Sanitary tube welding is a critical aspect of many industrial processes, allowing for the safe and efficient transfer of fluids and gases between components. Welding sanitary tubes requires a specific set of skills, and when done correctly, can be an important part of the overall sanitary welding procedure. Mastering the art of sanitary tube welding can be a daunting task, but with the right knowledge and practice, it can be achieved.
This comprehensive guide provides a thorough overview of the process, from the basics of welding to the more complex techniques. With detailed illustrations and step-by-step instructions, readers will gain confidence and understanding of the entire sanitary welding procedure. By the end, readers will be able to confidently and safely weld sanitary tubes with assurance that the welds will stand up to the toughest of industrial conditions.
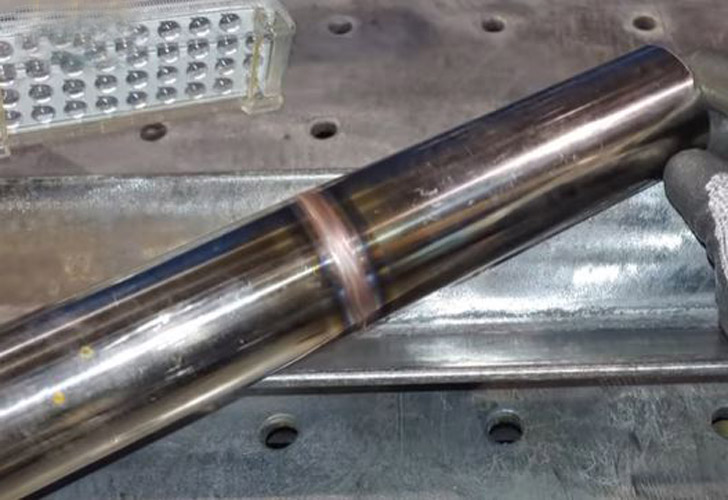
About Sanitary Tube Welding
Sanitary tube welding is the process of joining two components together using a gas-tight weld. These tubes are made of a variety of materials, including copper, aluminum, and steel. In some cases, other materials such as stainless steel, carbon steel, glass, and more may be used. The sanitary tube can be used to transfer liquids, gases, and even electricity. It is often used in the food and beverage industry, medical industry, oil and gas production, and more.
There are several different types of sanitary tubes with specific uses including low pressure, high pressure, oxygen, and nitrogen. Low pressure is used for the transfer of liquids such as water, oil, or even food products. High pressure is used for the transfer of gases such as oxygen or nitrogen. Oxygen is used to purify water or is used in medical equipment, while nitrogen is often used in the agricultural industry.
Safety and equipment for welding sanitary tubes
When welding sanitary tubes, it is critical to be safe and wear the appropriate equipment to protect the welder and the people and components being welded. Safety glasses or goggles should be worn to protect the eyes from debris and sparks. Gloves should be worn to protect the hands from burns and splatters. The welding equipment used should be gas-tight, and the welder’s workstation should be well-ventilated to reduce the risk of carbon monoxide and inhalation of fumes.
The equipment should also be equipped with a suitable shield to protect coworkers. Whenever welding on the line, it is also important to follow procedures to reduce the risk of accidents. The right equipment can also improve the quality of the weld. An electrode with a gap between the inner and outer electrodes can ensure a gas-tight weld with minimal heat loss and gassing. The length of the electrode used plays an important role in the weld quality too, with longer electrodes providing a better quality weld.
Geometry of welding sanitary tubes
The majority of welding processes require the use of a welding torch, which heats up an electrode to create a plasma arc. The arc then splashes out a stream of molten metal, which welds or bonds the two pieces together. The welding geometry of a torch plays an important role in the quality of the weld and the amount of heat generated. An understanding of the geometry of a weld can be used to modify welding geometry to improve the weld quality.
The two most common welding geometries are butt weld and fillet weld. Butt welds have the outer ring of the joint lined up with the torch’s nozzle, while fillet welds have the torch’s nozzle between the joint rings. The geometry of each weld can be changed to suit the desired weld geometry.
Sanitization and preparation of the welded joint
Before welding sanitary tubing, the joint to be welded is sanitized through the use of an insulator or a sacrificial sleeve. Both of these prepare the joint for welding and prevent contamination from the welding torch. After flushing, the joint has to be thoroughly dried and free of moisture. When sanitizing the joint, it is important to get rid of all impurities before welding. A joint with impurities will result in a poor weld.
The joint should also be properly prepared before welding with the right gaging and welding geometry. This will ensure the joint is ready for welding without defects or issues. The joint should be clean, dry, and well-gauged. The joint should also be properly prepped before welding with the right gaging and welding geometry.
Types of Sanitary Tubes
The type of sanitary tube used will depend on the application, the environment, and the intended use of the tubing. Low pressure sanitary tubes are ideal for the transfer of liquids like water or oil. These are typically made of nickel-plated brass with a polyethylene or polyvinyl chloride (PVC) sleeve. High pressure sanitary tubes are used for the transfer of gases like oxygen and nitrogen. These are typically made of stainless steel with an aluminum sheath.
Sanitary Welding Procedure
Sanitary tube welding is an advanced welding process and requires a thorough understanding of the welding process and geometry. The process of sanitary tube welding requires the same skills, equipment, and safety as other types of welding. This sanitary welding procedure can be a daunting task, but with the right knowledge and practice, it can be achieved. Before welding, the joint to be welded is thoroughly cleaned and properly prepared. The joint has to be thoroughly cleaned to remove all dust, debris, and dirt. The joint should then be flushed with clean water to remove any impurities.
After flushing, the joint has to be thoroughly dried and free of any moisture. The joint should also be well-gauged with the correct length of the welding torch. Sanitary tube welding can be done in a horizontal, vertical, or overhead position. The torch should be properly gaged and the joint should be properly prepared. Depending on the type of joint to be welded, the diameter of the sanitary tube may vary. The larger the diameter of the sanitary tube, the more difficult it is to weld.
Tips and tricks for welding sanitary tubing
- When welding with a stainless steel rod, it is important to oil the joint to reduce friction and heat loss.
- When welding sanitary tubing, it is important to keep your hands clean and free of grease, oil, or dirt.
- When welding, it is important to keep your work area clean and well-ventilated.
- When welding, important not to lean on the torch.
- When welding, it is important to use the correct torch geometry and continuously weld while the joint is still hot.
- When welding, it is important to rotate the joint and make multiple passe
- When welding, important to remove any major defects before welding again.
Summary
The welding geometry of these tubes can be modified to produce a variety of welds depending on the desired geometry. When welding sanitary tubing, it is important to be safe and wear the appropriate equipment to protect the welder and people being welded. This can be a daunting task, but with the right knowledge and practice, it can be achieved.