In the ever-evolving landscape of precision engineering, metal laser welding stands as a beacon of innovation and efficiency. This advanced welding technique has redefined the way metal components are joined together, offering unparalleled strength, durability, and precision. From the automotive to aerospace industries, the impact of metal laser welding is indisputable, promising enhanced structural integrity and superior product performance. Let’s delve into the intricacies of metal laser welding, exploring its advantages, processes, applications, considerations, equipment, safety precautions, comparisons with traditional methods, and the importance of training and certification in this field.
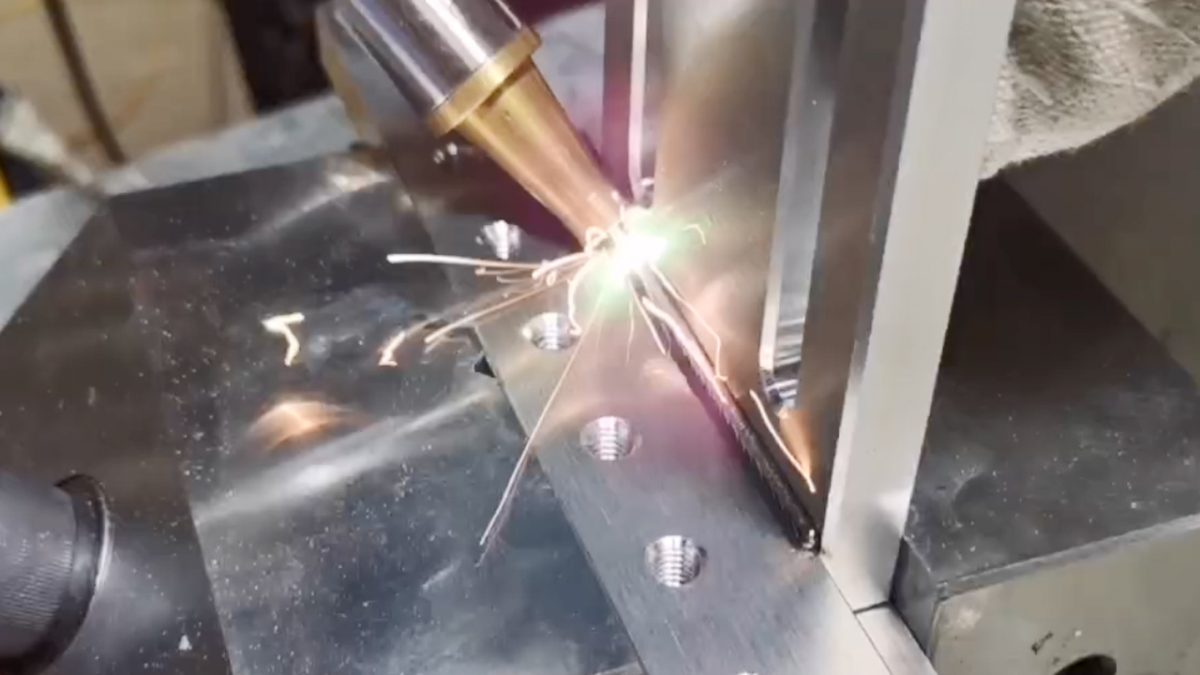
Image by heatsign
Advantages of Laser Welding Metals
Metal laser welding boasts a myriad of advantages that have positioned it as a preferred method for joining metal components. The precision and accuracy achieved through laser welding result in minimal distortion of the workpiece, ensuring that the structural integrity of the materials remains uncompromised. The concentrated heat source of the laser enables deep weld penetration, leading to stronger and more durable joints.
The non-contact nature of the process reduces the risk of contamination and allows for the welding of intricate and hard-to-reach areas, further expanding the application possibilities. The speed and efficiency of metal laser welding contribute to significant time and cost savings, making it an economically viable choice for various industries.
Maser welding metal also facilitates the welding of dissimilar metals with varying thicknesses, overcoming the limitations of traditional welding methods. The ability to weld a wide range of materials, including stainless steel, aluminum, titanium, and more, underscores the versatility of metal laser welding. This adaptability makes it a valuable asset in the production of components for diverse applications, from medical devices to electronic enclosures.
The precise control over the welding parameters, such as power, pulse duration, and beam focus, allows for customization according to specific material properties and application requirements, ensuring optimal results. These advantages collectively position metal laser welding as a cornerstone of modern manufacturing and engineering processes, driving advancements across industries.
The environmental benefits of laser welding metal are also noteworthy, as the process generates minimal fumes and waste compared to traditional welding methods. The reduced energy consumption and heat-affected zones contribute to a more sustainable and eco-friendly approach to metal joining, aligning with the global shift towards greener manufacturing practices. This confluence of advantages establishes laser welding metal as a pivotal technology that not only elevates the quality and performance of products but also aligns with the principles of sustainability and efficiency.
Types of Metal Laser Welding Processes
Laser welding metal encompasses various processes, each tailored to specific applications and material requirements. The two primary methods are conduction mode welding and keyhole mode welding. Conduction mode welding, also known as heat conduction welding, is characterized by its low power density and shallow penetration, making it suitable for thin and highly reflective materials. This method relies on the conduction of heat through the material, creating a stable and controlled weld pool.
On the other hand, keyhole mode welding, or deep penetration welding, utilizes high power density to create a vapor-filled cavity, or keyhole, within the material. This approach enables deep penetration and is ideal for thick materials, ensuring robust and secure welds. The selection of the welding process is determined by factors such as material thickness, joint design, heat input requirements, and desired weld characteristics, highlighting the versatility and adaptability of laser welding metal.
Pulsed laser welding and continuous wave (CW) laser welding are additional variations that offer distinct advantages based on the specific application. Pulsed laser welding delivers energy in periodic pulses, allowing for precise control over the heat input and minimizing thermal distortion. This method is often favored for thin materials and delicate components, where maintaining material integrity is paramount. Conversely, CW laser welding provides a continuous and stable heat source, enabling rapid and efficient welding of thicker materials.
The suitability of each process depends on factors such as weld speed, power density, and material composition, necessitating a thorough understanding of the nuances of each method for optimal results. The diverse range of metal laser welding processes underscores its adaptability to a multitude of industrial requirements, cementing its status as a cornerstone of modern manufacturing techniques.
The evolution of laser welding metal has also led to the development of hybrid welding processes that combine laser technology with other welding methods, such as arc welding or electron beam welding. These hybrid approaches leverage the strengths of each individual method, providing enhanced flexibility and precision in joining dissimilar materials or complex geometries. By integrating laser welding with complementary techniques, manufacturers can achieve synergistic effects, further expanding the capabilities and applicability of metal joining processes. This convergence of technologies exemplifies the continuous innovation within the field of metal laser welding, driving advancements in engineering and manufacturing across diverse sectors.
Applications of Laser Welding Metals
The versatility and precision of laser welding metal have propelled its widespread adoption across an array of industries, revolutionizing the production of components and structures. In the automotive sector, laser welding metal plays a pivotal role in the fabrication of vehicle bodies, exhaust systems, fuel tanks, and various structural components. The ability to join dissimilar materials, such as aluminum and high-strength steel, with exceptional precision and strength has elevated the quality and performance of automotive assemblies, contributing to enhanced safety and fuel efficiency. Additionally, the seamless and aesthetically pleasing welds achieved through laser welding have become integral to the design and functionality of modern automotive designs, offering a perfect blend of form and function.
Aerospace applications also benefit significantly from laser welding metal, where the demand for lightweight yet durable components necessitates advanced joining techniques. Laser-welded assemblies are employed in aircraft structures, engine components, and intricate systems, providing the necessary strength and reliability required for aerospace operations. The precise control over weld parameters and the ability to weld complex geometries make metal laser welding indispensable in the aerospace industry, where safety, performance, and weight considerations are paramount.
The medical sector leverages laser welding metal for the fabrication of medical devices, implants, and surgical instruments, where biocompatibility, precision, and structural integrity are critical. The non-contact nature of laser welding minimizes the risk of contamination, ensuring the production of high-quality medical components that meet stringent regulatory standards.
Beyond automotive, aerospace, and medical applications, laser welding metal finds extensive use in consumer electronics, telecommunications, renewable energy, and various manufacturing sectors. From the production of electronic enclosures to the assembly of solar panels, the precision and efficiency of laser welding contribute to the seamless integration of components, enhancing product performance and longevity. The broad spectrum of applications underscores the versatility and impact of metal laser welding across diverse industries, solidifying its position as a transformative technology in the realm of precision engineering.
Factors to Consider in Laser Welding Metal
The successful implementation of laser welding metal hinges on a thorough consideration of various factors that influence the welding process and outcomes. Material properties, such as reflectivity, thermal conductivity, and melting point, play a crucial role in determining the feasibility and effectiveness of laser welding. Understanding the behavior of different materials under laser irradiation is essential for optimizing welding parameters and achieving robust welds. Joint design and fit-up are equally significant, as the geometry and alignment of the components directly impact the welding process and the integrity of the resulting joints. Proper preparation of the joint surfaces, including cleanliness and fitment, is imperative for ensuring successful laser welding and minimizing defects.
The selection of appropriate welding parameters, including laser power, pulse duration, focal spot size, and travel speed, demands meticulous attention to detail to ensure optimal weld quality and efficiency. The interplay of these parameters influences the depth of penetration, heat input, and microstructural characteristics of the weld, necessitating a comprehensive understanding of laser welding principles. Furthermore, the control of shielding gases and their flow rates is vital for protecting the weld pool and minimizing oxidation during the welding process. The establishment of an inert atmosphere around the weld area is essential for preserving the metallurgical integrity of the materials and preventing the formation of undesirable oxides.
Environmental considerations, such as fume extraction and ventilation, also warrant attention to maintain a safe and healthy work environment during metal laser welding operations. Adequate ventilation systems and proper personal protective equipment are integral to mitigating potential hazards associated with laser welding, ensuring the well-being of operators and personnel. Additionally, the assessment of post-weld treatments, such as stress relief annealing and surface finishing, contributes to the overall quality and performance of laser-welded components. These considerations collectively underscore the meticulous planning and execution required for successful metal laser welding, highlighting the technical expertise and attention to detail integral to this advanced joining technique.
Choosing the Right Metal Laser Welding Equipment
The selection of suitable metal laser welding equipment is a critical determinant of the overall welding performance and productivity. Key considerations when choosing laser welding systems include power capacity, beam delivery options, control interfaces, and automation capabilities. High-power laser sources offer increased versatility and the ability to weld a broader range of materials and thicknesses, making them suitable for demanding industrial applications. The flexibility of beam delivery options, such as fiber optics or articulated arms, impacts the accessibility and maneuverability of the laser beam, influencing the feasibility of welding complex geometries and hard-to-reach areas.
Intuitive control interfaces and software integration enhance the operability and precision of laser welding systems, allowing for seamless adjustment of welding parameters and real-time monitoring of the welding process. The integration of automation features, including robotic arms and CNC systems, facilitates the precise positioning of components and the execution of complex welding sequences, further streamlining production processes and ensuring consistent weld quality. Moreover, the availability of advanced monitoring and quality control systems, such as in-process imaging and weld inspection technologies, contributes to the assurance of weld integrity and the identification of potential defects, bolstering the reliability of laser-welded components.
The scalability and adaptability of laser welding equipment are essential considerations for accommodating future production requirements and expanding application possibilities. The ability to integrate additional functionalities, such as hybrid welding capabilities or multi-axis motion control, enhances the versatility and value proposition of laser welding systems, catering to evolving industry demands.
The availability of comprehensive training, technical support, and service networks from equipment suppliers is crucial for ensuring the proficiency and uptime of laser welding operations. The careful evaluation and selection of metal laser welding equipment based on these considerations are pivotal for achieving optimal welding results and maximizing the potential of this advanced joining technology.
Safety Precautions in Metal Laser Welding
Ensuring the safety of personnel and the integrity of equipment is paramount in metal laser welding operations. The high-power laser radiation emitted during welding poses potential hazards to operators and bystanders, necessitating the implementation of stringent safety measures. Adequate training and awareness programs are essential for educating personnel about the risks associated with laser welding and the proper use of personal protective equipment. The utilization of laser safety eyewear with appropriate optical density ratings is imperative for safeguarding against accidental exposure to laser radiation, protecting the eyes from potential injury.
The establishment of controlled access zones and the implementation of interlock systems on laser welding equipment contribute to the prevention of unauthorized exposure and the enforcement of safe operating practices. Additionally, the incorporation of beam enclosure and beam path monitoring systems mitigates the risk of unintended laser beam exposure, enhancing the overall safety of laser welding environments. Proper ventilation and fume extraction systems are instrumental in controlling airborne contaminants and maintaining air quality within the welding area, ensuring a healthy working environment for personnel.
Regular maintenance and inspection of laser welding equipment, including beam delivery components, protective enclosures, and safety interlocks, are essential for identifying and addressing potential hazards and maintaining compliance with safety standards. The adherence to established safety protocols and regulations, such as those outlined by regulatory bodies and industry standards organizations, is fundamental for fostering a culture of safety and responsibility in metal laser welding operations.
By prioritizing safety through comprehensive training, equipment safeguards, and adherence to best practices, organizations can create a secure and conducive environment for the application of metal laser welding, safeguarding the well-being of personnel and the integrity of production processes.
Comparing Laser Welding with Traditional Welding Methods
The comparison between metal laser welding and traditional welding methods reveals distinct advantages and considerations that differentiate these joining techniques. Conventional welding processes, such as arc welding and resistance welding, rely on the localized application of heat through electrical currents or gas flames to melt and fuse metal components. While these methods have been foundational in manufacturing for decades, they are often associated with limitations such as heat-affected zones, distortion, and slower welding speeds. In contrast, laser welding metal offers precise energy delivery, minimal heat-affected zones, and the ability to weld dissimilar materials with varying thicknesses, overcoming many of the constraints associated with traditional welding methods.
The non-contact nature of laser welding eliminates the need for physical contact between the welding tool and the workpiece, reducing the risk of contamination and damage to delicate materials. Moreover, the concentrated and coherent nature of the laser beam enables deep penetration and high welding speeds, contributing to increased productivity and efficiency compared to traditional welding methods. The ability to achieve fine and intricate welds with minimal distortion and post-weld cleanup further distinguishes metal laser welding as a superior choice for applications that demand precision and aesthetic appeal.
In terms of environmental impact, metal laser welding stands out for its minimal generation of fumes, reduced energy consumption, and the potential for automated and unmanned welding operations, aligning with sustainability and workplace safety objectives. Traditional welding methods, on the other hand, may produce significant emissions and require extensive manual labor, presenting challenges in meeting stringent environmental regulations and operational efficiency targets. While each welding method has its unique strengths and applications, the advancements and advantages offered by metal laser welding position it as a transformative and future-ready technology that continues to shape the landscape of modern manufacturing and engineering.
Training and Certification in Metal Laser Welding
The proficiency and competence of personnel engaged in metal laser welding are fundamental to ensuring the quality and integrity of welding operations. Comprehensive training programs that encompass theoretical knowledge, practical skills, and safety protocols are essential for equipping welders, technicians, and engineers with the expertise required for proficient laser welding. Training curricula should cover topics such as laser principles, material behavior, welding parameters, equipment operation, and troubleshooting, providing a holistic understanding of the intricacies of metal laser welding. Hands-on training with laser welding equipment and simulated welding scenarios allows participants to apply theoretical concepts and develop proficiency in executing welding tasks.
Certification programs that validate the skills and knowledge of individuals in metal laser welding serve as a
Conclusion
Laser welding metal is a reliable and cost effective way to join two pieces of metal. The process itself is not particularly complex once you understand the basics. The right machine for your job will depend on the type of materials you are joining and the desired results.