Are you looking to calculate the cost of CO2 welding for your project? Understanding the expenses involved in CO2 welding can help you budget more effectively and make informed decisions. In this article, we will guide you through the process of calculating CO2 welding costs and provide you with valuable insights to optimize your project’s expenses.
The following formula is used to calculate the cost of CO2 welding: Total Welding Cost = (Electrode Consumption x Electrode Cost) + (Labor Cost per Hour x Welding Time) + (Gas Cost per Cubic Foot x Gas Consumption) This formula takes into account the key elements that contribute to the overall welding cost: electrode consumption, labor charges, and gas cost. |
CO2 welding is a widely-used welding method known for its versatility and cost-effectiveness. By using carbon dioxide gas as a shielding medium, it ensures a strong and durable weld joint. However, determining the precise cost of CO2 welding requires taking into account various factors such as electrode consumption, labor charges, gas prices, and material thickness.
We will walk you through the step-by-step process of calculating the cost of CO2 welding, covering everything from identifying the necessary variables, calculating material consumption, determining labor costs, and factoring in overhead expenses. By following our guide, you will gain a comprehensive understanding of how to accurately estimate CO2 welding costs and make better financial decisions for your welding projects.
Importance of Calculating Welding Costs
Calculating welding costs is essential for any project, as it allows you to plan your budget accurately and avoid any financial surprises. Whether you’re a professional welder or a project manager overseeing welding operations, understanding the cost implications of CO2 welding can help you make informed decisions and optimize your expenses.
By calculating welding costs, you can assess the feasibility of a project, determine the profitability, and compare different welding methods to find the most cost-effective option. Additionally, accurate cost calculations enable you to provide accurate quotes to clients, ensuring transparency and avoiding any financial discrepancies later on.
Factors to Consider When Calculating CO2 Welding Costs
Calculating the cost of CO2 welding involves considering various factors that contribute to the overall expenses. Here are some key factors to consider:
Electrode Consumption: The consumption rate of electrodes depends on the welding process, material thickness, and joint design. It is crucial to determine the electrode consumption accurately, as it directly affects the cost of welding.
Labor Charges: The cost of labor plays a significant role in calculating welding costs. The labor charges can vary depending on the skill level of the welder, the complexity of the project, and the time required to complete the welding.
Gas Prices: Carbon dioxide gas is used as a shielding medium in CO2 welding. The cost of gas can vary depending on the region and supplier. It is essential to factor in the gas prices to calculate the overall welding cost accurately.
Material Thickness: The thickness of the material being welded affects the welding time, electrode consumption, and gas usage. Thicker materials require more welding time and higher electrode consumption, which can significantly impact the cost of CO2 welding.
The Formula for Calculating CO2 Welding Costs
To calculate the cost of CO2 welding, you can use the following formula:
Total Welding Cost = (Electrode Consumption x Electrode Cost) + (Labor Cost per Hour x Welding Time) + (Gas Cost per Cubic Foot x Gas Consumption)
This formula takes into account the key elements that contribute to the overall welding cost: electrode consumption, labor charges, and gas cost.
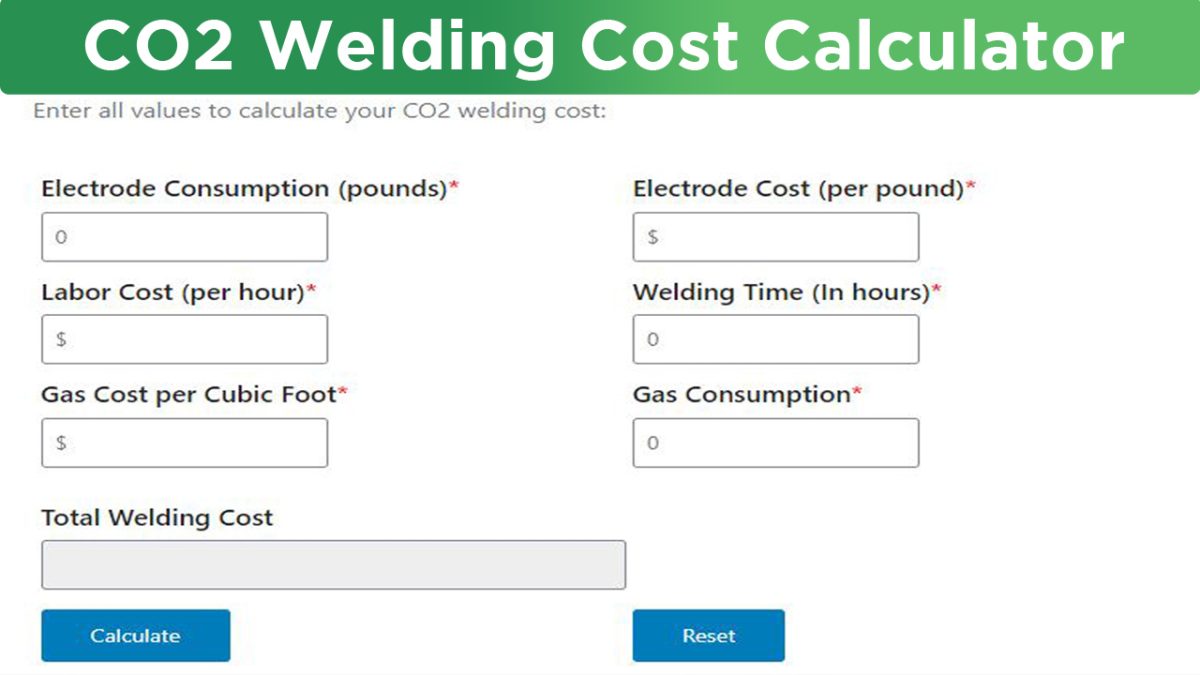
Breaking Down the Components of the Formula
Let’s break down the components of the formula to understand how each factor contributes to the overall welding cost:
Electrode Consumption x Electrode Cost: This term represents the cost of electrodes used during the welding process. The electrode consumption is typically measured in pounds, and the cost per pound can vary depending on the electrode type and supplier.
Labor Cost per Hour x Welding Time: This term represents the labor charges for the welding process. The labor cost per hour is determined by the wage rate of the welder or welding team. The welding time is the total time required to complete the welding, including setup, actual welding, and cleanup.
Gas Cost per Cubic Foot x Gas Consumption: This term represents the cost of carbon dioxide gas used as a shielding medium. The gas cost per cubic foot can vary depending on the supplier and region. The gas consumption is calculated based on the flow rate and the total welding time.
Examples of Calculating CO2 Welding Costs
Let’s consider a practical example to illustrate how to calculate CO2 welding costs:
Example: – Electrode Consumption: 5 pounds – Electrode Cost: $10 per pound – Labor Cost per Hour: $25 – Welding Time: 4 hours – Gas Cost per Cubic Foot: $0.50 – Gas Consumption: 100 cubic feet
Using the formula mentioned earlier, we can calculate the total welding cost as follows:
Total Welding Cost = (5 pounds x $10 per pound) + ($25 per hour x 4 hours) + ($0.50 per cubic foot x 100 cubic feet)
Total Welding Cost = $50 + $100 + $50 = $200
In this example, the total welding cost for the project is $200.
Tips for Reducing CO2 Welding Costs
While calculating the cost of CO2 welding is essential, finding ways to reduce those costs can significantly impact your project’s budget. Here are some tips to help you reduce CO2 welding costs:
Optimize Welding Parameters: By optimizing welding parameters such as voltage, current, and wire feed speed, you can minimize electrode consumption and reduce overall welding costs.
Minimize Material Waste: Proper planning and accurate measurements can help minimize material waste, reducing the need for additional welding and lowering costs.
Invest in Training: Well-trained welders can work more efficiently, reducing labor costs and improving productivity.
Compare Gas Suppliers: Research and compare different gas suppliers to find the most competitive prices without compromising on quality.
Tools and Software for Calculating CO2 Welding Costs
Several tools and software are available to simplify the process of calculating CO2 welding costs. These tools can help you save time and ensure accurate calculations. Some popular options include:
Welding Cost Estimator: This software allows you to input the necessary variables and provides an estimate of the welding costs based on industry-standard formulas.
Welding Cost Calculator: Similar to the welding cost estimator, this tool helps you calculate welding costs based on specific project requirements.
Spreadsheet Software: Tools like Microsoft Excel or Google Sheets offer customizable templates and formulas that can be used to create your own welding cost calculator.
Common Mistakes to Avoid When Calculating CO2 Welding Costs
While calculating CO2 welding costs, it’s important to avoid common mistakes that can lead to inaccurate estimations. Here are some mistakes to watch out for:
Neglecting Overhead Expenses: Overhead expenses such as equipment maintenance, consumables, and indirect labor costs should be included in the calculations to ensure accurate cost estimates.
Using Incorrect Variables: Ensure that you have the correct values for electrode consumption, labor charges, gas prices, and material thickness. Using incorrect variables can lead to inaccurate cost calculations.
Underestimating Material Thickness: Failing to account for material thickness can result in underestimating electrode consumption and gas usage, leading to higher costs.
Conclusion and Final Thoughts
Calculating the cost of CO2 welding is an essential aspect of any welding project. By understanding the factors involved and using the appropriate formula, you can accurately estimate the welding costs and make informed financial decisions. Additionally, implementing cost-saving measures and avoiding common mistakes can help optimize your welding expenses.
Remember to consider factors such as electrode consumption, labor charges, gas prices, and material thickness when calculating CO2 welding costs. Utilizing tools and software can streamline the process and ensure accurate estimations. By following the guidelines provided in this article, you’ll be well-equipped to calculate CO2 welding costs and optimize your welding projects.