When it comes to welding thin metal, there are several challenges that you need to be aware of. One of the main challenges is the tendency for thin metal to warp during the welding process. This is because thin metal has less structural integrity compared to thicker materials, making it more susceptible to distortion. To prevent warping, it’s important to use proper welding techniques and avoid excessive heat input. Another challenge when welding thin metal is the potential for burn-through. Burn-through occurs when the heat input is too high, causing the metal to melt and create holes. To avoid burn-through, it’s crucial to use the appropriate welding settings and control the heat input.
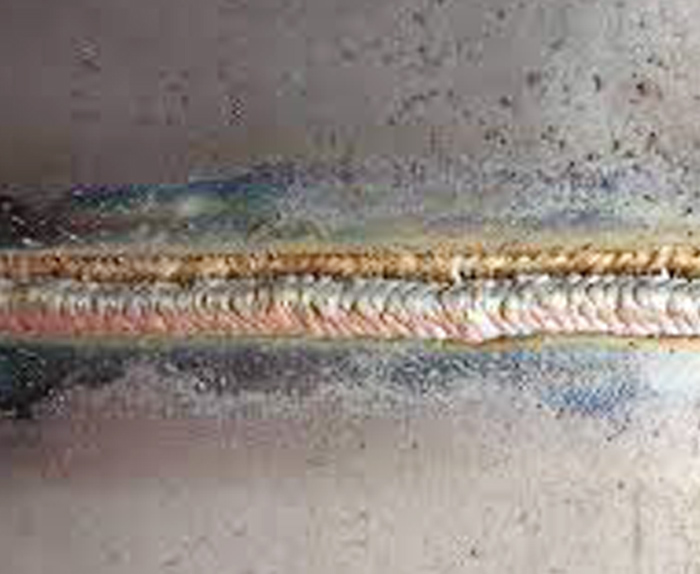
Photos by reddit
Thin metal is more prone to distortion caused by the welding process. This can result in an uneven and unattractive weld. To minimize distortion, it’s important to use tack welds and distribute the heat evenly across the metal. By understanding these challenges, you can take the necessary precautions and adjust your welding technique to achieve clean and strong welds on thin metal.
Safety precautions for MIG welding thin metal
Before diving into MIG welding thin metal, it’s important to prioritize safety. Here are some safety precautions you should always follow:
- Wear protective gear: This includes a welding helmet with a proper shade, welding gloves, flame-resistant clothing, and safety glasses.
- Ensure proper ventilation: MIG welding produces harmful fumes and gases, so make sure you work in a well-ventilated area or use exhaust fans to remove the fumes.
- Use a welding curtain: Set up a welding curtain or screen to protect yourself and others from the intense light and sparks.
- Keep a fire extinguisher nearby: Accidents can happen, so it’s essential to have a fire extinguisher within reach in case of emergencies.
- Inspect your equipment: Regularly check your welding machine, cables, and gas supply to ensure they are in good working condition.
By following these safety precautions, you can protect yourself and create a safe working environment while MIG welding thin metal.
Choosing the right MIG welding machine for thin metal
When it comes to MIG welding thin metal, selecting the right welding machine is crucial. Here are some factors to consider:
- Amperage range: Look for a welding machine that offers a wide amperage range, as this will allow you to adjust the heat input according to the thickness of the metal.
- Wire feed speed control: Opt for a machine that provides precise control over the wire feed speed. This will enable you to fine-tune the welding process and achieve better results on thin metal.
- Pulse welding feature: Some advanced MIG welding machines offer a pulse welding feature, which can be beneficial when welding thin metal. This feature allows for better control of the heat input and reduces the chances of burn-through.
- Portability: Consider the portability of the welding machine, especially if you work on different job sites. Look for a lightweight and compact machine that is easy to transport.
By choosing the right MIG welding machine, you can ensure that you have the necessary tools to weld thin metal effectively.
Selecting the appropriate wire and gas for thin metal welding
When it comes to MIG welding thin metal, selecting the right wire and gas combination is crucial for achieving clean and strong welds. Here are some considerations to keep in mind:
- Wire diameter: Use a thin wire diameter that matches the thickness of the metal. Thinner wires, such as 0.023 or 0.030 inches, are ideal for welding thin metal.
- Wire material: For general-purpose welding on thin metal, ER70S-6 carbon steel wire is commonly used. However, if you’re working with stainless steel or aluminum, make sure to choose the appropriate wire material.
- Gas selection: The choice of shielding gas depends on the type of metal you’re welding. For carbon steel, a mixture of 75% argon and 25% carbon dioxide (CO2) is commonly used. For stainless steel, a mixture of 98% argon and 2% carbon dioxide or helium is recommended. Aluminum welding typically requires pure argon.
By selecting the appropriate wire and gas combination, you can optimize the welding process and achieve high-quality welds on thin metal.
Preparing the thin metal for welding
Proper preparation of the thin metal is essential for achieving successful welds. Here are some steps to follow:
- Clean the metal: Remove any dirt, rust, or paint from the surface of the metal using a wire brush or sandpaper. This will ensure good weld penetration and reduce the chances of contamination.
- Bevel the edges: If the metal thickness allows, consider beveling the edges before welding. Beveling creates a V-shaped groove, which increases the weld’s surface area and improves penetration.
- Clamp the metal: Secure the thin metal in place using clamps or magnetic welding jigs. This will prevent the metal from moving during the welding process and help maintain alignment.
Taking the time to properly prepare the thin metal will result in cleaner and stronger welds.
Techniques for MIG welding thin metal
When it comes to MIG welding thin metal, employing the right techniques is crucial. Here are some techniques to consider:
- Use a lower heat setting: Adjust the heat input to a lower setting to prevent excessive heat buildup and reduce the chances of burn-through or warping.
- Employ a stitch welding technique: Instead of continuously welding along the entire seam, use a stitch welding technique. This involves welding short sections at a time, allowing the metal to cool between welds and minimizing distortion.
- Move quickly: When welding thin metal, it’s important to move quickly to avoid excessive heat buildup. Maintain a steady welding speed and keep the arc length consistent.
- Employ a backstep technique: Instead of welding in a straight line, consider using a backstep technique. This involves welding in a backward motion, which helps control the heat input and reduces the chances of burn-through.
By employing these techniques, you can achieve precise and controlled welds on thin metal.
Common mistakes to avoid when welding thin metal
When MIG welding thin metal, it’s important to avoid common mistakes that can compromise the quality of the welds. Here are some mistakes to watch out for:
- Excessive heat input: Using too much heat can result in burn-through, warping, and distortion. Always start with a lower heat setting and gradually increase if necessary.
- Insufficient cleaning: Failing to remove dirt, rust, or paint from the metal surface can lead to poor weld penetration and contamination. Ensure the metal is clean before welding.
- Inconsistent welding speed: Welding too slowly or too quickly can affect the quality of the weld. Maintain a steady welding speed and adjust it according to the thickness of the metal.
- Poor joint fit-up: Inadequate joint preparation can result in weak welds. Take the time to properly fit and align the metal pieces before welding.
By avoiding these common mistakes, you can ensure that your welds on thin metal are strong and reliable.
Tips for achieving strong and clean welds on thin metal
To achieve strong and clean welds on thin metal, consider the following tips:
- Practice on scrap metal: Before working on your actual project, practice welding on scrap metal of similar thickness. This will help you fine-tune your technique and ensure better results.
- Use a push technique: When MIG welding thin metal, use a push technique instead of a pull technique. This involves pushing the welding gun away from the weld pool, which helps control the heat input and reduces the chances of burn-through.
- Use tack welds: Instead of continuously welding along the entire seam, use tack welds to hold the metal pieces together. Tack welds act as temporary supports and help maintain alignment.
- Keep the travel angle consistent: Maintain a consistent travel angle, typically around 15 to 20 degrees, throughout the welding process. This will ensure even heat distribution and improve weld quality.
By implementing these tips, you can achieve strong and clean welds on thin metal, even as a beginner.
Conclusion and final thoughts
MIG welding thin metal requires precision, finesse, and attention to detail. By understanding the challenges, following safety precautions, choosing the right equipment, and employing the appropriate techniques, you can achieve clean and strong welds on thin materials.
Remember to prioritize safety by wearing protective gear, ensuring proper ventilation, and inspecting your equipment regularly. Choose a MIG welding machine that offers a wide amperage range, precise wire feed speed control, and portability. Select the appropriate wire and gas combination based on the type of metal you are welding. Prepare the thin metal by cleaning the surface and considering beveling if needed.