When it comes to joining thin sheet metals, MIG welding proves to be an invaluable technique due to its precision and efficiency. However, knowing the right settings is crucial for achieving clean and durable welds. Whether you’re a novice welder or looking to refine your skills, understanding the optimal MIG welding settings for sheet metal is essential.
In this comprehensive guide, we’ll delve into the intricacies of MIG welding sheet metal and explore the ideal settings for different metal thicknesses. From voltage and wire feed speed to shielding gas selection, we will unravel the key parameters that can make or break your welding results. By the end of this article, you’ll be equipped with the knowledge to fine-tune your MIG welder and master the art of welding sheet metal like a seasoned pro. So, let’s dive in and discover the secrets to achieving pristine welds with MIG welding on sheet metal.
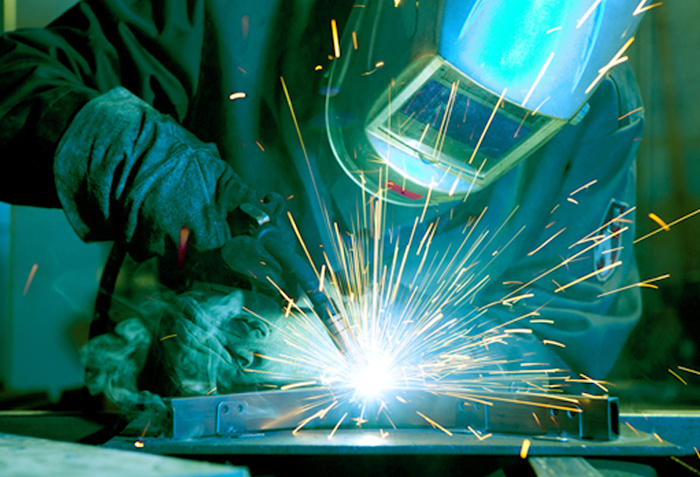
Photos: viofreear.xyz
About Sheet Metal Welding
Sheet metal welding requires a different approach compared to welding thicker materials. The thin nature of sheet metal demands precise control over the welding parameters to prevent burn-through and distortion. Additionally, the type of metal being welded, such as steel, aluminum, or stainless steel, influences the welding process. Understanding the characteristics of the specific metal you’re working with is crucial for achieving high-quality welds.
Developing a keen eye for identifying the thickness of the sheet metal is also essential. This allows you to select the appropriate welding settings and techniques to ensure optimal penetration and fusion without compromising the integrity of the metal. By understanding the unique challenges posed by welding sheet metal, you can tailor your approach to deliver exceptional results.
In the realm of sheet metal welding, precision and attention to detail are paramount. Achieving clean and strong welds on thin metals requires meticulous planning and execution. With the right knowledge and techniques at your disposal, you can elevate your welding capabilities and produce professional-grade results.
Factors to Consider When MIG Welding Sheet Metal
Before diving into the specifics of MIG welding settings for sheet metal, it’s essential to consider the critical factors that influence the welding process. The thickness of the sheet metal, type of metal, and joint design all play pivotal roles in determining the ideal welding settings. Understanding these factors allows you to tailor your approach and make informed decisions to achieve optimal weld quality.
Another crucial consideration is the choice of shielding gas. While carbon dioxide (CO2) is commonly used for welding steel, a mixture of argon and carbon dioxide (often referred to as C25) is preferred for welding stainless steel or aluminum. The selection of the appropriate shielding gas directly impacts the stability of the arc, weld penetration, and overall weld appearance.
The welding position, whether it’s flat, horizontal, vertical, or overhead, can influence the heat input and travel speed required for successful welds. Adapting your welding technique to accommodate different positions is essential for maintaining consistency and weld integrity across various sheet metal applications.
MIG Welding Sheet Metal Settings
Achieving optimal MIG welding settings for sheet metal hinges on precise control over voltage and wire feed speed. For thin sheet metals, lower voltage settings are typically recommended to minimize heat input and reduce the risk of burn-through. As a general guideline, starting with a lower voltage range, such as 16-18 volts, provides a solid foundation for welding sheet metal.
In conjunction with voltage, adjusting the wire feed speed is crucial for achieving a stable and uniform weld bead. A slower wire feed speed is often preferred for welding thin sheet metals, allowing for better control and fusion without overwhelming the metal with excessive heat input. Fine-tuning the wire feed speed to match the selected voltage setting is essential for achieving a harmonious balance that promotes clean and consistent welds.
When it comes to shielding gas selection, the appropriate gas flow rate and composition must be carefully calibrated to ensure adequate coverage and protection of the welding area. Proper gas shielding is instrumental in preventing atmospheric contamination and promoting a stable arc, ultimately contributing to the overall quality of the welded joint.
Sheet Metal Welding Techniques
In addition to setting up the MIG welder with the right parameters, employing suitable welding techniques is crucial for achieving pristine welds on sheet metal. Maintaining a consistent travel speed and maintaining a steady hand are fundamental aspects of successful sheet metal welding. Slow and steady movements allow for precise control over the weld pool, minimizing the risk of overheating and distortion.
Furthermore, employing a series of tack welds along the joint before completing the full weld bead helps distribute heat and minimize warping. Tack welding serves as a strategic approach to stabilize the metal and ensure proper alignment before executing the final weld, contributing to the overall integrity of the welded assembly.
Utilizing a backstepping technique, where the weld bead is laid in a reverse direction from the intended progression, can also mitigate heat buildup and distortion. This method facilitates uniform heat dissipation and reduces the likelihood of creating excessive stress within the metal, resulting in a more structurally sound weld.
Common Mistakes to Avoid When MIG Welding Sheet Metal
Despite the precision and attention to detail required for MIG welding sheet metal, common pitfalls can hinder the quality of the welds if not addressed. One common mistake is using excessive heat, leading to burn-through and warping of the sheet metal. It’s essential to exercise restraint and adhere to the recommended voltage and wire feed speed settings to prevent these issues.
Neglecting proper joint preparation and fit-up can also compromise the integrity of the weld. Inadequate cleaning of the metal surfaces, poor joint alignment, or gaps between the sheet metals can result in incomplete fusion and weak welds. Prioritizing meticulous joint preparation is essential for establishing a strong foundation for the welding process and ensuring consistent weld quality.
Another critical mistake to avoid is neglecting gas shielding, which can lead to weld contamination and porosity. Proper gas flow rates and ensuring the integrity of the gas delivery system are imperative for creating a conducive welding environment. By addressing these common mistakes and implementing best practices, you can elevate the quality of your sheet metal welds and achieve professional-grade results.
MIG Welding Sheet Metal Tips
To enhance your proficiency in MIG welding sheet metal, incorporating certain tips and techniques can significantly impact the overall quality of your welds. Utilizing a smaller diameter welding wire, such as 0.023 inches, offers better control and precision when working with thin sheet metals. The finer wire diameter allows for more delicate welds, minimizing the risk of excessive heat input and distortion.
Employing a welding gun with a shorter nozzle and a smaller contact tip can also enhance maneuverability and access to confined spaces, facilitating more precise and controlled welds. Practicing on scrap pieces of sheet metal to fine-tune your settings and techniques before tackling actual projects allows for experimentation and refinement, ultimately contributing to improved weld quality.
Implementing a dedicated welding sequence, starting from the center of the joint and progressing outward, helps distribute heat evenly and minimizes distortion. This systematic approach contributes to the uniformity and structural integrity of the weld, ensuring a robust and durable joint. By incorporating these tips into your sheet metal welding endeavors, you can elevate your skills and produce superior welds.
Best Practices for Finishing and Protecting Welded Sheet Metal
Once the welding process is complete, it’s essential to focus on post-weld finishing and protection to ensure the longevity and aesthetics of the welded assembly. Conducting thorough cleaning and surface preparation, such as removing spatter and smoothing out weld beads, contributes to a polished and professional appearance. This attention to detail enhances the visual appeal of the welded components.
Applying a suitable primer and paint system to the welded surfaces provides protection against corrosion and enhances the overall durability of the assembly. Selecting a high-quality paint that is compatible with the specific metal type ensures long-term resistance to environmental elements, preserving the integrity of the welded structure and maintaining its aesthetic appeal.
Moreover, integrating edge rounding and deburring techniques on the welded edges enhances safety and minimizes the risk of sharp protrusions. This extra step not only ensures a more refined and professional finish but also promotes user safety and handling of the welded components. By embracing these best practices for finishing and protecting welded sheet metal, you can elevate the overall quality and functionality of your welded assemblies.
Resources for Further Learning About MIG Welding Sheet Metal
Continuing education and exploration of advanced welding techniques are essential for honing your skills in MIG welding sheet metal. Leveraging resources such as welding handbooks, online tutorials, and instructional videos enables you to expand your knowledge and stay abreast of the latest developments in sheet metal welding. Additionally, seeking mentorship from experienced welders and participating in workshops or training programs can provide invaluable insights and practical guidance for refining your welding expertise.
Exploring specialized welding forums and community platforms allows you to engage with fellow welding enthusiasts, exchange knowledge, and seek advice on specific welding challenges. The collective wisdom and experiences shared within these communities can offer fresh perspectives and innovative solutions to elevate your sheet metal welding capabilities.
Furthermore, attending industry trade shows and exhibitions dedicated to welding and metal fabrication provides a firsthand opportunity to explore cutting-edge welding technologies and engage with industry experts. Networking with industry professionals and staying attuned to emerging trends and best practices equips you with the tools and insights to continuously enhance your proficiency in MIG welding sheet metal.
Mastering the art of MIG welding sheet metal
MIG welding sheet metal requires a combination of technical expertise, precision, and dedication to continuous improvement. By understanding the nuances of sheet metal welding, considering critical factors, and honing your welding techniques, you can achieve exceptional weld quality and elevate the overall standard of your welded assemblies.
With a firm grasp of the optimal MIG welding settings for sheet metal, coupled with best practices for welding, finishing, and protecting welded components, you can embark on your welding endeavors with confidence and proficiency. Embracing a mindset of continual learning and exploration of advanced welding resources ensures that you stay ahead of the curve and consistently deliver superior results in your sheet metal welding pursuits.
As you embark on your journey to master MIG welding sheet metal, remember that each weld presents an opportunity to refine your skills and showcase your craftsmanship. By integrating the knowledge and insights shared in this guide, you are poised to elevate your sheet metal welding capabilities and achieve pristine welds that stand the test of time. Here’s to your ongoing success in mastering the art of MIG welding sheet metal!