Are you a beginner in the world of welding and looking to try out flux core welding? You’ve come to the right place. In this article, we will provide you with valuable tips to help you get started with flux core welding and achieve outstanding results.
What is Flux Core Welding?
Flux core welding is a versatile and popular welding technique that utilizes a hollow wire electrode filled with flux. The flux acts as a shielding agent, protecting the weld from contamination and producing cleaner, stronger welds. Unlike other welding methods, flux core welding does not require the use of external shielding gas, making it more convenient and cost-effective.
Flux core welding is commonly used in various applications, including construction, automotive repairs, and metal fabrication. It is especially suitable for outdoor welding projects due to its ability to withstand windy conditions and provide excellent penetration.
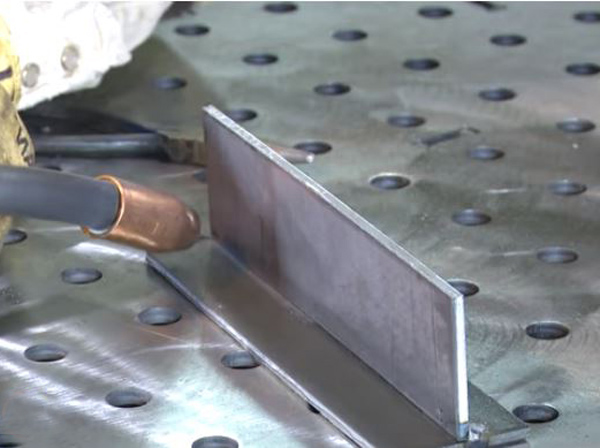
Advantages of Flux Core Welding
Flux core welding offers several advantages that make it an attractive choice for beginners and professionals alike. One of the main advantages is its versatility. Flux core welding can be used on a wide range of materials, including mild steel, stainless steel, and aluminum. This makes it a valuable skill for welders working in different industries.
Another advantage of flux core welding is its ease of use. Unlike some other welding methods, flux core welding does not require precise control over the welding environment. It can be performed in less than ideal conditions, such as windy or outdoor settings. This makes it a great option for DIY enthusiasts and hobbyists.
Flux core welding produces strong, durable welds with excellent penetration. The flux in the electrode helps to remove impurities from the weld, resulting in cleaner and stronger joints. This makes flux core welding suitable for structural applications where strength and reliability are crucial.
Flux Core Welding vs Other Welding Methods
While flux core welding offers many advantages, it’s important to understand its differences and limitations compared to other welding methods.
One key distinction is the absence of a separate shielding gas in flux core welding. Instead, the flux contained within the wire electrode vaporizes during the welding process, creating a protective shield around the weld. This eliminates the need for external shielding gas, making flux core welding more portable and cost-effective.
Another difference lies in the quality of the weld produced. Flux core welding tends to produce welds with more spatter compared to other methods, such as MIG welding. However, this can be mitigated with proper technique and adjustments to the welding parameters.
It’s also worth noting that flux core welding may not be suitable for all materials. While it is compatible with a wide range of metals, it may not provide the same level of precision and control as other methods like TIG welding. In such cases, it is important to consider the specific requirements of the project and choose the appropriate welding method accordingly.
Essential Equipment for Flux Core Welding
Before diving into flux core welding, it’s crucial to have the right equipment. Here are some essential tools and gear you will need to get started:
Welding Machine
Choose a flux core welding machine that is capable of welding. Look for a machine that offers adjustable voltage and wire feed speed settings to ensure precise control over the welding process.
Flux Core Wire
Select the appropriate flux core wire based on the material you will be welding. Different wires are designed for specific applications, so be sure to choose the right one for your project.
Welding Helmet
Invest in a high-quality welding helmet with an auto-darkening feature to protect your eyes from bright welding arcs. A good helmet should also provide sufficient face and neck coverage for maximum safety.
Welding Gloves
Opt for heavy-duty welding gloves that offer both heat resistance and dexterity. These gloves will protect your hands from sparks, heat, and potential burns.
Welding Jacket
Wear a flame-resistant welding jacket to protect your upper body from sparks, splatter, and UV radiation. It’s important to choose a jacket that fits well and covers your arms and torso adequately.
Welding Clamps
Use welding clamps to secure your workpiece in place, ensuring stability and accurate alignment during the welding process. This will help you achieve clean and precise welds.
Safety Precautions for Flux Core Welding
As with any welding process, safety should always be a top priority when practicing flux core welding. Here are some essential safety precautions to keep in mind:
Protective Clothing
Wear flame-resistant clothing, including a welding jacket, long pants, and steel-toed boots. Avoid loose-fitting clothing that may catch fire or get tangled in the welding equipment.
Eye and Face Protection
Use a welding helmet with a proper shade lens to protect your eyes and face from harmful UV radiation. Wear safety glasses with side shields to protect against flying debris and sparks.
Ventilation
Ensure proper ventilation in your workspace to minimize the inhalation of welding fumes and gases. If working indoors, consider using a fume extraction system or welding in a well-ventilated area.
Fire Safety
Keep a fire extinguisher or a bucket of sand nearby in case of any fire emergencies. Additionally, remove any flammable materials from your workspace to reduce the risk of fire.
Electrical Safety
Inspect your welding equipment regularly for any damaged cords or loose connections. Avoid standing on wet surfaces or touching the electrode with bare skin to prevent electric shock.
Remember, safety is paramount when it comes to welding. Always follow the manufacturer’s instructions for the proper use and maintenance of your welding equipment.
Flux Core Welding Techniques for Beginners
Now that you’re equipped with the necessary knowledge and safety precautions, let’s dive into some essential flux core welding techniques for beginners. These techniques will help you achieve strong and visually appealing welds:
Proper Welding Position
Position yourself comfortably and maintain a steady stance while welding. This will ensure better control and accuracy throughout the welding process. Experiment with different positions to find the one that works best for you.
Travel Speed
Maintain a consistent travel speed while welding to achieve even penetration and prevent excessive heat buildup. Too fast of a travel speed can lead to poor fusion, while too slow of a speed can result in excessive heat input and distortion.
Angle and Direction
Hold the welding gun at a slight angle of around 10-15 degrees in the direction of travel. This will help ensure proper fusion and prevent undercutting. Push the weld pool forward while maintaining a steady forward motion for smoother welds.
Stitch Welding
For long continuous welds, consider using the stitch welding technique. Instead of welding the entire length in one pass, divide it into shorter sections or stitches. This helps to prevent overheating and distortion, especially on thicker materials.
Cleanliness and Preparation
Properly clean and prepare the metal surfaces before welding. Remove any rust, paint, oil, or contaminants that may interfere with the welding process. A clean workpiece ensures better weld quality and reduces the risk of defects.
Remember, practice makes perfect. Take the time to experiment with different techniques and settings to find what works best for your specific welding needs.
Common Mistakes to Avoid in Flux Core Welding
While learning flux core welding, it’s common to encounter some challenges and make mistakes along the way. Here are some common mistakes to avoid:
Incorrect Wire Size and Type: Ensure you are using the correct wire size and type for the material you are welding. Using the wrong wire can lead to poor weld quality and increased spatter.
Improper Wire Feed Speed: Adjust the wire feed speed based on the thickness of the material and the welding parameters. Too high of a wire feed speed can lead to excessive spatter, while too low of a speed can result in incomplete fusion.
Inconsistent Travel Speed: Maintain a consistent travel speed throughout the welding process. Inconsistent travel speed can lead to uneven welds and poor fusion.
Neglecting Cleanliness: Clean the metal surfaces thoroughly before welding to remove any contaminants. Neglecting cleanliness can result in poor weld quality and increased spatter.
Lack of Proper Joint Preparation: Ensure proper joint preparation, including beveling or chamfering if required. Improper joint preparation can lead to poor fusion and weak welds.
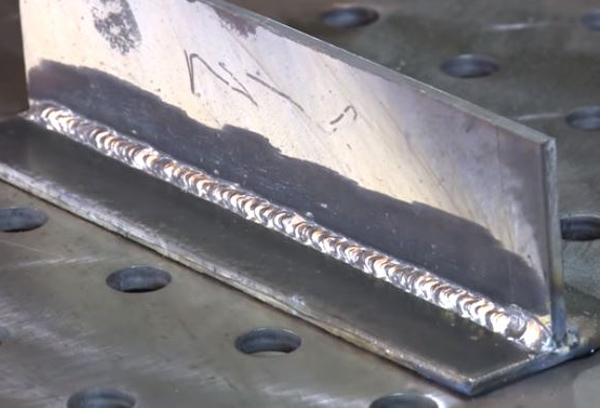
By avoiding these common mistakes, you will be well on your way to achieving high-quality welds with flux core welding.
Troubleshooting Common Issues in Flux Core Welding
Even with the best techniques and precautions, it’s possible to encounter some common issues while flux core welding. Here are some troubleshooting tips to help you overcome these challenges:
- Excessive Spatter: Excessive spatter can be reduced by adjusting the wire feed speed and voltage settings. Cleaning the workpiece thoroughly and using an anti-spatter spray can help minimize spatter.
- Porosity: Porosity, or the presence of small holes in the weld, can be caused by contaminated base metal or improper shielding. Ensure the base metal is clean and free from any contaminants, and adjust the shielding gas flow if necessary.
- Lack of Penetration: If you’re experiencing a lack of penetration, try increasing the voltage and wire feed speed. Additionally, ensure the joint is properly prepared and that the weld pool is adequately sized.
- Uneven Welds: Uneven welds can be caused by inconsistent travel speed or improper heat input. Maintain a steady travel speed and adjust the heat settings as needed to achieve even and uniform welds.
- Burn-Through: Burn-through occurs when the heat input is too high, causing the metal to melt through. To prevent burn-through, reduce the heat input by lowering the voltage and wire feed speed or using a smaller wire size.
Remember, troubleshooting requires patience and practice. Don’t be discouraged if you encounter issues along the way. Take the time to analyze and understand the root cause of the problem, and make the necessary adjustments to improve your welding technique.
Recommended Flux Core Welding Tips and Tricks
To further enhance your flux core welding skills, here are some additional tips and tricks:
Practice on Scrap Metal: Before tackling important projects, practice your welding skills on scrap metal to gain confidence and refine your technique.
Maintain Consistent Arc Length: Maintain a consistent arc length between the welding gun and the workpiece. This helps to ensure stable arc characteristics and better control over the welding process.
Use a Drag Technique: Consider using a drag technique, where the welding gun is dragged along the workpiece instead of pushing it. This can help improve visibility and control over the weld pool.
Experiment with Different Wire Types: Experiment with different types of flux core wires to find the one that suits your specific welding needs. Some wires offer better performance on certain materials or in specific welding positions.
Keep an Eye on Welding Parameters: Monitor and adjust the welding parameters, such as voltage, wire feed speed, and travel speed, to achieve optimal weld quality. Keep a record of the settings that work best for different materials and thicknesses.
By incorporating these tips and tricks into your welding practice, you’ll continuously improve your skills and achieve better results.
Conclusion and Next Steps for Beginners in Flux Core Welding
Congratulations! You have reached the end of this comprehensive guide on flux core welding tips for beginners. Armed with the knowledge of flux core welding techniques, safety precautions, troubleshooting, and expert recommendations, you are ready to embark on your journey as a skilled flux core welder.
Remember, practice is key to mastering any skill. Start with small projects and gradually work your way up to more complex tasks. With time and experience, you will become more proficient in flux core welding and unlock your potential as a skilled welder.
As you gain confidence, consider expanding your knowledge by exploring other welding techniques, such as MIG, TIG, or stick welding. Each method has its own unique advantages and applications, and being well-versed in multiple techniques will make you a more versatile and sought-after welder.
So, keep pushing your boundaries, honing your skills, and never stop learning. The world of welding is vast, and your potential is unlimited. Now go out there and create something amazing with flux core welding.