Deposition rate is an essential factor that impacts the effectiveness and productivity of welding operations. It refers to the amount of filler metal deposited in a welding process over a specific time. Accurately calculating the deposition rate is crucial for achieving optimal welding performance, reducing costs, and ensuring quality welds.
In this article, we will explore the concept of deposition rate in welding and learn how to calculate it effectively. We will discuss the factors that can influence the deposition rate, the importance of calculating it, and the steps you can follow to determine the rate accurately. By the end of this article, you will have a comprehensive understanding of deposition rate calculation in welding and its significance in achieving maximum efficiency and performance.
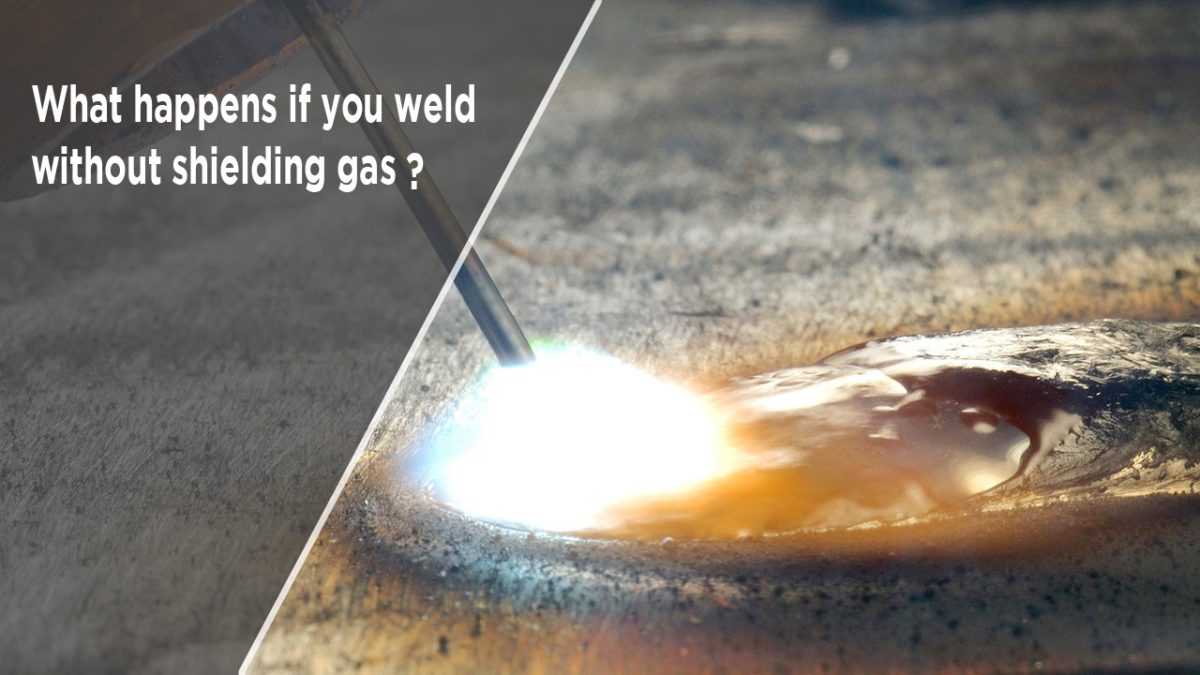
Image by amarineblog
Understanding the Deposition Rate in Welding
Deposition rate in welding refers to the amount of material deposited on the welded surface over a given period. It is a critical parameter that determines the efficiency and effectiveness of the welding process, as well as the quality of the weld produced. When welding, understanding the deposition rate is essential, as it influences the welding process’s speed, productivity, and the final result.
The welding deposition rate definition can vary, depending on the welding process, the type of material used, and the welding machine. However, generally, deposition rate in welding process is calculated by measuring the weight or volume of the deposited material over a defined time, typically per hour.
Deposition rate is dependent on different variables such as welding current, voltage, speed, electrode size, and type of filler material used. By monitoring and understanding these factors, the welder can calculate the deposition rate accurately, thereby improving productivity and ensuring optimal results.
Factors Affecting Deposition Rate in Welding
Several factors can influence deposition rate in welding. It is essential to understand these factors to optimize the welding process and achieve desired outcomes. Some of the critical factors affecting deposition rate in welding are:
Factors | Description |
---|---|
1. Welding Parameters | The welding parameters, such as voltage, amperage, and travel speed, significantly affect deposition rate in welding. These parameters must be set correctly to achieve optimal results. |
2. Welding Position | The deposition rate may vary depending on the welding position, such as flat, horizontal, vertical, or overhead. A change in position can affect the heat input and lead to differences in deposition rates. |
3. Welding Technique | The welding technique used, such as TIG, MIG, or stick welding, can impact the deposition rate. Each technique has a specific deposition rate range, and it is crucial to choose the appropriate technique for the desired results. |
4. Electrode Diameter | The electrode diameter can influence deposition rate in welding. A larger electrode diameter leads to a higher deposition rate, while a smaller diameter results in a lower rate. |
5. Welding Material | The material being welded can also affect deposition rate. Materials with high thermal conductivity dissipate heat more quickly, resulting in a lower deposition rate. |
These are some of the significant factors that influence the deposition rate in welding. Understanding them is crucial for optimizing the welding process and achieving the desired results.
Importance of Calculating Deposition Rate in Welding
Calculating the deposition rate in welding is a crucial step towards achieving productivity, efficient resource management, and high-quality welds. When you accurately measure the amount of material deposited during the welding process, you can effectively control the parameters of your welding operation, making it more efficient and effective.
For instance, by using the weld deposition rate calculation, you can determine how much material is being deposited per hour and make changes to your production plan accordingly. You can also use this information to optimize the welding process, reduce material and labor costs, and minimize wastage.
Furthermore, calculating the deposition rate allows you to ensure that you are meeting the necessary quality standards. By monitoring the amount of material being deposited, you can confirm that the desired weld size and strength have been achieved, meeting the requirements of the project specifications. Overall, understanding and calculating deposition rate in welding can have a significant impact on the successful outcome of your welding project.
Steps to Calculate Deposition Rate in Welding
Calculating the deposition rate in welding is crucial for assessing productivity and ensuring quality welds. Follow these simple steps to accurately calculate the deposition rate:
Gather necessary information: You will need to know the wire feed speed, travel speed, and the diameter of the electrode being used.
Calculate the cross-sectional area of the weld: Multiply the weld bead width by depth.
Calculate the weight of the weld deposit: Multiply the cross-sectional area of the weld by the length of the weld (in inches) and by the weight of the metal deposited per cubic inch.
Calculate the deposition rate: Divide the weight of the weld deposit (in pounds) by the total time it took to make the weld (in hours).
Keep track of your data: It’s important to record your data accurately for future reference and comparison.
By following these steps, you can calculate the deposition rate in welding and gain valuable insights to optimize welding parameters and improve efficiency and performance.
Enhancing Efficiency and Performance Through Deposition Rate Calculation
Calculating deposition rate is essential for welding operations as it helps in optimizing the welding parameters, reducing costs, and achieving the desired outcomes. By accurately calculating the rate, you can improve the overall efficiency and performance of your welding process.
To enhance efficiency and performance, there are several ways to utilize deposition rate information:
Optimizing welding parameters: By knowing the deposition rate, you can adapt your welding parameters, such as voltage, amperage, and travel speed, to achieve desired results, such as improved penetration and reduced spatter. This optimization ultimately leads to less rework, faster production times, and lower costs.
Resource management: Deposition rate information can be utilized to manage resources such as welding wire and shielding gas. With this information, you can ensure that you have enough resources to complete the job while minimizing waste.
Quality assurance: Deposition rate information can be used to develop standards, ensuring that the welding process achieves the desired quality levels. Setting and achieving these standards contributes to positive brand reputation and customer satisfaction.
Example:
Welding Parameters | Deposition rate | Output |
---|---|---|
250 amps, 26 volts, 10 inches/min | 5 lb/hour | Strong and smooth welds, minimal spatter |
200 amps, 24 volts, 8 inches/min | 4 lb/hour | Weak and inconsistent welds, excessive spatter |
As shown in the above example, optimizing the welding parameters by considering deposition rate improved the output and minimized the spatter resulting in efficient and quality welding.
Optimizing Deposition Rate: Best Practices and Techniques
When it comes to welding deposition rate calculation, optimizing the rate is essential for achieving maximum productivity and quality. Here are some best practices and techniques that can help:
- Use the highest possible amperage without sacrificing quality
- Select the right wire size and type for the job
- Stay within the specified parameters for the electrode
- Keep the electrode stick out as short as possible
- Avoid weaving the electrode excessively
- Use the correct travel speed
- Ensure proper preheating and interpass temperatures
- Clean the base metal thoroughly
- Use a push rather than a pull technique with the electrode
By following these techniques, you’ll be able to optimize the deposition rate in your welding projects and achieve better results.
Conclusion
Deposition rate is a critical factor in welding that determines productivity and quality. By accurately calculating the deposition rate, you can optimize your welding processes and achieve better results. We hope this article has provided you with valuable insights into the concept of deposition rate, its significance, and the steps to calculate it.
Remember to consider various factors that can affect deposition rate, such as welding parameters, material properties, and environmental conditions. By following best practices and techniques, you can further enhance efficiency and performance in your welding projects.
Stay mindful of deposition rate in welding and keep refining your skills to become a skilled welder. Thank you for reading, and we hope you found this article informative and useful!
FAQ
What is deposition rate in welding?
Deposition rate in welding refers to the amount of material, typically in terms of weight or volume, that is added to the weld joint during the welding process. It is an important parameter that determines the speed and efficiency of the welding operation.
How do you calculate deposition rate in welding?
To calculate the deposition rate in welding, you need to determine the weight or volume of filler material deposited per unit of time. This is typically measured in pounds per hour or ounces per minute. The calculation involves dividing the weight or volume of filler material by the total welding time.
What factors affect deposition rate in welding?
Several factors can influence the deposition rate in welding. The welding process, type of filler metal, welding technique, current and voltage settings, travel speed, and joint design are some of the key factors that can affect the deposition rate. It is important to consider and optimize these factors to achieve the desired deposition rate in welding.
Why is calculating deposition rate important in welding?
Calculating the deposition rate in welding is important for several reasons. It helps in assessing productivity and estimating the time required for a welding project. It also aids in managing resources effectively, such as determining the amount of filler material needed. Additionally, calculating the deposition rate allows for quality control and helps ensure consistent and high-quality welds.
What are the steps to calculate deposition rate in welding?
To calculate the deposition rate in welding, follow these steps: 1. Measure the weight or volume of filler material used during the welding process. 2. Determine the total welding time. 3. Divide the weight or volume of filler material by the welding time to calculate the deposition rate.
How can calculating deposition rate enhance efficiency and performance in welding?
Calculating the deposition rate in welding enables better control and optimization of welding parameters. By knowing the deposition rate, welders and operators can adjust their techniques, travel speeds, and current settings to achieve optimal productivity and quality. This enhances efficiency, reduces resources wastage, and improves overall performance in welding projects.
What are some best practices for optimizing deposition rate in welding?
To optimize deposition rate in welding, consider the following best practices: 1. Choose the appropriate welding process and technique for the application. 2. Select the right type and size of filler metal. 3. Maintain consistent and appropriate current and voltage settings. 4. Control travel speed to ensure proper heat input. 5. Ensure a proper joint design and fit-up for efficient welding. Implementing these best practices will help achieve the desired deposition rate and improve the overall efficiency and quality of welding operations.