Fusion welding plastic is a commonly used method in various industries, including construction and plumbing. This process involves joining pieces of plastic pipe together by melting the ends and fusing them together. It is a highly effective and durable technique when done correctly. However, it requires skill and precision to ensure a strong and leak-free connection. Whether you are a professional plumber or a DIY enthusiast, this ultimate guide will provide you with valuable tips and techniques from the pros to help you master the art of fusion welding plastic pipe.
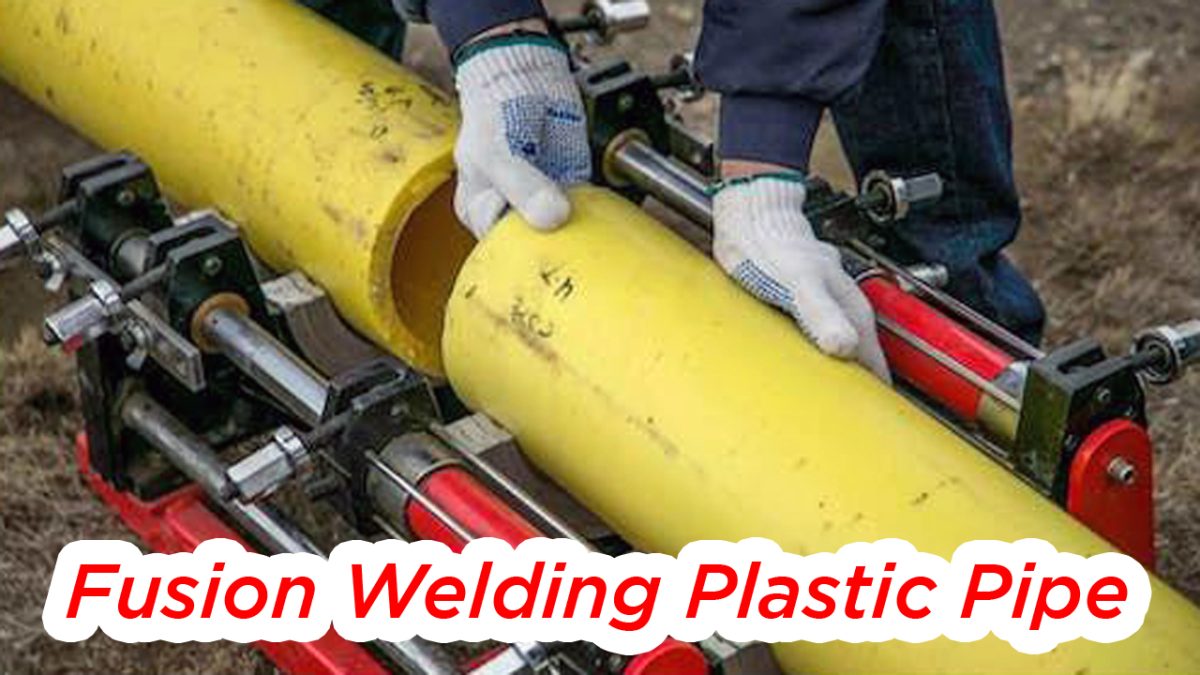
Importance of proper fusion welding techniques
Proper fusion welding techniques are essential for creating strong and durable connections between plastic pipes. When done correctly, fusion welding ensures a tight seal that is resistant to leaks and can withstand the test of time. This is particularly important in industries where the transportation of liquids or gases is involved, as any faults in the connections could lead to expensive repairs or potentially dangerous situations.
One vital aspect of fusion welding is the precise control of temperature and pressure during the welding process. Maintaining the correct fusion temperature and applying the optimal amount of pressure allows the plastic to melt and blend together effectively, resulting in a solid bond.
Another crucial factor is the preparation of the pipe ends. Before fusion welding, it is essential to clean and square off the ends of the pipes to be joined. This ensures that there are no contaminants or irregularities that could interfere with the fusion process and compromise the integrity of the connection.
In the following sections, we will delve into the specific techniques and tips used by professionals to achieve successful fusion welding of plastic pipes. By following these guidelines, you can become skilled in this technique and ensure that your fusion-welded connections are of the highest quality.
Tools and equipment required for fusion welding plastic pipe
To achieve successful fusion welding of plastic pipes, it is essential to have the right tools and equipment at your disposal. Here are some of the key items you will need:
1. Fusion welding machine: This is the primary tool used for fusion welding plastic pipe. It is important to choose a machine that is suitable for the size and type of pipe you will be working with. There are various types of fusion welding machines available, including butt fusion machines, socket fusion machines, and electrofusion machines.
2. Pipe cutters: These are used to cut the plastic pipes to the desired length before welding. It is crucial to use a pipe cutter specifically designed for plastic pipes to ensure a clean, square cut.
3. Scrapers and cleaning tools: Proper cleaning of the pipe ends is essential for achieving a reliable fusion weld. Scrapers and cleaning tools help remove any dirt, debris, or oxidation from the surface of the pipe before welding.
4. Clamps and alignment tools: These tools are used to hold the pipes in the correct position during the welding process, ensuring proper alignment and preventing misalignment or movement.
5. Measuring tools: Accurate measurements are crucial for achieving precise fusion welding. Use measuring tools such as calipers or rulers to ensure proper alignment and fit of the pipes.
6. Protective gear: Safety should always be a priority when performing fusion welding. Wear protective gear such as gloves, safety glasses, and appropriate clothing to protect yourself from burns, hot plastic, and fumes.
Having the right tools and equipment is an important first step towards mastering fusion welding of plastic pipes. In the next section, we will explore the steps involved in preparing the pipes for fusion welding. Stay tuned for an in-depth breakdown of each step!
Preparing the plastic pipe for fusion welding
Preparing the plastic pipe for fusion welding is a crucial step to ensure a successful and reliable weld. Here are the steps involved in preparing the pipes:
1. Inspect the pipe: Before starting the preparation process, carefully inspect the pipe for any visible damage or irregularities. Look for cracks, dents, or scratches that could compromise the integrity of the weld.
2. Mark the pipe: Use a marker or a piece of chalk to mark the area where the pipe will be cut. This will help ensure accuracy when cutting the pipe to the desired length.
3. Cut the pipe: Using a pipe cutter designed for plastic pipes, make a clean and square cut at the marked area. Ensure that the cut is straight and smooth to achieve a proper fit during the welding process.
4. Deburr the pipe: After cutting the pipe, use a deburring tool to remove any rough edges or burrs created during the cutting process. Smooth out the edges to prevent interference with the fusion process.
5. Clean the pipe ends: Proper cleaning of the pipe ends is essential for achieving a reliable fusion weld. Use a scraper or cleaning tool to remove any dirt, debris, or oxidation from the surface of the pipe. Make sure to clean both the inner and outer surfaces of the pipe ends.
By following these steps, you will be well-prepared to move on to the next stage of fusion welding: fusing the pipes together. Stay tuned for the upcoming section where we will delve into the various fusion welding techniques used by professionals.
Step-by-step fusion welding process
In this section, we will explore the step-by-step fusion welding process for plastic pipes. Before we jump into the techniques, it’s important to note that fusion welding is a method used to join plastic pipes together by melting and fusing their ends. This creates a solid and leak-proof connection.
1. Align the pipes: Position the pipes to be welded so that their ends are aligned perfectly. This alignment is crucial for achieving a strong and durable weld.
2. Heat the fusion machine: Preheat the fusion machine to the appropriate temperature according to the type of plastic pipe being welded. Different types of plastic require different temperatures for fusing.
3. Clamp the pipes: Once the machine is heated and ready, clamp the pipes securely into the fusion machine. The clamps should hold the pipes firmly in place without deforming their shape.
4. Apply pressure: The fusion machine applies pressure to both ends of the pipes to ensure proper contact during the fusion process. This pressure helps in heating the pipe ends evenly and promoting a strong weld.
5. Heat and melt the pipe ends: The fusion machine heats the pipe ends simultaneously, melting the plastic and creating a molten state. This molten material then fuses together as the heat is maintained.
6. Cool and solidify: After a sufficient fusion time, the machine stops applying heat, and the pipes begin to cool and solidify. It’s important to let the pipes cool naturally without any external cooling methods to ensure a proper fusion.
7. Inspect the weld: Once the pipes have cooled, inspect the weld to ensure it is smooth, uniformly fused, and devoid of any visible defects. A successful fusion weld should appear seamless, with no gaps or voids.
By following these step-by-step instructions, you can confidently proceed with the fusion welding process. In the next section, we will explore some advanced techniques used by professionals to improve the integrity and strength of fusion welds. Stay tuned!
Common challenges and troubleshooting techniques
In this next section, we will dive into some common challenges that can arise during the fusion welding process and provide you with troubleshooting techniques to overcome them. Fusion welding, while an effective method, is not without its potential pitfalls. Understanding these challenges and knowing how to address them will help you achieve successful fusion welds consistently.
One common challenge is pipe misalignment. Even with careful positioning, pipes may shift slightly during the welding process, resulting in misalignment. To rectify this, use clamps or supports to secure the pipes in place and make any necessary adjustments before continuing.
Another challenge is inadequate heating or cooling of the pipe ends. If the fusion machine doesn’t reach the desired temperature or if the pipes cool too quickly, the weld may be weak or imperfect. To counter this, double-check the machine’s temperature settings and ensure proper insulation and cooling time.
Additionally, imperfect fusion can occur due to contaminants on the pipe ends, such as dirt or oil. Thoroughly clean and prepare the pipe ends before welding, and use high-quality cleaning solvents to remove any residue.
Lastly, if you encounter a failed fusion weld, it’s important to have a plan for repair. Depending on the severity of the issue, options include cutting out the faulty section and rejoining the pipes or using a reinforcement technique like electrofusion.
By being aware of these common challenges and familiarizing yourself with the corresponding troubleshooting techniques, you can tackle any hiccup that may arise during your fusion welding projects. In the following section, we will discuss some additional tips and best practices to further enhance your fusion welding skills.
Maintenance and inspection tips for fusion welded plastic pipe
Now that you’ve learned about troubleshooting techniques for fusion welding plastic pipe, it’s time to shift our focus towards maintenance and inspection. These aspects are crucial for ensuring that your fusion welds stand the test of time and perform effectively.
Regular maintenance is essential to keep your fusion welding equipment in top shape. Be sure to follow the manufacturer’s guidelines for maintenance and servicing intervals. This may include cleaning and lubricating moving parts, checking for any signs of wear or damage, and replacing worn-out components as needed.
Inspecting fusion welds is equally important. Periodically evaluate the quality of your fusion welds to identify any potential issues, such as signs of cracking, leaks, or distortion. Utilize appropriate inspection methods, such as visual inspection, pressure testing, or non-destructive testing, to validate the integrity of your welds.
Additionally, consider implementing a comprehensive record-keeping system to document important information, including fusion parameters, maintenance schedules, and inspection results. This will help you track the performance of your fusion welds over time and identify trends or patterns that may require attention.
By prioritizing maintenance and conducting regular inspections, you can ensure the longevity and reliability of your fusion welds.
Benefits and applications of fusion welded plastic pipe
Understanding the advantages and potential uses of fusion welding can help you make informed decisions about whether it is the right technique for your specific needs.
One of the key benefits of fusion welded plastic pipe is its superior strength and durability. Fusion welding creates a continuous, leak-proof joint, eliminating the risk of weak points or potential failure. This makes it ideal for applications where reliability and long-lasting performance are crucial, such as in water or gas distribution systems, industrial piping, and underground infrastructure.
Another advantage of fusion welding plastic pipe is its versatility. It can be used with a wide range of pipe materials, including high-density polyethylene (HDPE), polypropylene (PP), and polyvinyl chloride (PVC). This flexibility allows for compatibility with various liquids and gases, making it suitable for diverse applications such as plumbing, irrigation, chemical processing, and wastewater treatment.
Furthermore, fusion welding plastic pipe offers excellent resistance to corrosion, chemicals, and environmental factors such as temperature fluctuations and UV radiation. This makes it a reliable choice for installations in harsh or corrosive environments, reducing maintenance and replacement costs over time.
In the following sections, we will delve deeper into each of these applications, providing you with practical insights and key considerations for successful fusion welding projects. Stay tuned to discover how fusion welded plastic pipe can revolutionize your next installation.
Safety precautions to follow during fusion welding
When it comes to fusion welding plastic , it is crucial to prioritize safety at all times. By following the proper safety precautions, you can minimize the risk of accidents, ensure the integrity of the welded joints, and protect yourself and others involved in the project.
First and foremost, before beginning any fusion welding project, ensure that you have the necessary training and qualifications. Fusion welding requires specific skills and knowledge to perform correctly, so it is essential to undergo comprehensive training from a reputable organization or attend a certified welding course.
Additionally, always wear appropriate personal protective equipment (PPE) when working with fusion welding equipment. This includes safety goggles or a face shield, gloves, and flame-resistant clothing. These precautions help protect you from potential hazards such as heat, flying debris, and chemical exposure.
Furthermore, create a safe and well-ventilated work environment. Welding produces fumes and gases that can be harmful if inhaled, so ensure that you have adequate ventilation to prevent the build-up of these substances. If necessary, use respiratory protection equipment to further minimize any potential risks.
Lastly, always adhere to the manufacturer’s guidelines and recommendations when using fusion welding equipment. This includes proper machine setup, correct temperature, and pressure settings, and ensuring that all components are in good working condition. Regularly inspect and maintain your equipment to guarantee optimal performance and minimize the chances of accidents.
By following these safety precautions, you can confidently undertake fusion welding projects while prioritizing the well-being of yourself and those around you.
Conclusion and Mastering at fusion welding for seamless plumbing projects
Fusion welding plastic can be a complex process that requires attention to detail and strict adherence to safety precautions. By following the tips and techniques shared by the pros, you can achieve high-quality and secure welded joints that will stand the test of time.
Throughout this ultimate guide, we have covered the essential tools, materials, and techniques needed for successful fusion welding. We have also discussed the importance of safety precautions to minimize the risk of accidents and ensure the integrity of your work.
Remember to always prioritize safety by obtaining the necessary training and qualifications before starting any fusion welding project. Wear appropriate personal protective equipment (PPE), create a well-ventilated work environment, and adhere to the manufacturer’s guidelines for equipment usage.
With this guide in hand, you are well-equipped to tackle fusion welding projects with confidence. Whether you are a beginner or have some experience, mastering fusion welding techniques will enable you to create seamless plumbing installations that meet the highest standards.