Micro spot welding, also known as micro resistance spot welding, is a highly specialized welding process that is used to join small components together with pinpoint accuracy. This process involves the use of a small, precisely controlled electrical current to create a localized heat zone, which effectively fuses the materials being joined. Unlike traditional welding techniques, micro spot welding is tailored for applications that demand extreme precision and control, such as in the manufacturing of electronic devices, medical equipment, and jewelry.
The key to the success of micro spot welding lies in its ability to deliver high-quality welds without causing any damage to the surrounding areas. This makes it an indispensable tool for industries where the integrity of tiny components and delicate materials is paramount. By harnessing the power of micro spot welding, manufacturers can achieve seamless, durable connections in even the most intricate projects, driving innovation and pushing the boundaries of what is possible in miniaturized welding applications.
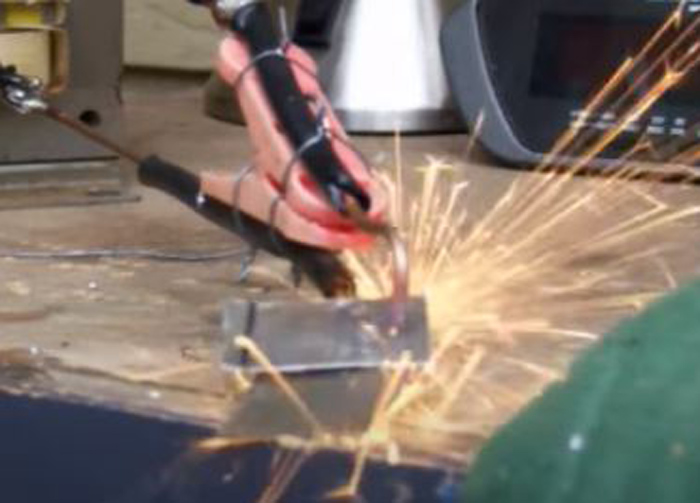
Image by bbewamit on YT
When it comes to micro spot welding, attention to detail is paramount. Every aspect of the process, from the selection of materials to the calibration of the equipment, must be meticulously managed to ensure the highest level of precision and reliability. The art of micro spot welding is a fusion of technological prowess and artisanal skill, where the tiniest of welds can have a monumental impact on the performance and longevity of the final product.
Applications of Micro Spot Welding
The applications of micro spot welding span a wide range of industries, each benefiting from the precision and versatility that this specialized welding process offers. In the realm of electronics manufacturing, micro spot welding plays a crucial role in assembling intricate circuitry and delicate components with sub-millimeter precision. From tiny sensors to microchips, the ability to create robust, reliable connections at a miniature scale is essential for ensuring the functionality and durability of electronic devices.
In the medical industry, micro spot welding is instrumental in the fabrication of medical devices and implants, where the demand for biocompatible materials and precise assembly is non-negotiable. Whether it’s joining tiny components for pacemakers, surgical instruments, or medical sensors, micro welding enables the creation of seamless, sterile connections that meet the stringent requirements of the healthcare sector.
The jewelry industry also harnesses the power of micro welding to create intricate designs and repair delicate pieces with unparalleled precision. From seamlessly joining tiny metal components to repairing intricate filigree work, micro spot welding empowers artisans to work on a micro scale without compromising the structural integrity and aesthetic appeal of the jewelry.
Advantages of Micro Spot Welding
The advantages of micro spot welding are multifaceted, making it a preferred choice for applications that demand precision, reliability, and minimal heat-affected zones. One of the primary benefits of micro spot welding is its ability to create strong, durable welds in small, confined spaces, where traditional welding methods may not be feasible. This makes it an ideal solution for joining tiny components and working with delicate materials that require a gentle touch.
Additionally, micro welding offers excellent repeatability and control, ensuring consistent weld quality across a large volume of production. The precise control of the welding parameters, such as current, time, and pressure, allows manufacturers to achieve uniform and reliable welds, thus minimizing the risk of defects and rework. This level of consistency is invaluable in industries where the reliability and performance of the final product are of utmost importance.
Another key advantage of micro spot welding is its ability to minimize the heat-affected zone, thereby reducing the risk of material distortion, discoloration, or warping. This is particularly crucial when working with heat-sensitive materials or components that are susceptible to thermal damage. By confining the heat input to a localized area, micro welding preserves the integrity of the surrounding materials, resulting in clean, aesthetically pleasing welds without compromising the structural strength.
Micro Spot Welding Process
The micro spot welding process involves several key steps, each contributing to the precise and controlled formation of welds in miniature applications. The first step in the process is the preparation of the materials to be joined. This may involve cleaning the surfaces to ensure optimal weld quality and removing any contaminants that could interfere with the welding process. Proper material preparation is essential for achieving strong, reliable welds in micro applications.
Once the materials are prepared, the next step is to position them in the welding fixture or tooling. This ensures that the components are aligned correctly and held securely in place during the welding process. Precision fixturing is critical for achieving accurate weld placement and minimizing the risk of misalignment, which could compromise the integrity of the final weld.
With the materials positioned and secured, the welding parameters are set based on the specific requirements of the application. This includes determining the appropriate welding current, duration, and pressure, all of which are carefully controlled to achieve the desired weld quality. The ability to finely tune these parameters is what sets micro welding apart, allowing for tailored adjustments to accommodate varying materials and component geometries.
Once the welding parameters are configured, the welding cycle is initiated, applying the precise electrical current and pressure to create the weld. The localized heat generated by the electrical current softens the materials at the weld interface, allowing them to fuse together and form a strong, metallurgical bond. The duration of the welding cycle is carefully monitored to ensure that the heat input is controlled and the weld is formed with precision.
After the welding cycle is complete, the welded components are allowed to cool before being removed from the fixture. This cooling period is essential for solidifying the weld and ensuring that it achieves the necessary mechanical and metallurgical properties. Once cooled, the welded assembly undergoes inspection to verify the quality of the weld and confirm that it meets the specified standards for strength and integrity.
Equipment and Tools for Micro Spot Welding
The execution of micro spot welding relies on specialized equipment and tools designed to facilitate the precise application of electrical current and pressure for creating miniature welds. One of the key components of micro welding equipment is the power supply, which delivers the electrical energy required to generate the localized heat for welding. These power supplies are engineered to provide precise control over the welding parameters, including current, duration, and waveform, enabling tailored adjustments to suit the specific requirements of the application.
In addition to the power supply, micro spot welding equipment incorporates specialized welding electrodes, or tips, that come into direct contact with the materials being welded. These electrodes are designed to deliver the electrical current to the targeted weld area while applying the necessary pressure to ensure proper fusion of the materials. The selection of electrode materials and shapes is crucial for achieving optimal weld quality and minimizing electrode wear.
To support the precise positioning and alignment of the materials, micro welding tools often feature custom fixtures and tooling that secure the components in place during the welding process. These fixtures are designed to accommodate the unique geometries of the parts and ensure that they are held in the correct orientation for accurate welding. The ability to customize tooling for specific applications is essential for achieving consistent, high-quality welds.
Furthermore, modern micro welding equipment may incorporate advanced control systems and monitoring technologies that enable real-time feedback and adjustment during the welding process. This level of automation and monitoring enhances the precision and repeatability of micro spot welding, allowing for seamless integration into high-volume production environments and ensuring consistent weld quality across a range of applications.
Factors to Consider in Micro Welding
When embarking on micro spot welding projects, several critical factors must be taken into account to ensure the success and reliability of the welding process. Material selection is a fundamental consideration, as the compatibility of the materials being joined can significantly impact the weld quality and strength. Understanding the metallurgical properties, conductivity, and heat sensitivity of the materials is essential for optimizing the welding parameters and achieving robust welds.
The geometry and thickness of the components also play a pivotal role in micro spot welding, as the configuration of the parts can influence the distribution of heat and pressure during the welding process. Tailoring the welding parameters to accommodate variations in component geometry is vital for achieving consistent, high-quality welds across a diverse range of applications. Additionally, the surface condition of the materials, including cleanliness and flatness, must be carefully managed to ensure proper weld formation.
The welding environment and ambient conditions can impact the performance of micro welding, particularly in terms of electrical conductivity and heat dissipation. Controlling factors such as humidity, temperature, and air quality in the welding environment is crucial for maintaining stable welding conditions and achieving predictable outcomes. The ability to mitigate environmental variables empowers manufacturers to uphold the integrity and reliability of micro spot welding processes.
In addition to material and environmental considerations, the mechanical setup and calibration of the micro spot welding equipment are critical for achieving precise and repeatable welds. Proper alignment of the welding electrodes, accurate control of the welding parameters, and calibration of the welding tools are essential for ensuring that the applied energy and pressure result in consistent, high-integrity welds. Attention to detail in the setup and calibration processes is indispensable for achieving optimal welding performance.
Common Challenges in Micro Spot Welding
Despite its precision and versatility, micro spot welding is not without its challenges, and practitioners must be mindful of potential obstacles that could impact the quality and reliability of the welds. One common challenge in micro spot welding is the potential for electrode wear, which can occur due to the repeated application of electrical current and pressure on the materials being welded. Managing electrode wear through proper material selection and maintenance is essential for sustaining consistent welding performance.
Another challenge in micro spot welding is the risk of weld splatter, particularly when working with materials that are prone to spattering during the welding process. Weld splatter can result in surface contamination and compromise the aesthetic and functional quality of the welds. Implementing strategies to mitigate weld splatter, such as optimizing welding parameters and utilizing anti-spatter coatings, is crucial for preserving the cleanliness and integrity of the welded components.
Achieving consistent weld quality in micro welding can be challenging when working with dissimilar materials or complex geometries. Variations in material composition, conductivity, and thermal properties can introduce complexities that require careful consideration and fine-tuning of the welding parameters. Addressing these challenges involves a deep understanding of material behavior and the implementation of tailored welding strategies to accommodate diverse material combinations.
The size and scale of welding also present challenges, particularly when working with extremely small components or thin materials. Ensuring proper heat distribution, pressure application, and electrode contact in micro-scale applications demands a high level of precision and control. Overcoming these challenges may involve the development of specialized tooling, fixturing, and welding techniques tailored to the unique requirements of micro welding at a miniature scale.
Safety Measures in Micro Spot Welding
Maintaining a safe and secure working environment is paramount in micro welding, where the use of electrical energy and application of pressure pose potential hazards to the operator and surrounding personnel. Implementing safety measures that adhere to industry standards and best practices is essential for safeguarding against the risks associated with micro spot welding operations. One fundamental safety consideration is the use of personal protective equipment (PPE), including gloves, eye protection, and appropriate attire, to shield against electrical hazards, heat, and potential material splatter.
In addition to PPE, ensuring proper ventilation and air filtration in the welding environment helps minimize exposure to fumes and airborne contaminants that may result from the welding process. Adequate ventilation systems and exhaust hoods aid in maintaining a clean, breathable atmosphere for the welding operators and surrounding personnel. Controlling the dissemination of welding by-products and fumes contributes to a safer and healthier work environment.
Moreover, the proper handling and storage of welding equipment, including power supplies, electrodes, and fixtures, are essential for preventing accidental injuries and equipment damage. Securing the equipment in designated storage areas, inspecting it for any signs of wear or malfunction, and following manufacturer guidelines for maintenance and usage contribute to a safer workplace. Additionally, providing thorough training and certification for personnel involved in micro welding ensures that they are equipped with the knowledge and skills to execute welding operations safely and proficiently.
The implementation of safety protocols, such as establishing clear work procedures, conducting risk assessments, and adhering to regulatory requirements, fosters a culture of safety and responsibility in micro spot welding environments. By prioritizing safety at every stage of the welding process, from equipment setup to post-welding activities, organizations can mitigate risks and create a secure working environment for all involved.
Advancements in Micro Spot Welding Technology
The landscape of micro spot welding continues to evolve, driven by advancements in technology, materials, and manufacturing processes. One notable area of advancement lies in the development of advanced welding power supplies that offer enhanced precision, control, and monitoring capabilities. These next-generation power supplies leverage sophisticated control algorithms and real-time feedback mechanisms to optimize welding parameters and ensure consistent weld quality across diverse applications.
The integration of intelligent welding systems that incorporate machine learning algorithms and data analytics is revolutionizing the way micro spot welding is executed. These smart welding systems can adapt to dynamic welding conditions, self-optimize based on real-time performance data, and predict potential welding issues, thereby enhancing productivity and reducing the need for manual intervention. The convergence of advanced technologies with micro spot welding is paving the way for more efficient, reliable, and adaptive welding solutions.
Another area of advancement in micro welding technology is the development of innovative electrode materials and coatings that prolong electrode life, reduce spatter, and enhance weld quality. By leveraging novel materials and surface treatments, manufacturers can mitigate common challenges associated with electrode wear and weld spatter, ultimately improving the longevity and performance of the welding equipment. These advancements contribute to more sustainable and cost-effective welding operations.
Moreover, the emergence of additive manufacturing, or 3D printing, has brought about new opportunities for micro welding, particularly in the fabrication of complex, customized components with intricate geometries. Additive manufacturing technologies enable the creation of novel designs that may pose unique challenges for conventional welding methods. Micro spot welding techniques are being adapted and refined to accommodate the joining of 3D-printed parts, opening doors to unprecedented possibilities in micro-scale manufacturing and repairs.
As micro spot welding technology continues to progress, the industry is witnessing the convergence of digitalization, automation, and interconnected manufacturing systems, leading to more streamlined and interconnected welding processes. The integration of micro spot welding with Industry 4.0 principles, such as remote monitoring, predictive maintenance, and digital twin simulations, is reshaping the way welding
Conclusion
Micro spot welding is a highly detailed process of joining relatively small pieces of metal together using heat and pressure. This metalworking technique is incredible versatile, as it produces strong joints with good electrical resistance in a range of alloys and coatings. Considering the precision of the process, micro spot welding is not something to be done without expert knowledge and experience. Reach out to a professional today to explore your options for properly utilizing micro spot welding on your next project. Together, you can create stronger welds than ever before! Don’t wait any longer – get those pieces secured with satisfaction-guaranteed quality.