Tig welding is a popular technique used in the metal fabrication industry, especially when it comes to working with aluminum. The process involves melting metal pieces together using an arc and a filler material. Tig welding is highly versatile and can be used for a wide range of applications, from automotive repair to aerospace manufacturing. However, to achieve high quality welds, it’s crucial to select the right tig welding gas for aluminum. With so many options available, it can be overwhelming to choose the best gas for your project. But don’t worry, we have got you covered. In this ultimate guide, we will take you through everything you need to know about selecting the right tig welding gas for aluminum.
We will cover the different types of gases available, their properties, and how they affect the welding process. So whether you are a seasoned professional or a newbie in the welding industry, this guide will equip you with the knowledge and skills to make an informed decision when it comes to tig welding for aluminum.
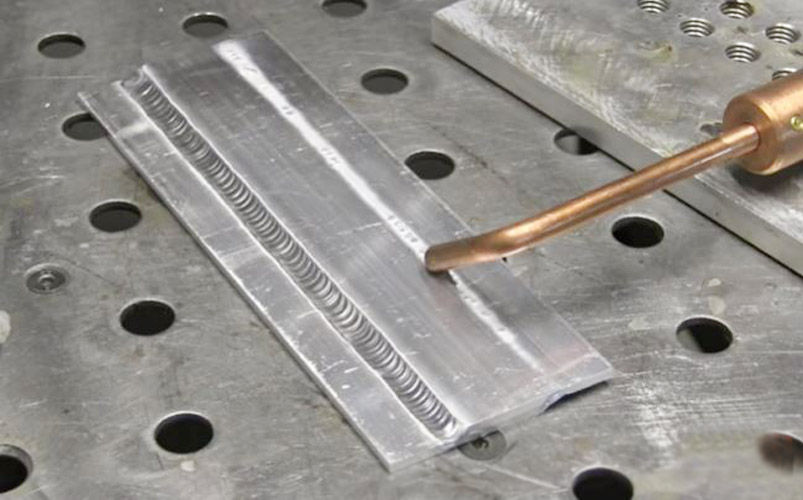
Photo by weldingtipsandtricks
What is tig welding?
Tig welding, also known as gas tungsten arc welding (GTAW), is a welding process that uses a non-consumable tungsten electrode to produce the weld. A filler material is used to join the metal pieces together. The process is typically used for welding thin sections of aluminum, stainless steel, and other metals that require precise control over the welding process.
The welding process is initiated by striking an arc between the tungsten electrode and the workpiece. The arc creates a high-temperature plasma that melts the metal pieces together. The filler material is added to the weld pool to join the metal pieces together. Tig welding is known for producing high-quality welds with excellent mechanical properties, making it a popular choice for high-performance applications.
Why is selecting the right tig welding gas important?
The choice of tig welding gas is critical in achieving high-quality welds. The gas used in the welding process serves several important functions. First, it shields the weld from atmospheric contamination, such as oxygen and nitrogen, which can cause porosity and other defects in the weld. Second, it helps to stabilize the arc and improve the heat transfer characteristics of the welding process. Finally, it can affect the mechanical properties of the final weld, such as its strength and ductility.
Given the critical role that tig welding gas plays in the welding process, it’s essential to select the right gas for your project. The choice of gas depends on several factors, including the type of metal being welded, the thickness of the metal, the welding position, and the desired mechanical properties of the final weld.
Factors to consider when selecting tig welding gas for aluminum
When selecting tig welding gas for aluminum, several factors should be considered. These include:
Type of metal being welded
The type of metal being welded is an essential consideration when selecting tig welding gas. Aluminum is a highly reactive metal that readily reacts with atmospheric gases such as oxygen and nitrogen. To prevent this reaction, an inert gas such as argon or helium is typically used as a shielding gas.
Thickness of the metal
The thickness of the metal being welded is another important factor to consider when selecting tig welding gas. Thicker sections of metal require a higher flow rate of gas to provide adequate shielding and heat transfer. Thinner sections of metal may require a lower flow rate of gas to prevent excessive turbulence in the weld pool.
Welding position
The welding position is also an important consideration when selecting tig welding gas. Welding in the vertical or overhead position requires a higher flow rate of gas to provide adequate shielding and prevent porosity in the weld. Welding in the flat or horizontal position may require a lower flow rate of gas to prevent excessive turbulence in the weld pool.
Desired mechanical properties
The desired mechanical properties of the final weld are another important consideration when selecting tig welding gas. Different gases can affect the strength, ductility, and other mechanical properties of the final weld. For example, a gas mixture containing helium can improve the penetration of the weld, resulting in a stronger joint.
Types of gases used in TIG welding for aluminum
Several types of gases are used in tig welding for aluminum. The most common gases used are argon, helium, and mixtures of argon and helium. Each gas has its unique properties and advantages.
Argon Gas For TIG Welding
Argon is the most commonly used gas in tig welding for aluminum. It’s an inert gas that doesn’t react with aluminum or other metals. It provides excellent shielding and helps to stabilize the arc during welding. Argon is also relatively inexpensive and widely available. It’s an excellent choice for welding thin sections of aluminum and provides a clean, cosmetic weld.
Helium Gas For TIG Welding
Helium is another gas that’s commonly used in tig welding for aluminum. It has a higher ionization potential than argon, which means it requires a higher voltage to initiate the arc. However, once the arc is established, helium provides excellent heat transfer characteristics and can penetrate deeper into the metal than argon. Helium is an excellent choice for welding thicker sections of aluminum or for applications that require a stronger weld.
Mixtures Gas For TIG Welding
Mixtures of argon and helium are also commonly used in tig welding for aluminum. These mixtures can provide the benefits of both gases, such as excellent shielding, arc stability, and heat transfer characteristics. The exact mixture of gases used depends on the specific application and desired welding characteristics.
Properties of each gas and how they affect the welding process
Each gas used in tig welding for aluminum has its unique properties and can affect the welding process differently. Understanding these properties is essential in selecting the right gas for your project.
Argon: Argon is an inert gas that doesn’t react with aluminum or other metals. It provides excellent shielding and helps to stabilize the arc during welding. Argon has a low ionization potential, which means it requires a lower voltage to initiate the arc. This can be an advantage when welding thin sections of aluminum. Argon also provides a clean, cosmetic weld, which is essential in applications where appearance is critical.
Helium: Helium has a higher ionization potential than argon, which means it requires a higher voltage to initiate the arc. Once the arc is established, helium provides excellent heat transfer characteristics and can penetrate deeper into the metal than argon. This can be an advantage when welding thicker sections of aluminum or when a stronger weld is required. Helium also provides a hotter arc, which can be beneficial in applications where a higher welding speed is desired.
Mixtures: Mixtures of argon and helium can provide the benefits of both gases. The exact mixture used depends on the specific application and desired welding characteristics. For example, a mixture with a higher helium content can provide better penetration and a stronger weld, while a mixture with a higher argon content can provide a clean, cosmetic weld.
How to calculate the amount of gas for tig welding aluminum?
Calculating the amount of gas needed for your welding project is essential to ensure adequate shielding and heat transfer. The amount of gas required depends on several factors, including the type of gas used, the flow rate, and the welding time.
To calculate the amount of gas needed, you can use the following formula:
Gas volume (cubic feet) = (flow rate (cubic feet per minute) x welding time (minutes)) / 60
For example, if you are using argon at a flow rate of 20 cubic feet per minute and welding for 30 minutes, the gas volume required would be:
Gas volume (cubic feet) = (20 x 30) / 60 = 10 cubic feet
Tips for using TIG welding gas for aluminum – storage, handling and safety measures
When using tig welding gas for aluminum, it’s essential to follow proper storage, handling, and safety measures. Here are some tips to keep in mind:
- Store gas cylinders in a cool, dry, well-ventilated area away from heat sources, flammable materials, and direct sunlight.
- Handle gas cylinders carefully, and always use a cylinder cart to transport them.
- Use the appropriate regulators and flow meters to ensure accurate gas flow rates.
- Always wear appropriate personal protective equipment, such as gloves, safety glasses, and a respirator.
- Ensure adequate ventilation in the welding area to prevent the buildup of hazardous fumes.
The impact of the final weld quality
Understanding these properties is essential in selecting the right gas for your project. Proper storage, handling, and safety measures are also essential when using tig welding gas for aluminum. By following these guidelines, you can achieve high-quality welds with excellent mechanical properties, making tig welding an excellent choice for a wide range of applications in the metal fabrication industry.