If you’re familiar with material inspection techniques, you’ve probably come across the terms NDE and NDT. While both methods are essential, many professionals tend to use the terms interchangeably, not realizing their unique differences. So, what is the difference between NDE and NDT? It’s critical to understand that both Non-Destructive Evaluation (NDE) and Non-Destructive Testing (NDT) utilize various testing techniques to examine materials, but with different focuses and objectives. In this article, we’ll delve into NDE versus NDT, highlighting their similarities, contrasts, and applications in various industries.
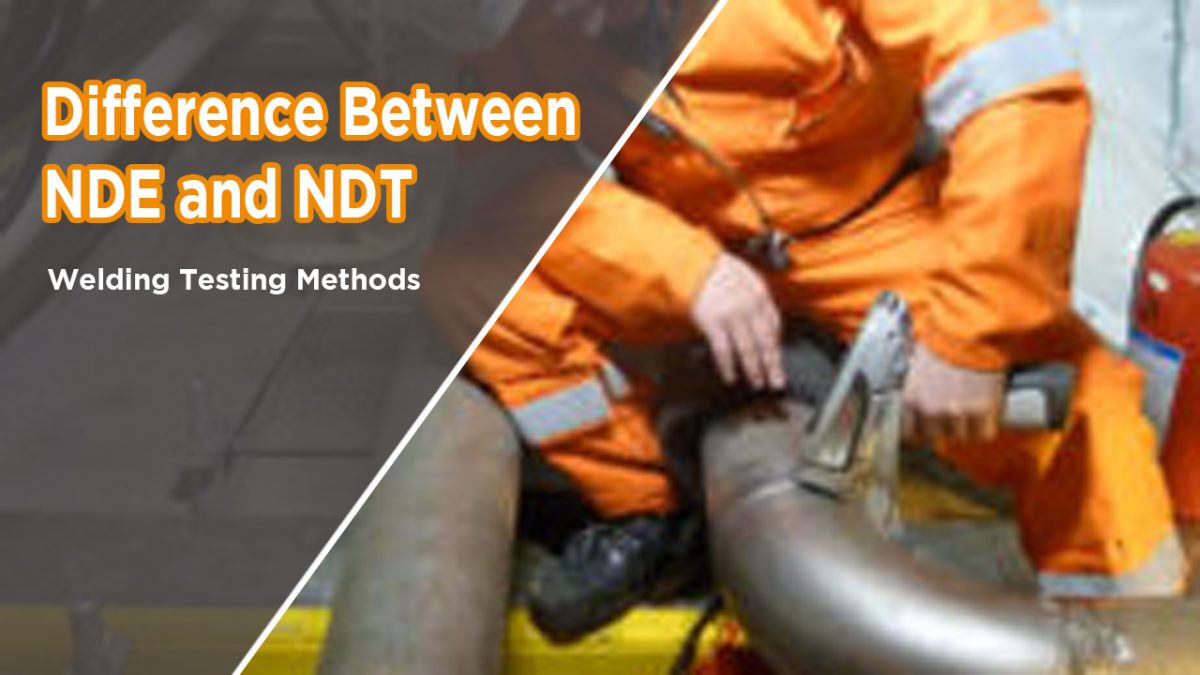
Image by aqcinspection
By the end of this guide, you’ll comprehend these two essential techniques and be better informed to choose which method best suits your project’s specific requirements. Let’s dive into the NDE and NDT comparison to understand their respective roles better.
What is NDE?
NDE, short for Non-Destructive Evaluation, is a technique used to assess the structural integrity of materials and components without causing any damage. NDE can be applied to various fields, including aerospace, automotive, construction, manufacturing, and more.
The goal of NDE is to identify and detect defects, flaws or cracks, evaluate material properties, and ensure the reliability and safety of components or structures. To achieve this, different non-destructive evaluation methods are employed to obtain information about a particular material or item.
NDE Method | Description |
---|---|
Visual Inspection | An examination of components’ surfaces to detect irregularities, corrosion, or other defects that may compromise their structural integrity. |
Ultrasonic Testing | Sending high-frequency sound waves through materials to assess their internal structure and detect imperfections. |
Radiographic Testing | Using X-rays or gamma rays to produce an image of the material’s internal structure and detect internal defects. |
Magnetic Particle Testing | Magnetizing materials and using ferromagnetic particles to detect surface or near-surface defects. |
Eddy Current Testing | Applying an electromagnetic field to detect cracks, corrosion, or other defects in conductive materials. |
By using these and other NDE methods, experts can make accurate assessments and assessments of materials or components, helping ensure quality and safety in various industries.
What is NDT?
Non-Destructive Testing (NDT) refers to a wide range of inspection techniques utilized to evaluate the integrity and properties of materials, components, or structures without causing damage or impairing their performance.
Unlike NDE, which focuses on evaluating the condition and performance of materials in use, NDT aims to detect, locate, and categorize defects and discontinuities that may negatively affect the safety, reliability, or quality of the product or system.
NDT employs various techniques, including Magnetic Particle Testing (MPT), Liquid Penetrant Testing (LPT), Eddy Current Testing (ECT), Ultrasonic Testing (UT), Radiographic Testing (RT), and Visual Testing (VT), each suited to specific applications and types of materials or conditions.
NDT Technique | Description | Application |
---|---|---|
MPT | Induces a magnetic field to detect surface or subsurface defects in ferromagnetic materials. | Used in aerospace, petrochemical, and construction industries. |
LPT | Applies a liquid solution that penetrates surface-breaking flaws, revealing otherwise invisible defects. | Commonly used in weld and casting inspections across various fields. |
ECT | Passes an alternating current through conductive materials to detect surface and subsurface cracks, voids, and corrosion. | Employed in the automotive, power generation, and aerospace sectors, among others. |
UT | Uses high-frequency sound waves to locate internal defects in a variety of materials and thicknesses. | Applicable to numerous sectors, from manufacturing to healthcare. |
RT | Uses X-rays or gamma rays to capture an image of an object’s internal structure or defects. | Widely used across various industries, including aerospace, engineering, and manufacturing. |
VT | Performs a surface inspection of materials, components, or structures using the human eye or imaging devices. | Commonly used in construction and maintenance of buildings and infrastructure, among other uses. |
NDT plays a critical role in ensuring the safety, reliability, and quality of diverse industries, from aerospace and automotive to oil and gas, healthcare, and beyond. Its application provides vital data to identify potential issues early and ensure compliance with industry standards and regulations.
NDE vs NDT Similarities
Non-Destructive Evaluation (NDE) and Non-Destructive Testing (NDT) are two techniques commonly used in various industries to inspect materials and structures without damaging them. Despite their unique approaches, NDE and NDT share some similarities.
NDE | NDT |
---|---|
Both techniques employ advanced equipment to detect, locate, and assess material defects and discontinuities. | Both techniques require trained personnel to operate and interpret results accurately. |
NDE and NDT adhere to industry standards that ensure safety, quality, and consistency of inspection practices. | NDE and NDT are non-invasive techniques, avoiding any damage to the specimens. |
Understanding the similarities and differences between NDE and NDT help industries make informed decisions when choosing inspection techniques for their specific purposes.
NDE vs NDT Contrast
While NDE and NDT share a common goal of inspecting materials without causing any damage, there are key differences between the two techniques.
NDE focuses on evaluating the performance and condition of materials to determine their suitability for a particular application. It involves assessing the material’s characteristics, such as its strength, durability, and corrosion resistance, and measuring its thickness, size, and shape.
On the other hand, NDT primarily focuses on detecting and locating defects or discontinuities in materials or structures. The purpose of NDT is to identify potential failures or issues that could compromise the integrity or safety of the object being inspected.
The techniques used in NDE and NDT differ as well. For example, radiographic testing and ultrasonic testing are commonly used in NDE, while magnetic particle testing and liquid penetrant testing are frequently employed in NDT.
Applications and Roles of NDE and NDT
Non-Destructive Evaluation (NDE) and Non-Destructive Testing (NDT) play vital roles in various industries, including:
Industry/ Sector | NDE Applications/ Roles | NDT Applications/ Roles |
---|---|---|
Manufacturing | Detecting internal and surface defects in products such as castings, forgings, and welds | Checking the integrity of welds and inspecting metal components for fatigue, cracks, and corrosion |
Construction | Checking the quality of concrete, steel, and other materials in buildings and infrastructure projects | Ensuring the safety and integrity of critical components such as pipelines, bridges, and dams |
Aerospace | Inspecting aircraft structures, engines, and components for defects and wear | Checking the quality of critical parts such as turbine blades, fan blades, and engine mounts |
Automotive | Inspecting engine blocks, cylinder heads, and other components for defects and dimensional accuracy | Checking the quality of parts such as castings, forgings, and sheet metal components for defects and damage |
Both NDE and NDT methods are crucial in ensuring quality, safety, and compliance with industry standards. By understanding the differences between these techniques, companies can make informed decisions about which method is best suited for their specific needs and requirements.
Conclusion
Overall, the key differences between NDE and NDT have been unveiled. NDE, or Non-Destructive Evaluation, focuses on evaluating the performance and condition of materials, while NDT, or Non-Destructive Testing, detects and locates defects and discontinuities. Both are necessary for ensuring quality and safety in various industries.
If you’re still unsure which method to choose, consider the specific requirements of your industry or project. This NDE vs NDT comparison guide should help you make an informed decision.
FAQ
What is the difference between NDE and NDT?
NDE stands for Non-Destructive Evaluation, while NDT stands for Non-Destructive Testing. Both methods involve inspecting materials or structures without causing damage. However, NDE focuses on evaluating performance and condition, while NDT primarily focuses on detecting and locating defects and discontinuities.
What is NDE?
NDE, or Non-Destructive Evaluation, is a technique used to assess the performance and condition of materials or structures without causing damage. It involves various methods such as visual inspection, ultrasonic testing, and radiographic testing.
What is NDT?
NDT, or Non-Destructive Testing, is a method employed to detect and locate defects or discontinuities in materials or structures without causing damage. It includes techniques like magnetic particle testing, liquid penetrant testing, and eddy current testing, among others.
What are the similarities between NDE and NDT?
Both NDE and NDT techniques share a common objective of inspecting and assessing materials or structures without causing damage. They require the use of advanced equipment, trained personnel, and adherence to industry standards.
How do NDE and NDT differ?
While NDE focuses on evaluating the performance and condition of materials or structures, NDT primarily focuses on detecting and locating defects and discontinuities. They employ different techniques and approaches to achieve their respective goals.
In what industries are NDE and NDT used?
NDE and NDT are utilized in various industries, including manufacturing, construction, aerospace, and automotive. They play crucial roles in ensuring quality and safety in these sectors.