Mastering the art of stick welding sheet metal can be a game-changer for both seasoned professionals and DIY enthusiasts. With its enduring appeal and robust results, stick welding brings a sense of craftsmanship to metalworking like no other. In this comprehensive guide, we delve into the nuanced techniques and best practices that elevate your sheet metal welding projects to new heights. Whether you are tackling automotive repairs or creating custom metal fabrications, the finesse of stick welding can make all the difference in achieving durable and seamless results.
Uncover the secrets to achieving immaculate welds on thin sheet metals and harness the full potential of this time-honored welding method. Gear up to transform your sheet metal welding prowess and unlock a world of possibilities with stick welding.
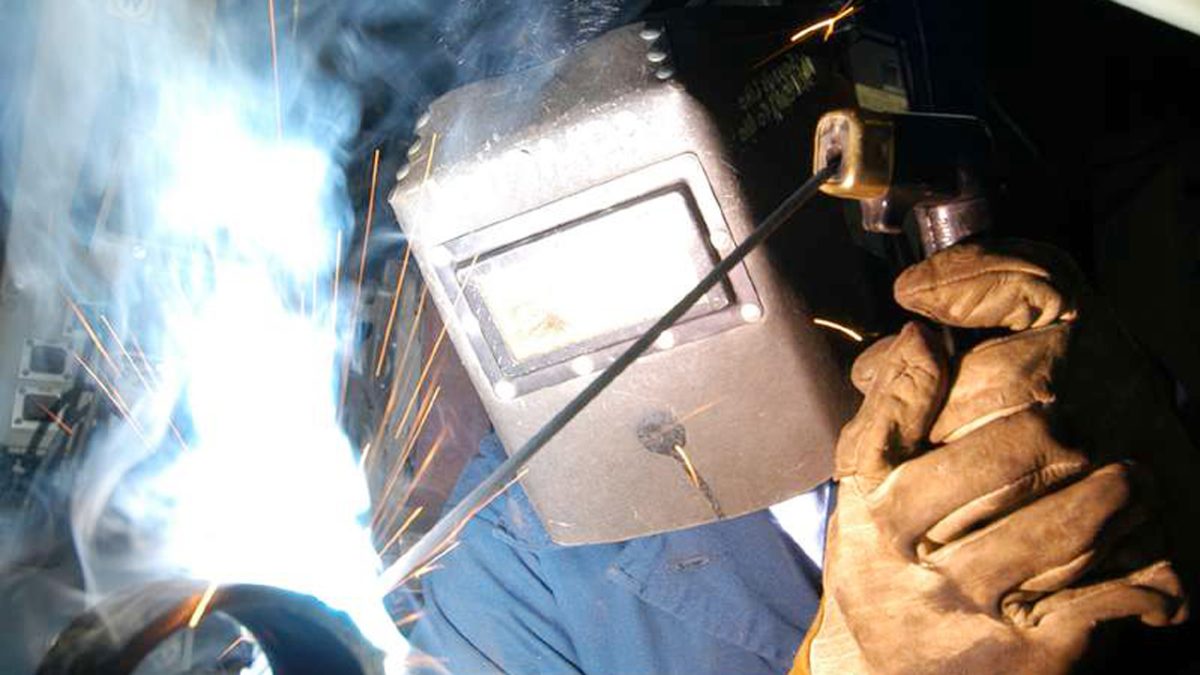
Image by imageindustries
Understanding the Stick Welding and Its Benefits for Sheet Metal
Stick welding, also known as shielded metal arc welding (SMAW), is a versatile and widely used welding process that involves the use of an electrode coated in flux to join metals. When it comes to sheet metal, the precise control and flexibility offered by stick welding make it an ideal choice for a range of applications. Unlike other welding methods, stick welding doesn’t require a shielding gas, making it suitable for outdoor welding or in windy conditions. This makes it a popular choice for automotive repairs, metal sculptures, and various fabrication projects. Stick welding is known for its ability to penetrate rusty or painted surfaces, making it an efficient option for welding older or pre-finished sheet metal.
Stick welding offers several benefits for sheet metal fabrication. It provides deep penetration, creating strong and durable welds on thin sheet metals. The simplicity of the equipment and the portability of stick welding machines make it accessible for both professionals and hobbyists. Furthermore, the versatility of stick welding allows for the welding of various metals, including steel, stainless steel, and cast iron, making it a go-to method for a wide range of projects.
Choosing the Right Stick Welding Equipment for Sheet Metal
Selecting the appropriate stick welding equipment is crucial for achieving high-quality welds on sheet metal. When working with thin sheet metals, it’s essential to use a welding machine that offers precise amperage control and a smooth arc. Look for a stick welding machine with a lower amperage range to ensure that you can fine-tune the welding parameters for thin sheet metal. Consider using a lower diameter electrode, such as 3/32 inch, to achieve more control and minimize heat input during the welding process.
In addition to the welding machine, the choice of electrode plays a significant role in stick welding sheet metal. Electrodes with a lower hydrogen content, such as E6010 or E6013, are well-suited for welding thin sheet metals as they produce cleaner and more controlled welds. It’s important to carefully match the electrode diameter and type to the specific requirements of the sheet metal being welded. By selecting the right equipment and electrode, you can set the stage for achieving precise and immaculate welds on sheet metal.
Preparing the Sheet Metal for Stick Welding
Proper preparation of the sheet metal surface is essential for successful stick welding. Before initiating the welding process, ensure that the sheet metal is clean and free from contaminants such as oil, rust, or paint. Use a wire brush or sandpaper to remove any surface impurities and create a clean welding surface. Additionally, consider using a degreaser or solvent to eliminate any residual oils or grease that could compromise the quality of the weld.
In some cases, it may be beneficial to use a metal cleaner or solvent specifically designed for pre-weld surface preparation. This can help ensure optimal weld penetration and minimize the risk of defects such as porosity or lack of fusion. Properly preparing the sheet metal surface sets the foundation for achieving strong and seamless welds, allowing the electrode to make direct contact with the metal and produce high-quality fusion.
Techniques for Stick Welding Sheet Metal
When stick welding sheet metal, employing the right techniques is crucial for achieving precise and aesthetically pleasing welds. Begin by striking the arc at the edge of the joint, allowing the electrode to establish proper fusion with the sheet metal. Maintain a consistent travel speed and angle to ensure even heat distribution and avoid excessive heat input that could lead to warping or burn-through. Use a weaving motion or back-and-forth technique to distribute the weld bead evenly across the joint, promoting optimal fusion and strength.
It’s important to monitor the welding parameters, such as amperage and arc length, to maintain control over the welding process. Adjust the amperage settings to match the thickness of the sheet metal, ensuring that the heat input is sufficient for proper fusion without causing distortion or burn-through. Maintaining a short arc length and a steady travel speed contributes to the creation of clean and uniform welds on the sheet metal. By employing these techniques, you can elevate the quality of your stick welding and achieve exceptional results on sheet metal projects.
Common Mistakes to Avoid When Stick Welding Sheet Metal
While stick welding offers numerous advantages for sheet metal fabrication, there are common mistakes that welders should avoid to ensure successful outcomes. One of the most prevalent mistakes is using excessive amperage, which can lead to burn-through and warping, particularly on thin sheet metals. It’s essential to adjust the amperage settings based on the thickness of the sheet metal to prevent overheating and maintain control over the welding process.
Another common mistake is neglecting proper joint preparation. Failing to clean and adequately prepare the sheet metal surface can result in weld contamination, porosity, or lack of fusion. Prioritize thorough surface cleaning and pre-weld preparation to optimize weld quality and structural integrity. Additionally, inconsistent travel speed or improper weaving techniques can lead to uneven weld beads and compromised fusion. By being mindful of these common mistakes and implementing best practices, welders can enhance their stick welding proficiency and achieve flawless results on sheet metal.
Advantages of Stick Welding Sheet Metal Fabrication
Stick welding offers several distinct advantages for sheet metal fabrication projects. Its versatility and flexibility make it well-suited for a wide range of applications, from automotive repairs to custom metal fabrications. The ability of stick welding to penetrate rusty or painted surfaces makes it an efficient option for welding older or pre-finished sheet metal without requiring extensive surface preparation. The simplicity and portability of stick welding equipment make it accessible for both professionals and hobbyists, allowing for greater creative freedom and flexibility in metalworking endeavors.
In terms of weld quality, stick welding provides deep penetration, resulting in strong and durable welds on thin sheet metals. This is particularly beneficial for applications that require robust and long-lasting welds, such as structural components or load-bearing elements. The cost-effectiveness of stick welding equipment and consumables makes it an attractive choice for sheet metal fabrication, offering a balance of performance and affordability for welding projects of varying scales.
Best Practices for Stick Welding Thin Sheet Metal
When stick welding thin sheet metal, following best practices is essential for achieving high-quality welds and minimizing the risk of distortion or burn-through. Begin by selecting the appropriate electrode type and diameter for the specific characteristics of the sheet metal, ensuring compatibility and optimal weld performance. Additionally, fine-tune the amperage settings on the welding machine to match the thickness of the sheet metal, preventing excessive heat input and preserving the integrity of the metal.
Maintain a short arc length and a consistent travel speed to promote even heat distribution and uniform fusion across the joint. Utilize proper weaving techniques to distribute the weld bead evenly and achieve structural strength without compromising the integrity of the sheet metal. Prioritize thorough surface cleaning and pre-weld preparation to eliminate contaminants and ensure direct electrode-to-metal contact for superior weld quality. By adhering to these best practices, welders can elevate their stick welding proficiency and produce flawless welds on thin sheet metal with confidence and precision.
Safety Measures for Stick Welding Sheet Metal
Safety is paramount when engaging in stick welding, particularly when working with sheet metal. Prior to commencing any welding activities, ensure that the work area is well-ventilated to prevent the accumulation of welding fumes and gases. Use appropriate personal protective equipment, including welding helmets with proper eye protection, flame-resistant clothing, gloves, and welding boots to safeguard against potential hazards. Additionally, have fire extinguishing equipment readily available in the event of a welding-related fire.
Avoid welding in proximity to flammable materials or surfaces to minimize the risk of fire hazards. It’s essential to be mindful of electrical safety and ensure that the welding machine is properly grounded to prevent electric shock or arc flash incidents. Regularly inspect the welding equipment and cables for any signs of wear or damage, and promptly address any issues to maintain a safe working environment. By prioritizing safety measures and adhering to best practices, welders can mitigate potential risks and create a secure environment for stick welding sheet metal.
Stick Welding vs Other Welding Methods for Sheet Metal
When considering welding methods for sheet metal, it’s essential to compare and contrast the advantages and limitations of stick welding with other popular welding techniques, such as MIG (Metal Inert Gas) welding and TIG (Tungsten Inert Gas) welding. While MIG welding offers higher deposition rates and greater efficiency for thicker sheet metals, stick welding excels in its ability to penetrate rusty or painted surfaces and its suitability for outdoor or adverse conditions. TIG welding, on the other hand, provides superior control and precision for thin sheet metal welding, making it a preferred choice for intricate and high-precision applications.
In terms of cost and accessibility, stick welding stands out for its simplicity and affordability, making it a viable option for hobbyists and professionals alike. Additionally, the versatility of stick welding in welding various metals, including steel, stainless steel, and cast iron, contributes to its widespread utility in sheet metal fabrication. Ultimately, the choice of welding method depends on the specific requirements of the project, the desired weld characteristics, and the environmental conditions in which welding will take place.
Conclusion and Recommendations for Stick Welding Sheet Metal
In conclusion, mastering the art of stick welding sheet metal opens up a world of possibilities for achieving exceptional welds and bringing creative metalworking projects to life. By understanding the nuances of stick welding and implementing the best practices outlined in this guide, welders can elevate their proficiency and produce immaculate welds on thin sheet metals. From selecting the right equipment and electrodes to employing precise welding techniques and prioritizing safety measures, every aspect of stick welding sheet metal contributes to the creation of durable and seamless welds.
For those embarking on sheet metal welding projects, it’s essential to recognize the advantages of stick welding, including its versatility, deep penetration, and accessibility. By honing their skills and adhering to safety protocols, welders can harness the full potential of stick welding and unlock a world of creative opportunities in sheet metal fabrication. Whether it’s automotive repairs, custom metal fabrications, or structural components, the finesse of stick welding can make all the difference in achieving durable and high-quality results. Embrace the art of stick welding and transform your sheet metal welding prowess with precision, craftsmanship, and a passion for metalworking excellence.
Stick welding sheet metal is not just a welding process; it’s an art form that empowers welders to create enduring and exceptional metalwork with finesse and mastery.