MIG welding, also known as Gas Metal Arc Welding (GMAW), is a popular welding process that utilizes a consumable wire electrode and a shielding gas to join metal. When it comes to welding square tubing, MIG welding offers several advantages, including speed, versatility, and ease of use. Square tubing, characterized by its four equal sides, is commonly used in various fabrication projects, making it essential to master the art of MIG welding for this specific application.
MIG welding square tubing requires a deep understanding of the welding process and the specific techniques needed to achieve strong, clean welds. By familiarizing yourself with the intricacies of both MIG welding and square tubing, you can elevate your welding skills and produce high-quality, professional-grade results.
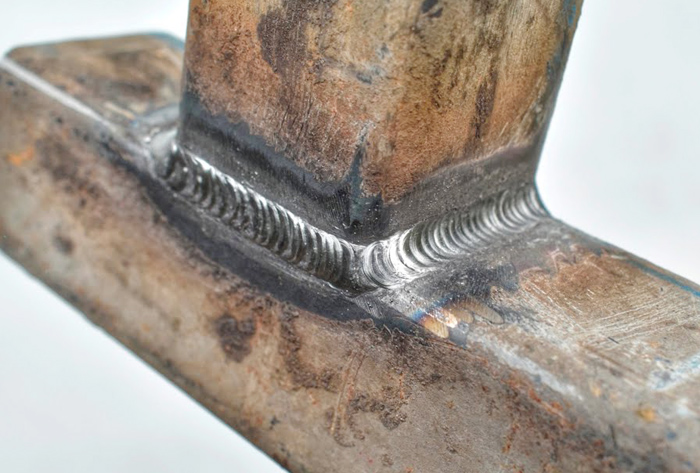
Photos: weld_d on YT
Advantages of Mig Welding Square Tubing
One of the key advantages of MIG welding square tubing is its efficiency and speed. The continuous wire feed and the ability to weld in various positions make MIG welding well-suited for square tubing, allowing for faster production and increased productivity. MIG welding provides excellent control over the welding process, enabling welders to achieve precise and consistent welds on square tubing with minimal spatter.
Moreover, MIG welding offers versatility in terms of the types of materials that can be welded, making it suitable for a wide range of square tubing applications. Whether you are working with mild steel, stainless steel, or aluminum square tubing, MIG welding provides the flexibility to weld different materials effectively, expanding the possibilities for your welding projects.
Mig Welding Square Tubing Techniques
When it comes to MIG welding square tubing, mastering the essential techniques is crucial for achieving optimal results. Start by preparing the square tubing, ensuring that the surfaces are clean and free from any contaminants that could compromise the weld quality. Proper preparation sets the foundation for successful MIG welding and contributes to the overall strength and integrity of the welds.
Next, selecting the appropriate welding wire is essential for MIG welding square tubing. The type and diameter of the welding wire should be compatible with the material of the square tubing and the welding parameters. Choosing the right welding wire ensures proper fusion and penetration, leading to strong and durable welds.
Proper manipulation of the welding gun and maintaining the correct welding angles are also critical techniques to master when MIG welding square tubing. Consistent travel speed, angle, and distance from the workpiece contribute to the overall weld appearance and quality. By honing these techniques, you can achieve smooth, uniform weld beads on square tubing, enhancing both the aesthetics and structural integrity of the welds.
Safety Measures for Mig Welding Square Tubing
Safety should always be a top priority when MIG welding square tubing. As with any welding process, it’s essential to adhere to safety precautions to protect yourself and others in the work environment. Ensure adequate ventilation to prevent the accumulation of welding fumes and gases, and wear appropriate personal protective equipment, including a welding helmet, gloves, and protective clothing.
Be mindful of the potential hazards associated with MIG welding, such as electrical shock, arc radiation, and molten metal splatter. Implementing proper grounding, using welding screens or curtains to contain sparks, and establishing a designated welding area can mitigate these risks and create a safer working environment for MIG welding square tubing. Prioritizing safety measures not only safeguards your well-being but also contributes to the overall quality and efficiency of the welding process.
Choosing the Right Mig Welding Machine for Square Tubing
Selecting the right MIG welding machine is paramount for achieving successful welds on square tubing. Consider factors such as the power source, amperage range, and welding output capabilities when choosing a MIG welder for square tubing applications. A suitable MIG welding machine should offer sufficient power and control to accommodate the specific requirements of welding square tubing, ensuring consistent and reliable performance.
Furthermore, the welding machine’s compatibility with different welding processes, such as pulse MIG welding, can enhance the versatility and precision of welding square tubing. Evaluate the features and capabilities of various MIG welding machines to identify the optimal equipment that aligns with your square tubing welding needs, ultimately contributing to the overall efficiency and quality of the welding process.
Common Mistakes to Avoid in Mig Welding Square Tubing
While mastering MIG welding square tubing, it’s essential to be aware of common mistakes that can compromise the weld quality and overall integrity of the workpiece. One prevalent mistake is inadequate surface preparation, which can lead to poor weld penetration and weak joints. Ensure thorough cleaning and proper fit-up of the square tubing to prevent these issues and promote solid weld fusion.
Another common mistake is improper wire feed and voltage settings, which can result in inconsistent weld beads and incomplete fusion. Understanding the optimal welding parameters for square tubing, including wire feed speed, voltage, and shielding gas flow rates, is crucial for achieving uniform and robust welds. By avoiding these common pitfalls and maintaining precision throughout the welding process, you can elevate the quality and durability of MIG welding on square tubing.
Tips for Achieving Strong and Clean Welds
To achieve strong and clean welds when MIG welding square tubing, consider implementing the following tips to optimize your welding technique and overall welding performance. First, focus on maintaining a steady travel speed and consistent torch manipulation to produce even and uniform weld beads along the length of the square tubing. This attention to detail contributes to the visual appeal and structural integrity of the welds.
Adjusting the welding parameters to match the specific characteristics of the square tubing material, such as thickness and alloy composition, can enhance the weld penetration and overall weld quality. By fine-tuning the welding settings, including voltage, wire feed speed, and shielding gas composition, you can tailor the welding process to the unique requirements of square tubing, resulting in stronger and more resilient welds.
Practicing proper weld bead placement and reinforcement techniques, such as weave patterns and multi-pass welding, can further strengthen the weld joints and improve the overall durability of the welded square tubing. By incorporating these tips into your MIG welding approach, you can elevate the quality and appearance of your welds, achieving superior results with square tubing applications.
Best Practices for Mig Welding Square Tubing
Incorporating best practices into your MIG welding process is essential for consistently producing high-quality welds on square tubing. Start by ensuring a stable and secure workpiece setup, which promotes precise torch positioning and minimizes potential distortion during the welding process. Proper clamping and alignment of the square tubing contribute to the accuracy and integrity of the welds.
Moreover, maintaining a clean and organized work environment, free from clutter and debris, enhances the efficiency and safety of MIG welding square tubing. Clearing the work area of any obstacles and establishing a systematic workflow streamlines the welding process and reduces the likelihood of errors or safety hazards.
Conducting thorough inspections and quality checks throughout the welding process, including post-weld visual examinations and non-destructive testing methods, ensures that the welded square tubing meets the required standards and specifications. By adhering to best practices and implementing rigorous quality control measures, you can consistently deliver superior MIG welding results with square tubing, meeting the demands of various fabrication projects.
Mig Welding Square Tubing Projects and Applications
The versatility of MIG welding square tubing extends to a wide range of projects and applications across diverse industries. From constructing frameworks and support structures to fabricating custom metal designs, square tubing serves as a foundational component in numerous welding applications. Whether you are working on architectural elements, furniture, automotive components, or industrial equipment, MIG welding square tubing offers the precision and reliability needed to bring your designs to life.
The seamless integration of MIG welding with square tubing enables welders to create intricate and durable assemblies, showcasing the strength and aesthetic appeal of welded metal structures. The adaptability of MIG welding in accommodating various square tubing materials and dimensions further expands the potential for innovative and functional welding projects across different sectors.
By harnessing the capabilities of MIG welding with square tubing, welders can embark on diverse and rewarding welding ventures, contributing to the creation of durable, high-quality metalwork that meets the demands of modern design and engineering requirements.
Final Thoughts
Mastering the art of MIG welding square tubing empowers welders to tackle diverse fabrication projects with confidence and precision. By understanding the advantages of MIG welding, honing the essential techniques, prioritizing safety measures, and implementing best practices, welders can elevate their welding skills and achieve superior results with square tubing applications.
Through the selection of the right MIG welding machine, avoidance of common welding mistakes, and adherence to practical tips, welders can produce strong and clean welds on square tubing, contributing to the structural integrity and visual appeal of the finished workpieces. The versatility and reliability of MIG welding with square tubing open up a world of creative possibilities, enabling welders to embark on innovative projects across various industries.
Embrace the comprehensive insights and guidance provided in this article to embark on a fulfilling journey of mastering MIG welding square tubing, unlocking the potential to create durable, high-quality metalwork and bring your welding projects to new heights of excellence.