Welding can be an incredibly useful tool for manufacturing processes. It can also be incredibly dangerous if you don’t know what you are doing. You need to have the right safety equipment and practice good safety habits as well. Spatter is essentially a welding term that refers to any piece of metal that gets flayed off when metal meets metal. This occurs when two pieces of different metals are welded together, which releases a vast array of smaller fragments called spatter.
The result is anything from small clumps of metal to large spatters that travel several feet away from the welding zone. Depending on how much spatter travels with it, there can be major consequences for your production process or even your business itself if it happens in a public space or at a customer site. In this article we will discuses about how to avoid spatter in welding properly.
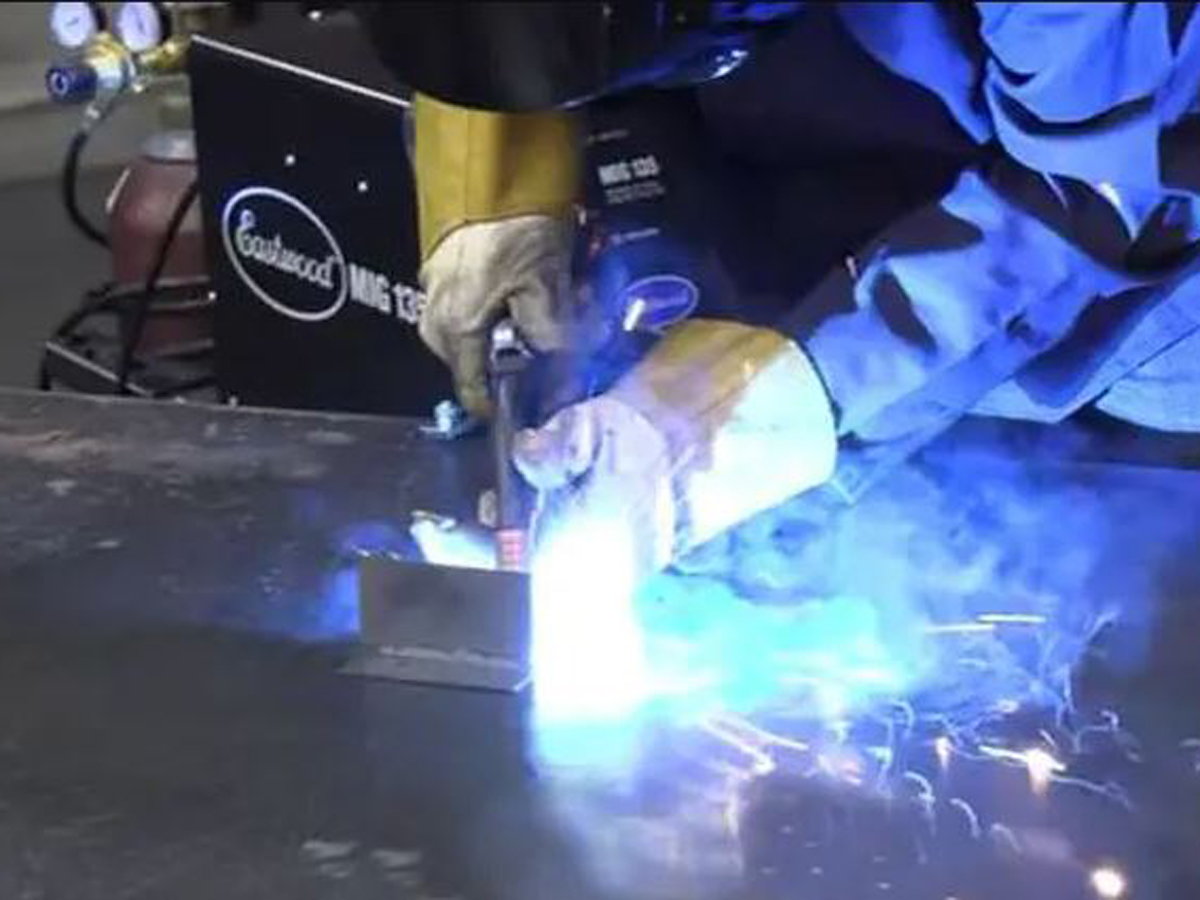
Photo by eastwoodco on YT
What causes spatter in welding?
Spatter happens when the weld pool is not filled properly, creating an air void that allows the weld to “pop” and fling pieces of metal. Welding is a complex process with many variables, and when one is out of balance, the outcome can be something like spatter. Another cause of spatter is when the weld pool is too thin, allowing the weld to be agitated by the torch or machine’s moving parts, causing the weld pool to be “popped”.
Avoid weld pooling
When welding, you want to create a smooth weld that fills all gaps and creates a solid connection. You can achieve this by keeping the welding torch or machine’s tip at the same height throughout the weld, causing a small bead of metal to cover the entire weld area. This weld is termed as a “stabilized” weld. If the weld pool is only partially filled, the void can cause spatter. If a void is created at the edge of the weld pool, it can allow the weld to “pop” and the fragments can travel hundreds of feet away.
To avoid the weld pool being too thin, make sure you weld a continuous bead from the edge of one weld to the edge of the next. If gaps are left between the welds, welding them together creates a solid edge that prevents spatter.
Know your shielding gas and equipment requirements
When you arc your metal, you create a reaction that creates heat and light. This holds atoms together and creates new materials. In order to achieve a weld, you need to control this reaction and prevent the materials being welded from coming into contact with each other. This is why you create a shielding gas environment, where the gases absorb the light and heat so the welding torch doesn’t cause disaster.
The shielding gas requirements vary depending on the type of welding you are doing, but they’re normally referred to as the Class G gas abbreviations, as shown below. Welding gas equipment such as the torch and gas line is regulated to prevent accidents and protect workers, so you need to make sure it’s always operating safely. When switching between different types of welding gases, you have to follow special precautions to prevent spatter.
Use vibrating wire continuously to avoid spatter in welding
As a continuous wire is fed through the torch, it’s made to move and jiggle a little. This continuously agitates the weld pool and stops the weld from being completely filled, which is often what causes spatter. If you only use a short piece of wire and then stop feeding it, the pool stays still and there is no vibration to agitate it. You can also use a simple piece of wood to push the wire back and forth, which is a good way to prevent welding spatter. To prevent the welding wire from getting stuck in the torch’s electrode, you can either use a brush to clear it or feed the wire through a hole in the torch, allowing it to continue while the electrode doesn’t get blocked.
Check the weld pool and surface quickly
The weld pool is essentially where the welding process happens, so you need to check it as soon as possible after welding. The best way to do this is with a “dry” welding surface, where the weld is not covered with slag. A dry surface allows you to see the weld pool and surface in great detail immediately after welding. If you wait too long, the weld pool and surface can become covered with slag, which obscures your view of the weld.
Most torches have a cooling function that keeps the weld pool cool for a short period of time, which means you can’t check the weld pool too soon. If the weld pool is still too hot when you check it, it’s not possible to see the details in the weld, and you may only be able to tell if the weld is good or not. You can keep the weld pool cool by using the torch’s air supply to blow air onto the electrode, or by using a water spray or fog from the nozzle.
Practice good welding habits and safety practices
In addition to knowing your equipment and shielding gas requirements, you need to practice good welding habits as well. This includes ensuring you keep your distance from the weld, have good lighting around the workpiece, and keep the weld pool and surface cool. You can use a “coolant” spray to cool the weld and surface, or spray water onto it. Another welding safety practice is to make sure you don’t weld at the same place repeatedly.
This allows you to check the weld and adjust the welding process if something’s not right. It’s best to weld a different piece of metal every time, so you can compare the welds and adjust where necessary. You also want to wear safety glasses or wear a welding helmet to protect your eyes, and make sure the torch is operating safely.
Learn more about how to avoid spatter in welding
Welding spatter is a dangerous occurrence that can cause serious consequences in manufacturing if not prevented. Fortunately, you can avoid this occurrence by following these welding spatter prevention methods. If you’re eager to get started, make sure you are adequately prepared for the task ahead.