When it comes to precision and efficiency in manufacturing, robotic laser welding emerges as a game-changer. The fusion of robotic automation with laser welding technology has revolutionized the production processes across industries. This advanced method offers unparalleled accuracy and speed, ensuring impeccable welds on various materials with minimal heat distortion. In a world where time-to-market and quality are non-negotiable, robotic laser welding stands out as the epitome of innovation.
The seamless synergy between robotics and laser technology amplifies productivity while maintaining the highest standards of precision, making it a preferred choice in modern manufacturing setups.
Not only does it deliver immaculate welds, but it also reduces material waste and operational costs, elevating the overall efficiency of the production line. Join us as we delve into the transformative prowess of robotic laser welding, understanding its versatile applications, and unraveling the myriad benefits it offers to industries worldwide.
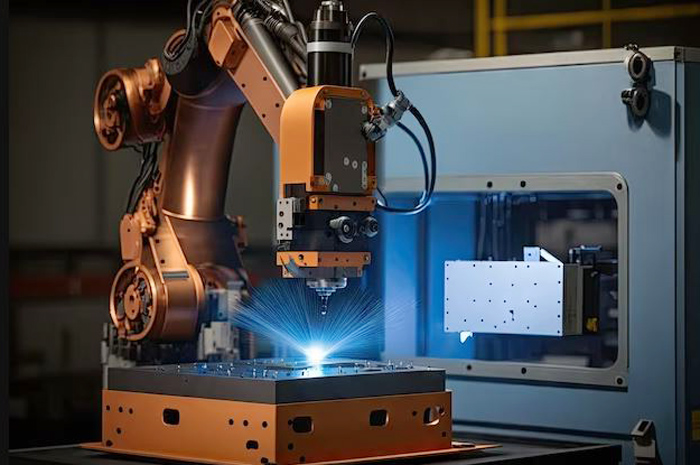
Image Source: FreeImages‍
Advantages of Robotic Laser Welding
Robotic laser welding offers a multitude of advantages that set it apart from traditional welding methods. Firstly, the precision achieved through robotic laser welding is unparalleled, ensuring uniform, high-quality welds with minimal room for error. The speed of the process is also a significant advantage, as robotic systems can perform complex welds at a fraction of the time it would take a human operator.
The heat-affected zone is minimized, reducing the risk of material distortion and ensuring the integrity of the welded components. Robotic laser welding is highly versatile, capable of welding a wide range of materials, from thin sheets to thick components, making it a go-to solution for diverse manufacturing needs.
Applications of Robotic Laser Welding
The applications of robotic laser welding span across numerous industries, including automotive, aerospace, electronics, medical devices, and more. In the automotive sector, robotic laser welding is used for joining components in car bodies, exhaust systems, and various structural elements, ensuring the structural integrity and durability of the vehicles. In aerospace, the precision and reliability of robotic laser welding are leveraged for joining critical components of aircraft, such as turbine blades, engine components, and fuel systems, where the highest standards of quality and performance are mandatory.
The electronics industry benefits from the clean and precise welds achieved through robotic laser welding, particularly in the production of consumer electronics, circuit boards, and intricate components. The medical device industry also relies on robotic laser welding for creating intricate and sterile welds in devices such as surgical instruments and implantable medical components.
How Robotic Laser Welding Works
Robotic laser welding operates through the precise coordination of a robotic arm and a high-powered laser beam. The robotic arm holds and positions the workpiece while the laser beam delivers concentrated heat to the welding area, causing the materials to fuse together. The process is meticulously controlled, ensuring consistent weld quality and accuracy.
The use of robotics allows for intricate and complex welding patterns to be executed with ease, while the laser technology ensures minimal heat input and distortion, resulting in clean and durable welds. The entire process is meticulously programmed and monitored, ensuring the highest level of repeatability and precision.
Factors to Consider for Robotic Laser Welding
Before integrating robotic laser welding into a manufacturing process, several factors need to be considered to ensure optimal performance. The material type and thickness play a crucial role in determining the suitability of robotic laser welding, as different materials may require specific laser parameters and techniques. The design and geometry of the components to be welded must be evaluated to ensure that the robotic system can access and weld all required areas.
Furthermore, considerations such as joint accessibility, fixturing, and part positioning should be taken into account to optimize the welding process. It’s also essential to assess the production volume and required weld quality to determine the most suitable robotic laser welding setup for the specific manufacturing needs.
Robotic Laser Welding vs Traditional Welding Methods
In comparison to traditional welding methods such as MIG or TIG welding, robotic laser welding offers distinct advantages. Traditional welding methods often involve manual labor, which can be time-consuming and susceptible to human error. Robotic laser welding, on the other hand, leverages automation to execute precise welds consistently and at a much faster rate.
The heat input in traditional welding methods can lead to material distortion and a larger heat-affected zone, whereas robotic laser welding minimizes these effects, resulting in cleaner and stronger welds. Additionally, the versatility of robotic laser welding allows for seamless adaptation to various materials and component geometries, offering a level of flexibility that traditional welding methods may struggle to match.
Industries Using Robotic Laser Welding
The utilization of robotic laser welding extends across a wide spectrum of industries, each leveraging its capabilities to enhance their manufacturing processes. In the automotive industry, robotic laser welding is employed for joining body panels, exhaust systems, and chassis components, ensuring structural integrity and durability. The aerospace sector relies on robotic laser welding for critical applications such as joining turbine components, fuel systems, and aircraft structural elements, where precision and reliability are paramount.
The electronics industry benefits from the clean and precise welds achieved through robotic laser welding, particularly in the production of consumer electronics, circuit boards, and intricate components, ensuring the integrity and functionality of electronic devices. The medical device industry also leverages robotic laser welding for creating intricate and sterile welds in devices such as surgical instruments and implantable medical components, meeting the stringent quality and safety standards of the healthcare sector.
Robotic Laser Welding Training and Certification
As the demand for robotic laser welding continues to rise, the need for skilled professionals proficient in operating and maintaining robotic welding systems becomes increasingly critical. Training and certification programs in robotic laser welding equip individuals with the knowledge and expertise to operate robotic welding systems, understand laser parameters, and ensure the quality and integrity of welded components.
These programs cover essential topics such as robotic programming, laser technology fundamentals, welding techniques, and safety protocols, providing participants with a comprehensive understanding of robotic laser welding processes and best practices. Certification in robotic laser welding not only validates the skills and competence of individuals but also assures employers of their ability to contribute to efficient and high-quality manufacturing processes.
Robotic Laser Welding Equipment and Technology
The equipment and technology utilized in robotic laser welding are crucial components that contribute to its efficiency and precision. High-powered industrial lasers, such as fiber lasers or CO2 lasers, are integral to the process, delivering the intense energy required for welding various materials. Robotic arms equipped with advanced sensors and precision controls ensure accurate positioning and movement, allowing for intricate and complex weld patterns to be executed with precision.
Additionally, vision systems and monitoring equipment play a vital role in ensuring the quality and consistency of the welds, providing real-time feedback and enabling adjustments to optimize the welding process. The integration of advanced software and controls further enhances the capabilities of robotic laser welding systems, enabling seamless programming, monitoring, and maintenance of the entire welding process.
Final Thoughts
Robotic laser welding stands at the forefront of modern manufacturing, offering unparalleled precision, speed, and versatility. Its transformative impact spans across industries, revolutionizing the way components and structures are joined, while elevating the standards of quality and efficiency. As the demand for immaculate welds and streamlined production processes continues to soar, robotic laser welding remains a cornerstone of innovation, driving advancements in manufacturing and engineering.
The seamless integration of robotic automation with laser technology has not only redefined the possibilities of welding but has also set new benchmarks for precision manufacturing. With its myriad benefits and diverse applications, robotic laser welding solidifies its position as a pivotal force in shaping the future of manufacturing across the globe.
In conclusion, the boundless potential of robotic laser welding continues to unfold, offering a glimpse into the future of precision manufacturing, where impeccable welds and unparalleled efficiency converge to redefine the boundaries of possibility.