses so many problems, as well as some effective solutions you can implement to get around these issues.
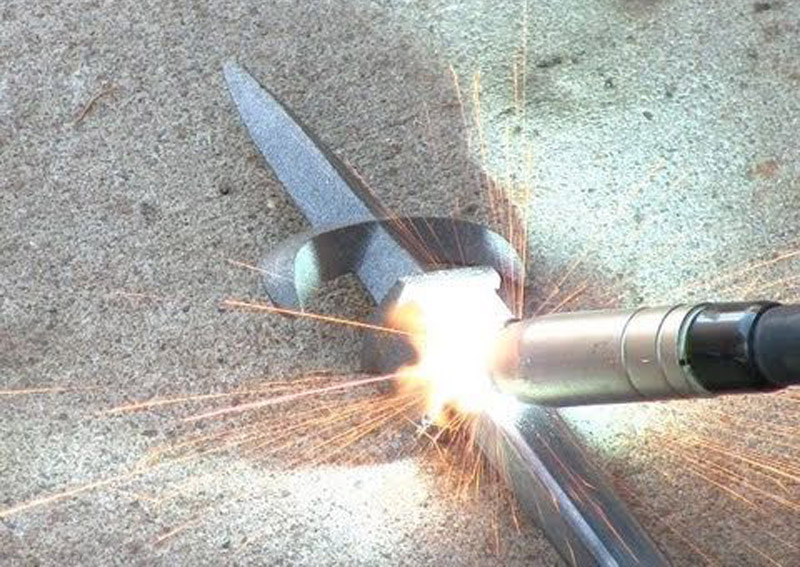
Definition of Welding Cast Iron to Steel
Cast iron is particularly well-suited for forming most types of joints. As a result, we can weld cast iron to steel with relative ease. The process of welding cast iron and steel exactly the same as welding any other type of material, including steel. Welding steel to cast iron involves melting the iron and steel together at a high temperature, while depositing a metal weld at a low temperature. The end result of this welding process is a metal weld that is strong enough to hold the two pieces together while maintaining their integrity. Depending on the type of weld used and the amount of heat applied, cast iron to steel welding can be done manually or via power welding equipment.
Why Welding Cast Iron and Steel is so Difficult?
The primary obstacle to weld cast iron to steel is the high thermal conductivity of the iron. This high conductivity means that the iron weld will be very porous and lose a great deal of strength over time. The reason that high thermal conductivity is such a major issue when welding cast iron to steel is that the two materials have such different thermal expansion properties. In other words, they expand at very different rates as they are heated and cooled.
In addition to thermal conductivity, the two materials themselves also pose a major challenge to welding. Iron has a very low melting point (-4.4°C), so there is little chance the weld will solidify and eventually fail.
Steel, on the other hand, has a much higher melting point of 1443°C. This means that, unless the weld joint is extremely well-insulated, there is a chance the weld will fail due to excessive heat transfer from the steel to the cast iron. With so many factors working against the welded joint, there aren’t many solutions that can overcome the thermal conductivity issues and still provide the same strength. Without some form of insulation to keep the two pieces from expanding at different rates, the weld will be very porous and lose a lot of strength over time.
Things to Consider When Welding Steel to Cast Iron
With so many issues working against the welded joint, it’s no wonder that welding cast iron and steel presents a significant challenge. With that in mind, let’s consider the best ways to tackle this welding challenge so that you can successfully weld cast iron to steel.
Be prepared
Welding cast iron to steel is a lot harder than welding steel. In fact, it’s one of the hardest types of welding you can do. This means that you will need to be a lot more prepared than you might otherwise be. Start by reading our welding tips for beginners article so that you are familiar with the basics and can avoid common mistakes. Then, make sure you have the right tools and safety gear to help you avoid injury and keep you safe while welding.
Avoid welding cast iron to cast iron
Many of the same issues that make welding cast iron to steel difficult also make it imperative that you don’t do it at all. First and foremost among these is the fact that the two types of iron are completely different. If you are attempting to weld cast iron to cast iron, you are going to encounter a lot of problems that simply don’t occur when welding steel to steel. We suggest you avoid this type of welding entirely until you have gotten a lot more experience.
Use the right welding method
While there are a number of techniques that can be used to weld cast iron to steel, they all share a common principle. The joints need to be insulated to prevent the two metals from expanding at different rates. This means that welding steel to cast iron should be done with a shielded arc welding method like gas tungsten arc welding (GTAW) or slag free arc welding (SFAW).
This method of welding will both protect the cast iron and allow for the appropriate use of shielding gas, which greatly reduces the chance of excessive heat transfer from the steel to the cast iron.
Use the right shielding gas
Shielding gas is also an important consideration when welding cast Iron with steel. While different welding methods will protect cast iron from excessive thermal conductivity, they don’t provide effective protection against slag. This is the black, caked-on material that forms on both the surface of the cast iron and the torch tip when welding cast iron. This slag can be extremely damaging to the joint, drastically lowering the strength of the weld and shortening the life of the joint.
The best way to prevent slag formation on the joint is to weld with a shielded arc welding method like GTAW or SFAW. This will not only protect the cast iron, but also allow for the proper use of shielding gas, which substantially reduces the chances of excessive heat transfer to the steel.
Recommended Tools and Materials
Welding equipment
You will need a welder to weld cast iron to steel, but you don’t need anything too expensive. A simple stick welder will work fine, as will a MIG welder if you are interested in learning the basics. You will need a welder to weld cast iron to steel, but you don’t need anything too expensive. A simple stick welder will work fine, as will a MIG welder if you are interested in learning the basics.
Oxygen, shielding gas
Shielding gas is important for protecting the weld from thermal conductivity, as well as preventing slag from forming on the torch tip. Make sure you don’t use argon as this causes slag formation. Shielding gas is important for protecting the weld from thermal conductivity, as well as preventing slag from forming on the torch tip. Make sure you don’t use argon as this causes slag formation.
Gas shut-off valves
You will also need valves to shut off the gas before removing the electrode and before putting the torch away. You will also need valves to shut off the gas before removing the electrode and before putting the torch away.
MIG Welder
We are going to be welding with a MIG, so make sure you get one that’s capable of running a MIG wire. We are going to be welding with a MIG, so make sure you get one that’s capable of running a MIG wire.
Stick Welder
Again, we are going to be welding with a stick welder, so make sure you get one that’s capable of running a stick wire.
Type of Welding Cast Iron to Steel
Shielded
As we mentioned above, shade arc welding is the best method for welding cast iron to steel, and it provides the most effective type of protection. As we mentioned above, shade-arc welding is the best method for welding cast iron to steel, and it provides the most effective type of protection.
Slag free Arc
Free welding is an acceptable alternative to shield arc welding, but it is not as effective as the latter. Arc free welding is an acceptable alternative to shield arc welding, but it is not as effective as the latter.
Welding Gas
There is the option of using a welding gas other than argon. This includes using CO2 for slag-free joint protection and CO for arc-free production.
How to Weld Cast Iron to Steel?
Welding cast iron to steel is a challenging process, but it can be done with the right equipment and technique. Here are the steps to follow:
- Clean the cast iron and steel surfaces thoroughly to remove any rust, dirt, or oil.
- Preheat the cast iron to approximately 500-1200°F, depending on the thickness of the material. This will help prevent cracking during the welding process.
- Use a nickel based welding electrode or wire, as this type of filler metal is compatible with both cast iron and steel.
- Weld the joint using the appropriate welding technique, such as stick welding or MIG welding. Be sure to maintain the preheat temperature throughout the process.
- Allow the welded joint to cool slowly to room temperature to minimize the risk of cracking.
With the right equipment and technique, welding cast iron and steel can be a successful process. However, it is important to note that this type of welding should only be attempted by experienced welders.
Tips for Successful Welding Cast Iron to Steel
Welding cast iron to steel can be challenging due to the differences in the materials, but there are some tips that can help ensure a successful weld:
Prepare the surfaces
Before welding, make sure to thoroughly clean and prepare the surfaces of both the cast iron and steel. This will help ensure a strong bond between the two materials.
Preheat the cast iron
Cast iron is prone to cracking when exposed to sudden temperature changes, so preheating the cast iron before welding can help prevent this.
Use the right welding rod
Nickel based welding rods or wires are ideal for welding cast iron to steel, as they are compatible with both materials.
Choose the right welding technique
Stick welding and MIG welding are two common techniques used for welding cast iron and steel. Stick welding is often preferred for thicker materials, while MIG welding is better suited for thinner materials.
Control the heat
When welding, it is important to control the heat to prevent the cast iron from overheating and cracking. This can be done by using a lower amperage setting, making shorter welds, and allowing the material to cool between welds.
Allow for proper cooling
After welding, it is important to allow the material to cool slowly to prevent cracking. This can be done by wrapping the weld in heat resistant material or allowing it to cool in a furnace.
By following these tips, you can increase your chances of successfully welding cast iron with steel. It is important to note that welding steel to cast iron is a complex process that should only be attempted by experienced welders.
Consequences of Welding Cast Iron to Steel
Welding cast iron to steel can have both positive and negative consequences, depending on the quality of the weld and the intended use of the welded joint. Here are some possible consequences:
Positive consequences:
Increased strength
Welding cast iron with steel can create a strong, durable joint that is capable of handling heavy loads and stress.
Cost savings
Welding cast iron and steel can be a more cost-effective solution than replacing a damaged component entirely.
Versatility
Welding cast iron to steel can allow for the creation of unique, custom components that may not be available commercially.
Negative consequences:
Cracking
Cast iron is prone to cracking when exposed to sudden temperature changes, so improper welding technique or insufficient preheating can lead to cracking in the welded joint.
Brittle welds
Welding cast iron with steel can result in a brittle weld if the wrong filler material is used, which can lead to premature failure of the joint.
Incompatibility
Welding cast iron and steel can result in an incompatible joint if the two materials have different expansion rates, which can cause stress and eventual failure of the joint.
Welding cast iron to steel can be a successful process if done correctly, but it is important to carefully consider the intended use of the welded joint and ensure it is done by an experienced welder to avoid negative consequences.
Final Thoughts
Welding cast iron to steel can be a challenging and complex process that requires careful consideration and proper technique. While it can result in a strong and durable joint, it is important to weigh the potential positive and negative consequences before attempting to weld these materials together. Proper preparation, preheating, and filler material selection are crucial to ensure a successful weld and avoid issues such as cracking or brittleness.
Welding steel to cast iron should only be attempted by experienced welders to minimize the risk of failure and ensure a high quality, long-lasting joint.