Are you looking to learn how to weld exhaust pipe? Whether you are a DIY enthusiast or a professional mechanic, having the know how to weld exhaust pipes can come in handy. In this article, we will explore three common welding methods used for exhaust pipe welding with MIG, TIG, and flux core welding.
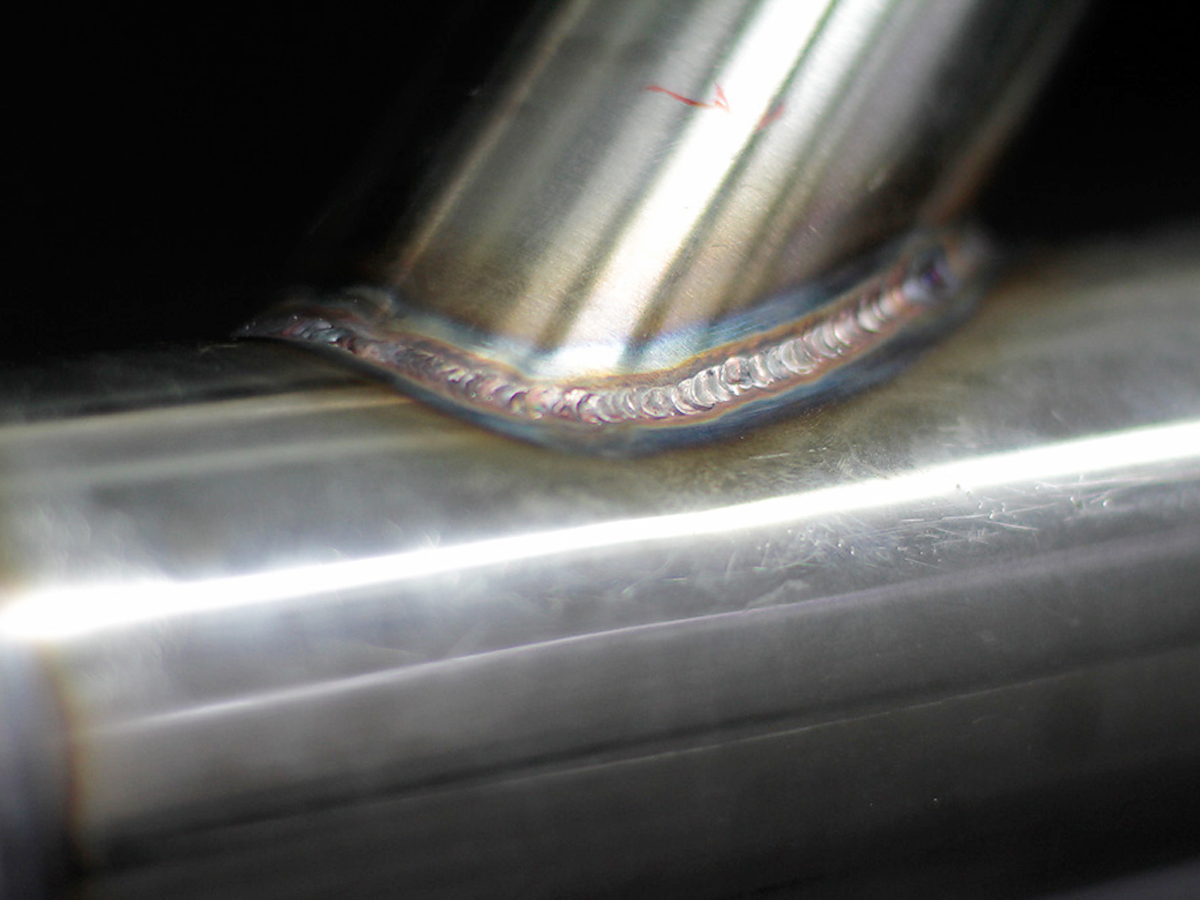
Photos by thestadel
Understanding the Different Welding Methods – Mig, Tig, and Flux Core
Welding exhaust pipes requires a good understanding of different welding methods. Let’s take a closer look at each one:
How to Weld Exhaust Pipe with MIG Welding?
MIG welding, also known as Gas Metal Arc Welding (GMAW), is a popular choice for exhaust pipe welding due to its ease of use and versatility. It involves feeding a wire electrode through a welding gun, which is then melted to create a strong bond between the exhaust pipe and the filler material.
One of the advantages of MIG welding is its ability to handle thicker materials, making it suitable for repairing exhaust pipes that have suffered extensive damage. It also offers faster welding speeds, which can be a time-saving factor for professionals working on multiple projects.
It’s important to note that MIG welding requires the use of shielding gas to protect the weld pool from atmospheric contamination. This means you will need to have a ready supply of shielding gas, such as argon or a mixture of argon and carbon dioxide, depending on the specific requirements of the exhaust pipe material.
How to Weld Exhaust Pipe with TIG Welding
TIG welding, or Gas Tungsten Arc Welding (GTAW), offers greater precision and control, making it ideal for thinner exhaust pipe materials. Unlike MIG welding, TIG welding uses a non-consumable tungsten electrode to create the arc, and a separate filler rod is used to add material.
One of the main advantages of TIG welding is its ability to produce high-quality welds with minimal distortion. This makes it a popular choice for welding stainless steel or aluminum exhaust pipes, where appearance and strength are crucial.
However, TIG welding requires a higher level of skill and practice compared to MIG welding. It involves using both hands simultaneously to control the torch and feed the filler rod, making it a more complex process. Additionally, TIG welding is a slower process compared to MIG welding, which may be a consideration if you’re working on time-sensitive projects.
How to Weld Exhaust Pipe with Flux Core Welding
Flux core welding is a self-shielding process that is often used when access to shielding gas is limited. It uses a flux core electrode, which contains a flux compound that releases a protective gas when heated. This eliminates the need for external shielding gas, making it a convenient option for welding exhaust pipes in outdoor or remote locations.
One of the advantages of flux core welding is its ability to handle dirty or rusty materials. The flux compound in the electrode helps to remove impurities and contaminants, resulting in a clean and strong weld. It’s also a good option for welding thicker materials, where the deeper penetration provided by flux core welding can be advantageous.
Flux core welding may not produce as clean and aesthetically pleasing welds compared to MIG or TIG welding. It also tends to generate more spatter, requiring additional cleanup after welding. If appearance is a critical factor for your exhaust pipe project, you may want to consider MIG or TIG welding instead.
Choosing the Right Welding Method for Your Exhaust Pipe
When deciding on the most suitable welding method for your exhaust pipe, there are a few factors to consider:
- Material: The type of material used for your exhaust pipe will influence the choice of welding method. MIG welding is suitable for thicker materials like mild steel, while TIG welding is preferred for stainless steel or aluminum. Flux core welding can handle a variety of materials, including rusty or dirty surfaces.
- Skill Level: The level of skill and experience you have with welding should also be taken into account. If you’re a beginner, MIG welding might be a more forgiving option, while experienced welders may prefer the precision and control offered by TIG welding.
- Time Constraints: If you’re working on a time-sensitive project, MIG welding’s faster welding speeds may be advantageous. However, if appearance and quality are more important, TIG welding might be worth the extra time investment.
- Access to Shielding Gas: If you’re working in a location where access to shielding gas is limited, flux core welding can be a convenient alternative.
Consider these factors carefully to ensure you choose the most appropriate welding method for your specific project requirements.
Safety Precautions When Welding Exhaust Pipes
Welding exhaust pipes involves working with high temperatures and potentially hazardous materials. It’s important to prioritize safety to protect yourself and those around you. Here are some essential safety precautions to follow:
- Personal Protective Equipment (PPE): Wear appropriate PPE, including a welding helmet with a proper shade, flame-resistant clothing, gloves, and safety glasses.
- Ventilation: Ensure proper ventilation in the welding area to remove fumes and gases. Welding in a well-ventilated space or using a fume extraction system is recommended.
- Fire Safety: Keep a fire extinguisher nearby and clear any flammable materials from the welding area. Be cautious of sparks and ensure a fire-safe environment.
- Electric Shock: Avoid contact with live electrical parts and ensure proper grounding of your welding equipment.
- Welding Area Preparation: Clean the area around the exhaust pipe to remove any flammable or combustible materials. Secure the pipe in a stable position to prevent movement during welding.
Always follow the manufacturer’s instructions and consult appropriate safety guidelines to ensure a safe welding environment.
Tips and Tricks for Welding Exhaust Pipes
To achieve the best results when welding exhaust pipes, consider these tips and tricks:
Cleanliness: Thoroughly clean the surfaces to be welded, removing any rust, paint, or debris. This will ensure a clean, strong weld.
Fit-up: Ensure proper fit-up of the exhaust pipe sections to be welded. Good fit-up minimizes gaps and ensures a solid weld.
Welding Technique: Practice proper welding technique, maintaining a steady hand and consistent travel speed. Avoid excessive heat that can distort the pipe or cause burn-through.
Back Purging: For TIG welding stainless steel exhaust pipes, consider using back purging to prevent oxidation on the inside of the pipe. This involves filling the pipe with an inert gas, such as argon, to create a protective atmosphere.
Post-Weld Cleanup: After welding, clean the weld area to remove any slag or spatter. This will improve the appearance and longevity of the weld.
Remember, practice makes perfect. Take the time to refine your welding skills and experiment with different techniques to achieve the best results.
Common Mistakes to Avoid When Welding Exhaust Pipes
To ensure a successful welding project, be aware of these common mistakes and avoid them:
- Insufficient Preparation: Failing to clean and prepare the surfaces properly can result in weak or flawed welds.
- Inadequate Heat Control: Welding with too much or too little heat can lead to distortion, burn-through, or incomplete penetration. Practice controlling the heat to achieve optimal results.
- Poor Fit-up: Neglecting to properly align and fit the exhaust pipe sections can result in weak welds and leaks.
- Incorrect Electrode Selection: Choosing the wrong type or size of electrode for your welding method and material can lead to subpar welds. Consult welding charts and guidelines to select the appropriate electrode.
- Lack of Practice: Welding exhaust pipes requires skill and practice. Don’t rush into a project without sufficient practice and familiarity with your chosen welding method.
By avoiding these common mistakes and taking the time to master your welding technique, you’ll be well on your way to achieving strong and durable welds on your exhaust pipes.
Mastering the Art of Welding Exhaust Pipes
Welding exhaust pipes may seem daunting at first, but with the right knowledge and practice, you can become proficient in this essential skill. Understanding the different welding methods – MIG, TIG, and flux core – allows you to choose the most suitable technique for your specific project requirements.
Remember to prioritize safety by wearing proper PPE and following safety guidelines. Take the time to clean and prepare the surfaces, ensuring a good fit-up for strong welds. Practice good welding technique, control heat, and learn from any mistakes along the way. With patience and perseverance, you will soon master the art of welding exhaust pipes and be able to tackle any repair or upgrade with confidence. So go ahead, grab your welding gear, and start turning those exhaust pipe dreams into reality!