Are you faced with the challenge of welding copper to stainless steel? Joining these two metals together can be a daunting task due to their significant differences in properties. However, with the right techniques and precautions, it is possible to achieve a strong and durable bond between them. In this article, we will explore the various methods and considerations involved in welding copper to stainless steel, providing you with expert tips and guidance to ensure your welding projects are a success.
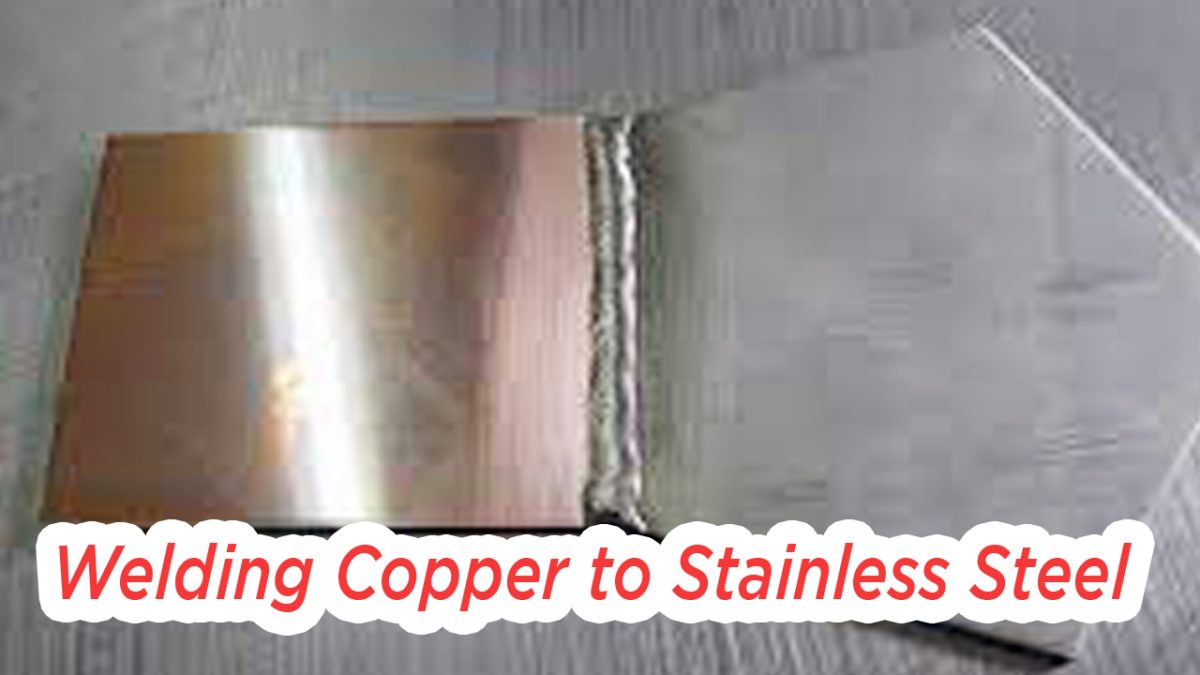
Challenges of Welding Copper to Stainless Steel
Before diving into the welding process, it’s crucial to understand the challenges associated with joining copper and stainless steel. These metals have distinct thermal conductivities, coefficients of expansion, and melting points, which can affect the success of the weld. Copper has excellent thermal conductivity, while stainless steel has a lower coefficient of expansion. These differences can lead to issues such as cracks, distortion, or a weak bond if not properly addressed.
The Importance of Proper Preparation Before Welding
Proper preparation is essential when welding copper to stainless steel. The first step is to ensure that both metals are clean and free from any contaminants like oil, grease, or dirt. Use a degreasing agent or solvent to thoroughly clean the surfaces that will be welded.
Next, it is crucial to remove any oxides or scales that may have formed on the metal surfaces. This can be achieved by wire brushing, sanding, or using a chemical pickling solution specifically designed for each metal. Proper preparation ensures optimal bonding and prevents defects in the weld.
Different Methods for Welding Copper to Stainless Steel
Several methods can be used to weld copper to stainless steel. The choice of method depends on factors such as the joint configuration, the thickness of the materials, and the desired strength of the weld. Let’s explore three commonly used methods: TIG welding, MIG welding, and spot welding.
TIG Welding Copper to Stainless Steel
Tungsten Inert Gas (TIG) welding, also known as Gas Tungsten Arc Welding (GTAW), is a popular method for joining copper to stainless steel. TIG welding uses a non-consumable tungsten electrode to produce the arc, while a separate filler metal is added manually. This method offers precise control and produces high-quality welds with excellent appearance and strength. However, TIG welding requires skill and expertise to achieve optimal results.
MIG Welding Copper to Stainless Steel
Metal Inert Gas (MIG) welding, also referred to as Gas Metal Arc Welding (GMAW), is another commonly used method for welding copper to stainless steel. MIG welding utilizes a consumable wire electrode that is continuously fed through a welding gun. A shielding gas is also used to protect the molten weld pool from atmospheric contamination. MIG welding is known for its speed and ease of use. However, it may not be suitable for all applications as it can create a less aesthetically pleasing weld compared to TIG welding.
Spot Welding Copper to Stainless Steel
Spot welding is a fast and efficient method for joining copper to stainless steel. This process involves applying pressure and an electric current to create a localized weld spot between the two metals. Spot welding is commonly used in sheet metal fabrication and can produce strong and reliable welds. However, it may not be suitable for thicker materials or complex joint configurations.
Common Issues and Troubleshooting in Welding Copper to Stainless Steel
Despite following the proper techniques and precautions, issues may arise during the welding process. Some common problems include porosity, cracking, and intermetallic phase formation. Porosity occurs when gas becomes trapped in the weld pool, resulting in voids or holes. Cracking can occur due to the differences in thermal expansion and contraction rates between copper and stainless steel. Intermetallic phase formation can lead to a brittle weld. Understanding these issues and implementing appropriate troubleshooting techniques can help overcome these challenges and achieve a successful weld.
Safety Precautions When Welding Copper to Stainless Steel
Safety should always be a top priority when welding. When welding copper to stainless steel, it is important to protect yourself from potential hazards. Wear appropriate personal protective equipment (PPE), including welding gloves, a welding helmet with a proper shade, and protective clothing. Ensure proper ventilation in the workspace to prevent the buildup of harmful fumes and gases. Additionally, be mindful of electrical hazards and take necessary precautions to avoid electric shock.
Best Practices for Successful Welding Copper to Stainless Steel
To ensure successful welds between copper and stainless steel, it’s important to follow best practices. Here are some key tips to keep in mind:
- Select the appropriate welding method based on the project requirements.
- Clean and prepare the surfaces thoroughly before welding.
- Use the correct filler metal or flux to facilitate bonding between the two metals.
- Maintain proper shielding gas flow and adjust welding parameters according to the material thickness.
- Monitor the weld pool and adjust the travel speed to achieve optimal penetration and fusion.
- Post-weld heat treatment may be necessary to relieve residual stresses and improve the mechanical properties of the weld.
By implementing these best practices, you can achieve strong and durable welds between copper and stainless steel, ensuring the longevity and reliability of your projects.
Can you weld copper to stainless steel?
Yes, you absolutely can weld copper to stainless steel! Isn’t that amazing? The ability to join these two different metals together opens up a whole new world of possibilities for engineers, fabricators, and craftsmen alike. Imagine being able to create intricate structures and designs that combine the strength and durability of stainless steel with the excellent thermal and electrical conductivity of copper. It’s like a dream come true!
Conclusion
Welding copper to stainless steel may present its challenges, but with the right techniques and precautions, it is possible to achieve a successful bond between these two metals. Understanding the properties and compatibility of copper and stainless steel, proper cleaning and preparation, and selecting the appropriate welding method are key factors in achieving strong and durable welds.
By following best practices and safety precautions, you can confidently tackle welding projects that involve joining copper and stainless steel, creating reliable and long-lasting connections.