Step into the fascinating world of microscopic welding, where tiny yet powerful technologies are shaping the future. As technology continues to advance at an extraordinary pace, the capabilities of microscopic welding are revolutionizing various industries. From medical devices and electronics to aerospace engineering and automotive applications, the precision and versatility of microscopic welding techniques are unlocking limitless possibilities.
Put on your metaphorical magnifying glass as we delve into the intricate details of this minuscule yet mighty process. Explore the remarkable advancements in micro welding technology and the pivotal role it plays in enhancing the durability, conductivity, and overall performance of miniature components. Witness how these imperceptible welds are laying the foundation for groundbreaking innovations in fields where precision is paramount.
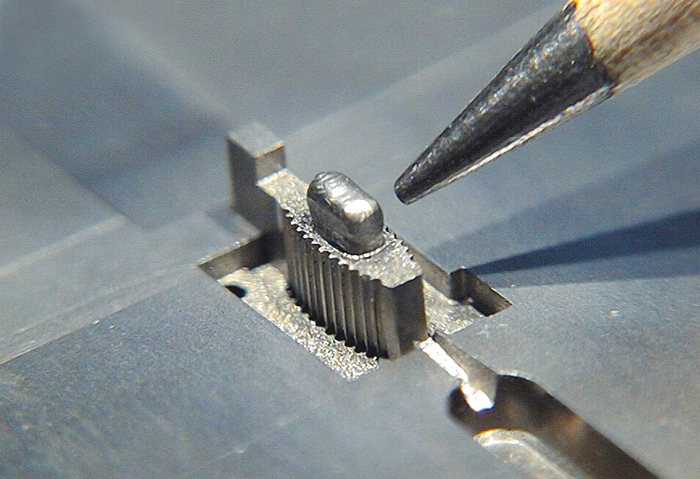
Image : microarcwelding.com
Understanding the Microscopic Welding System
Microscopic welding, also known as micro-welding or micro joining, refers to the process of creating welds on a micro-scale. This intricate technique involves fusing tiny components together using specialized equipment and precise control mechanisms. The welds produced through microscopic welding are often on a sub-millimeter scale, requiring exceptional precision and attention to detail.
The fundamental principle of microscopic weld lies in the controlled application of heat and pressure to join miniature components without causing damage to the surrounding materials. This delicate process demands a high level of skill and expertise to ensure the integrity and reliability of the welds. Microscopic welding is a critical aspect of microfabrication, enabling the assembly of intricate structures and devices with unparalleled accuracy and consistency.
Applications of Microscopic Welding
The applications of microscopic welding span across a diverse range of industries, each benefiting from the precision and reliability it offers. In the medical field, microscopic welding plays a crucial role in the assembly of medical devices, such as pacemakers, stents, and surgical instruments. The ability to create durable and biocompatible welds at a micro-scale is essential for ensuring the safety and effectiveness of these life-saving devices.
In the electronics industry, micro welding is employed in the production of microchips, sensors, and other miniaturized components. The precise and controlled nature of micro welding is instrumental in maintaining the electrical conductivity and mechanical integrity of these intricate electronic devices. Additionally, the aerospace and automotive sectors utilize micro welding for joining small-scale components that require exceptional strength and durability under extreme conditions.
Advantages of Microscopic Welding
The advantages of microscopic welding are multifaceted, offering a myriad of benefits that contribute to its widespread adoption across various industries. One of the primary advantages is the ability to create strong and reliable bonds between miniature components without compromising their structural integrity. The precision of microscopic welding results in minimal heat-affected zones and distortion, ensuring the overall performance and longevity of the assembled parts.
Furthermore, microscopic welding facilitates the joining of dissimilar materials, allowing for the integration of diverse materials with distinct properties. This capability is particularly valuable in applications where the combination of different materials is essential to achieve specific performance requirements. The non-invasive nature of welding minimizes the risk of damage to surrounding components, making it an ideal choice for delicate and intricate assemblies.
Techniques and Processes in Microscopic Welding
Microscopic welding encompasses various techniques and processes tailored to meet the unique demands of micro-scale assembly. One of the commonly employed methods is laser micro-welding, which utilizes focused laser beams to generate localized heat for precise joining of miniature components. This technique offers exceptional control over the heat input and allows for rapid, high-precision welding without significant thermal distortion.
Another prominent approach is micro-TIG (Tungsten Inert Gas) welding, which involves the use of a fine tungsten electrode to produce precise welds in micro and macro applications. The ability to precisely control the arc and filler material deposition makes micro-TIG welding well-suited for joining miniature components with utmost accuracy and repeatability. Resistance micro welding and micro-plasma welding are employed for specific applications that require controlled heat input and minimal material distortion.
Equipment and Tools for Microscopic Welding
The execution of welding relies on specialized equipment and tools designed to meet the exacting requirements of micro-scale assembly. Advanced welding systems equipped with high-resolution optics and precision motion control mechanisms are essential for achieving the minute weld dimensions and positional accuracy demanded by microscopic welding applications.
Microscopes with magnification capabilities ranging from 10x to over 100x are integral for visualizing the welding process and ensuring precise alignment of the components. Additionally, fine-tipped electrodes, laser systems, and micro-manipulators play a pivotal role in facilitating the intricate maneuvers required for microscopic welding. These tools are engineered to provide the operator with the dexterity and control necessary to perform welds at a sub-millimeter scale with exceptional accuracy and repeatability.
Training and Certification
Given the specialized nature of microscopic welding, comprehensive training and certification programs are essential for individuals seeking to master this intricate skill. Training courses focused on microscopic welding encompass theoretical knowledge, practical skills development, and hands-on experience with advanced welding equipment and techniques. These programs are designed to impart a deep understanding of micro-scale welding principles, materials behavior at the micro-level, and the nuances of working with miniature components.
Certification in microscopic weld serves as a validation of an individual’s proficiency and competence in executing micro-scale welds to exacting standards. Accredited certification programs typically evaluate the candidate’s knowledge, practical skills, and adherence to industry best practices. Attaining certification in microscopic welding not only enhances an individual’s credibility but also demonstrates their commitment to upholding the highest standards of quality and precision in micro-scale assembly.
Safety Measures in Microscopic Welding
While microscopic welding may involve working with diminutive components, the adherence to stringent safety measures is paramount to safeguard the well-being of operators and ensure the integrity of the welded assemblies. Personal protective equipment, including specialized eyewear with magnification capabilities, is essential for shielding the eyes from intense light and potential debris generated during the welding process.
Proper ventilation and fume extraction systems are crucial to mitigate the exposure to fumes and airborne contaminants produced during microscopic weld operations. Adherence to established protocols for handling and disposing of hazardous materials, such as welding consumables and cleaning agents, is imperative to maintain a safe and healthy working environment. Rigorous safety training and ongoing awareness of potential hazards are fundamental aspects of promoting a culture of safety in microscopic welding practices.
Common Challenges in Microscopic Welding
Despite the precision and advanced technology associated with microscopic welding, several challenges are inherent to working at the micro-scale. One of the primary challenges revolves around achieving consistent and reliable weld quality, especially when dealing with miniature components that are susceptible to heat-induced deformations and material interaction complexities. Overcoming these challenges necessitates a deep understanding of material properties, thermal behavior, and the interplay of forces at the micro-level.
Another common challenge is maintaining alignment and positional stability during the welding process, particularly when working with sub-millimeter components. The slightest deviation in alignment can significantly impact the integrity of the weld, underscoring the need for meticulous control and precision in microscopic welding operations. Moreover, the limited accessibility and visibility of the weld zone present challenges in ensuring optimal weld penetration and fusion across miniature joint interfaces.
Industries Utilizing Microscopic Welding
The utilization of microscopic welding extends across a spectrum of industries, each leveraging the precision and versatility of micro-scale assembly for diverse applications. In the medical field, microscopic welding is instrumental in the production of implantable medical devices, microfluidic systems, and miniature surgical instruments. The ability to create hermetically sealed, biocompatible welds at the micro-level is pivotal for ensuring the performance and safety of these critical medical components.
The electronics industry relies on micro welding for the fabrication of microchips, sensors, and microelectromechanical systems (MEMS) that power a myriad of electronic devices. The precise joining of miniaturized components is essential for maintaining the functionality and reliability of electronic assemblies. Additionally, the aerospace and automotive sectors benefit from microscopic welding in the assembly of miniaturized sensors, actuators, and micro-scale components that are integral to the performance and safety of aircraft and automotive systems.
Final Thoughts
The world of microscopic welding offers a captivating glimpse into the realm of precision engineering and micro-scale assembly. The remarkable advancements in micro welding technology have positioned microscopic welding as a cornerstone of modern manufacturing and technology. From its pivotal role in enhancing the durability and performance of miniature components to its far-reaching applications across diverse industries, microscopic welding continues to shape the landscape of innovation and progress.
As we peer through the metaphorical magnifying glass, we gain a deep appreciation for the meticulous craftsmanship and ingenuity required to navigate the intricacies of microscopic welding. The fusion of advanced techniques, specialized equipment, and unwavering attention to detail underscores the profound impact of micro welding on the development of cutting-edge technologies and the realization of groundbreaking innovations. Embracing the imperceptible yet mighty world of micro welding unveils a universe of possibilities, where precision knows no bounds and where the smallest welds wield the power to transform the future.