When it comes to precision welding techniques, two methods that come to mind are laser welding and TIG welding. Both welding techniques have their own unique characteristics, advantages, and applications, and understanding their key differences is crucial in determining which technique to use for specific projects.
In this article, we will explore and compare laser welding vs TIG welding in depth, including their process, advantages, and applications. By the end of this article, you will have a comprehensive understanding of these two welding techniques, enabling you to make an informed decision when choosing the appropriate welding method for your specific needs.
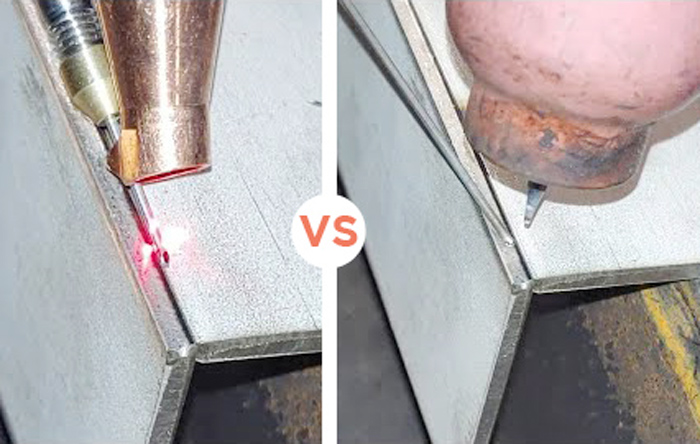
Photos: weldHAGOJIBI
Understanding Laser Welding
Laser welding is a precision welding technique that uses a high-energy laser beam to melt and fuse metal parts together. The process involves focusing the laser beam on a specific area of the metal, which rapidly heats and melts the material.
The laser beam used in welding is generated by a laser resonator, which directs the beam through a series of mirrors and lenses to the welding site. The laser beam can be precisely controlled, allowing for accurate and repeatable welds.
One of the key benefits of laser welding is its precision. The laser beam can be focused on a small area, allowing for precise control of the weld. This makes laser welding ideal for welding small or delicate parts, as well as for applications that require high accuracy and consistency.
Laser Welding Process
The laser welding process typically involves a few key steps:
- Cleaning and preparing the parts to be welded
- Positioning the parts and aligning them precisely, often using a jig or fixture
- Activating the laser beam and directing it onto the welding site
- Moving the laser beam across the welding site in a controlled manner
- Allowing the metal to cool and solidify after welding is complete
The laser welding process can be performed manually or using an automated system. Automated systems are often used for high-volume production runs, while manual welding may be used for small-scale or custom projects.
Precision Welding Techniques
Laser welding is a precision welding technique that offers a number of advantages over other welding methods. Some of the key benefits of laser welding include:
- High precision and accuracy
- Minimal distortion and heat-affected zones
- High weld strength and quality
- Faster welding speeds
- Minimal consumable materials
These advantages make laser welding an ideal choice for industries such as aerospace, automotive, electronics, and medical device manufacturing. Laser welding can be used to join a variety of metals, including aluminum, stainless steel, and titanium.
Exploring TIG Welding
Tungsten Inert Gas (TIG) welding is a precise welding technique that requires skill and experience. It is commonly used for welding thin materials such as aluminum, stainless steel, and copper. TIG welding uses a non-consumable tungsten electrode and a shielding gas to protect the weld from oxidation.
The TIG welding process involves the following steps:
- Clean the area to be welded
- Set up the equipment, including the welding machine and gas supply
- Insert the tungsten electrode into the welding torch
- Connect the ground clamp to the workpiece
- Start the welding process with an arc
- Add filler metal to the weld as necessary
- Control the heat input and weld pool size
- Complete the weld and allow it to cool
TIG welding offers several advantages, including:
- Excellent control over the weld pool size and shape
- Ability to weld thin materials without burning through
- Produces high-quality, precise welds
- Minimal spatter and fumes
TIG welding is commonly used in the aerospace, automotive, and electronics industries. It is also widely used for welding sculptures, artwork, and other creative projects due to its precise nature.
Comparison of Laser Welding vs Traditional Welding
When it comes to welding, there are two main families of techniques: traditional welding and laser welding. Traditional welding encompasses a wide range of methods, including gas welding, arc welding, and resistance welding. In contrast, laser welding is a modern precision welding process that uses a concentrated laser beam to join metals and other materials.
The main difference between laser welding and traditional welding lies in the precision and efficiency of the process. While traditional welding techniques require a lot of heat and may result in rough edges or weakened materials, laser welding offers high precision and control, allowing for welding in hard-to-reach areas and producing a clean, smooth finish.
Laser Welding | Traditional Welding |
---|---|
Uses a concentrated laser beam to join materials | Uses heat, pressure, or electricity to join materials |
Provides high precision and control | May result in rough edges or weakened materials |
Produces a clean, smooth finish | May require additional finishing work |
Another advantage of laser welding over traditional welding is the ability to weld dissimilar materials, including metals and plastics. Traditional welding methods often require similar materials to be joined together. Laser welding, on the other hand, can join a variety of materials with precision and strength.
Overall, while traditional welding techniques have their place in many industries, laser welding stands out as a reliable, precise, and efficient welding process that offers clear advantages over traditional methods.
Advantages and Applications of Laser Welding vs TIG Welding
Both laser welding vs TIG welding have unique advantages and are utilized in various industries. Let’s take a closer look at how these precision welding techniques can benefit your project:
Advantages of Laser Welding:
- High precision and accuracy due to the focused beam of light.
- Minimal distortion, making it ideal for delicate components.
- Minimal heat input, reducing the risk of material damage and warping.
- Fast welding speed, increasing productivity and efficiency.
- Wide range of materials can be welded, including metals, plastics, and ceramics.
- Minimal post-welding processing is required, reducing overall costs.
Applications of Laser Welding:
Industry | Applications |
---|---|
Automotive | Welding of engine components, transmission parts, body panels, and exhaust systems. |
Medical | Welding of surgical instruments, implants, and medical devices. |
Electronics | Welding of microelectronics, sensors, and connectors. |
Jewelry | Welding of precious metals, including gold, silver, and platinum. |
Advantages of TIG Welding:
- High-quality welds with strong mechanical properties.
- Greater control over the welding process, allowing for adjustments during welding.
- Less expensive equipment and materials compared to laser welding.
- Effective for welding thin materials.
- Ability to weld a variety of metals, including stainless steel, aluminum, and copper alloys.
Applications of TIG Welding:
Industry | Applications |
---|---|
Aerospace | Welding of aircraft components, including frames, fuselage, and landing gear. |
Construction | Welding of pipelines, bridges, and structural frames. |
Food and Beverage | Welding of tanks, pipes, and vessels for food and beverage processing. |
Power Generation | Welding of power plant components, including turbines and heat exchangers. |
Choosing between laser welding and TIG welding depends on the specific requirements of your project. Consider the material, production volume, and desired welding quality when making your decision.
Final Thoughts
As we come to the end of this article, we hope that you now have a clear understanding of the difference between laser welding vs TIG welding techniques. While both methods are precision welding techniques, they have their unique characteristics that make them suitable for specific welding applications. When it comes to laser welding, it offers a highly efficient and precise welding process that is ideal for welding thin materials. Its non-contact process and ability to weld dissimilar materials makes laser welding popular in industries such as electronics, medical equipment, and automotive manufacturing.
TIG welding, on the other hand, is a versatile welding technique that can be used on various materials and thicknesses. Its precision, clean welds, and ability to work in different positions make it ideal for welding critical components in aerospace, defense, and automotive industries.
Choosing the Right Welding Technique
When choosing between laser welding and TIG welding, it is important to consider the specific project requirements, the material being welded, budget, and the desired outcome. While laser welding offers precision and speed, TIG welding is versatile and can be used on a wider range of materials. It is also important to consider the cost of equipment and maintenance. Laser welding machines can be more expensive than TIG welding machines, but they offer a non-contact process that reduces damage to the material being welded.
In conclusion, both laser welding and TIG welding techniques have their advantages and applications in various industries. Choosing the appropriate welding technique depends on the project requirements, material being welded, budget, and desired outcome.
FAQ
What is the difference between laser welding and TIG welding?
Laser welding uses a high-powered laser beam to melt and join materials, while TIG welding uses a tungsten electrode to create an arc and melt the materials together. Laser welding offers precise control and high welding speeds, while TIG welding offers excellent control over the weld pool and is often used for thinner materials.
What are the advantages of laser welding?
Laser welding offers high precision, minimal heat input, and the ability to weld complex geometries. It is also faster than most traditional welding methods and produces minimal distortion in the surrounding area.
What are the advantages of TIG welding?
TIG welding allows for precise control, produces clean and high-quality welds, and can be used on a wide range of materials, including stainless steel, aluminum, and copper. It is also suitable for welding thinner materials.
How does laser welding work?
Laser welding works by focusing a high-powered laser beam onto the materials to be joined. The laser heat melts and fuses the materials together, creating a strong weld. The process is controlled by computer systems to ensure precise welding results.
How does TIG welding work?
TIG welding works by creating an arc between a tungsten electrode and the materials to be welded. The heat of the arc melts the materials, and a separate filler metal can be added if needed. TIG welding requires a shielding gas to protect the weld from atmospheric contamination.
When should I choose laser welding over TIG welding?
Laser welding is ideal for applications that require high precision, speed, and minimal heat input. It is commonly used in industries such as automotive, aerospace, and electronics. TIG welding is suitable for more intricate welds and thinner materials, making it popular in industries like fabrication, piping, and jewelry making.
Can laser welding replace traditional welding methods?
Laser welding offers several advantages over traditional welding methods, including faster speeds and less distortion. However, it may not be suitable for all applications. Traditional welding methods still have their place, especially for larger and thicker structures where laser welding may not be cost-effective.