Step into the realm of cutting-edge manufacturing as we delve into the unrivaled precision and efficiency of laser welding. By harnessing the power of concentrated light energy, this transformative process is redefining the way we approach metal joining. From automotive and aerospace industries to electronics and medical devices, laser welding stands as the hallmark of immaculate craftsmanship and unparalleled strength.
In our exploration of the laser welding process, we uncover the seamless fusion of art and science, where each beam of light represents the epitome of accuracy. Unleashing a symphony of photons, these devices deliver meticulous welds with minimal heat-affected zones, promising pristine results for even the most intricate components.
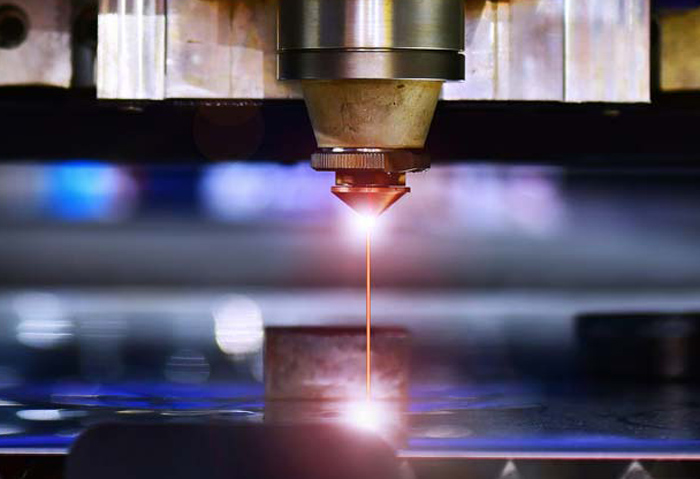
Image : zerohourparts.com
Types of Laser Welding Processes
Laser welding encompasses several distinct processes, each tailored to specific material types and thicknesses. The most common techniques include conduction welding, deep penetration welding, and pulsed laser welding. Conduction welding is ideal for thin materials, utilizing lower power levels to create shallow welds. Deep penetration welding, on the other hand, is suited for thicker materials, employing high-power density to achieve deep, narrow welds.
Pulsed laser welding provides greater control over heat input, making it suitable for delicate materials and intricate designs. Each method offers unique advantages, catering to a wide range of manufacturing requirements.
Advantages of Laser Welding
The laser welding process presents a multitude of advantages over traditional welding methods. Firstly, its non-contact nature eliminates the need for physical force, reducing the risk of deformation and material contamination. The focused heat input results in minimal distortion and negligible thermal stress, preserving the structural integrity of the welded components.
Moreover, the precision of laser welding allows for intricate designs and tight tolerances, enabling seamless joins in intricate geometries. The high welding speed and minimal heat-affected zones contribute to increased productivity and superior aesthetic appeal. These advantages collectively position laser welding as the premier choice for achieving high-quality, durable welds.
Applications of Laser Welding
The versatility of laser welding extends across a diverse array of industries. In the automotive sector, it is employed for joining car body components, exhaust systems, and battery assemblies, ensuring robust connections with minimal weight addition. Within the aerospace industry, laser welding is utilized for fabricating aircraft structures, engine components, and fuel systems, meeting stringent quality and safety standards. Furthermore, the electronics industry leverages laser welding for micro-welding delicate components in electronic devices, ensuring precise connections without thermal damage.
In the medical field, laser welding facilitates the assembly of medical devices and implants, guaranteeing biocompatibility and structural integrity. These applications exemplify the indispensable role of laser welding in achieving uncompromising quality across various sectors.
Factors Influencing Laser Welding Quality
Several critical factors influence the quality of laser welding. The choice of laser wavelength and pulse duration, as well as the beam focus and power density, directly impact the penetration depth and heat-affected zone. Material properties, such as reflectivity and thermal conductivity, also play a pivotal role in determining the weld quality.
Proper joint fit-up, shielding gas selection, and beam delivery systems contribute to the overall welding precision and integrity. Understanding and optimizing these factors are imperative for achieving consistent, high-quality laser welds across different materials and applications.
Laser Welding vs Traditional Welding Methods
In comparison to traditional welding methods, laser welding offers unparalleled precision, minimal thermal distortion, and superior aesthetic appeal. Traditional welding techniques, such as gas metal arc welding (GMAW) and tungsten inert gas (TIG) welding, often result in larger heat-affected zones and increased material distortion due to the broader energy dispersion.
Additionally, laser welding excels in welding dissimilar materials, such as aluminum to steel, which can be challenging with traditional methods. While traditional welding methods remain relevant for certain applications, laser welding stands as the epitome of precision and efficiency in modern manufacturing.
Safety Precautions in Laser Welding
Laser welding necessitates strict adherence to safety protocols to mitigate potential hazards associated with high-powered laser equipment. Personal protective equipment, including laser safety glasses and appropriate attire, is essential for safeguarding against direct or reflected laser beams. Adequate ventilation and fume extraction systems are imperative to prevent inhalation of hazardous fumes and particulates generated during the welding process.
Furthermore, training in laser safety practices and emergency procedures is crucial for mitigating the risks associated with laser welding. By prioritizing safety measures, manufacturers can ensure a secure working environment for laser welding operations.
Choosing the Right Laser Welding Equipment
Selecting the appropriate laser welding equipment is paramount to achieving optimal results. Factors to consider include the power output, beam quality, and wavelength of the laser system, tailored to the specific material and application requirements. Additionally, the versatility of the equipment, such as its ability to accommodate different joint configurations and thicknesses, is crucial for addressing diverse welding needs.
Integration of advanced features, such as real-time monitoring and control systems, enhances process visibility and quality assurance. By investing in reliable and versatile laser welding equipment, manufacturers can elevate their production capabilities and maintain a competitive edge in the market.
Training and Certifications for Laser Welding
Proficiency in laser welding demands comprehensive training and certifications to ensure adherence to industry standards and best practices. Through specialized training programs, welders gain proficiency in laser equipment operation, process optimization, and safety protocols. Certifications validate the expertise of welders, demonstrating their competency in executing precise and reliable laser welds.
Moreover, continuous professional development and upskilling in laser welding techniques and technologies are essential for staying abreast of industry advancements and refining welding proficiency. By investing in training and certifications, manufacturers can cultivate a skilled workforce capable of delivering superior laser welding solutions.
Final Thoughts
In the realm of modern manufacturing, the laser welding process stands as a beacon of precision, efficiency, and innovation. Its ability to deliver immaculate welds with minimal heat-affected zones, coupled with its diverse applications across industries, underscores its indispensable role in achieving superior joinery. By understanding the nuances of laser welding processes, harnessing its advantages, and prioritizing safety and training, manufacturers can unlock the full potential of this transformative technology.
As we continue to push the boundaries of precision joining, laser welding remains at the forefront, illuminating the path toward a future defined by impeccable craftsmanship and unwavering strength.