New to MIG welding? Don’t worry, you are in the right place. Mastering MIG welding takes time, but with the right MIG welding tips and tricks, you can expedite the learning process and hone your skills faster. Whether you are a DIY enthusiast or looking to kickstart a career in welding, understanding the nuances of MIG welding is essential. In this comprehensive guide, we will walk you through practical tips and expert techniques that will help you achieve clean, strong welds and avoid common pitfalls.
From choosing the right equipment to mastering welding techniques, we’ve got you covered. By the time you finish reading, you will be ready to tackle your first MIG welding project with confidence. So, grab your helmet and let’s dive into the world of MIG welding mastery.
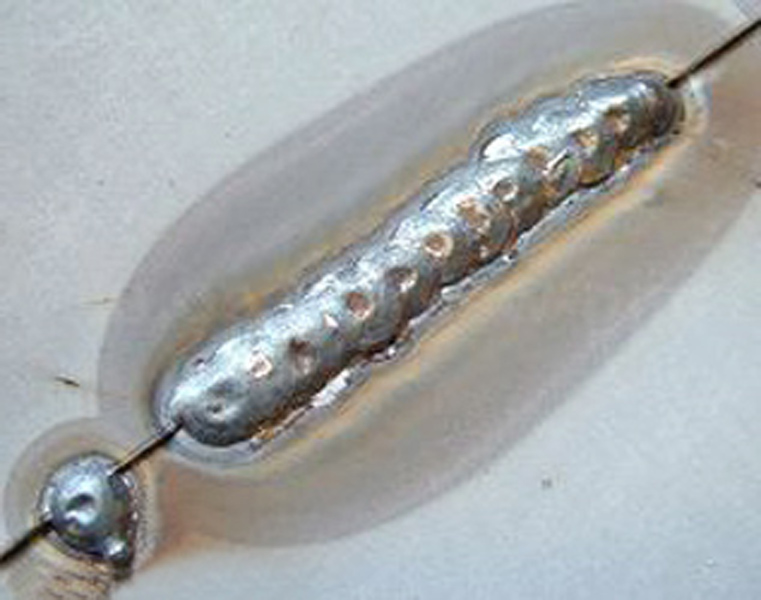
What is MIG welding?
MIG welding, or Metal Inert Gas welding, is a versatile and relatively easy welding process that uses a continuously feeding wire electrode and an inert gas to join two pieces of metal. The process is commonly used in automotive, construction, and manufacturing industries due to its efficiency and ability to produce clean welds. MIG welding is known for its speed and ease of use, making it an excellent choice for beginners and professionals alike.
MIG welding works by creating an electrical circuit between the workpiece and the wire electrode, causing the wire to melt and form a weld pool. The inert gas, typically argon or a mixture of argon and carbon dioxide, is used to shield the weld pool from atmospheric contaminants, ensuring a clean and strong weld. Understanding the basics of how MIG welding works is crucial for anyone looking to master this welding technique.
To get started with MIG welding, it’s essential to familiarize yourself with the equipment and safety precautions necessary for a successful welding experience. Let’s dive into the essential equipment for MIG welding.
Essential equipment for MIG welding
Before diving into MIG welding, it’s crucial to have the right equipment in place to ensure a smooth and efficient welding process. The essential equipment for MIG welding includes a MIG welder, welding gun, wire electrode, shielding gas, welding helmet, gloves, and protective clothing. Investing in high-quality equipment will not only improve the quality of your welds but also ensure your safety during the welding process.
A MIG welder, also known as a wire welder, is the core equipment used in MIG welding. It consists of a power source, wire feeder, and welding gun, all of which work together to create the electric arc needed for welding. When selecting a MIG welder, consider factors such as amperage range, duty cycle, and input power requirements to ensure it meets your specific welding needs.
In addition to the MIG welder, a welding gun and wire electrode are essential components for MIG welding. The welding gun is used to control the wire feed and direct the shielding gas, while the wire electrode, typically made of steel or aluminum, serves as the filler material for creating the weld. Choosing the right wire electrode for your welding project is crucial for achieving strong and clean welds.
Once you have the necessary equipment in place, it’s important to prioritize safety precautions to protect yourself and others during the welding process. Let’s explore the essential safety precautions for MIG welding.
Safety precautions for MIG welding
Safety should always be the top priority when engaging in any welding activity, including MIG welding. To ensure a safe and secure welding environment, it’s important to follow proper safety precautions and use personal protective equipment (PPE) at all times. This includes wearing a welding helmet with a proper auto-darkening lens, flame-resistant clothing, welding gloves, and safety glasses.
In addition to personal protective equipment, it’s crucial to work in a well-ventilated area to prevent exposure to welding fumes and gases. Proper ventilation helps maintain air quality and reduces the risk of inhaling harmful substances produced during the welding process. If welding indoors, consider using a welding fume extractor or positioning fans to ensure adequate ventilation.
It’s important to be mindful of potential fire hazards when MIG welding. Keep a fire extinguisher within reach and clear the work area of any flammable materials or debris. Ensure that the workpiece is securely grounded to prevent electrical shock and maintain a safe welding environment. By prioritizing safety precautions, you can minimize risks and focus on achieving quality welds. Now that we have covered safety precautions, let’s move on to setting up your MIG welder.
MIG welding settings and Tips
Properly setting up your MIG welder is essential for achieving consistent and high-quality welds. Start by selecting the appropriate wire electrode and shielding gas based on the type of metal you’ll be welding. For example, mild steel typically requires a mix of 75% argon and 25% carbon dioxide, while stainless steel may require pure argon gas.
Adjust the wire feed speed and voltage settings on your MIG welder to match the thickness of the metal you’re welding. Refer to the welder’s manual or welding parameter chart for recommended settings based on the material thickness. Fine-tuning these settings will help you create a stable arc and achieve proper penetration during the welding process.
Once the welder settings are dialed in, ensure that the welding gun and wire feed mechanism are properly assembled and in good working condition. Check for any signs of wear or damage and replace any worn components to prevent interruptions during welding. Proper setup of your MIG welder is essential for achieving consistent and quality welds. Now that your welder is set up, let’s explore techniques for achieving quality MIG welds.
Mig Welding Techniques for achieving quality welds
MIG welding requires a combination of proper technique, hand positioning, and steady welding motion. Begin by practicing proper gun angle and travel speed to achieve a consistent weld bead. The ideal gun angle is typically between 5 to 15 degrees, with a slight drag angle to ensure proper shielding gas coverage.
Maintain a steady travel speed, moving the welding gun in a straight line along the weld joint to create a uniform bead. Avoid pausing or hesitating during the welding process to prevent excessive heat buildup and potential burn-through. Practice these techniques on scrap metal to build confidence and refine your welding skills before tackling actual projects.
In addition to proper mig welding techniques, mastering the manipulation of the welding gun and controlling the wire feed is essential for achieving clean and strong welds. Experiment with different hand positions and gun movements to find the most comfortable and effective technique for your welding style. By honing your mig welding techniques, you can produce professional-looking welds with minimal spatter and distortion.
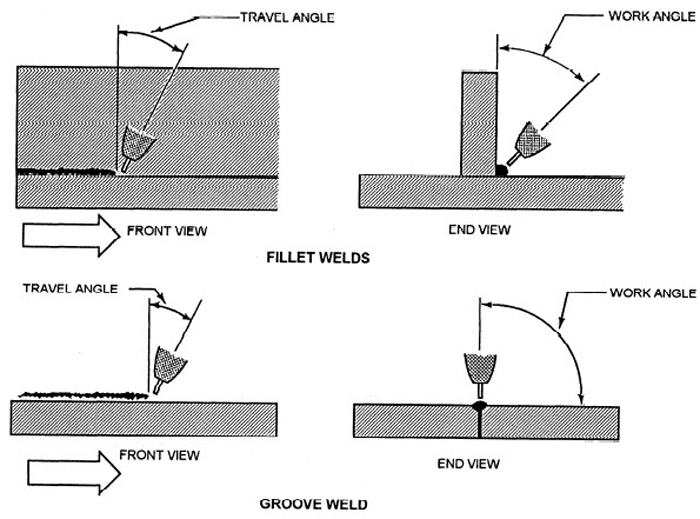
Common mistakes to avoid in MIG welding
MIG welding, like any skill, comes with its fair share of challenges and common mistakes. One of the most common mistakes in MIG welding is improper gun angle and travel speed, leading to inconsistent weld beads and poor penetration. To avoid this, practice maintaining a consistent gun angle and steady travel speed to produce uniform and strong welds.
Another common mistake is using the wrong wire electrode or shielding gas for the type of metal being welded. Always match the wire electrode and shielding gas to the specific metal to achieve optimal weld quality. Overlooking proper surface preparation, such as cleaning and removing rust or paint from the workpiece, can lead to contamination and weaken the weld.
Inadequate heat control and improper welder settings can result in incomplete fusion and weak welds. Take the time to fine-tune your welder settings and monitor the heat input to ensure proper penetration and fusion. By understanding and avoiding these common mistakes, you can elevate your MIG welding skills and produce professional-grade welds. Now that we’ve covered common mistakes, let’s move on to proper maintenance of MIG welding equipment.
Proper maintenance of MIG welding equipment
Maintaining your MIG welding equipment is crucial for ensuring consistent performance and extending the lifespan of your welding gear. Start by regularly inspecting and cleaning the welding gun, wire feed mechanism, and contact tips to remove any debris or spatter buildup. This helps prevent interruptions and ensures smooth wire feeding during welding.
In addition to cleaning, periodically check the condition of the wire electrode and replace it if it shows signs of wear or rust. Proper storage of the wire electrode in a dry and clean environment is essential for preventing contamination and maintaining its integrity. Regularly inspect the gas regulator and hoses to detect any leaks or damage, and replace any faulty components to maintain a consistent gas flow.
Lastly, perform routine maintenance on the MIG welder itself by checking for loose connections, inspecting the power source, and ensuring proper grounding. Following a proactive maintenance routine will not only prolong the life of your MIG welding equipment but also minimize the risk of welding defects and inconsistencies. Now that we’ve covered equipment maintenance, let’s explore advancing your skills through MIG welding projects.
Advancing your skills through MIG welding projects
One of the best ways to refine your MIG welding skills is by taking on a variety of welding projects that challenge and expand your abilities. Start with simple projects, such as welding two pieces of metal together to form a strong bond, and gradually progress to more complex tasks, such as fabricating metal structures or creating intricate weld patterns.
Consider experimenting with different types of metals and thicknesses to broaden your welding capabilities and gain experience with various welding techniques. Whether it’s automotive repairs, custom metal artwork, or structural welding, each project presents an opportunity to apply and refine your MIG welding skills.
Seek out welding mentors or join welding communities to gain insights and learn from experienced welders. Embracing new challenges and continuously pushing the boundaries of your welding abilities will ultimately lead to mastery and confidence in your MIG welding skills. Now that we’ve discussed advancing your skills, let’s move on to troubleshooting common issues in MIG welding.
Troubleshooting common issues in MIG welding
Despite your best efforts, you may encounter occasional issues or challenges during the MIG welding process. One common issue is excessive spatter, which can result from high welding currents, improper wire feed speed, or using the wrong gas mixture. To reduce spatter, fine-tune your welding parameters and ensure proper shielding gas coverage.
Another common issue is weld porosity, characterized by the presence of small cavities or holes in the weld bead. Weld porosity can occur due to inadequate gas shielding, contaminated base metal, or excessive moisture in the shielding gas. To address this issue, inspect and improve gas coverage, clean the workpiece thoroughly, and monitor the quality of your shielding gas.
Additionally, inconsistent weld penetration or lack of fusion may arise from improper heat input and inadequate welding techniques. Fine-tune your welder settings, practice proper welding techniques, and conduct thorough inspections of your welds to identify and address any penetration issues. By troubleshooting common welding issues, you can enhance your problem-solving skills and ensure the quality of your welds. Now that we’ve covered troubleshooting, let’s conclude with a summary and resources for further learning.
Conclusion and resources for further learning
MIG welding requires a combination of technical knowledge, proper equipment, and hands-on experience. By understanding the fundamentals of MIG welding, prioritizing safety precautions, and honing your welding techniques, you can achieve clean, strong welds and elevate your welding skills. Remember to invest in high-quality equipment, maintain a proactive maintenance routine, and continuously challenge yourself with new welding projects to advance your skills.
For further learning and exploration, consider enrolling in welding courses, attending workshops, or seeking guidance from experienced welders. Online resources, welding forums, and instructional videos can also provide valuable insights and tips for enhancing your MIG welding proficiency. Embrace the learning process, stay curious, and never stop refining your craft. With dedication and practice, you’ll soon become a proficient MIG welder ready to take on a wide range of welding challenges.
MIG welding presents an exciting journey for beginners, offering a versatile and accessible entry point into the world of welding. By following the tips and techniques outlined in this guide, you will be well-equipped to embark on your MIG welding endeavors with confidence and enthusiasm. So, put your newfound knowledge to the test, embrace the sparks, and let your welding skills shine. Happy welding!