Welding is a hugely important process in modern manufacturing, used to connect two pieces of metal together. While there are many different types of welding, the most popular of them stringer vs weave bead welding. Stringer welding is a process that involves creating a single line of weld along the joint of the two pieces of metal. Weave bead welding is slightly different, as it involves laying a bead of weld across the joint and then weaving it in and out of the previous bead to create a pattern.
Both of these processes have their advantages and disadvantages, and each type of welding is more suited to certain applications. Discover the difference between stringer vs weave bead welding and learn which type of welding is best for your project.
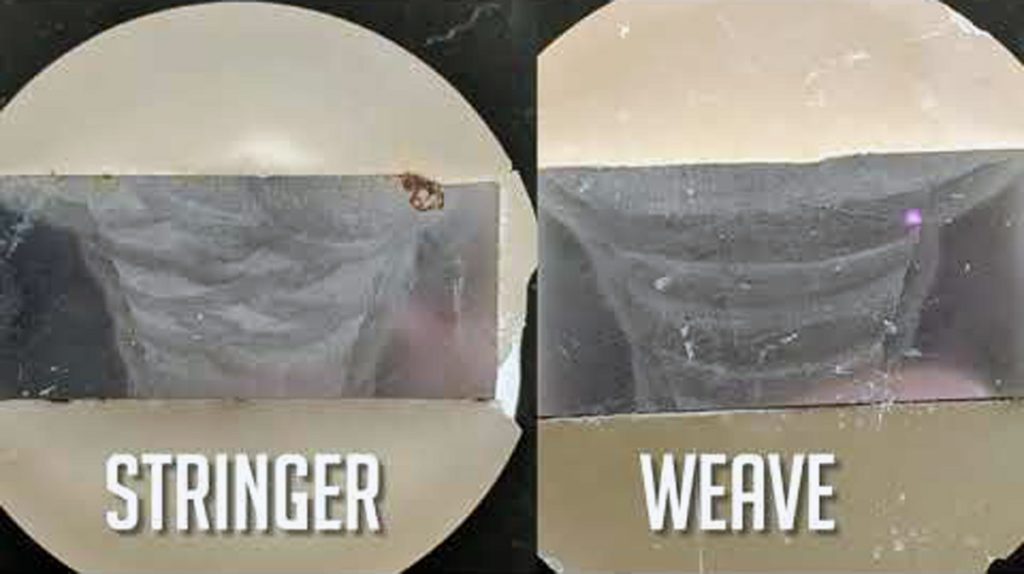
Photo by Welddotcom
What is Stringer Welding?
Stringer welding is a process that involves creating a single line of welding along the two pieces of metal together. The welder will typically begin at one end of the joint and slowly move the welding torch in a straight line along the entire joint. Stringer welding is a great option for long welds, as there is less risk of creating weak spots or gaps in the weld. Stringer welding is cost-effective and can be performed quickly, making it a popular choice for many manufacturing projects.
When performing stringer welding, it is important to use the correct welding technique and materials. The welder should use a consistent speed and angle when making the weld, and should ensure that the metal is properly prepared before welding.
What is Weave Bead Welding?
Weave bead welding is slightly different from stringer welding, as it involves laying a bead of welding across the joint and then weaving it in and out of the previous bead. This process is more time consuming, but it can create a stronger weld due to the increased surface area. Weave bead welding is typically used for shorter welds, as it can be difficult to achieve a consistent pattern for longer welds.
When performing weave bead welding, it is important to use the correct technique and materials. The welder should adjust the speed and angle of the welding torch to create a uniform pattern, and should ensure that the metal is properly prepared before welding.
Advantages of Stringer Welding
Stringer welding has a number of advantages over other types of welding. As mentioned earlier, it is a cost-effective and time-saving option for long welds. Stringer welding can be used on a variety of metals, and is particularly well suited to thin metals such as sheet metal. The single line of weld also ensures that there are no weak spots or gaps in the weld, making it a great choice for strength and durability.
Advantages of Weave Bead Welding
Weave bead welding also has several advantages over other types of welding. As mentioned earlier, it can create a stronger weld due to the increased surface area. It is well suited for short welds, as it can be difficult to achieve a consistent pattern for longer welds. Weave bead welding is also more aesthetically pleasing, as it can create a decorative pattern along the joint.
Disadvantages of Stringer Welding
While stringer welding has several advantages, there are also some potential drawbacks. One of the main disadvantages is that it is not well suited for short welds, as it can be difficult to keep a consistent line of weld along a short joint. Stringer welding is not as aesthetically pleasing as weave bead welding, as it creates a single line of weld along the joint.
Disadvantages of Weave Bead Welding
Weave bead welding also has a few drawbacks. As mentioned earlier, it is time consuming and more difficult to achieve a consistent pattern for longer welds. It is more expensive than stringer welding due to the increased time and materials required.
Best Practices for Stringer vs Weave Bead Welding
When performing stringer vs weave bead welding, it is important to use the correct welding technique and materials. The welder should use a consistent speed and angle when making the weld, and should ensure that the metal is properly prepared before welding. The type of welding rod also will depend on the type of metal being welded, and it is important to use the correct rod to ensure a strong and secure weld.
It is also important to practice proper safety measures when performing any type of welding. The welder should wear protective clothing and equipment, including a welding mask and gloves, to protect themselves from sparks and heat. Additionally, the area should be properly ventilated to ensure that no harmful gases are released into the air.
What Type of Welding Should You Use?
The type of welding that is best suited for your project will depend on the type of metal being welded and the length of the weld. For long welds, stringer welding is typically the best option as it can be performed quickly and is cost-effective. For short welds, weave bead welding is generally the best option as it can create a stronger weld and is more aesthetically pleasing.
Tips for Choosing the Right Welding Method
When choosing the best welding method for your project, there are a few factors to consider. First, you should consider the type of metal and the length of the weld. For long welds, stringer welding is typically the best option, while for short welds, weave bead welding is generally the best option. It is also important to consider the cost and time required for each type of welding, as well as the aesthetics of the weld.
Final Thoughts
Stringer vs weave bead welding are two of the most popular types of welding, and each type of welding has its advantages and disadvantages. Stringer welding is a cost-effective and time-saving option for long welds, while weave bead welding is more time consuming but can make a stronger weld. When choosing the best welding method for your project, it is important to consider the type of metal being welded, the length of the weld, the cost and time required, and the aesthetics of the weld. With this knowledge, you can choose the best welding method for your project and ensure a strong and secure welding.