Proven technology and record-low costs make gasless flux core welding (GFCW) an increasingly attractive option for many manufacturing operations. This type of arc welding uses a wire instead of a stick electrode to produce welds, cutting down on maintenance and extending the life of your process components.
This blog will help you get up to speed so that you can integrate gasless flux core welding into your manufacturing process with ease. You will learn about the advantages and disadvantages of gasless flux core welding, explore the various types of gasless flux core welding processes, understand the cost implications and more.
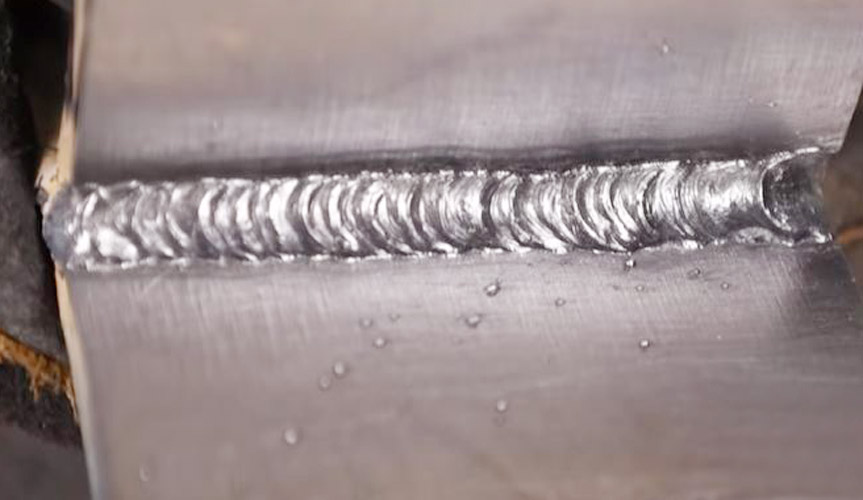
Photo by TimWelds on YT
About the Gasless Flux Core Welding
Gasless flux core welding is a type of arc welding that uses a wire electrode and a flux cored wire to produce welds. Welding machines that are dedicated to this process are called gasless welders, and they use a wire electrode instead of a stick electrode. This electrode is called a rod or slinger and is made of tungsten, nickel or cobalt. The flux cored wire is also made of these metals, but instead of a core made of rod, the wire has a coating of nickel or molybdenum on the inside.
This coating helps to improve weld quality and promote better weld penetration. Gasless flux core welding is a viable alternative to stick welding because it uses less electricity and has fewer maintenance requirements. It can also be used to make more complicated welds, such as fillet welds and penetration welds.
Advantages of Gasless Flux Core Welding
There are some advantage of welding:
Less Maintenance – Gasless flux core welding is easy to maintain because there are no electrodes and no consumable parts to change. The only wear item on a GFCW welder is the wire itself.
Great weld quality – Gasless flux core welding produces high-quality welds with excellent penetration and a smooth surfaces. This makes it well-suited for applications in which an aesthetic finish is important.
Flexible Welding Applications – Gasless flux core welding can produce a huge variety of types of welds.
Disadvantages of Gasless Welding
More complicated process – GFCW is a more complicated process than stick welding. Because the weld is produced by wire instead of a stick electrode, there are additional steps to set up the welder and start welding.
More expensive process – The cost of setting up a GFCW process is higher than stick welding. There are also additional costs associated with welding with a wire instead of a stick electrode.
More hazardous process – The welding process is more hazardous than stick welding. In addition to the increased risk of welding accidents, there are also additional health hazards present in GFCW welding.
GFCW Process Types
GFCW welders use three basic process types: flux core arc, direct current, and alternating current.
Flux Core Arc. Flux core arc welding uses flux cored wires and rods made from tungsten, nickel or cobalt. The flux core wire has a coating of nickel or molybdenum on the inside.
Direct Current. Direct current welding uses high-frequency alternating current that’s produced by a generator. The alternating current creates a strong electric arc between the electrode (rod) and the workpiece.
Alternating Current. The third welding process type is alternating current. This process type uses low-frequency alternating current that’s produced by a transformer.
Setting Up for Gasless FCAW
Before you can begin welding, you will need to set up the welding area properly. This includes making sure that the welding machine is set up and that all of the safety gear is in place. It is important to make sure that the metal pieces you are welding are clamped securely and that the electrodes are properly attached to the welding machine.
Once the machine is set up and the metal pieces are clamped securely, you can begin welding. Make sure that the metal pieces are clean and free of any dirt or debris, as this can cause the welding process to be less effective. It is important to make sure that the metal pieces are in the correct position, as this will ensure that the weld is strong and reliable.
Gasless Flux Core Welding Techniques
Once you have all the necessary tools and materials, you can start learning the basics of gasless flux core welding. The most important technique is the “stitch weld”, which involves welding two pieces of metal together in a series of overlapping circles. This technique is used to make strong, durable welds and should be mastered before attempting any other types of welding.
Another important technique is the “butt weld”, which involves welding two pieces of metal together end-to-end. This technique is ideal for joining two pieces of metal together that have similar thicknesses, as it provides a strong and reliable weld.
This technique can also be used to join two pieces of metal that have different thicknesses, although it is important to be careful when doing so as the thinner metal may be more prone to warping. The “fillet weld” is another important technique to master, as it is used to join two pieces of metal at an angle. This technique is ideal for joining two pieces of metal that have different thicknesses, as it provides a strong and reliable weld.
Safety Considerations for Gasless Weld
Gasless flux core welding is relatively safe, as long as the appropriate safety measures are taken. It is important to always wear the necessary safety gear, such as a welding helmet, gloves, and protective clothing. It is important to make sure that the welding area is free of any flammable materials, as sparks from the welding process can easily ignite them.
Make sure that the welding machine is set up correctly and that all of the necessary safety measures have been taken. This includes making sure that the machine is properly grounded and that the welding cables are in good condition. It is important to make sure that the machine is not exposed to high temperature objects, as this can cause the machine to overheat and potentially cause a fire.
Tips for Better Gasless Flux Core Weld
Once you have the necessary tools and materials and have mastered the basics of gasless flux core welding, there are a few tips and tricks that can help you become an expert. One of the most important tips is to practice welding regularly, as this will help you become more familiar with the process and hone your skills. It is important to always keep your welding machine and tools clean and in good condition, as this will ensure that the welding process is as efficient and safe as possible.
It is also important to pay attention to the position of the welding electrodes, as this can have a major impact on the quality of the weld. It is important to make sure that the metal pieces you are welding are clean and free of any dirt or debris, as this can cause the welding process to be less effective.
Troubleshooting Tips
If you are having trouble with your gasless flux core welding, there are a few troubleshooting tips that can help. One of the most common problems is that the welding machine is not set up correctly, which can cause the welding process to be less effective. It is important to make sure that the electrodes are properly attached to the welding machine and that the welding cables are in good condition. Another common problem is that the metal pieces are not in the correct position, which can cause the weld to be weak or unreliable.
Common Mistakes to Avoid when Gasless Welding
When it comes to gasless flux core welding, it is important to avoid making any common mistakes. One of the most common mistakes is not wearing the appropriate safety gear. Make sure that the welding area is free of any flammable materials, as sparks from the flux core welding process can easily ignite them. Another mistake is not preparing the metal pieces properly before welding, as this can cause the welding process to be less effective. It is important to make sure that the metal pieces are clamped securely and that the electrodes are properly attached to the welding machine.
Make sure that the welding machine is set up and that all of the safety measures have been taken. This includes making sure that the machine is properly grounded and that the cables are in good condition. Make sure that the welding machine is not exposed to any high temperature objects, as this can cause the machine to overheat and potentially cause a fire.
How much does GFCW cost?
GFCW costs are dependent on several factors, including the type of GFCW welding machine being used and the location of the operation. For example, a gasless flux core welder that’s in operation for an hour in a Southern state will cost more than the same machine operating in a Northern state. The cost of a GFCW process also depends on its type. In general, the more expensive processes such as flux core arc have better weld quality and are therefore more expensive than the lower cost processes such as alternating current welding. When comparing prices, be sure to consider the entire cost of a GFCW system, including equipment cost, installation cost, maintenance cost, training cost and the cost of consumables.
Last word about GFCW
GFCW is proven technology with proven cost savings. This technology has developed and changed little since the 1950s, and it’s easy to implement because it doesn’t require a big investment in new equipment. GFCW is suitable for many types of industries and processes. Gasless welding offers high-quality welds with excellent penetration. This makes it well-suited for applications in which an aesthetic finish is important, including structural, marine and pipe welds. Gasless welding is also a low maintenance process, so it’s easy to maintain.
Gasless welding costs are dependent on a number of factors, type of welding machine being used and the location of the operation. The cost of a GFCW process also depends on its type. When comparing prices, be sure to consider the entire cost of a GFCW system, including equipment cost, installation cost, maintenance cost, training cost and the cost of consumables.